Need your expert opinion on applying HOMster (usd A700) for home use
Hello Mr. Bateman,
First off, I must Thank You for the very interesting and educational threads on HOM of horns! Through these threads I was introduced and intrigued by Dr. Geddes work--amazing stuff! One day I hope I will be fortunate enough to sample his system and have one in my home 😉
In the meantime, I would like to build my home theater system using USD A-700 horns from my previous car--car was broken into and all my components besides the horns were stolen. Currently I have a Marantz sr6005 receiver on route and the horns and nothing else. My knowledge in audio is elementary at best and I am pretty much stuck. I was wondering if you could recommend a budget setup for this type of system (I plan to go stereo rather than surround sound). Here are some specific questions that I had:
1)Should I use a passive or active crossover?
2)Should the crossover be at the manufacturer's recommendation of 800zHz?
3)Midrange frequency coverage: Do you recommend pairing with some midrange drivers (I can't seem to find any one way midrange bookshelf speakers straight out of the box) or do you think pairing with a sub (or three per Dr. Geddes) would suffice?
I know your time is precious and so any help would be much appreciated!
Thank you in advance,
Fred
Hello Mr. Bateman,
First off, I must Thank You for the very interesting and educational threads on HOM of horns! Through these threads I was introduced and intrigued by Dr. Geddes work--amazing stuff! One day I hope I will be fortunate enough to sample his system and have one in my home 😉
In the meantime, I would like to build my home theater system using USD A-700 horns from my previous car--car was broken into and all my components besides the horns were stolen. Currently I have a Marantz sr6005 receiver on route and the horns and nothing else. My knowledge in audio is elementary at best and I am pretty much stuck. I was wondering if you could recommend a budget setup for this type of system (I plan to go stereo rather than surround sound). Here are some specific questions that I had:
1)Should I use a passive or active crossover?
2)Should the crossover be at the manufacturer's recommendation of 800zHz?
3)Midrange frequency coverage: Do you recommend pairing with some midrange drivers (I can't seem to find any one way midrange bookshelf speakers straight out of the box) or do you think pairing with a sub (or three per Dr. Geddes) would suffice?
I know your time is precious and so any help would be much appreciated!
Thank you in advance,
Fred
I've received a few emails asking about where to buy the reticulated foam that I used in this project. I bought it from McMaster Carr. They stock a gazillion products, so I thought I'd post the part numbers on this thread, in case you guys could use that.
I am using 1/2" reticulated foam. It's part #2195K53 and it's $107 for a lifetime supply. (OK, that's forty square feet, but it's more than I'll ever need.)
I first used 1/4" foam, which is part #2195K52, but I wouldn't recommend that. It's a p.i.t.a. to work with due to requiring twice as many layers.
Geddes has noted that ideally you should use a solid block of the stuff. Pretty sure that would cost hundreds of dollars though.
If I'm not mistaken, plain ol' polyester fiberfill will function in a similar manner as the reticulated foam. The foam has a number of advantages though:
The advantage of polyfill is that you can get it at Wal Mart, any craft store, it's 1/10th the cost, etc
I am using 1/2" reticulated foam. It's part #2195K53 and it's $107 for a lifetime supply. (OK, that's forty square feet, but it's more than I'll ever need.)
I first used 1/4" foam, which is part #2195K52, but I wouldn't recommend that. It's a p.i.t.a. to work with due to requiring twice as many layers.
Geddes has noted that ideally you should use a solid block of the stuff. Pretty sure that would cost hundreds of dollars though.
If I'm not mistaken, plain ol' polyester fiberfill will function in a similar manner as the reticulated foam. The foam has a number of advantages though:
- The density is consistent, so you won't run into a situation where the stuffing on one side isn't consistent with the stuffing on the other
- the foam doesn't 'settle' due to gravity. I've had my Summas for four years now and the foam plug hasn't shrunk or settled or deformed whatsoever. The foam plug looks exactly the same as it did when i bought them.
- If you use fiberfill, you would have to weigh it on a scale to be sure that the amount is the same on both sides, and again, you can't get the density to match as well as you can with the foam.
