your concept
shin
your design is elegant to say the least you must have put a great deal of time into just getting the volumes right for your driver selection let alone the drafting part of your thoughts
it would be fair to say that you would have minimal problems adapting your drafting skills to the proposed CNC machine that is in the pipeline
some questions for you
if your internal bracing is so tight how will you tie in the rebates to the side panels and also incorparate the attenuating material for the damping
from the drafts it appears that both top and bottom woofers share the same volume so are they wired in serial push pull or parallal or some other configuration
do you plan to tri amp bi amp or other will the crossover be active or passive or a combo
if passive it will be fun getting that stuff in side your cabinets
best of luck on your project and a successful new year to you
speedie
shin
your design is elegant to say the least you must have put a great deal of time into just getting the volumes right for your driver selection let alone the drafting part of your thoughts
it would be fair to say that you would have minimal problems adapting your drafting skills to the proposed CNC machine that is in the pipeline
some questions for you
if your internal bracing is so tight how will you tie in the rebates to the side panels and also incorparate the attenuating material for the damping
from the drafts it appears that both top and bottom woofers share the same volume so are they wired in serial push pull or parallal or some other configuration
do you plan to tri amp bi amp or other will the crossover be active or passive or a combo
if passive it will be fun getting that stuff in side your cabinets
best of luck on your project and a successful new year to you
speedie
Hi Ant - long time no... err... chat.
Just spotted this thread today. New project looks great - very high standard as always.
Very pleased/jealous to see you've taken the plunge on a CNC machine. You'll find it'll opens up all sorts of design ideas that wouldn't necessarily be practical when done by hand. My (roughly) 2ft x 3.5ft machine is a bit limiting when cutting bigger (or many) parts, so you'll find a 4ft^2 system great. Out of interest, what's the machine you've gone for?
I don't know how much you've played with CNC before, so a few tips/ideas:
Just spotted this thread today. New project looks great - very high standard as always.
Very pleased/jealous to see you've taken the plunge on a CNC machine. You'll find it'll opens up all sorts of design ideas that wouldn't necessarily be practical when done by hand. My (roughly) 2ft x 3.5ft machine is a bit limiting when cutting bigger (or many) parts, so you'll find a 4ft^2 system great. Out of interest, what's the machine you've gone for?
I don't know how much you've played with CNC before, so a few tips/ideas:
- For 2D cutting (shapes, pockets) I've stopped cutting through into a spoil board and leaving tabs. You have to clean up the tabs anyway (trimming bit on a router table) so I now favour onion skinning: leaving a thin (1-2mm) layer of material on the cut out path. I find it ultimately gives a more even edge finish, and doesn't cut into a spoil board. This also leaves more scope for easier vacuum clamping.
- 2.5D machining - yea, it takes a long time! Cutting just one example and making a mold for casting is not a bad idea. I found a local pro CNC shop that uses 100mm CNC modelling board - I get lots of pretty large pieces for free, as they consider offcuts as waste. You can glue them together, they're easy to cut/sand, and they're great for making molds. A powder additive mixed into casting resin can make it cheaper to cast as it bulks it out a bit. Silicone molding rubber is pricey though.
- Assuming you don't already have software - Mach 3 is a great controller app, and I've found SheetCAM is good for 2D generating of gcode from CAD files.
- Milling MDF is dust central. If I had the space I'd create a separate room just for the CNC machine, let it cut, then enter the room with a respirator and clean up. As it is I'm running a dust extractor all the time the machine cuts (as the machine's in the garage). Works well, but it's not very neighbour (or electricity bill) friendly.
For 2D cutting (shapes, pockets) I've stopped cutting through into a spoil board and leaving tabs. You have to clean up the tabs anyway (trimming bit on a router table) so I now favour onion skinning: leaving a thin (1-2mm) layer of material on the cut out path. I find it ultimately gives a more even edge finish, and doesn't cut into a spoil board. This also leaves more scope for easier vacuum clamping.
Hey Sploo.
Thanks for the tip.
Assuming you don't already have software - Mach 3 is a great controller app, and I've found SheetCAM is good for 2D generating of gcode from CAD files.
