Ok watch out for the small bronze ring is often overlooked or lost during revision work.
Ouch, I now know why I am having problems with my older 124, (speed adjustment) it was definitely missing in the collection of parts I bought when I was restoring this table. It had been stripped of almost everything but the motor and intermediate pulley. For some reason I felt compelled to rescue it, a decision I have not regretted as it is definitely the less finicky of the two I own.
Anyone know of a suitable replacement?
Ouch, I now know why I am having problems with my older 124, (speed adjustment) it was definitely missing in the collection of parts I bought when I was restoring this table. It had been stripped of almost everything but the motor and intermediate pulley. For some reason I felt compelled to rescue it, a decision I have not regretted as it is definitely the less finicky of the two I own.
Anyone know of a suitable replacement?
Kevin no problem, I can make this ring for you.
Kevin no problem, I can make this ring for you.
Is that something you do on a regular basis? Mine has also disappeared. I would love to be able to adjust the speed 🙂
My apologies in advance if this has been covered in this forum elsewhere.
Does anyone have a source for the springs that are incorporated into what I see commonly described as the "Block Switch" on a TD 124
Does anyone have a source for the springs that are incorporated into what I see commonly described as the "Block Switch" on a TD 124

I am amazed by this thread, its is like the 124 wikipedia.
I´ve been reading the thread, but I haven't found any reference about the fact that Thorens recomends Texaco ROG oil for the Step intermediate pulley and Idler wheel on the MKII manual (page 13 and 14). That oil has 4 times the viscosity of the ROB oil, ROB oil is ISO 46 viscosity and ROG 220. Any one has any opinion on the use of that oil, maybe it helps to reduce the noise.
I´ve been reading the thread, but I haven't found any reference about the fact that Thorens recomends Texaco ROG oil for the Step intermediate pulley and Idler wheel on the MKII manual (page 13 and 14). That oil has 4 times the viscosity of the ROB oil, ROB oil is ISO 46 viscosity and ROG 220. Any one has any opinion on the use of that oil, maybe it helps to reduce the noise.
My apologies in advance if this has been covered in this forum elsewhere.
Does anyone have a source for the springs that are incorporated into what I see commonly described as the "Block Switch" on a TD 124![]()
Send me a PM with your shipping and I will send some. I have a bunch of these switches here.
Best,
Jim
I am amazed by this thread, its is like the 124 wikipedia.
I´ve been reading the thread, but I haven't found any reference about the fact that Thorens recomends Texaco ROG oil for the Step intermediate pulley and Idler wheel on the MKII manual (page 13 and 14). That oil has 4 times the viscosity of the ROB oil, ROB oil is ISO 46 viscosity and ROG 220. Any one has any opinion on the use of that oil, maybe it helps to reduce the noise.
Checking my own copy of the service manual and can corroborate.... and this certainly bears further investigation. I found mention of the ROG as recommended for the stepped pulley bearing. ROB for the motor bushings and felts.
This nomenclature is for a long time outdated. Texaco now classifies their tubine oils as "R&O" and don't use the letters B or G in the product descriptions. Just R&O followed by the (ISO) viscosity value.
Fwiw dept:
The higher viscosity lube at the stepped pulley may not induce any significant increase in drag...(pure speculation). The stepped pulley bearing is under pressure below at the belt ring and above at the idler......and with some distance in elevation between those two loadings. It likely would not hurt to try something 'thicker' at the stepped pulley. It also seems that the 'flow' characteristics of a turbine oil is also desirable at this maintenance point as well as at all others within the drive train.
With regard to stepped pulley generated noise I can say from my own observations that the last design stepped pulley bearing and pulley do generate more noise than the early design. But I do not think this 'noise',-- which seems to be air borne and not contributing to vibrations pulsing through the chassis,-- is of no consequence.
-Steve
Checking my own copy of the service manual and can corroborate.... and this certainly bears further investigation. I found mention of the ROG as recommended for the stepped pulley bearing. ROB for the motor bushings and felts.
This nomenclature is for a long time outdated. Texaco now classifies their tubine oils as "R&O" and don't use the letters B or G in the product descriptions. Just R&O followed by the (ISO) viscosity value.
Fwiw dept:
The higher viscosity lube at the stepped pulley may not induce any significant increase in drag...(pure speculation). The stepped pulley bearing is under pressure below at the belt ring and above at the idler......and with some distance in elevation between those two loadings. It likely would not hurt to try something 'thicker' at the stepped pulley. It also seems that the 'flow' characteristics of a turbine oil is also desirable at this maintenance point as well as at all others within the drive train.
