First-time poster, long-time reader. I have looked as deep as I can but I have not found discussions regarding a design in this direction.
In university in the 80s, I saw a performance where the artists left the stage with battery-powered units containing a small synth and an amplified speaker in the end of a 3-4 foot long acrylic tube about 4" in diameter. They bounced sound off objects and turned the whole auditorium into a moving sound environment. It was very cool. The idea of moving outdoors in a sculpture park, or industrial space, tiled tunnel, and creating soundscapes is compelling.
I am starting to build a more capable version and working through the theories of projected sound. The intent is to have a beam of sound. As this is an instrument and not reproducing existing sound, there can be color, naturally would like the sound as true as possible given the constraints.
I am starting to firm up the design directions. The system will run off a lithium-ion bike battery 48V 15A powering a 100W amplifier. The system will allow various synth options. This being said and the models below, I am not an audio expert and am very open to directions. The horns will be produced from either composite materials, carbon fiber or flax fiber, or thermo molded acrylic.
Horn designs with compression drivers seem best suited to this task. Conical shapes seem to intuitively beam more than flared end shapes. I have designed the length and throat diameter around the lower frequency of the driver 300 Hz, as well as the maximum manageable portable size. The horn in the images below is 1.14 meters and has a diameter of 0.36 meters. The taper is based on the linear progression of the length and the circumference being equal, with a smooth curve from 50.8mm at the mouth.
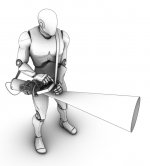
The second design is based on a parabolic reflector. Based on systems used in museums for projecting into specific listening areas. The system would ideally be modular so that different waveguides could be fitted bayonet style. The dish is sized larger than the horn, but I am unclear on the approach here for sizing to frequency. The compression driver is piped forward and reflects from the rear-facing parabolic dome to the main parabolic dish. The intent is to direct waves forward in as tight a beam as possible and have them break up and reflect back from objects in the environment.
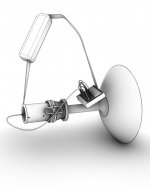
Thanks for your time!
In university in the 80s, I saw a performance where the artists left the stage with battery-powered units containing a small synth and an amplified speaker in the end of a 3-4 foot long acrylic tube about 4" in diameter. They bounced sound off objects and turned the whole auditorium into a moving sound environment. It was very cool. The idea of moving outdoors in a sculpture park, or industrial space, tiled tunnel, and creating soundscapes is compelling.
I am starting to build a more capable version and working through the theories of projected sound. The intent is to have a beam of sound. As this is an instrument and not reproducing existing sound, there can be color, naturally would like the sound as true as possible given the constraints.
I am starting to firm up the design directions. The system will run off a lithium-ion bike battery 48V 15A powering a 100W amplifier. The system will allow various synth options. This being said and the models below, I am not an audio expert and am very open to directions. The horns will be produced from either composite materials, carbon fiber or flax fiber, or thermo molded acrylic.
Horn designs with compression drivers seem best suited to this task. Conical shapes seem to intuitively beam more than flared end shapes. I have designed the length and throat diameter around the lower frequency of the driver 300 Hz, as well as the maximum manageable portable size. The horn in the images below is 1.14 meters and has a diameter of 0.36 meters. The taper is based on the linear progression of the length and the circumference being equal, with a smooth curve from 50.8mm at the mouth.
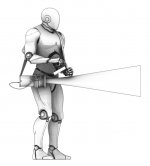
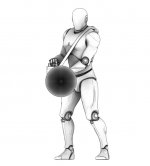
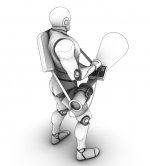
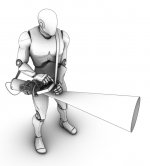
The second design is based on a parabolic reflector. Based on systems used in museums for projecting into specific listening areas. The system would ideally be modular so that different waveguides could be fitted bayonet style. The dish is sized larger than the horn, but I am unclear on the approach here for sizing to frequency. The compression driver is piped forward and reflects from the rear-facing parabolic dome to the main parabolic dish. The intent is to direct waves forward in as tight a beam as possible and have them break up and reflect back from objects in the environment.
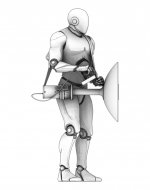
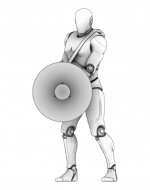
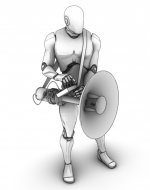
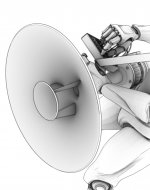
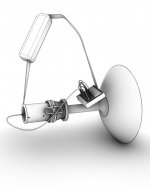
Thanks for your time!
