If you are insistent on using solid wood despite the potential drawbacks, see if you can use quartersawn oak instead of flatsawn. The quartersawn not only has interesting figure, but it will change in thickness instead of width based on wood movement caused by changes in humidity. This will help greatly avoid cracking if you build it correctly. If you know how wood behaves as moves, you can use each piece of wood in a location where it is least likely to have issues. Do a bit of research about wood movement before you start cutting any of your valuable lumber. Or just use plywood, but I sense you would strongly prefer to avoid that.
I've used veneered MDF sides with basic dadoed joints and inset a piece of hardwood several times. It's strong and easy.
Can you source paper backed veneer easily? If so, it would allow you to easily veneer the MDF or basic plywod you'd use for the sides. It typically is available in popular woods, so cherry, oak, walnut, etc.
Can you source paper backed veneer easily? If so, it would allow you to easily veneer the MDF or basic plywod you'd use for the sides. It typically is available in popular woods, so cherry, oak, walnut, etc.
I've used veneered MDF sides with basic dadoed joints and inset a piece of hardwood several times. It's strong and easy.
Can you source paper backed veneer easily? If so, it would allow you to easily veneer the MDF or basic plywod you'd use for the sides. It typically is available in popular woods, so cherry, oak, walnut, etc.
Actually, you just gave me an idea.
As much as I hate veneering, I could veneer some MDF panels and then run a dado along the thickness, spline it to some rounded over hardwood (I have oak and a few bits of walnut in the workshop).
Only issue that gives me is exposed end grain on the MDF as it meets the baffle.
MarkAudio Pluvia 7 Gold drivers
Keep in mind that it is really copper. Haven’t seen any MA gold cones since Gen 1.
dave
...MDF baffle...
But won’t be very stiff. Please lose the MDF.
dave
Actually, you just gave me an idea.
As much as I hate veneering, I could veneer some MDF panels and then run a dado along the thickness, spline it to some rounded over hardwood (I have oak and a few bits of walnut in the workshop).
Only issue that gives me is exposed end grain on the MDF as it meets the baffle.
You can make your front baffle the full width. On the back, assuming you'll rabbet the edges, you can glue on a strip of veneer or hardwood (pre veneering)
FYI, the speakers pictured with 'real' wood baffles aren't solid - they're 'thick' (1/4") veneer on MDF. The teak baffle was MDF trimmed all around with solid teak, and then overlaid with the think veneer.
I included a picture of a chest with massive finger joints to show a joint you don't want. It's a commission I'm currently working on.
Attachments
Actually, you just gave me an idea.
As much as I hate veneering, I could veneer some MDF panels and then run a dado along the thickness, spline it to some rounded over hardwood (I have oak and a few bits of walnut in the workshop).
Only issue that gives me is exposed end grain on the MDF as it meets the baffle.
I forgot to mention that I'd suggest making your dadoed joint first, then veneer, then insert your hardwood piece and trim with a flush trim bit in a router.
But won’t be very stiff. Please lose the MDF.
dave
18mm MDF won't be stiff?
I've used it plenty on other boxes.
If you are insistent on using solid wood despite the potential drawbacks, see if you can use quartersawn oak instead of flatsawn. The quartersawn not only has interesting figure, but it will change in thickness instead of width based on wood movement caused by changes in humidity. This will help greatly avoid cracking if you build it correctly. If you know how wood behaves as moves, you can use each piece of wood in a location where it is least likely to have issues. Do a bit of research about wood movement before you start cutting any of your valuable lumber. Or just use plywood, but I sense you would strongly prefer to avoid that.
I get everyone loves plywood. But cost is way too high.
How much is the difference given driver cost, other costs and your labour. Likely not much in the scheme of things.
I too have used lots of MDF, gave it up a couple decades ago. I ask, why put all that effort into a box made from inferior material.
If you do need a small peiece for just the baffle (why not more solid), contact Stefan at KJF, he likely has some scraps the right size.
