Member
Joined 2009
Paid Member
I like the look of the 10.3 in the pencil. A friend of mine is suggesting I build him a pair. I haven't asked if a port/plinth is something he wants - the last pair of speakers I showed him was a pair of micro-castles where the port is hidden in the base. Is there a design for the 10.3 with a castle-esque port in the bottom instead of on the front ? If not, would Scott and/or Dave be willing to offer a design for public use should there be interest ?
Just move the vent tp the bottom and lift the Pensil up off the floor... you might have to play with that height a bit.
dave
dave
Member
Joined 2009
Paid Member
Thanks guys. These are questions I have to explore with my friend - right now I am wondering what options I can offer. I am also looking at the differences between the paper and metal drivers. He has a preference for paper and tube amps but I am getting the perception that the metal version is a better choice. The more I read about what people have to say about these drivers, the more I am tempted to build a pair for myself at the same time!
Member
Joined 2009
Paid Member
OK - the project is confirmed. I will build a pair of 10.3 Pensils to the plans linked in post 1 of this thread. I plan to use 17.5mm Birch Plywood and will add internal braces using 11mm Birch ply.
The drivers will go into a basement for slow cooking, should be able to get quite a few hours on them before the boxes are ready.
The drivers came with removable bezel - is this optional, does it affect the sound ?
Any words of wisdom regarding the box build ?
The drivers will go into a basement for slow cooking, should be able to get quite a few hours on them before the boxes are ready.
The drivers came with removable bezel - is this optional, does it affect the sound ?
Any words of wisdom regarding the box build ?
The drivers came with removable bezel - is this optional, does it affect the sound ?
They are optional, i have a growing collection of them
dave
words of "wisdom" suggests a measure of ego on the part of the bestower of such 😉, but I'll happily offer a few suggestions
- 11-12mm material might be a bit thin for bracing on this build, IIRC, I used 15mm on my recent Pensil10.3 build
- Whatever material you use for bracing, try an interlocking notch of at least 1 - 1.5" , and be sure to align the braces off center on the exterior panels, using spacing blocks to keep them square
- When boring holes in the braces with a drill mounted hole-saw, I lightly score the face, then bore several 1/4 - 3/8" through holes inside the circle to allow for chips to exhaust out the bottom - this keeps things cooler and speeds up cutting, as well as making it easier to spin out the cut plug
- I always bore holes in both brace panels at the same time, with some sacrifice scrap to prevent tear-out on the bottom face (see, there are a couple of good uses for MDF in speaker building 😀)
- If you're planning on some type of grille for WAF, consider flush mounted neo magnets under the veneer and on a light MDF frame - use a brad-point bit to drill the baffles and MDF frames together for perfect alignment, and before assembly.
- As it's very likely the volume of damping fill will need to be adjusted, fabricate with the back panel removable, and seal with closed cell foam weatherstrip tape ( Home Depot, etc). Be sure to make allowance for the compressed thickness of this gasket when placing the attachment cleats on enclosure panels. I countersink the screw holes on back panel to prevent tear out when they are removed for adjusting fill.
- Be sure to chamfer the rear side of driver through hole before assembly.
I can't think of anything else at the moment - after a few scores of build, a lot of it becomes muscle memory
- 11-12mm material might be a bit thin for bracing on this build, IIRC, I used 15mm on my recent Pensil10.3 build
- Whatever material you use for bracing, try an interlocking notch of at least 1 - 1.5" , and be sure to align the braces off center on the exterior panels, using spacing blocks to keep them square
- When boring holes in the braces with a drill mounted hole-saw, I lightly score the face, then bore several 1/4 - 3/8" through holes inside the circle to allow for chips to exhaust out the bottom - this keeps things cooler and speeds up cutting, as well as making it easier to spin out the cut plug
- I always bore holes in both brace panels at the same time, with some sacrifice scrap to prevent tear-out on the bottom face (see, there are a couple of good uses for MDF in speaker building 😀)
- If you're planning on some type of grille for WAF, consider flush mounted neo magnets under the veneer and on a light MDF frame - use a brad-point bit to drill the baffles and MDF frames together for perfect alignment, and before assembly.
- As it's very likely the volume of damping fill will need to be adjusted, fabricate with the back panel removable, and seal with closed cell foam weatherstrip tape ( Home Depot, etc). Be sure to make allowance for the compressed thickness of this gasket when placing the attachment cleats on enclosure panels. I countersink the screw holes on back panel to prevent tear out when they are removed for adjusting fill.