Welcome to the forum!
A cool idea and thanks for the neat drawings, they help to understand exactly what you want to do. As you have already figured out, the laws of physics dictate that getting tight directivitiy at low frequencies means big horns or dishes.
You might want to look and.or experiment with 3" cone drivers in this application. Getting a compression driver down to 300Hz isn't easy, despite what the specs might say.
A cool idea and thanks for the neat drawings, they help to understand exactly what you want to do. As you have already figured out, the laws of physics dictate that getting tight directivitiy at low frequencies means big horns or dishes.
You might want to look and.or experiment with 3" cone drivers in this application. Getting a compression driver down to 300Hz isn't easy, despite what the specs might say.
My guess is that with a conical horn of that size, you get pretty good beaming down to about 1100Hz. Under that it would go wide very quickly. But it would certainly work to throw sound were you want it. Hand held funnel time megaphones do that, and they aren't any bigger.
cool project - - perhaps this driver
PRV Audio 5MR450-NDY-4 5" Midrange Neodymium Woofer 4 Ohm
PRV Audio 5MR450-NDY 5" Midrange Neodymium Woofer 8 Ohm
PRV Audio 5MR450-NDY-4 5" Midrange Neodymium Woofer 4 Ohm
PRV Audio 5MR450-NDY 5" Midrange Neodymium Woofer 8 Ohm
Pano, thanks! I'll take a look at 3" cones, for some reason I was prejudiced against small cones. Question though, do cones mounted in the ends of waveguides typically need captive air behind them, or are they moving freely?
Does having multiple cones feeding into the end of a horn bring any benefit?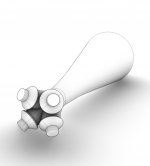
Beaming down to 1100 Hz should be good, in process of roughing out a working version of that horn shape now for an existing 90mm cone speaker.
Does having multiple cones feeding into the end of a horn bring any benefit?
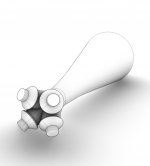
Beaming down to 1100 Hz should be good, in process of roughing out a working version of that horn shape now for an existing 90mm cone speaker.
? you could get by shorter for 300Hz. maybe around 80cm
A $30 mono TPA3116D2 and 20v tool battery might be adequate
A $30 mono TPA3116D2 and 20v tool battery might be adequate
Attachments
Last edited:
Thanks for that suggestion, what do you like about those cones in particular?
I downloaded Hornresp software but have not figured it out yet, was running off the "horn length equal to wavelength" rule of thumb. I will spend more time learning it, shorter for sure is better, beaming is the main design goal.
I have Sure Electronics 1x100W amp now for the prototype system. I will be powering a small modular synth as well from the battery, so building in extra capacity.
I downloaded Hornresp software but have not figured it out yet, was running off the "horn length equal to wavelength" rule of thumb. I will spend more time learning it, shorter for sure is better, beaming is the main design goal.
I have Sure Electronics 1x100W amp now for the prototype system. I will be powering a small modular synth as well from the battery, so building in extra capacity.
Yes it does, and was seen often even in the old days. Now it's quite common in line array PA speakers where 2 drivers are used per horn Getting beyond 2 might get tricky, you don't want them to interfere and cancel each other or otherwise give you a strange frequency response.Does having multiple cones feeding into the end of a horn bring any benefit?
As this is a special usage, you will probably need to experiment and try a few things to get what you want. I see prototypes in your future. Freddi has been kind enough to model the cone cannon for you and that's a big help. Thanks Freddi!

Forum member GM might also chime in, he has real world experience making load horns that carry a distance.
@Freddi. You went right for the big guns with that PRV driver, didn't you? 😉 I was thinking more along the lines of the FaitalPRO 3FE22 3" or its 4" brother. If multiple drivers are used, the neo 3" might be the smart choice. Do you think it would have enough output?
Your designs with the flared ends differ from the 4" acrylic tube you first had seen.
Maybe you dont want a horn at all - given the objective is to ricochet a sound off some distant surface - You want a narrow beam. A horn is meant to cover a wide swath at a distance, like some section of seats in a theater. Trucks and trains have horns and when they blow, you can here them everywhere.
I dont know how to make an acoustic beam. I do recall someone else in the forum wanting to do something similar for a Halloween spooky distant voice effect; I'm pretty sure the thread is here somewhere.
Regarding power handling OP did say "synth", which I take to be a function generator, followed by a swept filter, followed by an envelope generator. Could be continuous, depending on whether the key is held down or not.
