It's pre-dawn and I am heavily caffeinated so I thought I would let my brain thoughts spill out with the intention that something helpful or constructive may occur.
I forget who used the 3k CF fabric and 2 part epoxy on the back of the Staples presentation cardboard, my apologies. I do recall that it had fantastic results, though. It's definitely one of the designs I want to rip off... Uhhh. I mean replicate. For some reason it just fell off the radar in the group, which is a shame. Anyhow, since then a couple of folks have been getting good results with the honeycomb crush proof cardboard, which required reinforcement of the rear panel with glue and paper. I'm wondering if the cf/epoxy approach would make a killer skin for that type of cardboard as well. I'm also curious as to if it would work as a back skin for xps/eps, or even the canvasses. It will be a bit before I could experiment with these combos but some of you who are already working with those substrates may want to try it out.
I recall mention at some point that DML Panels allow for some overlap. I was thinking about doing a 2 way crossed over array with a large low range panel of the cf/cardboard or maybe xps/eps, and then a plexi panel like Dave's for mids and highs. Due to limitations of wall space, and trying to keep things on axis, I was wondering if, and how much, I might be able to hang the HF panel in front of the LF panel, and what considerations I may want to consider in advance. Thoughts?
Lastly, I had a idea for those who like frames for floor units, or just for damping. It's a wild concept and wouldn't be easy or practical to execute but hey, dreamers gotta dream, right? So anyway, what if you had a strong frame with some kind of air bladder recessed in it, along the circumference of the panel. Like, imagine taking a bicycle inner tube and wrapping it around the edges of your panel. Then you could use air pressure to change the amount of damping with a fairly fine level of control. It's kind of like the recently submitted design with the screw clamp system and foam, except it would work to dampen all 4 sides of the panel equally and you wouldn't have to worry about foam compression over time. The bladder would also probably have interesting isolating properties (maybe good, maybe bad? LOL).
Lastly, has anyone considered using sound dampener a.k.a Dynamat or a similar product for edge or pinpoint damping? It's adhesive backed (and that adhesive is strong!) and it has rediculous mass/weight in tiny quantities, yet it lies flat. Seems like it would be an attractive alternative to bluetac and AA batteries or washers/coins/other random heavy things.
Thanks in advance for amusing my ramblings.
I forget who used the 3k CF fabric and 2 part epoxy on the back of the Staples presentation cardboard, my apologies. I do recall that it had fantastic results, though. It's definitely one of the designs I want to rip off... Uhhh. I mean replicate. For some reason it just fell off the radar in the group, which is a shame. Anyhow, since then a couple of folks have been getting good results with the honeycomb crush proof cardboard, which required reinforcement of the rear panel with glue and paper. I'm wondering if the cf/epoxy approach would make a killer skin for that type of cardboard as well. I'm also curious as to if it would work as a back skin for xps/eps, or even the canvasses. It will be a bit before I could experiment with these combos but some of you who are already working with those substrates may want to try it out.
I recall mention at some point that DML Panels allow for some overlap. I was thinking about doing a 2 way crossed over array with a large low range panel of the cf/cardboard or maybe xps/eps, and then a plexi panel like Dave's for mids and highs. Due to limitations of wall space, and trying to keep things on axis, I was wondering if, and how much, I might be able to hang the HF panel in front of the LF panel, and what considerations I may want to consider in advance. Thoughts?
Lastly, I had a idea for those who like frames for floor units, or just for damping. It's a wild concept and wouldn't be easy or practical to execute but hey, dreamers gotta dream, right? So anyway, what if you had a strong frame with some kind of air bladder recessed in it, along the circumference of the panel. Like, imagine taking a bicycle inner tube and wrapping it around the edges of your panel. Then you could use air pressure to change the amount of damping with a fairly fine level of control. It's kind of like the recently submitted design with the screw clamp system and foam, except it would work to dampen all 4 sides of the panel equally and you wouldn't have to worry about foam compression over time. The bladder would also probably have interesting isolating properties (maybe good, maybe bad? LOL).