With regard to stepped pulley generated noise I can say from my own observations that the last design stepped pulley bearing and pulley do generate more noise than the early design. But I do not think this 'noise',-- which seems to be air borne and not contributing to vibrations pulsing through the chassis,-- is of no consequence.
-Steve
that last phrase " is of no consequence". Bad grammar and wrong meaning. should have said " is of any consequence."
-Steve
I am trying to get those oils to do a comparison.
On the iddler there is no problem, as the wheel turns very slow with a lot of torque, and on the step I think that as the axel is very thin there slouldn´t be any problem either.
I´ll let you know
On the iddler there is no problem, as the wheel turns very slow with a lot of torque, and on the step I think that as the axel is very thin there slouldn´t be any problem either.
I´ll let you know
Tool to extract TD 124 bronze bushing
Hello,
I’ve restored my THORENS TD 124, thanks to a lot of advices I’ve found on different forums, and it’s now my turn to contribute.
Topic : Tool to extract or insert main platter bearing’s bronze bushings.
Content :Tutorial to realize a simple, cheap and efficient tool to change the bronze bushings of the TD 124 main platter bearing.
It is a small tool which enables you to change easily the bronze bushing from the spindle bearing without any risk for your precious turntable.
You need a few parts available on the Internet for cheap :
- 1 CHC bolt, hex socket head cap screw, DIN 912 M10 x 100, total thread length, 16 mm for the head diameter (Allen key number 8)
- 1 hexagonal nut DIN 934 M10
- 8 flat washers, narrow type Z, NFE 25513, M20 (DIN125 A)
- 1 flat washer, large type L, NFE25513, M10 (DIN125 A)
- 1 nylon flat washer M8 (DIN125 A), 16 mm extern diameter, central hole enlarge from 8 to 10 mm
- 1 bandwidth of adhesive tape for electrician
- 1 tube of super glue (Loctite or cyanolit)
How to proceed :
A - Insert the nylon washer against the head of the CHC bolt. It is used for protecting the top of the bronze bushing during its extraction or its insertion in the bearing’s shaft.
B - Wind a bandwidth of adhesive tape around the bolt, just below the nylon washer until you get close to the internal diameter of the bronze bushing (approximatively 14 mm). This tape protects the inside of the first bushing and enables you to center the CHC bolt.
C - Stick with some superglue the 8 flat washers M20 so as to form a kind of « cage », which will be used to take the former bronze bushings out and get it back. This « cage » is useless during the insertion of the new bushings.
Here we are, your tool is ready to be used !
You just have to take off the main platter bearing’s shaft from the turntable after having checked the position and the tightening level of the three fixing screws.
The hexagonal nut, the M10 washer and the cage in case of extraction all together must be positioned at the base of the bearing’s shaft.
Use an Allen wrench to block the CHC bolt inside the shaft, and use an open-end wrench or an adjustable wrench to turn the nut further, but remember to act gently and gradually.
An illustrated tutorial in English and in French is attached
Antoine Bouchez from Annecy (France)
Hello,
I’ve restored my THORENS TD 124, thanks to a lot of advices I’ve found on different forums, and it’s now my turn to contribute.
Topic : Tool to extract or insert main platter bearing’s bronze bushings.
Content :Tutorial to realize a simple, cheap and efficient tool to change the bronze bushings of the TD 124 main platter bearing.
It is a small tool which enables you to change easily the bronze bushing from the spindle bearing without any risk for your precious turntable.
You need a few parts available on the Internet for cheap :
- 1 CHC bolt, hex socket head cap screw, DIN 912 M10 x 100, total thread length, 16 mm for the head diameter (Allen key number 8)
- 1 hexagonal nut DIN 934 M10
- 8 flat washers, narrow type Z, NFE 25513, M20 (DIN125 A)
- 1 flat washer, large type L, NFE25513, M10 (DIN125 A)
- 1 nylon flat washer M8 (DIN125 A), 16 mm extern diameter, central hole enlarge from 8 to 10 mm
- 1 bandwidth of adhesive tape for electrician
- 1 tube of super glue (Loctite or cyanolit)
How to proceed :
A - Insert the nylon washer against the head of the CHC bolt. It is used for protecting the top of the bronze bushing during its extraction or its insertion in the bearing’s shaft.