The advantage of polyfill is that you can get it at Wal Mart, any craft store, it's 1/10th the cost, etc
Polyfill absorbs high frequencies, the reticulated foam has much less HF attenuation.I've received a few emails asking about where to buy the reticulated foam that I used in this project. I bought it from McMaster Carr. They stock a gazillion products, so I thought I'd post the part numbers on this thread, in case you guys could use that.
I am using 1/2" reticulated foam. It's part #2195K53 and it's $107 for a lifetime supply. (OK, that's forty square feet, but it's more than I'll ever need.)
Geddes has noted that ideally you should use a solid block of the stuff. Pretty sure that would cost hundreds of dollars though.
If I'm not mistaken, plain ol' polyester fiberfill will function in a similar manner as the reticulated foam.
The advantage of polyfill is that you can get it at Wal Mart, any craft store, it's 1/10th the cost, etc
Polyfill absorbs high frequencies, the reticulated foam has much less HF attenuation.
An educated guess is that the very open foam is used to literally break up the space between the horn walls to reduce reflections within the horn walls.
If you want thicker pieces look at Home Despot. They sell wedges to insert into eves trough or gutters for keeping leaves out.
An educated guess is that the very open foam is used to literally break up the space between the horn walls to reduce reflections within the horn walls.
The foam is designed to reduce HOM's.
HOM's will have a longer path length than the direct sound.
Because of their longer path length, they will spend more time within the foam, hence be attenuated more than the direct sound.
The foam is designed to reduce HOM's.
HOM's will have a longer path length than the direct sound.
Because of their longer path length, they will spend more time within the foam, hence be attenuated more than the direct sound.
Yep.
See the Youtube video, how a wave is triggered from one end, it reaches the other, then reflects back to the source? Horns and waveguides work the same way. Geddes research indicates that the reflected waves (the higher order modes) are what makes horns and waveguides sound obnoxious.
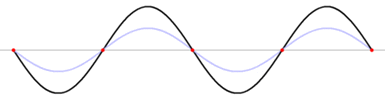
Here's the same idea, but animated
Homster! part 2
Patrick,
Thanks for your work on this. Very interesting.
Do you have a link for part 2? The one posted earlier doesn't seem to work.
Regards,
Paul
Patrick,
Thanks for your work on this. Very interesting.
Do you have a link for part 2? The one posted earlier doesn't seem to work.
Regards,
Paul
I'm in agreement with both of you guys. I just explained the physical mechanism to get the effect you are describing.
High frequency distortion is the real culprit in this discussion call it what you will. And the effects of high frequency distortion can be mitigated by a few means. One of which is intelligent horn design. The other is the method Earl fell back on which is the the foam plug. Call it an intelligent engineering bandaid. It works as attested to by John more than once.
Nice graphic John. The internet has positive uses!
[COLOR=inherit !important]
#s3gt_translate_tooltip_mini { display: none !important; }[/COLOR]
High frequency distortion is the real culprit in this discussion call it what you will. And the effects of high frequency distortion can be mitigated by a few means. One of which is intelligent horn design. The other is the method Earl fell back on which is the the foam plug. Call it an intelligent engineering bandaid. It works as attested to by John more than once.
Nice graphic John. The internet has positive uses!
[COLOR=inherit !important]
#s3gt_translate_tooltip_mini { display: none !important; }[/COLOR]
Mark
To me it is not a choice of A) good horn design or B) foam attenuation, but A and B, because all devices have some HOMs.
To me it is not a choice of A) good horn design or B) foam attenuation, but A and B, because all devices have some HOMs.
I'm in agreement with both of you guys. I just explained the physical mechanism to get the effect you are describing.
High frequency distortion is the real culprit in this discussion call it what you will. And the effects of high frequency distortion can be mitigated by a few means. One of which is intelligent horn design. The other is the method Earl fell back on which is the the foam plug. Call it an intelligent engineering bandaid. It works as attested to by John more than once.
Nice graphic John. The internet has positive uses!
[COLOR=inherit !important]
#s3gt_translate_tooltip_mini { display: none !important; }[/COLOR]
No one has really been able to figure out how to measure HOMs.
