Great F4!!! It would put (too) many hi-end amplifiers to shame! Great job - congratulations!!!
Member
Joined 2002
Great F4!!! It would put (too) many hi-end amplifiers to shame! Great job - congratulations!!!
I agree, that is top notch!
Thanks for the kind words.
The concept is straight forward – the case is built around the heat sinks, they are 300x150mm (Fischer KL-271). If the heat sinks are the sides we obviously need 4 other elements – lid, bottom, front and back. Front is 10mm aluminium, the other 3 parts are 6mm. Everything is CNC machined, shot blasted (glass pearls) and anodized. Not painted etc.. There are washers between the bottom/lid and the heat sinks to allow air exchange. The principle is copied from Chris “Elfenreiters” cases who is also one of the two guys who organized the PCB group buy etc.. You can find more information in the thread in the German Analogforum here.
Here are the pictures of Chris’ cases (registration required).
In the same thread you will see some pictures of my cases in different stages of “production”.
E.G. here after shot blasting before anodizing:
So – the concept is stolen 🙂D), the details like engravings, bevels, logos, exact sizes etc. have been drafted by me and executed perfectly by a guy I know. I think this really makes the difference – it’s basically done perfectly. It’s not easy to get this kind of perfect result no matter how much money you are prepared to spend. You need to find somebody (or be somebody) who not only has the technical capabilities and skills but also really cares. 🙂
Best Regards
Sven
PS: I do have nightmares about accidentally scratching it! 😀
The concept is straight forward – the case is built around the heat sinks, they are 300x150mm (Fischer KL-271). If the heat sinks are the sides we obviously need 4 other elements – lid, bottom, front and back. Front is 10mm aluminium, the other 3 parts are 6mm. Everything is CNC machined, shot blasted (glass pearls) and anodized. Not painted etc.. There are washers between the bottom/lid and the heat sinks to allow air exchange. The principle is copied from Chris “Elfenreiters” cases who is also one of the two guys who organized the PCB group buy etc.. You can find more information in the thread in the German Analogforum here.