The machine comes with Mach3 although I'm not familiar with it. That's something I'll have to learn.
Milling MDF is dust central. If I had the space I'd create a separate room just for the CNC machine, let it cut, then enter the room with a respirator and clean up. As it is I'm running a dust extractor all the time the machine cuts (as the machine's in the garage). Works well, but it's not very neighbour (or electricity bill) friendly.
I know what you mean. Even a hand held router cutting a couple of holes creates a lot of dust so a CNC machine would be even worse. I anticipated this and ordered the machine with a dust/noise enclosure that cover the working area. You can hookup a dust shoe onto the milling head attachment and extract from there and also catch the airborne particles within the enclosure via a second hose. This will keep the dust down to healthy levels.
I always want to try audiotechnology c-quence. The poly cone keeps me from using them.
Cheers
Henry
you can get the C-Quenze with carbon/paper sandwich cone option, not just the flex units. i'm looking at them now, but oh my $$$
@ Shin: i'm going to ignore the everything sounds the same pundits and ask the question since you have compared them in the same cabinet and with digital XO, i'm also using digital 2 way, but with multichannel dac and allocator.
so the question is, how did you find the C-Quenze vs SS revelator? see i have some 18W8531 G00 and i was looking at the C-Quenze 18 H 52 17 06 SD KA P (symetric drive, carbon paper sandwich cone and Kapton/alloy former) as a possible cost no object alternative to try in the same build. do you have any comment?
i'm not going to ask a silly question like is it worth more than twice the money, because we are at the pointy end of the market and value is relative. but i dont see many comparisons of these drivers, or really any descriptions of the upgraded C-Quenze at all, so i would very much like your input.
the comments on previous pages of all drivers in the same exact setup are imo a bit inane, it will never happen, you are posing a theoretical situation that will never occur. also transducers have been described by most as having the most profound effect on sound. people (not me) say transports of a minimum quality, DACs of sufficient quality, amps of a sufficient quality, bits of a sufficient quality, conductors of a sufficient quality and now transducers of a sufficient quality, all sound the same. Might I ask what those people are doing here at this forum? please leave us and go live in your world of sufficiently high quality mediocrity.
Some of the above comments in the right context have merit, but seriously we are all different people with different ideas of what constitutes good sound, why would we ever WANT them all to sound the same?
Last edited:
BTW Shin, i'm very much looking forward to your realisations, now you have such a powerful tool to make the vision a reality. If that means that you will now be moving into a more professional landscape that constitutes less sharing of your process and ideas, i can only wish you well and thank you for the insights so far
Hey Sploo.
Thanks for the tip.
...
The machine comes with Mach3 although I'm not familiar with it. That's something I'll have to learn.
...
You can hookup a dust shoe onto the milling head attachment
Be really careful with hold downs, bolts etc. Good clamping of sheets is a must - you can easily drag a 4x2ft 3/4" thick sheet of MDF across a table if it's not well held down.
Also be really careful when it comes to tool paths vs. clamps. Let's just say that a 1/4" up-cut spiral solid carbide bit doing 18k rpm and travelling at 2" per second is 'interesting' when it clips a 6mm steel bolt that's being used to hold down parts
Mach3 is great. The set up takes time, but it's a cracking piece of software and well worth the cash. Good motor tuning is crucial though for the best results. Is the machine a K2, ShopSabre, something else?