Maybe you dont want a horn at all - given the objective is to ricochet a sound off some distant surface - You want a narrow beam. A horn is meant to cover a wide swath at a distance, like some section of seats in a theater. Trucks and trains have horns and when they blow, you can here them everywhere.
I dont know how to make an acoustic beam. I do recall someone else in the forum wanting to do something similar for a Halloween spooky distant voice effect; I'm pretty sure the thread is here somewhere.
Regarding power handling OP did say "synth", which I take to be a function generator, followed by a swept filter, followed by an envelope generator. Could be continuous, depending on whether the key is held down or not.
I wonder if a "saucer" sled could make some sort of parabolic speaker..
In the US there's inexpensive re-entrant horns - I don't kn ow how loud the associated compression drivers can play at 300Hz but this smaller model comes close to the bell size stated
https://www.parts-express.com/pedocs/specs/300-194--dayton-audio-rph16-spec-sheet.pdf
In the US there's inexpensive re-entrant horns - I don't kn ow how loud the associated compression drivers can play at 300Hz but this smaller model comes close to the bell size stated
https://www.parts-express.com/pedocs/specs/300-194--dayton-audio-rph16-spec-sheet.pdf

Last edited:
I thought about that too, but don't those horns have wide spread? On purpose, of course.
The tube or tight come would look a lot cooler.
The tube or tight come would look a lot cooler.
They have wide spread where the mouth size vs frequency loses control
compare to the horn response model of the slightly smaller mouth
compare to the horn response model of the slightly smaller mouth

Attachments
Last edited:
its got a good motor plus a recone kit. I don't know how rugged a 1.5" voice coil would be. How intense is the program material ?
Freddi, thanks for the suggestion, I will give those a try as well.
I assume the range of what will be played will hit the range of intense. The signals out can be the full spectrum of tone and envelopes plus noise. I don't know everything I will be throwing at it yet, but I expect things are going to break along the way.
that's about the same as the one I showed for a 3 foot horn. With a long slowly expanded "neck", yes the longer horn would be tighter above 2KHz. The Dayton 16" horn probably has about 3 foot of path length.
It'll be interesting to see his final choice.
It'll be interesting to see his final choice.
Last edited:
Yes it does, and was seen often even in the old days. Now it's quite common in line array PA speakers where 2 drivers are used per horn Getting beyond 2 might get tricky, you don't want them to interfere and cancel each other or otherwise give you a strange frequency response.
As this is a special usage, you will probably need to experiment and try a few things to get what you want. I see prototypes in your future. Freddi has been kind enough to model the cone cannon for you and that's a big help. Thanks Freddi!
Forum member GM might also chime in, he has real world experience making load horns that carry a distance.
Thanks for that. Will try with a Y split and the two 90mm I have. Yes, planning on doing lots of trial and error. Fail early and often.
@Freddi thanks for running the simulations!
Your designs with the flared ends differ from the 4" acrylic tube you first had seen.
Maybe you dont want a horn at all - given the objective is to ricochet a sound off some distant surface - You want a narrow beam. A horn is meant to cover a wide swath at a distance, like some section of seats in a theater. Trucks and trains have horns and when they blow, you can here them everywhere.
I dont know how to make an acoustic beam. I do recall someone else in the forum wanting to do something similar for a Halloween spooky distant voice effect; I'm pretty sure the thread is here somewhere.
Regarding power handling OP did say "synth", which I take to be a function generator, followed by a swept filter, followed by an envelope generator. Could be continuous, depending on whether the key is held down or not.
I'm using Rhino3d software, they have a nice parabola tool that allows setting up the curves quickly, and revolved into surfaces. I look for Halloween posts, thanks for the tip.
The synth that I will be testing is a small modular system. Pico System III. dimensions are small, about 128mm high x 210mm wide.
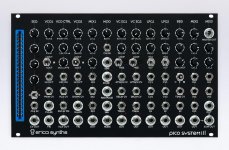
There are no keys, but the note control input can be done from another mounted unit or sequencer.
This would probably get me close, an old sat dish will probably work also for a cheap test.I wonder if a "saucer" sled could make some sort of parabolic speaker..
They have wide spread where the mouth size vs frequency loses control
compare to the horn response model of the slightly smaller mouth
These charts are so interesting, thanks again for taking the time to model them up. Will get into the software and see if I can learn more.
You'll want to know how loud you can go with one.. they may get heavy.Does having multiple cones feeding into the end of a horn bring any benefit?
- Home
- Loudspeakers
- Full Range
- Shoulder slung, waveguide, synth beamer