Here are the pictures of Chris’ cases (registration required).
In the same thread you will see some pictures of my cases in different stages of “production”.
E.G. here after shot blasting before anodizing:
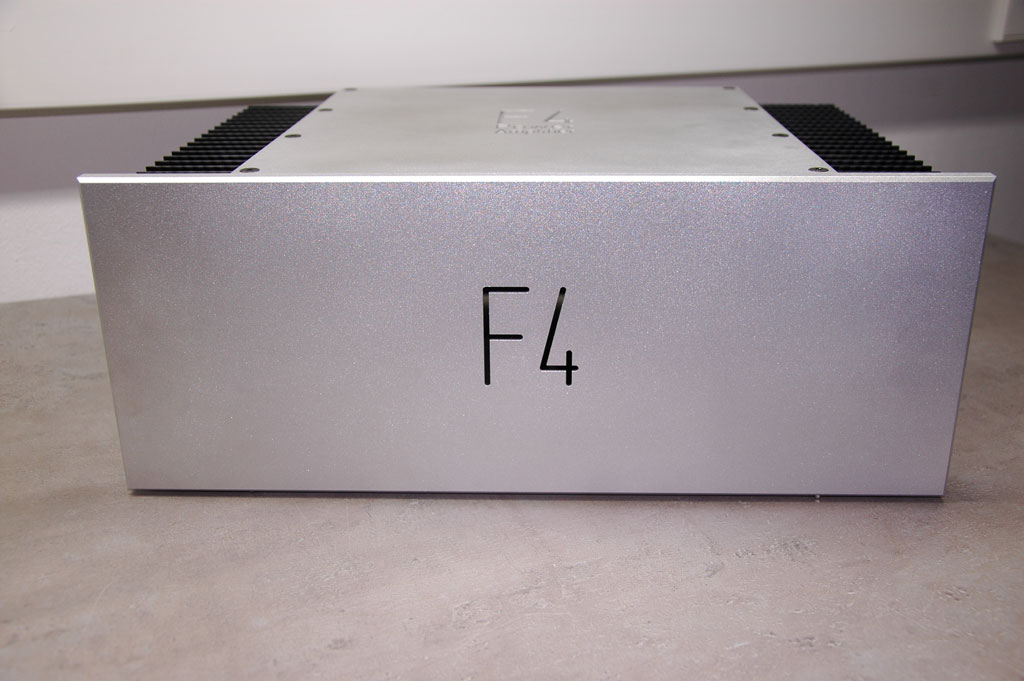
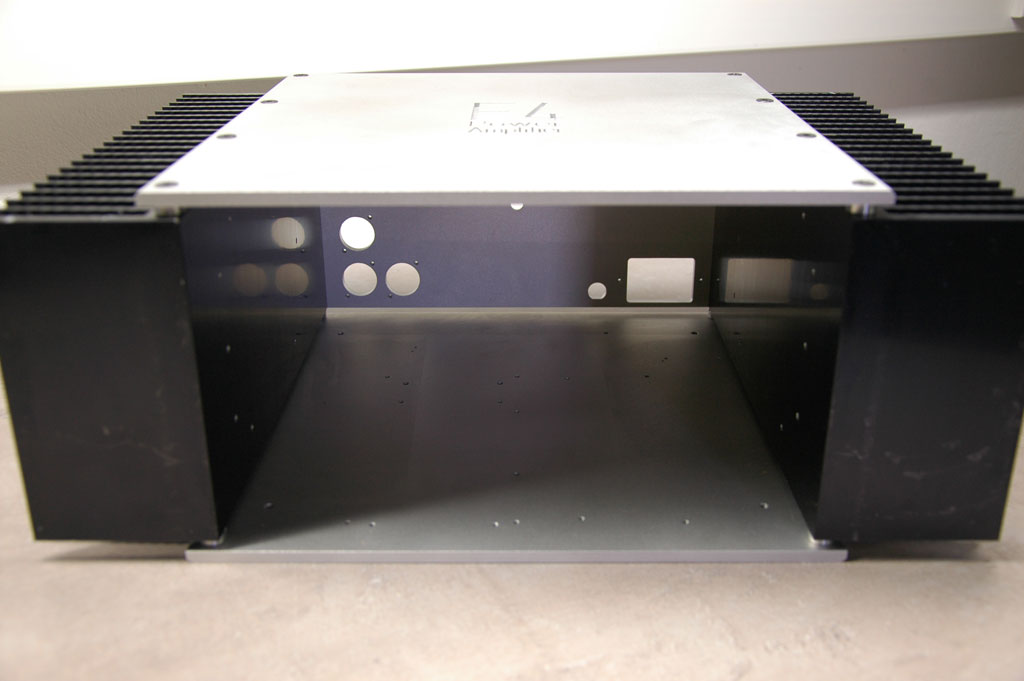
An externally hosted image should be here but it was not working when we last tested it.
So – the concept is stolen 🙂D), the details like engravings, bevels, logos, exact sizes etc. have been drafted by me and executed perfectly by a guy I know. I think this really makes the difference – it’s basically done perfectly. It’s not easy to get this kind of perfect result no matter how much money you are prepared to spend. You need to find somebody (or be somebody) who not only has the technical capabilities and skills but also really cares. 🙂
Best Regards
Sven
PS: I do have nightmares about accidentally scratching it! 😀
... the heat sinks, they are 300x150mm (Fischer KL-271).
Awesome looking amps!!! Well done!! 🙂
Where have you bought the heat sinks? 😕
Apologies, the heat sinks are not Fischer, they are Seifert Electronic KL-271. I ordered them directly from Seifert. It's been a while. 😀
Sven
PS: If you are not fed up yet - close-up's 🙂 1,2
Sven
PS: If you are not fed up yet - close-up's 🙂 1,2
Last edited:
ZV1
First Pass project I make 🙂 had to say goodbye to my dear IRFP250, so I need a waay better heat sink
I'm not actually a fan of class A amps, but I'm really happy with this little guy🙂
First Pass project I make 🙂 had to say goodbye to my dear IRFP250, so I need a waay better heat sink
I'm not actually a fan of class A amps, but I'm really happy with this little guy🙂
An externally hosted image should be here but it was not working when we last tested it.
An externally hosted image should be here but it was not working when we last tested it.
An externally hosted image should be here but it was not working when we last tested it.
An externally hosted image should be here but it was not working when we last tested it.