Lastly, has anyone considered using sound dampener a.k.a Dynamat or a similar product for edge or pinpoint damping? It's adhesive backed (and that adhesive is strong!) and it has rediculous mass/weight in tiny quantities, yet it lies flat. Seems like it would be an attractive alternative to bluetac and AA batteries or washers/coins/other random heavy things.
Thanks in advance for amusing my ramblings.
In the APM (Accurate Pistonic Motion) woofer, the composite diaphragm is connected to the coil in 4 points, which transfer the vibrations to the diaphragm. Some drivers have 8 such points.
I was trying to tell in the earlier posts that one should try an old driver (take the cone off and connect the coil to the DNL panel) to get a better "exciter" than these low-level exciters some companies sell.
I was trying to tell in the earlier posts that one should try an old driver (take the cone off and connect the coil to the DNL panel) to get a better "exciter" than these low-level exciters some companies sell.
Attachments
Last edited:
One last brain dump before I pass out.
It seems like pretty much everyone in here is using or seeking to use DMLs for some degree of purist music listening, and I'm all for that but I'm also a big home theater guy and I am wondering about how viable they are for HT, and more specifically Atmos. I am not seeing many people doing this and I'm not sure if it's because there is good reasoning behind it or if it's just not a "thing" yet. I'd rather not be the Guinea Pig if it's a flawed concept.
I am currently running a reflective 9.1 (5.1.4) system with conventional drivers, etc. I guess my main concern is the bi/di/chaotic nature of DMLs. It has its benefits for big sound but when you're dealing with object based audio (Atmos/DTS-X) will the sound be too diffused to render the 3d landscape properly, especially for the height channels? Also are DMLs up to handling the crazy transients, and mixture of dialogue, music and effects of movies? This is all assuming the panels are executed well and supplemented with subwoofers of course.
Also since the exciters used in DMLs have such low power ratings (10-40 WRMS @4ohms) how much would I have to worry about nuking them at ~220 WRMS from my Marantz? I can use the Audessey DSP to level match them with the sub (and any tradition drivers I may keep using) so with proper setup I would probably be fine as long as I was careful not to overdrive them, right?
It seems like pretty much everyone in here is using or seeking to use DMLs for some degree of purist music listening, and I'm all for that but I'm also a big home theater guy and I am wondering about how viable they are for HT, and more specifically Atmos. I am not seeing many people doing this and I'm not sure if it's because there is good reasoning behind it or if it's just not a "thing" yet. I'd rather not be the Guinea Pig if it's a flawed concept.
I am currently running a reflective 9.1 (5.1.4) system with conventional drivers, etc. I guess my main concern is the bi/di/chaotic nature of DMLs. It has its benefits for big sound but when you're dealing with object based audio (Atmos/DTS-X) will the sound be too diffused to render the 3d landscape properly, especially for the height channels? Also are DMLs up to handling the crazy transients, and mixture of dialogue, music and effects of movies? This is all assuming the panels are executed well and supplemented with subwoofers of course.
Also since the exciters used in DMLs have such low power ratings (10-40 WRMS @4ohms) how much would I have to worry about nuking them at ~220 WRMS from my Marantz? I can use the Audessey DSP to level match them with the sub (and any tradition drivers I may keep using) so with proper setup I would probably be fine as long as I was careful not to overdrive them, right?
In the Sony APMs, the aluminium tubes come through the diaphragm to the outer surface, transferring the vibrations to both sides of the diaphragm. The amount of such tubes are from 4 to 8. The driver is (the drivers are) boxed in an enclosure that has a bass reflex transfer, which is usually in the front as a slit. The back sound waves are also used.
The "high-end" DMLs made by companies have some sort of a frame and some sort of enclosure, and the panels are fixed to the surround softly or rigidly. Interestingly, none of the manufacturers stay in the market for long.
Studying the Sony APMs, one can deduce that one type (material) of panel won't give the full range of sounds, so you have to make it at least 2, one for highs, one for mid-lows. The panels can't be half the wall high and as wide as a window pane. Would be ugly that way. They should be small and aesthetic.