The enclosure is a great idea. Just don't have the space for it in my garage. BTW I built a shoe for mine, as the original was a bit too puny:
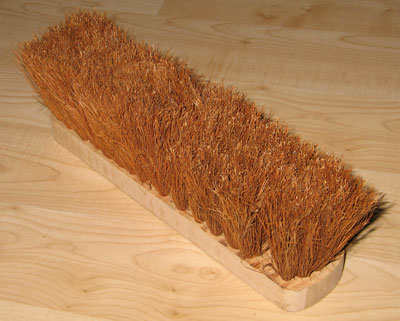
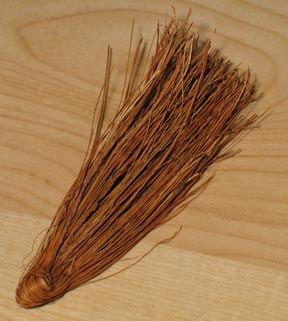
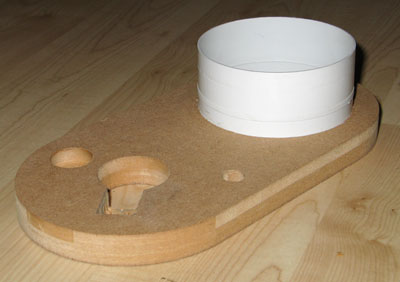
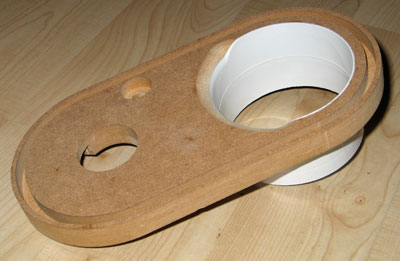
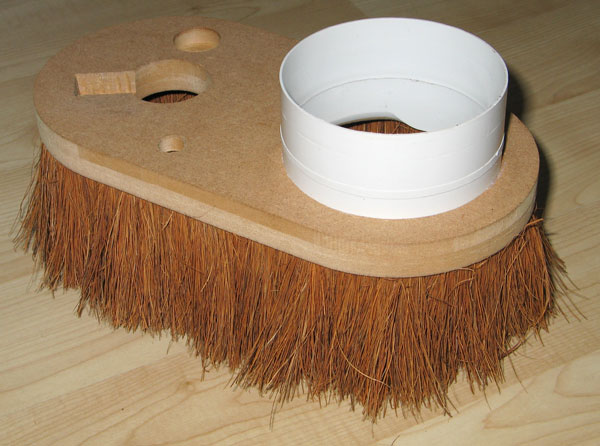
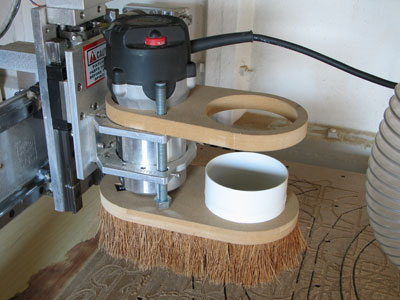
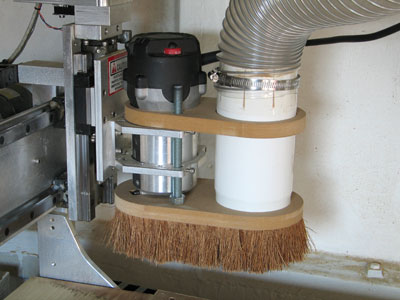
Good dust extraction is a must. I'd recommend at least a 3hp blower. If you can fit it in (I can't) then a cyclone separator (Bill's Cyclone Dust Collection Research - Home Page) would be a great idea.
so the question is, how did you find the C-Quenze vs SS revelator? see i have some 18W8531 G00 and i was looking at the C-Quenze 18 H 52 17 06 SD KA P (symetric drive, carbon paper sandwich cone and Kapton/alloy former) as a possible cost no object alternative to try in the same build. do you have any comment?
Quick note to say you can't get the sandwich cone in anything less than the 10" at the moment. I believe they're working on the 15" version though.
But ignoring that detail I'd say the two are well matched. With the AT you get the chance to customise the TS to a certain extent which is always a nice option to have. The AT is better made but the SS is fine in this area too. Generally AT are easier to drive. SS rev. have more extension in general and sound better in the bass to my ear.
I don't yet have the upgraded c-quenze with me right now. So can't comment on those yet.
BTW Shin, do you perchance have a DXF or similar of the revelator 18W/8531 G00? i'm about to start modelling it in the next day or 2 to 'test fit' the enclosure, but a ready made model would be superb!!
I do have a basic cosmetic only model. This is just the mounting flange and cone. The basket and motor are omitted.
