Illusus said:http://www.mcmaster.com part no. 8560K921
This may work...comes in 12"x12"- so no mistakes!
edit: bad link
I just measured a vinyl record - 11 and 14/16" ya ain't a woofin' when you say no mistakes, would the next step be finding the right machinest (lathe?) to take this 12 X 12" square 3" deep slab on?
8560K921
Clear Cast Acrylic Sheet 3" Thick, 12" X 12"
In stock at $145.08 Each
Hola Marco...
sklimek said:
I just measured a vinyl record - 11 and 14/16" ya ain't a woofin' when you say no mistakes, would the next step be finding the right machinest (lathe?) to take this 12 X 12" square 3" deep slab on?
8560K921
Clear Cast Acrylic Sheet 3" Thick, 12" X 12"
In stock at $145.08 Each
Hola Marco...
If you have to go find help anyway, I'd personally prefer a CNC milling machine over a lathe in this case. Clamping the workpiece in a milling machine is not a problem, and you have no problems of things flying around.
Magura
agent.5 said:If your CNC guy needs to produce a bigger quanty to economize the project, please let us know as a few of us are looking for turntable platter.
OK, I might not be the best guy in the world though being as I used Google - Phoenix - CNC to see what's up. But yeah I'll visit a couple places to try and start to get a feel for what it might take.
Stan
If you are thinking of going that route heres my 2c:
Get your platter machined up, also get a decent thickness piece of stainless or brass to fit the bottom of the platter. Get the machinist to bore holes in the plate and matching ones tapped in the platter so you can screw it all together. Then bore out the platter for the lead shot and use the metal plate to hold it all together. The metal plate will usefully add mass, stability and flywheel effect to the platter.
Fran
Get your platter machined up, also get a decent thickness piece of stainless or brass to fit the bottom of the platter. Get the machinist to bore holes in the plate and matching ones tapped in the platter so you can screw it all together. Then bore out the platter for the lead shot and use the metal plate to hold it all together. The metal plate will usefully add mass, stability and flywheel effect to the platter.
Fran
woodturner-fran said:If you are thinking of going that route heres my 2c:
Get your platter machined up, also get a decent thickness piece of stainless or brass to fit the bottom of the platter. Get the machinist to bore holes in the plate and matching ones tapped in the platter so you can screw it all together. Then bore out the platter for the lead shot and use the metal plate to hold it all together. The metal plate will usefully add mass, stability and flywheel effect to the platter.
Fran
Thanks Fran, I am interested in the possibility of the lead shot bored holes as well if it is not cost prohibited and will convey the info.
I’ve started a folder and will make a trip soon to a couple CNC milling shops in Phoenix and start getting some info to report back. It’s going to be a slow process though as I have many things on my plate right now that is not diy – related.
Stan
Good article from 'The Analog Dept.' on an Teres acrylic platter lead shot upgrade and bearing install:
http://www.theanalogdept.com/teres_platter_upgrade.htm
They're using threaded brass plugs to seal off the 'shot'. I'm hopin' to email Fran as well before I go to a CNC mill to get a fix on his 'flywheel' idea for sealing the shot, mass and stability.
Stan
http://www.theanalogdept.com/teres_platter_upgrade.htm
They're using threaded brass plugs to seal off the 'shot'. I'm hopin' to email Fran as well before I go to a CNC mill to get a fix on his 'flywheel' idea for sealing the shot, mass and stability.
Stan
woodturner-fran said:Kilowattski - you are right - I should have made that clear in my response above. My response above was for the plinth only - not the platter (seeing as the recent posts were about plinths rather than platters).
For the platter, yes, you must evenly space out the holes - 12 of them in mine IIRC and when you drill them drill each one to the same depth. You should be using a scales and filling each one to within 1g of each other. The silicone/oil/whatever is not really a good idea if you are making a wood platter as the oil will eventually seep through. Acrylic though you should be fine.
Regardless of whether its the platter or the plinth balance is important. In motorsports you balance the suspension of the car, its called corner balancing where you evenly distribute the weight of the vehicle to all four tires. The resonance of the car is lowered and you run faster laps and less tire wear. I have a VPI HW19, the weight of the motor on the upper left corner, grossly unbalances the table. Putting a counterbalance on the opposing corner, reduces resonance resulting in a quieter table. You could implement this technique, using a scale. You could either adjust via adding weight or moving your footers to evenly distribute the weight. YMMV.
As for the platter, again taking from motorsports. You could use static balancing. You would balance the platter on a point and add weight accordingly keeping balance. There are miniature versions of this tool, comes with a bubble level. I'm sure you'll find something in ebay.
Anyway, all this talk has inspired me to build from scratch as well. I'm taking my woodworking equipment out of storage. I figure all I need is a router table, bandsaw, lathe, drill press and if you don't mind, here's a picture of my work.