The "high-end" DMLs made by companies have some sort of a frame and some sort of enclosure, and the panels are fixed to the surround softly or rigidly. Interestingly, none of the manufacturers stay in the market for long.
Studying the Sony APMs, one can deduce that one type (material) of panel won't give the full range of sounds, so you have to make it at least 2, one for highs, one for mid-lows. The panels can't be half the wall high and as wide as a window pane. Would be ugly that way. They should be small and aesthetic.
There a guy selling somewhat damaged Sony APM A7E for 10 quid. Maybe someone like to have look inside?
If you are interested, have a look. Found them in internet.
The earlier Sony APM-12ES bass driver appears to have a smaller cone between the flat panel and the coil. The fourth image.
The early APM-6 mid/low woofer had 4 coils to drive the flat panel.
Hope these photos give some ideas to DIYers.
An early advertisement below.
The earlier Sony APM-12ES bass driver appears to have a smaller cone between the flat panel and the coil. The fourth image.
The early APM-6 mid/low woofer had 4 coils to drive the flat panel.
Hope these photos give some ideas to DIYers.
An early advertisement below.
Attachments
And, here is a video, where you can see what the Technics honeycomb driver looks like. The flat honeycomb panel/diaphragm is "excited" by a thin polypropylene cone connected to the coil. No push-pull of air, but transferring the vibrations to a very stiff membrane by a stiff cone. This means small disks or flat surfaces can make good sound waves, if the (composite) material is quite stiff.
Have a look at how the honeycomb disk was made.
Have a look at how the honeycomb disk was made.
Last edited:
This picture shows some of my various shaped panels over the last 10years.
As for how many exciter or panels ,that is up to you,you can make it as complicated as you like,multiple amps,eq,xo,you name it.
All the things you have mentioned have been discussed on various threads on the web over the years.
It's a long read ,you'll be grey haired like me by the time you've finished reading them all,plus patents .
When I first started looking into dml,I purchased 40 or so exciters ,as it was thought that like the podiums ,the more the better!
That is why I have so many panels lying around with exciters still attached.
I have found dml interesting and fun.
Hope you will too.
Steve
Thanks Steve. I plan on doing some experimenting for sure. I have a pair of DAEX25QLP-4 exciters and a 2x18 T class amp arriving this week. I wanted to start small. As you have probably seen, I have a lot of questions and ideas. I'm expecting to be tinkering and contributing a lot in the near future.
Interesting line of thought.
As sound waves move away from the source radially, why not use disks? Even in a cone, the waves move along the cone surface and on it, radially. So, why not use two different materials for the panel, one for mid/low, one for high?
Thinking about the sound waves coming out of the back, and to get lows out of it, why not box the back and leave a bass-reflex hole (or a transmission line) out of that?
Attached is a two material drawing of a disk.
The circular design seems to be well documented as having some of, if not the, worst frequency responses if I recall correctly. Standing wave and cancelation issues I think. I'm not sure about having a dual mass construction like that. Haven't seen anything in my readings so far with that kind of design. Could be worth messing with but I'm not sure if the waves would transfer from substrate to substrate as imagined, giving you the best of both. I'm guessing the heavier would just damp the lighter and you'd maybe get strange cancelations. That's just a guess though. I am not that kind of engineer. Haha.
Has anyone tried using these plastic diffusers for fluorescent light fixtures as a component? They are relatively light, rigid, and resonant, and have a similar shape to the core of the crush proof cardboard. Seems to me if you were to adhere a thin substrate to one or both sides it might make a decent DML. Same with the lens covers for the same type of lights. Smooth on one side, textured dimples on the other, light, rigid, resonant. If you combined them with another substrate like cardboard or thinner xps/eps it could work. The dimples my help with standing waves since they break up the flatness of the surface. Could get interesting results depending on which surface faces outwards, if you used them on the front.