Send me your email address via PM and I'll send you it. DXF format is usually 2D so you'll need to specify which 3D format you'd prefer.
Also be really careful when it comes to tool paths vs. clamps. Let's just say that a 1/4" up-cut spiral solid carbide bit doing 18k rpm and travelling at 2" per second is 'interesting' when it clips a 6mm steel bolt that's being used to hold down parts![]()
Bet that's interesting when that happens.
Is the machine a K2, ShopSabre, something else?
The machine is a Strike one. A relatively new company in the UK and one of the few that offers reasonable prices yet doesn't skimp on the quality.
The website is incoming but here's the address anyway:
Strikecncrouters.com
I almost went for a High-Z T1400 from CNC-Step. But a few things put me off. First off they're in Germany so shipping was expensive. Other stuff that swayed my decision were 110mm of Z axis travel vs. 200mm on the Strike, no dust enclosure option and a more awkward 1400mm x 800mm working area which doesn't lend itself to standard size boards like 4x4ft
But by all accounts they look like good budget machines and I do like the storage built into the stand. Great for putting the PC in there to keep it from dust. I'll probably do something similar on the Strike:
I don't have a picture just yet of the Strike but will post plenty once it arrives.
BTW I built a shoe for mine, as the original was a bit too puny
Nice work there.
Last edited:
Bet that's interesting when that happens.
Indeed. The cutter lost, but only after chewing off most of the head of the bolt (that's a 12mm dia, 5mm high dome of steel). Even cooler... err scarier... was the fact the rotation of the tool unscrewed the bolt and lifted it out of the table surface for an even more 'crunchy' end result. Joy
The machine is a Strike one. A relatively new company in the UK and one of the few that offers reasonable prices yet doesn't skimp on the quality...
...I almost went for a High-Z T1400 from CNC-Step
Interesting. Haven't heard of them.
I did look at CNC-Step when I was after a machine, but decided their stuff looked a bit flimsy, had fairly low cutting speeds, and tended to use only stepper motors. For less than the cost of one of their systems I was able to import (and pay many different taxes on) a machine from the US (a servo motor based K2 KG-3925). That was when you got nearly 2 USD to 1 GBP though.
200mm Z should be useful - though it'll have to be sturdy to not flop about. Looking forward to seeing pics!
The latest Aurora iteration but I'm still playing about with bits:
Strike are pretty busy so the CNC has been pushed back towards the end of January.
Any recommendation on CAM packages?
I use Solidworks 2011 and I've noticed there are a number of plugins. This is seems the most logical step as your working within two programs that are integrated and (hopefully) both understand one another.
The two I've been looking at are SolidCAM and MasterCAM. I've seen some fairly reasonable prices for used copies on ebay and they both appear to be good. No idea which is more suited to someone starting out though.
As mentioned before Mach3 will be running the CNC.
Strike are pretty busy so the CNC has been pushed back towards the end of January.
Any recommendation on CAM packages?
I use Solidworks 2011 and I've noticed there are a number of plugins. This is seems the most logical step as your working within two programs that are integrated and (hopefully) both understand one another.
The two I've been looking at are SolidCAM and MasterCAM. I've seen some fairly reasonable prices for used copies on ebay and they both appear to be good. No idea which is more suited to someone starting out though.
As mentioned before Mach3 will be running the CNC.
Attachments
Have you got pricing on either of those packages yet? Might end up being more than the cost of the machine 
I have a seat of NX cam 7.5 and Esprit 2011. I prefer Esprit. Looked at all the usual suspects like Mastercam, etc.
I don't know what people usually use for routers, but one-cnc is very well priced and should do everything you need. (2.5 axis should be fine for what you are doing, simultaneous 3 axis would not be necessary)
Sent from my Sony Tablet S using Tapatalk
I have a seat of NX cam 7.5 and Esprit 2011. I prefer Esprit. Looked at all the usual suspects like Mastercam, etc.