But one thing that you CAN measure, is that the foam doesn't have much of a measurable effect on some horns, and on others, IT DOES. For instance, the horn described in this thread, it's output went down quite a bit with the foam. Which I think indicates that it has a lot of HOMs.
But one thing that you CAN measure, is that the foam doesn't have much of a measurable effect on some horns, and on others, IT DOES. For instance, the horn described in this thread, it's output went down quite a bit with the foam. Which I think indicates that it has a lot of HOMs.
I think that depends a lot on the specifics of the foam. I have actually seen people used closed cell foam which will be a massive attenuation. Then open cell foam comes in pore sizes from 20 - 60 pore / in^2. The attenuation differences across this range are immense. Unless you are buying foam from a specialist, you probably don't know what you are getting.
PS. I think that I could measure HOMs if I needed to, but it would be an intensive technique. I did show how the foam changed the impulse response, mostly in the delayed tail, which is where we would expect HOMs to show up. Since HOMs will have a small effect on directivity we could most likely find them that way as well, but one would need extremely high resolution to do it that way.
Last edited:
I can attest to what the Dr is saying here
as far as "polyurethane" foams go it looks to me you would want a polyether foam, not a polyester foam???
BTW Dr. Geddes, isnt your patent on this still in effect?
as far as "polyurethane" foams go it looks to me you would want a polyether foam, not a polyester foam???
BTW Dr. Geddes, isnt your patent on this still in effect?
I think that depends a lot on the specifics of the foam. I have actually seen people used closed cell foam which will be a massive attenuation. Then open cell foam comes in pore sizes from 20 - 60 pore / in^2. The attenuation differences across this range are immense. Unless you are buying foam from a specialist, you probably don't know what you are getting.
PS. I think that I could measure HOMs if I needed to, but it would be an intensive technique. I did show how the foam changed the impulse response, mostly in the delayed tail, which is where we would expect HOMs to show up. Since HOMs will have a small effect on directivity we could most likely find them that way as well, but one would need extremely high resolution to do it that way.
I agree with you Earl.
And I agree that the foam plug works.
Pointing out the reasons is not a criticism of your design decisions. There is never a free lunch in anything audio. Good design work is continuously a balance of greater or lesser evils.
I've been designing waveguides for car audio far longer than I've been designing waveguides for home audio, in fact it was car audio waveguides that led me down the path of designing hundreds of waveguides. There are few endeavors that I've devoted more time to, and I've been grinding away at it for 30+ years.
So it was a bit of a shock when a Facebook admin disagreed with me on one of the most fundamental concepts of car audio waveguides, and then even more shocking when they banned me for a month for disagreeing with their opinion on car audio horns. (On a side note, the Facebook admin has never designed a single car audio waveguide, ever.)
I'm sure this post will earn me a permanent ban from the group, but I think it's worth posting a rebuttal, in the unlikely event that someone from the Facebook group wanders across the post.
The statement that got me banned, was that I stated "Car audio waveguides depend on the dash to extend the mouth of the horn.
Here's how this works:
In the picture above, the car audio waveguide that is located under the dash of the car uses the dash that is located above the horn to extend the size of the mouth.
One way to visualize this, is if you took one of those big ol' Electrovoice HR90 horns from the 80s, and you hacked off a big chunk of the BOTTOM half of the horn.
The reason that I described this concept in the Facebook forum was because a member had proposed taking a set of car audio waveguides and running them in his house. The results of this will be exceptionally poor, because car audio waveguides depend on that dash to function properly.
It's important to me that this is well known, for two reasons:
So it was a bit of a shock when a Facebook admin disagreed with me on one of the most fundamental concepts of car audio waveguides, and then even more shocking when they banned me for a month for disagreeing with their opinion on car audio horns. (On a side note, the Facebook admin has never designed a single car audio waveguide, ever.)
I'm sure this post will earn me a permanent ban from the group, but I think it's worth posting a rebuttal, in the unlikely event that someone from the Facebook group wanders across the post.