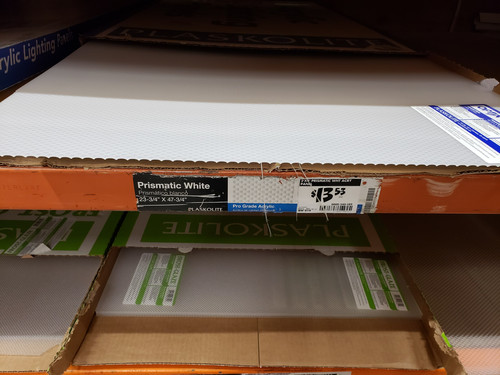
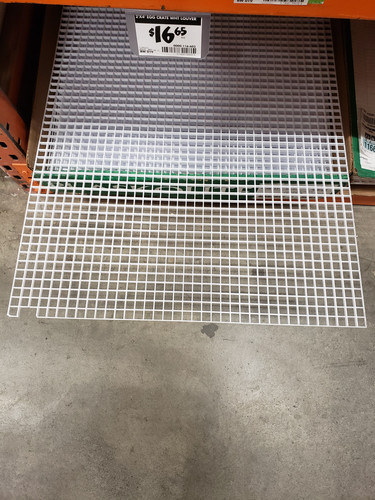
Interesting line of thought.
As sound waves move away from the source radially, why not use disks? Even in a cone, the waves move along the cone surface and on it, radially. So, why not use two different materials for the panel, one for mid/low, one for high?
Thinking about the sound waves coming out of the back, and to get lows out of it, why not box the back and leave a bass-reflex hole (or a transmission line) out of that?
Attached is a two material drawing of a disk.
Manger Driver? Haven't read this article for quite a while, but it mentions, "Instead, Josef W. Manger relied on the principle of bending waves, which starting from the centre of a plate-like diaphragm, travel to the outside, like waves after a stone is thrown into the water" rather than pistonic motion of the diaphragm.
I have heard the driver, mounted in a box some years ago, and it was very fast and detailed from memory.
Manger(R) Sound Transducer — Manger Audio
Attachments
Manger Driver? Haven't read this article for quite a while, but it mentions, "Instead, Josef W. Manger relied on the principle of bending waves, which starting from the centre of a plate-like diaphragm, travel to the outside, like waves after a stone is thrown into the water" rather than pistonic motion of the diaphragm.
I have heard the driver, mounted in a box some years ago, and it was very fast and detailed from memory.
Manger(R) Sound Transducer — Manger Audio
Thanks for the link. Didn't know about this. 🙂
About transferring sound from material to another; place a spoon in a glass and place it on the table and knock on the table at some point, you'd hear tingling of the spoon against the glass.
Second, using the same material for the panel, but you can add another material, such as paint, balsa, another thickness of the same material, etc on one area, and leave the other area without it, and test it. The idea of testing the sound, is subjective from your own ears, rather than any measuring instrument. Whatever the instrument measurements, you'd decide to sound is good or bad -- in your memory, you have remembrance of how other speakers sounded. You can't get all the range from one driver, however "high-end" it is.
Third, as you are the DIYer, you'd have to try different materials, otherwise, you won't know. Sony and Technics had proved that small square or round disks fixed to the "voice" coil can give quite nice sound. I've heard APMs in the 90s, but Technics not so long ago.
If you need to make a nice sounding, powerful DML, you'd need to create your own "exciter" from a standard driver, after all you are the DIYer. The commercial ones are too weak.
Last edited:
It looks like Manger was saying the same thing as I was trying to say -- different materials in different sections in circles. You have to damp the further end to get the lows.
Last edited:
This is the best link, I ever got. Thank you very much, pal!
Found this video. Sounds quite different, coming from my speakers.
How its made.
Last edited:
The 8 pointed inverted star on the Manger composite panel driver is just eye-candy. 🙂 It could be 96 pointed inverted star and so on. By making those points infinite, it becomes a circle.
So, we need three layers in the round DML panel. Adding and/or subtracting the width, thickness, type etc, you can get a optimum sounding DML disk. The inventor Josef Manger appears to be more of a DIYer than a scientist or an engineer.
So, we need three layers in the round DML panel. Adding and/or subtracting the width, thickness, type etc, you can get a optimum sounding DML disk. The inventor Josef Manger appears to be more of a DIYer than a scientist or an engineer.