I don't know what people usually use for routers, but one-cnc is very well priced and should do everything you need. (2.5 axis should be fine for what you are doing, simultaneous 3 axis would not be necessary)
Sent from my Sony Tablet S using Tapatalk
Have you got pricing on either of those packages yet? Might end up being more than the cost of the machine![]()
Yes they come up on ebay fairly regularly with the dongle and manuals. They're not the latest versions I'm looking at but as a beginner I don't mind having a few year old version. Prices seem to be around the £200-500 mark depending on the version number.
What attracted me to those two (MasterCAM & SolidCAM) were that they plug directly into Solidworks and you then have one environment for both CAD and CAM. The two programs works together as one so to speak.
I use NX7.5 CAD and CAM (at work) for my DIY CNC router (at home).
I'm making these, using rear mounted Focal drivers. A PC will be the crossover (starting with Allocator, then maybe Soundeasy UE3 or Audiolense), playing around with perfect phase.
If I don't like the Audiom bumps on the tweeter, I'll machine a baffle without the bumps. If the open midrange doesn't work out, I'll box in the side walls.
The speaker is modular, 3 boxes, so I can move it, but it will also allow me to try different configurations.
As for CAD/CAM, I can use NX, Solidworks and Pro/E. I like NX best, for speakers it's magic as you can quickly build single solid model driving the concept, then cut and shut associative panels from it. Then blow them out to individual parts for machining. Creating internal volumes is easy too.
Solidworks is reasonably flexible for this too, but Pro/E is woeful. You'll spend all day playing at building it panel by panel and mucking with assy's rather than getting the job done.
It's not how I use NX for work projects, but it's quick and gets the job done.
I can only use NX CAM, but I have heard good things about Solidworks+Mastercam.
I'll start my own thread, one of these days.
Mark
I'm making these, using rear mounted Focal drivers. A PC will be the crossover (starting with Allocator, then maybe Soundeasy UE3 or Audiolense), playing around with perfect phase.
If I don't like the Audiom bumps on the tweeter, I'll machine a baffle without the bumps. If the open midrange doesn't work out, I'll box in the side walls.
The speaker is modular, 3 boxes, so I can move it, but it will also allow me to try different configurations.
As for CAD/CAM, I can use NX, Solidworks and Pro/E. I like NX best, for speakers it's magic as you can quickly build single solid model driving the concept, then cut and shut associative panels from it. Then blow them out to individual parts for machining. Creating internal volumes is easy too.
Solidworks is reasonably flexible for this too, but Pro/E is woeful. You'll spend all day playing at building it panel by panel and mucking with assy's rather than getting the job done.
It's not how I use NX for work projects, but it's quick and gets the job done.
I can only use NX CAM, but I have heard good things about Solidworks+Mastercam.
I'll start my own thread, one of these days.
Mark
Attachments
Yes they come up on ebay fairly regularly with the dongle and manuals. They're not the latest versions I'm looking at but as a beginner I don't mind having a few year old version. Prices seem to be around the £200-500 mark depending on the version number.
What attracted me to those two (MasterCAM & SolidCAM) were that they plug directly into Solidworks and you then have one environment for both CAD and CAM. The two programs works together as one so to speak.
I'd be very wary of someone selling software packages that start at $10k (if your lucky) for that sort of money. Way more likely to be cracked versions. Definitely contact your local reseller to make sure it's legit.
Sent from my Sony Tablet S using Tapatalk
I'd be very wary of someone selling software packages that start at $10k (if your lucky) for that sort of money. Way more likely to be cracked versions. Definitely contact your local reseller to make sure it's legit.
Indeed. I'd be a bit careful. I think a lot of software licenses don't allow reselling, so whilst you probably wouldn't end up facing the law, I doubt you'd get any support.
As a poor DIY home builder
I have an older version (not the new SheetCAM TNG) but I've found it to be very good and very simple. Les (who I believe is the developer) has always been great in fixing bugs and giving support. The latest version is £110, and based on the one I run, should be very good value. For my workflow - it takes DXF, and drops out gcode with the supplied Mach post processor. Simples.
For 3D milling, I've played with eval versions of MeshCAM, with decent results. I've not done enough with it to make a judgement, but it's where I'd start if I wanted to do some 3D work. Currently $175.