The statement that got me banned, was that I stated "Car audio waveguides depend on the dash to extend the mouth of the horn.
Here's how this works:


In the picture above, the car audio waveguide that is located under the dash of the car uses the dash that is located above the horn to extend the size of the mouth.


One way to visualize this, is if you took one of those big ol' Electrovoice HR90 horns from the 80s, and you hacked off a big chunk of the BOTTOM half of the horn.
The reason that I described this concept in the Facebook forum was because a member had proposed taking a set of car audio waveguides and running them in his house. The results of this will be exceptionally poor, because car audio waveguides depend on that dash to function properly.
It's important to me that this is well known, for two reasons:
- I don't want someone to waste time on something that is doomed to fail
- More importantly, I think, is that there's only about 10-20 people online who are still talking about car audio waveguides. They've REALLY gone out of style, and that's a bummer because they can work really well. Because of this, I'd hate to see someone evaluate a set of them in a way that's inappropriate, and then come away with the idea that they don't sound good. They DO sound good... if properly installed. And a proper installation depends on the dash.
Here's some citations to back up my claims:
2007~2011 Honda Civic Si | DiyMobileAudio.com Car Stereo Forum
"That gap between the horn mouth and the knee panels should be closed up as best you can. The horn uses the bottom of the dash to help extend the horn."
2007~2011 Honda Civic Si | DiyMobileAudio.com Car Stereo Forum
"That gap between the horn mouth and the knee panels should be closed up as best you can. The horn uses the bottom of the dash to help extend the horn."
Here's a thread from over a decade ago, where I made similar claims as I make today. In the thread, the designer of the most popular car audio waveguides in history (Eric Stevens) adds a few replies, and did not disagree with my evaluation of how car audio waveguides work:
Under dash horns and stage height | DiyMobileAudio.com Car Stereo Forum
Under dash horns and stage height | DiyMobileAudio.com Car Stereo Forum
Here's another citation to back my claim:
Comparing horns to regular speakers for car audio | DiyMobileAudio.com Car Stereo Forum
"The general rule for horns are as far back and as wide a possible for the best possible imaging. Also ensuring a good transition between the horn mouth and the dash allows the horns to use the curvature of the dash to effectively extend the horn mouth which helps to raise the soundstage (kind of counter intuitive until you think of it like that). Eric had a great thread on here on the basics of tuning horns (as they are different than traditional cones)."
Comparing horns to regular speakers for car audio | DiyMobileAudio.com Car Stereo Forum
"The general rule for horns are as far back and as wide a possible for the best possible imaging. Also ensuring a good transition between the horn mouth and the dash allows the horns to use the curvature of the dash to effectively extend the horn mouth which helps to raise the soundstage (kind of counter intuitive until you think of it like that). Eric had a great thread on here on the basics of tuning horns (as they are different than traditional cones)."
Here's another citation:
feat. Richard Clark by SQOLOGY Car Audio Podcast | Free Listening on SoundCloud
This is a podcast that interviews Richard Clark, who had the most winning car in the car audio competitions of the early 90s.
According to Car Audio and Electronics, Richard Clark installed Altec compression drivers under the dash of his Buick Grand National. Normally, these giant Altec drivers would require a much larger horn. By leveraging the dash to extend the mouth, Clark was able to make it work. This was arguably the "golden age" of horns in car audio, because this was an era where amplifiers were expensive and low powered. What set Clark apart from just about anyone of the era was that his car was loud AND sounded good.
This was very unusual at the time, because car audio competitions basically devolved into a "Sound quality" camp and a "SPL" camp. The SQ cars didn't get very loud, and the SPL cars weren't known for sound quality. Clark did both, and blew a lot of minds.
feat. Richard Clark by SQOLOGY Car Audio Podcast | Free Listening on SoundCloud
This is a podcast that interviews Richard Clark, who had the most winning car in the car audio competitions of the early 90s.

According to Car Audio and Electronics, Richard Clark installed Altec compression drivers under the dash of his Buick Grand National. Normally, these giant Altec drivers would require a much larger horn. By leveraging the dash to extend the mouth, Clark was able to make it work. This was arguably the "golden age" of horns in car audio, because this was an era where amplifiers were expensive and low powered. What set Clark apart from just about anyone of the era was that his car was loud AND sounded good.