B - Wind a bandwidth of adhesive tape around the bolt, just below the nylon washer until you get close to the internal diameter of the bronze bushing (approximatively 14 mm). This tape protects the inside of the first bushing and enables you to center the CHC bolt.
C - Stick with some superglue the 8 flat washers M20 so as to form a kind of « cage », which will be used to take the former bronze bushings out and get it back. This « cage » is useless during the insertion of the new bushings.
Here we are, your tool is ready to be used !
You just have to take off the main platter bearing’s shaft from the turntable after having checked the position and the tightening level of the three fixing screws.
The hexagonal nut, the M10 washer and the cage in case of extraction all together must be positioned at the base of the bearing’s shaft.
Use an Allen wrench to block the CHC bolt inside the shaft, and use an open-end wrench or an adjustable wrench to turn the nut further, but remember to act gently and gradually.
An illustrated tutorial in English and in French is attached
Antoine Bouchez from Annecy (France)
Attachments
Can I merge this with the active TD-124 thread so that it does not disappear over time? 😀 Up to you.
Edit: OP agreed and this information has been merged into this thread.
Edit: OP agreed and this information has been merged into this thread.
I am trying to get the Texaco Regal R&O 46 and 220 but is very difficult to get those here in europe.
I might try the Mobil DTE 25 and DTE BB, those ones are easy to get here the only problem is they came in 20L cans 😱😱
I might try the Mobil DTE 25 and DTE BB, those ones are easy to get here the only problem is they came in 20L cans 😱😱
Checking my own copy of the service manual and can corroborate.... and this certainly bears further investigation. I found mention of the ROG as recommended for the stepped pulley bearing. ROB for the motor bushings and felts.
This nomenclature is for a long time outdated. Texaco now classifies their tubine oils as "R&O" and don't use the letters B or G in the product descriptions. Just R&O followed by the (ISO) viscosity value.
Fwiw dept:
The higher viscosity lube at the stepped pulley may not induce any significant increase in drag...(pure speculation). The stepped pulley bearing is under pressure below at the belt ring and above at the idler......and with some distance in elevation between those two loadings. It likely would not hurt to try something 'thicker' at the stepped pulley. It also seems that the 'flow' characteristics of a turbine oil is also desirable at this maintenance point as well as at all others within the drive train.
With regard to stepped pulley generated noise I can say from my own observations that the last design stepped pulley bearing and pulley do generate more noise than the early design. But I do not think this 'noise',-- which seems to be air borne and not contributing to vibrations pulsing through the chassis,-- is of no consequence.
-Steve
My steppulley vibration measurements on this noise shows it is around the 450 Hz- 500Hz , clearly seen on the picture.
View attachment Steppulley Bearing noise TD124.2 asis.bmp
Next picture the pulley driven by hand and short measurement .
View attachment Thorens TD124 Vibration Steppulley noise Hand drive.bmp
Mostly the clearance on the bushings is to much and better replace them .
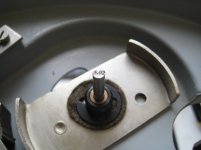
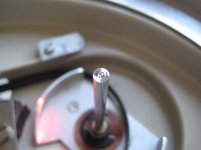
My steppulley vibration measurements on this noise shows it is around the 450 Hz- 500Hz , clearly seen on the picture.
View attachment 567511
Next picture the pulley driven by hand and short measurement .
View attachment 567513
Mostly the clearance on the bushings is to much and better replace them .
View attachment 567514
View attachment 567515
minus 60 to minus 80 db. Not very noisy.
You picture an early stepped pulley bearing design. I am curious if you have made measurement comparisons between the early and late stepped pulley bearings?
My "measurements" have been conducted with a mechanic's stethoscope. Subjective but repeatable so long as my mental state and hearing also repeat.
-Steve
minus 60 to minus 80 db. Not very noisy.
You picture an early stepped pulley bearing design. I am curious if you have made measurement comparisons between the early and late stepped pulley bearings?
My "measurements" have been conducted with a mechanic's stethoscope. Subjective but repeatable so long as my mental state and hearing also repeat.
-Steve
The steppulley picture is from the later one bearing in the chassis !
Noise about -60 till -40 depends from belt tension . No measurements from the first pulley yet.
Volken
The steppulley picture is from the later one bearing in the chassis !
Noise about -60 till -40 depends from belt tension . No measurements from the first pulley yet.