I'd be very wary of someone selling software packages that start at $10k (if your lucky) for that sort of money. Way more likely to be cracked versions. Definitely contact your local reseller to make sure it's legit.
Sent from my Sony Tablet S using Tapatalk
But the software pirates wouldn't be able to copy the dongle?
The couple of auctions I've seen look legit. I understand I'll get no support as these version are a few years old and you generally need to pay a yearly fee like they do at work for Solidworks.
But the software pirates wouldn't be able to copy the dongle?.
Probably not. And quite probably legit originals, but probably violating some T&Cs of the vendor. Worth checking... it's not impossible they'll support someone that bought it second hand (possibly with you having to pay for support) but probably unlikely.
I've not used a system with an all-in-one design and CAM interface, so couldn't comment how much 'worse' the separate packages are, but it does me OK.
All of these (including the dino) were done with free/cheap packages (i.e. ProgeCAD Lite + SheetCAM + Mach 3):
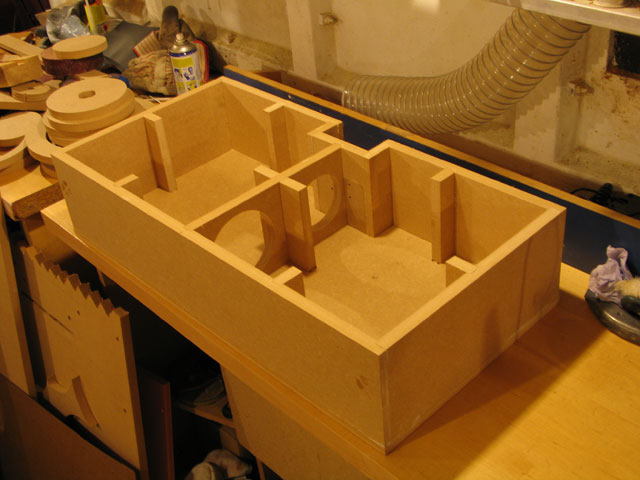
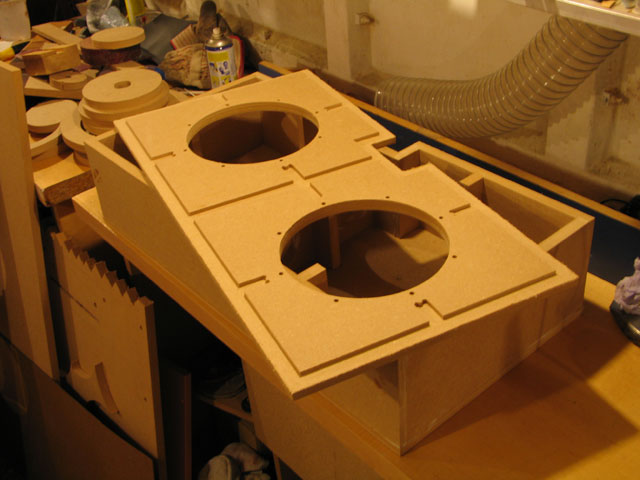
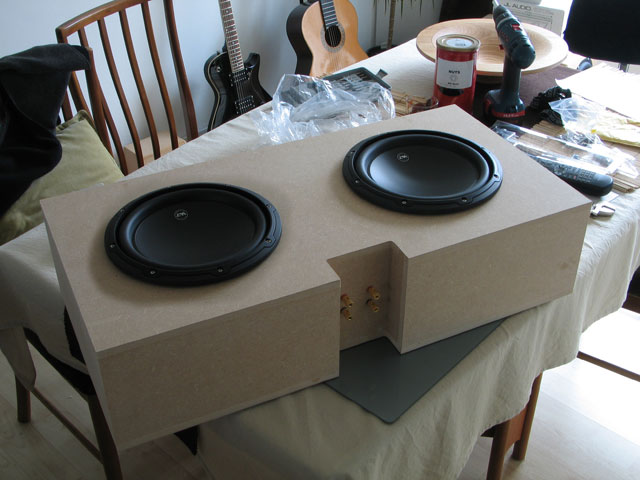
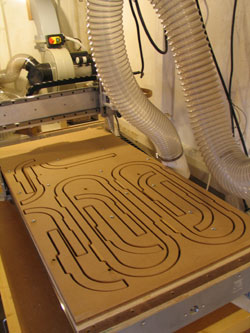

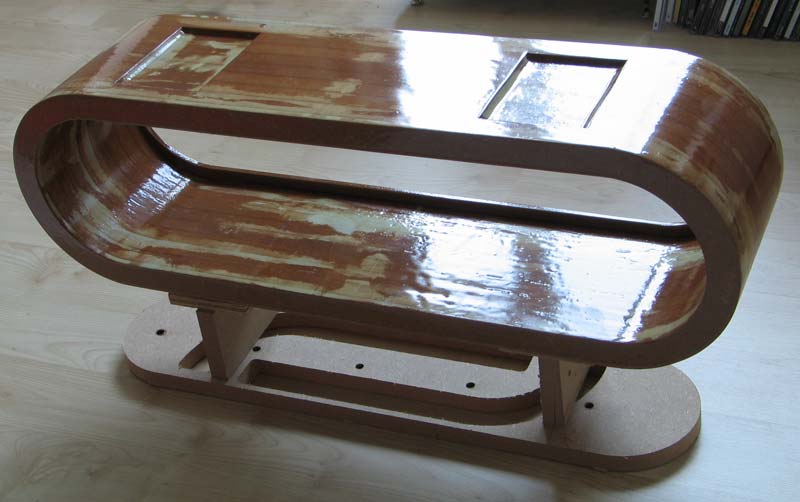

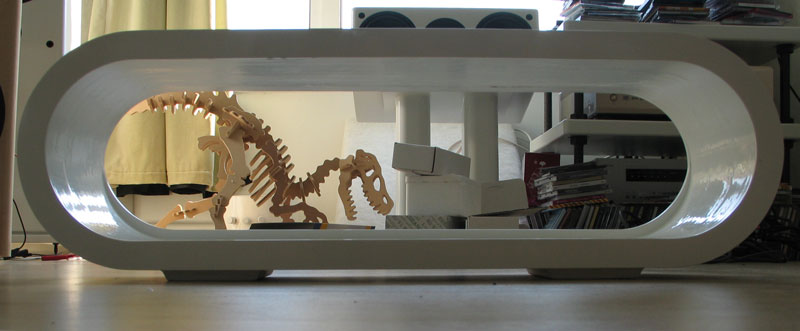
Longball
Probably not. And quite probably legit originals, but probably violating some T&Cs of the vendor. Worth checking... it's not impossible they'll support someone that bought it second hand (possibly with you having to pay for support) but probably unlikely.