Gapmedia.
I think it was 5 or 6years ago that I listened to the manger speakers,the owner was very excited about them.
I was very enthusiastic about being able to listen to them,but found I hard to conceal my disappointment.
All I could hear was a speaker in a box 😱 even though it was a very expensive box!
I have no idea what the unit would sound like on an open panel.
I hear the same sound when I hear a BMR in a box ,although I did listen to one horn loaded BMR that wasn't too bad.
I haven't listened to a BMR on an open panel either,I must ask my friend to lend me his unit for a test?
You would probably get the same effect if you put an electrostatic panel in a box?
Steve
I think it was 5 or 6years ago that I listened to the manger speakers,the owner was very excited about them.
I was very enthusiastic about being able to listen to them,but found I hard to conceal my disappointment.
All I could hear was a speaker in a box 😱 even though it was a very expensive box!
I have no idea what the unit would sound like on an open panel.
I hear the same sound when I hear a BMR in a box ,although I did listen to one horn loaded BMR that wasn't too bad.
I haven't listened to a BMR on an open panel either,I must ask my friend to lend me his unit for a test?
You would probably get the same effect if you put an electrostatic panel in a box?
Steve
Last edited:
Balanced Mode Radiator (BMR) or Distributed Mode Loudspeaker (DML) are just words, where people coin them to try to explain something. All what we hear is distributed and balanced by our ears. They, the ears, either like to hear those sounds, or demand you to get away from them. Everything we hear, see, touch, smell etc is subjective feeling. One likes the sound of one type of a speaker, while others don't. The measuring instruments don't care two hoots.
Attached is a bluetooth speaker, I bought online as a present to a kid. I bought it just because of the upward firing driver and most importantly cone distributor. I had never heard of it before. I put the small speaker on the shelf and ran some music (Solar Radio) and asked my wife if the music is good. She couldn't pinpoint the source of the sound. Her hearing is very good. It simply filled the room, for such a small thing! (She found it later, of course.)
Manger surely was a DIYer. The idea of triple thicknesses, or 3 different materials, all placed radially had come to him in the 60s, last century. I am not taking into consideration his 8 point inverted star, that's just eye-candy, looking for a high price tag. I remember my pals and I, as students experimenting with vibrations of all kinds of materials in the 70s and 80s. Life took a different turn later, those "playing" had to be stopped.
Daniela Manger trying to explain the matter.
Attached is a bluetooth speaker, I bought online as a present to a kid. I bought it just because of the upward firing driver and most importantly cone distributor. I had never heard of it before. I put the small speaker on the shelf and ran some music (Solar Radio) and asked my wife if the music is good. She couldn't pinpoint the source of the sound. Her hearing is very good. It simply filled the room, for such a small thing! (She found it later, of course.)
Manger surely was a DIYer. The idea of triple thicknesses, or 3 different materials, all placed radially had come to him in the 60s, last century. I am not taking into consideration his 8 point inverted star, that's just eye-candy, looking for a high price tag. I remember my pals and I, as students experimenting with vibrations of all kinds of materials in the 70s and 80s. Life took a different turn later, those "playing" had to be stopped.
Daniela Manger trying to explain the matter.
Attachments
Last edited:
Chdsl.
Manger is a BMR ,words are sometimes useful.
Steve
Maybe, but getting used to abbreviations, one tends to lose contact with the real issue.
They are all distributed and balanced, and most importantly, it is about sound, and your ears. 🙂
I am really glad that @Gapmedia giving the link. It put me in the right track.
Last edited:
A "distributed mode loudspeaker" doesn't have to be a board hung with strings or a board by itself. Its a flat surface (maybe, not even a flat surface) that transmits sound louder from a source, an "exciter." The exciter doesn't have to be those that sold commercially today directed to DIYers.
Whatever the surface, it should bring joy to ears. 🙂
Whatever the surface, it should bring joy to ears. 🙂
- Home
- Loudspeakers
- Full Range
- A Study of DMLs as a Full Range Speaker