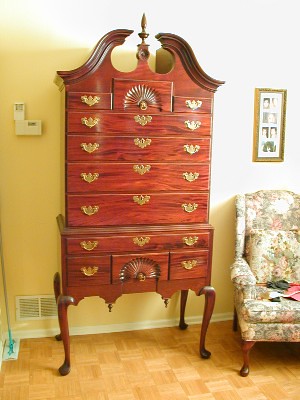
I bought two of these cutting boards, made up of little cubes of beachwood:
(not exactly the same)
Would that be usable for a TT base, considering stability etc?
BTW there is no way I can find lead shot here in the Netherlands, apparently it can't be sold anymore. Any dutchies who can help me out?
Thanks
An externally hosted image should be here but it was not working when we last tested it.
(not exactly the same)
Would that be usable for a TT base, considering stability etc?
BTW there is no way I can find lead shot here in the Netherlands, apparently it can't be sold anymore. Any dutchies who can help me out?
Thanks
Lead shot are banned throughout most of Europe, I think -- for environmental reasons. Should be some leftovers though. Physics supply co's also used to carry led shot or grains.
You can make your own fairly easily, if you can get lead though.. thatchers usually stock lead in plates, and metal suppliers have ingots. All you need is a blow torch, a suitable sieve of some kind and a bucket of water. Extreme accuracy or uniformity is not necesseary for our purpose. Google "make lead shot"......
EDIT: Just googled it myself gain- Seems like diver's supplies might also be a possible source...
You can make your own fairly easily, if you can get lead though.. thatchers usually stock lead in plates, and metal suppliers have ingots. All you need is a blow torch, a suitable sieve of some kind and a bucket of water. Extreme accuracy or uniformity is not necesseary for our purpose. Google "make lead shot"......
EDIT: Just googled it myself gain- Seems like diver's supplies might also be a possible source...
This is a link to a small machine to make lead shot. should give some ideas...
http://www.svartkrutt.net/engshotmaker.php
and indeed you can use an MDF mold, - but if you need 10-20 kgs, that's going to take some time!
Making shavings with a plane, a rough file ....
- a surform file or plane should do the trick! We don't need round balls , do we? Thin shavings will do just as well, I think...
There used to be something called lead sand, too.......
And of course, steel shot and vismut shot are the hunters replacements for lead, - at a higher price!
http://www.svartkrutt.net/engshotmaker.php
and indeed you can use an MDF mold, - but if you need 10-20 kgs, that's going to take some time!
Making shavings with a plane, a rough file ....
- a surform file or plane should do the trick! We don't need round balls , do we? Thin shavings will do just as well, I think...
There used to be something called lead sand, too.......
And of course, steel shot and vismut shot are the hunters replacements for lead, - at a higher price!
Sorry to burst all your bubbles, but I've been there and done that with the lead shot!!!!
I tried making my own and, well, you get lumps rather than shot.
I got mine from a guy in teh UK, I think he was called "clay and game reloaders"
link
Yes, its expensive, and yes shipping is horrendous.
The decision is yours!
Fran
I tried making my own and, well, you get lumps rather than shot.
I got mine from a guy in teh UK, I think he was called "clay and game reloaders"
link
Yes, its expensive, and yes shipping is horrendous.
The decision is yours!
Fran
Well, - yes, there should still be sources for lead shot, as the ban here in Norway is just two years old, but the ban here not only deals with lead shot for hunting, - it actually says " all uses, trade and import...." - but in relations to EU, Norway as always seems to more catholic than the Pope!
And as you point to in your link, there are alternatives. Question is then : Do we only want it for the extra mass only, or do we need the inherent damping properties of lead?
The trick in making your own, though, is that the drip hole needs to be conciderably smaller than the shot you're making. Gauge 6 shot is appx 2.5mm, and needs a drip hole less than 1mm.
And as you point to in your link, there are alternatives. Question is then : Do we only want it for the extra mass only, or do we need the inherent damping properties of lead?
The trick in making your own, though, is that the drip hole needs to be conciderably smaller than the shot you're making. Gauge 6 shot is appx 2.5mm, and needs a drip hole less than 1mm.
YNWOAN said:Well, you never know - at least I didn't advise against consuming it![]()
You're right, and I wasn't offended
Oh, and the chopping block is an excellent place to start with regard to making a plinth or base.
Okay thanks, so far I've been using two 1 cm plywood sheets of different kinds glued together, but that was only temporarily, it's time to move on. (and make something with a higher WAF/less DIY factor
Miniwatt said:
You're right, and I wasn't offendedBetter safe than sorry after all..
Okay thanks, so far I've been using two 1 cm plywood sheets of different kinds glued together, but that was only temporarily, it's time to move on. (and make something with a higher WAF/less DIY factor)
I think that the chopping block would make an excellent plinth. If your wife doesn't like it you can always cover it with a nice veneer.
- Status
- This old topic is closed. If you want to reopen this topic, contact a moderator using the "Report Post" button.
- Home
- Source & Line
- Analogue Source
- My DIY Teres Turntable