Martin, I have been looking at your Picasa albums yesterday. It leaves a bittersweet feeling - most impressive in terms of skills, tools, process and result , depressing in terms of the realization that one will never ever get to that level, not in 100 years…. Thanks for sharing, anyway. 😉Your very well planned and finely crafted F4 looks great from any angle! This is DIY at a truly high level, I like it much!
Martin
Sven
Sven, thanks. These things required hard work and I put a lot of time an dedication into these projects. I think it is the goal and the will to reach it, that can drive people to new levels. In my albums I wanted to share ideas with an instructive aspect about how to make things and overcome difficulies. Hope that it is much more inspiring than depressing!
Martin
Martin
I think it's inspiring!!!
It's always good to know that an inspired, skilled and dedicated individual can outperform the industrial giants at their own game.
It's always good to know that an inspired, skilled and dedicated individual can outperform the industrial giants at their own game.
> the heat sinks are 300x150mm (Fischer KL-271).
Do correct me if I am wrong, but I believe Fischer uses the prefix SK exclusively for their high power extrusions.
Judging from your photos, I belive the extrusions you have are Seifert KL271, which is 300mm wide and 83.5mm deep. It has 21 fins at 14.7mm pitch, and the base plate thickness is 15.5mm.
The closest equivalent from Fischer is SK157, which is also 300x83.5. However it is not 100% compatible, as it has 23 fins at 13.4mm pitch, and a base plate thickness of 12mm.
At 150mm extrusion length, Seifert quotes a Rth of 0.12K/W, and Fischer almost double at 0.25K/W. But in my experience with Seifert Rth figures, they tend to be extremely optimistic. Even the Fischer figures are only true when dT = 80 degC. But I guess most of you would want to operate at dT < 40 degC.
So realistically, one can dissipate about 135W per heatsink, placed vertical and black anodised.
Regards,
Patrick
Do correct me if I am wrong, but I believe Fischer uses the prefix SK exclusively for their high power extrusions.
Judging from your photos, I belive the extrusions you have are Seifert KL271, which is 300mm wide and 83.5mm deep. It has 21 fins at 14.7mm pitch, and the base plate thickness is 15.5mm.
The closest equivalent from Fischer is SK157, which is also 300x83.5. However it is not 100% compatible, as it has 23 fins at 13.4mm pitch, and a base plate thickness of 12mm.
At 150mm extrusion length, Seifert quotes a Rth of 0.12K/W, and Fischer almost double at 0.25K/W. But in my experience with Seifert Rth figures, they tend to be extremely optimistic. Even the Fischer figures are only true when dT = 80 degC. But I guess most of you would want to operate at dT < 40 degC.
So realistically, one can dissipate about 135W per heatsink, placed vertical and black anodised.
Regards,
Patrick
>
So realistically, one can dissipate about 135W per heatsink, placed vertical and black anodised.
Regards,
Patrick
Does anodising the heatsink black helps in dissipating heat?
I did a quick simulation for both sinks based on the published geometries by the manufacturer.
At 40 degC temperature rise, the SK157 will dissipate 145W, and the KL271 135W.
Given the accuracy of the simulation probably identical, perhaps slight advantage to the Fischer due to larger dissipation surfaces (more fins).
Patrick
PS for this particular sink size, the optimum fin pitch is 10mm.
.
At 40 degC temperature rise, the SK157 will dissipate 145W, and the KL271 135W.
Given the accuracy of the simulation probably identical, perhaps slight advantage to the Fischer due to larger dissipation surfaces (more fins).
Patrick
PS for this particular sink size, the optimum fin pitch is 10mm.
.
Last edited:
40C @ 140W is equivalent to 0.29C/W @ dt=40C
Using a DF factor of 1.2 to convert to dt=75C then Rth s-a comes out at ~0.24C/W
It would seem that the Rth s-a of a 150mm length of this heatsink is not well represented by either manufacturer.
Using a DF factor of 1.2 to convert to dt=75C then Rth s-a comes out at ~0.24C/W
It would seem that the Rth s-a of a 150mm length of this heatsink is not well represented by either manufacturer.
Fischer did quote 0.25K/W (read from a graph).
I thought that is pretty close to the 0.24C/W that you mentioned above ??
Seifert is of course way out.
Patrick
I thought that is pretty close to the 0.24C/W that you mentioned above ??
Seifert is of course way out.
Patrick
- Home
- Amplifiers
- Pass Labs
- Pictures of your diy Pass amplifier