Volken
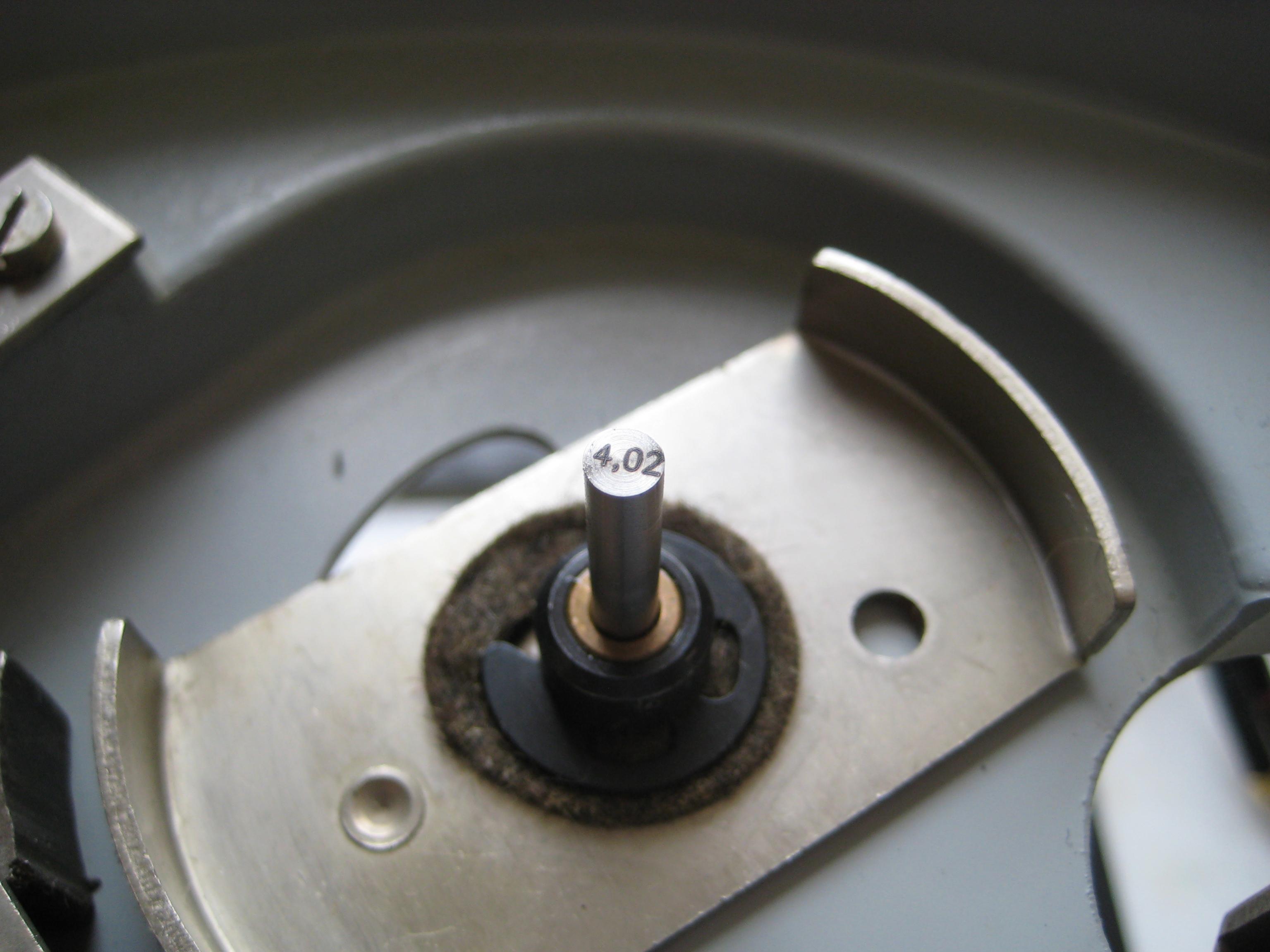
OK. Looking at the photo full size I see that the 'shaft' has been removed from the stepped pulley. And I can see the bushing at the base holding the shaft.
The early version features a shaft that is fixed solid (with two set screws) to the base and the bushings are held within the stepped pulley.
The later version with the shaft (which you have removed) set-screwed into the stepped pulley and the bushings within the base as pictured.
Yet, a measurement / comparison between the two designs might be warranted because of the numerous complaints of stepped pulley noise associated with the mkII players.
-Steve
- Home
- Source & Line
- Analogue Source
- Restoring and Improving A Thorens TD-124 MKII