This was very unusual at the time, because car audio competitions basically devolved into a "Sound quality" camp and a "SPL" camp. The SQ cars didn't get very loud, and the SPL cars weren't known for sound quality. Clark did both, and blew a lot of minds.
If anyone is interested in learning more about waveguides in cars, I think this podcast is probably the best place to start:
feat. Mark Eldridge by SQOLOGY Car Audio Podcast | Free Listening on SoundCloud
Mark Eldridge began working with Richard Clark, and installed waveguides in his Toyota 4Runner. The reason that I like Mark's podcast so much, is that he has a great way of breaking down how everything works. As I understand it, Eldridge teaches classes on car audio. I'm thinking about taking one, I was really blown away by his presentation, he's a great communicator.
In the podcast, Mark talks about how he pushed the concept further and further. He didn't just make waveguides to put in the car, he took it a step further and redesigned the whole dash! As Mark describes it, the shape of the dash is critical to the sound. (Because the dash and the waveguide work together as one cohesive unit.)
Here's Mark's 4Runner
It may be difficult to tell where the waveguides are in this picture. You might think they're the black strip across the dash. But they're not. The mouth of the waveguides is in the gap between the windshield and the dash, and the windshield and the dash extend the horn mouth.
When you're putting Altec compression drivers in a car, at some point you want a lower xover point. Mark and I went down the same path, opting for coaxial designs. I went with Unity horns, Mark went with Tannoy coaxes.
Cars as Mobile Sound Stages - WSJ
https://archive.is/UlIl2 (this link is paywall free)
When the Wall Street Journal wanted to talk about car audio, they went to Mark Eldredge. In the article, Eldredge states:
"My current project started out as a Nascar Sprint Cup Dodge Intrepid used in the 2002 season. I bought it in 2004, and I’ve put about 3,500 hours into it. The car was perfect for building audio, because as a racing car, it had no passenger seat, no dashboard or center console, none of the stuff the factory usually puts in, that you have to build around when installing audio. I could build the audio first, place all components in the optimal position, then build all the other stuff around that."
feat. Mark Eldridge by SQOLOGY Car Audio Podcast | Free Listening on SoundCloud
Mark Eldridge began working with Richard Clark, and installed waveguides in his Toyota 4Runner. The reason that I like Mark's podcast so much, is that he has a great way of breaking down how everything works. As I understand it, Eldridge teaches classes on car audio. I'm thinking about taking one, I was really blown away by his presentation, he's a great communicator.
In the podcast, Mark talks about how he pushed the concept further and further. He didn't just make waveguides to put in the car, he took it a step further and redesigned the whole dash! As Mark describes it, the shape of the dash is critical to the sound. (Because the dash and the waveguide work together as one cohesive unit.)

Here's Mark's 4Runner


It may be difficult to tell where the waveguides are in this picture. You might think they're the black strip across the dash. But they're not. The mouth of the waveguides is in the gap between the windshield and the dash, and the windshield and the dash extend the horn mouth.
When you're putting Altec compression drivers in a car, at some point you want a lower xover point. Mark and I went down the same path, opting for coaxial designs. I went with Unity horns, Mark went with Tannoy coaxes.
Cars as Mobile Sound Stages - WSJ
https://archive.is/UlIl2 (this link is paywall free)
When the Wall Street Journal wanted to talk about car audio, they went to Mark Eldredge. In the article, Eldredge states:
"My current project started out as a Nascar Sprint Cup Dodge Intrepid used in the 2002 season. I bought it in 2004, and I’ve put about 3,500 hours into it. The car was perfect for building audio, because as a racing car, it had no passenger seat, no dashboard or center console, none of the stuff the factory usually puts in, that you have to build around when installing audio. I could build the audio first, place all components in the optimal position, then build all the other stuff around that."
- Home
- Loudspeakers
- Multi-Way
- The HOMster! (or How I Learned How to Fix a Horn)