MDF is not stiff, it does not have the magic damping assets it is claimed to have, its only asset is that it is cheap.
dave
I too have used lots of MDF, gave it up a couple decades ago. I ask, why put all that effort into a box made from inferior material.
If you do need a small peiece for just the baffle (why not more solid), contact Stefan at KJF, he likely has some scraps the right size.
MDF is not stiff, it does not have the magic damping assets it is claimed to have, its only asset is that it is cheap.
dave
Last edited:
What do you suggest if not steel screws? I think all of my screws (and possibly nails) are steel. I was going to attach the inner batons with 18g brad nails.
Brass screws in Oak.
The tannin corrodes steel/iron and makes a black stain.
Even a steel stopper in a tube of PVA glue - use the glue and you get the black stain!
Also avoid steel wool when finishing, small particles get in the grain.
Perhaps I misunderstood you, when you glue up a larger board from smaller ones, you should alternate the cupping faces. When you look at the end grain one stick should curve up and the one next to it down. Typically a minimum of five sticks per finished piece.
Glue up one board long enough for the entire box. Then pick the better looking face and keep it all sides on the outside. You can cut the front baffle dado while one piece. I would also cut an open dado for the back.
Next up instead of biscuits use a longer spline inside the corners ou the box.
I would also use full length glue blocks on all seams.
Also be sure to use a finish on the inside that matches the outside. That keeps the moisture uniform in the wood to prevent cracking.
I would use a yellow PVA glue. Tape over the outside edges before applying glue. Done properly that might keep glue out of areas where it will stain the finish.
Most importantly oak comes in many types. I would use my local white oak as it is basically waterproof. The best wood has been kiln dried and then seasoned for a year or two before planeing to finished thickness.
Glue up one board long enough for the entire box. Then pick the better looking face and keep it all sides on the outside. You can cut the front baffle dado while one piece. I would also cut an open dado for the back.
Next up instead of biscuits use a longer spline inside the corners ou the box.
I would also use full length glue blocks on all seams.
Also be sure to use a finish on the inside that matches the outside. That keeps the moisture uniform in the wood to prevent cracking.
I would use a yellow PVA glue. Tape over the outside edges before applying glue. Done properly that might keep glue out of areas where it will stain the finish.
Most importantly oak comes in many types. I would use my local white oak as it is basically waterproof. The best wood has been kiln dried and then seasoned for a year or two before planeing to finished thickness.
it is possible to experience cracks later on because of these internal stresses
This is a very real problem, it has happened in at least a couple of the solid builds by Scott (not moose) & Bernie. The Yew uFonkenSET Bernie built for me suffered such, but Bernie was able to fix it.
Real wood can outperform MDF if you use the right techniques and wood. This is because (IMO) MDF is not well suited for loudspeakers.
These handily outpeformed the same in MDF (not a high mark to jump over) — now if we could just figre out how to dramaticallt harden the outer layer, they bruise easily (Western Red Cedar — vert stuff, very light, actally a softwood, has also been found to make very good tonearm wands).