Ah I see what your getting at now.
I know of some cases where the software developer retains the rights to your copy of the software. All your money ever pays for is the right to use it and as soon as you stop paying your license fee the program is being used illegally.
This is something I'll look into as I don't want to pay for software I can't use.
I've not used a system with an all-in-one design and CAM interface, so couldn't comment how much 'worse' the separate packages are, but it does me OK.
Neither have I but from the video's I've seen of both SolidCAM and MasterCAM it does seem very intuitive to have both the CAM and CAD side combined. Because Solidworks can be based around parametric parts, should you change one of these parts then the tool paths auto update too. Things like that for example.
All of these (including the dino) were done with free/cheap packages (i.e. ProgeCAD Lite + SheetCAM + Mach 3):
That combo seems to do all that my relatively simple requirements demand. However we use Solidworks at work so I've essentially got a company license that I'm able to use on my home PC. Same goes for Keyshot (used for rendering). What I don't have access to is the CAM software as this is handled by the production guys, which is a shame. I'll be trying one of the budget options if this second hand route turns out to be bogus. I'd figured a budget of upto £500 for CAM software. What are the main choices in this price range?
- Status
- This old topic is closed. If you want to reopen this topic, contact a moderator using the "Report Post" button.
- Home
- Loudspeakers
- Multi-Way
- Apollo Construction Diary