Or at least I'm calling it Take 7.
It's really the 3rd completely different cabinet.
Other 'takes' were trying out different size ports or different drivers, etc.
They've all been desinged to go with subs at 100Hz like my previous synergy thread
100Hz two-way synergy project.
That thread ended up turning into this 60x40
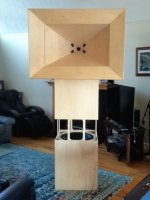
I've truly enjoyed this speaker, to the point I wanted to build another for stereo, but it's too damn big and heavy to move around. About 100 lbs.
One of the biggest joys in audio for me, is being able to move gear around, listen outside, swap stuff around, always making comparisons and learning.
So I've spent a few months researching how to get the synergy goodness, but shed alot of weight.
Anyway here's the outcome.
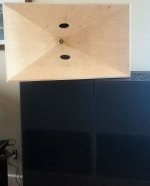
It's a 90x60, that has very close to the same primary horn width and height, but of course less depth due to its wider pattern.
It weighs in at a glorious 45 lbs !!!
Uses two dirt cheap faital 10FE200's as mids, and one not so cheap b&c dcx 464 coax cd, ...but getting the CD down to 500Hz is what lets it work.
I did a few things different from my previous attempts that all tried to adhere to the conventional synergy wisdom.
Biggest change was putting the mid ports in the center of the horn instead of in the corners.
I made a test horn where I could block ports easily and experimented a bit. I couldn't find a compelling case for corner ports, in terms of how the HF and VHF were effected.
That was a peasant surprise really, because I wanted the ports in the horn center as part of a weight reduction design. It allowed the mid drivers to go on the top and bottom in small cavities, and the horn side walls be all the cabinent there is.
Like this
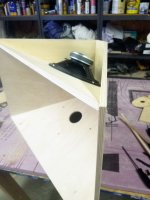
Plus, ports in the center of the horn are just plain easier to make
🙂
Also made a simple box to test port sizes and shapes, port thickness, and how much port frustrum matters. Picture a sealed box where you just lay a plate with various port tries on top, and move it around over the cone.
I used plates out of 12mm BB and thin steel sheet, and ended up choosing a 10:1 compression ratio in terms of hole size.
Surprisingly, I could not find anything to beat a simple round hole aligned with the center of the cone.
Neither could i find a reason to use thin ports, or even do anything to the wood hole other than a little roundover smoothing.
The port holes' center is 7.5" from the throat. Basically, the 10" drivers sit as close to the horn apex as possible, which also puts the port nearly under the center of the cone.
I always have to give sincere thanks to BWaslo for his speadsheet....I simply could not make a synergy without it.
Also need to thank Makita for my track saw Lol. It makes the bevel/miter cuts so easy and true...much better than i can do by table saw and sleds.
Oh, I've found I like to make the horn start at 1.4" square, and not have to round out the walls to mate the CD. It's been easier to add museum wax to the horn corners in the mouth.
Syn7 may or may not get a secondary flare depending on outdoor testing.
I should be able to make a detachable flare like in the first pic fairly easily.
What I really want to do is add a tractrix flare as the secondary flare.
Ala the K-402. I figure the K-402 first 2/3's from the throat is pretty much straight sided conical, and the last 1/3 tractrix. A conatrix or a tractical, depending on which end you look from haha