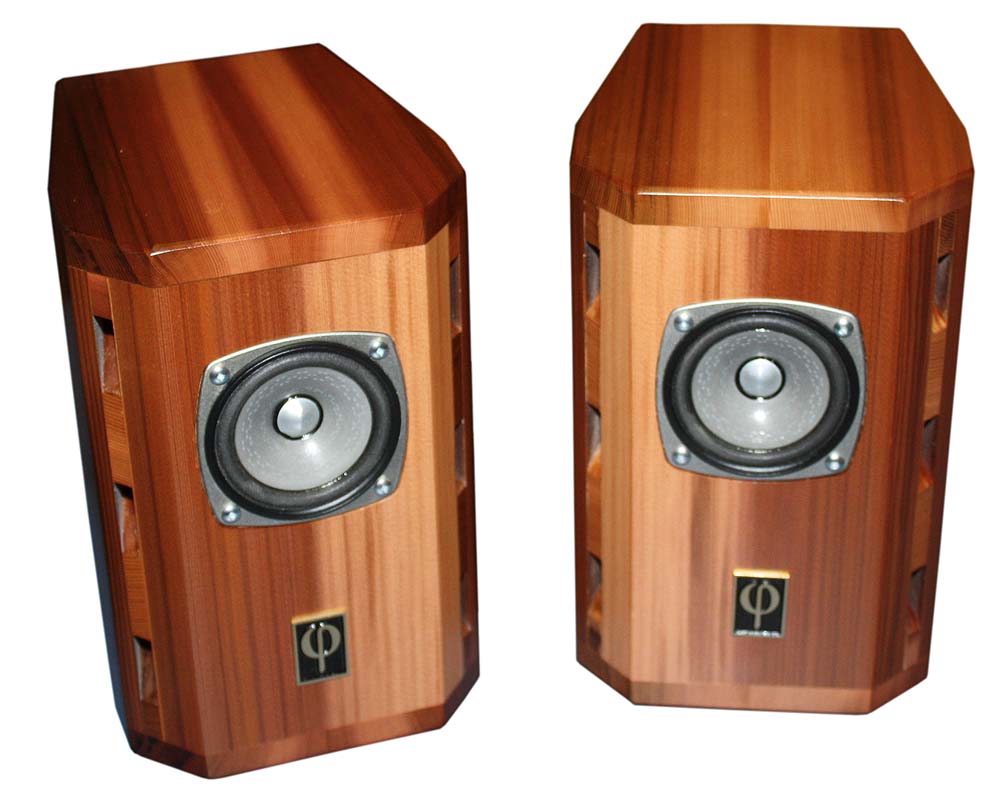
Softwood just means it's deciduous and has nothing to do with resistance to indentation.
I think you meant to say Cedar is a soft wood as well as being a softwood?
How did you determine the comparative performance of the wood vs MDF speakers?
Do you have measurements? I am genuinely interested.
I think you meant to say Cedar is a soft wood as well as being a softwood?
How did you determine the comparative performance of the wood vs MDF speakers?
Do you have measurements? I am genuinely interested.
soft wood as well as being a softwood
Yes.
It is light and stiff, the panels are small, gets the resonances up high where they will very unlikely be excited (ie as if they do not exist). FIve or six pairs of these, ownere love them.
How did you determine the comparative performance of the wood vs MDF speakers?
Listen to a pair of each, listen to the boxes with a mechanics stethoscope. It is as if the MDF has a steady emission of low level time smeard grunge that buries the detail.
dave
I'm glad to read this thread. It is fascinating as I have been thinking about building a set of speakers, and of course thinking about how to eliminate resonance and vibrations from the box.
Have you thought of multiple layers of relatively thin wood, with damping layers between each layer? Then finish up with your finish wood on the outside.
One suggestion might be to use relatively inexpensive tongue and groove spruce interlocking over a solid frame as a first layer. This is a light wood, softwood, and so could absorb vibrations also.
The solid frame could be made of different things, including glued hardwood. Perhaps again multiple layers of wood glued. A few years ago I was experimenting with scraps of wood; I glued together 4 layers of 1/4 inch pine and after it cured cut it into 1x1 inch lengths. They were very strong.
Just thinking out loud..... Any of this help?
Have you thought of multiple layers of relatively thin wood, with damping layers between each layer? Then finish up with your finish wood on the outside.
One suggestion might be to use relatively inexpensive tongue and groove spruce interlocking over a solid frame as a first layer. This is a light wood, softwood, and so could absorb vibrations also.
The solid frame could be made of different things, including glued hardwood. Perhaps again multiple layers of wood glued. A few years ago I was experimenting with scraps of wood; I glued together 4 layers of 1/4 inch pine and after it cured cut it into 1x1 inch lengths. They were very strong.
Just thinking out loud..... Any of this help?
- Home
- Design & Build
- Construction Tips
- Building using solid wood