- Be sure to chamfer the rear side of driver through hole before assembly.
I can't think of anything else at the moment - after a few scores of build, a lot of it becomes muscle memory
Member
Joined 2009
Paid Member
Thanks - this is indeed very handy. I've struggled with the use of the hole saw before, both over-heating and getting the plug stuck in there so I'll be trying that nugget out.
Imo, unless you have gorilla arms the removable back concept is overkill. A slightly oversized binding post plate, strategically located so you can reach where you cant thru the driver cutout should suffice.
words of "wisdom" suggests a measure of ego on the part of the bestower of such 😉, but I'll happily offer a few suggestions
- As it's very likely the volume of damping fill will need to be adjusted, fabricate with the back panel removable, and seal with closed cell foam weatherstrip tape ( Home Depot, etc). Be sure to make allowance for the compressed thickness of this gasket when placing the attachment cleats on enclosure panels. I countersink the screw holes on back panel to prevent tear out when they are removed for adjusting fill.
Last edited:
Member
Joined 2009
Paid Member
That's good thought, but in my case, my friend has elected not to use a terminal cup and prefers hi-end binding posts so a removable back will still be a good idea.
mp9 / Bigun:
as I remarked in another thread, with the larger drivers, the new 10s and certainly the 12P, one might be able to use a fixed back and still access interior for fill adjustment through either a combination of driver cut-out and larger terminal mounting plate - such as the very nice Dayton, which I've used;
Dayton Audio SBPP-BK Binding Post Plate Black Anodized 091-602
and / or via removable Bottom plate - dadoed or cleated - I've done that too
but on shallower tall cabinets, it can be quite a contortion to achieve even re-distribution / adjustment of fill without a removable panel - to continue the simian analogy, you'd need spider monkey arms made of rubber 😀
as I remarked in another thread, with the larger drivers, the new 10s and certainly the 12P, one might be able to use a fixed back and still access interior for fill adjustment through either a combination of driver cut-out and larger terminal mounting plate - such as the very nice Dayton, which I've used;
Dayton Audio SBPP-BK Binding Post Plate Black Anodized 091-602
An externally hosted image should be here but it was not working when we last tested it.
and / or via removable Bottom plate - dadoed or cleated - I've done that too
but on shallower tall cabinets, it can be quite a contortion to achieve even re-distribution / adjustment of fill without a removable panel - to continue the simian analogy, you'd need spider monkey arms made of rubber 😀
... prefers hi-end binding posts....
Which ones -- i've certainly run across some of those tha are not very good. I'd recommend Eichmann cablepods.
dave
Chris, thanks for the recommendation for Dayton Audio plates. The specs don't list hole diameter, only spacing, would you happen to know if they'll fit Eichmann CablePod binding post?
Member
Joined 2009
Paid Member
I will look into this - the fixed back provides for a stronger box and better construction in my experience so I do like this idea.
the pictured plate is 4"x4" - with IIRC 1/4" radius corners, so to make a nice rebate for flush mounting you need to make a jig for pattern following or mortising bit
the spacing is much wider than the 3/4" on Eichmann pods,
I think the plastic plate can be removed and the posts threaded through the holes in the Dayton plates - but it's been so long since I used either that it'd be conjecture whether the molded / indexed plastic "washers" on the Eichmanns would fit properly on the metal plates, and one does need to be careful with the amount of torque applied to the nuts, as well as heat and duration with soldering tools
with some creativity, these might work on the Dayton plates- and satisfy the criteria or low mass (at much lower price than the Eichmanns)
Mini Insulated Binding Post Pair Gold 320-3375
the spacing is much wider than the 3/4" on Eichmann pods,
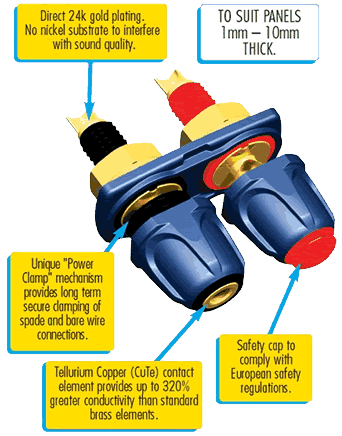
I think the plastic plate can be removed and the posts threaded through the holes in the Dayton plates - but it's been so long since I used either that it'd be conjecture whether the molded / indexed plastic "washers" on the Eichmanns would fit properly on the metal plates, and one does need to be careful with the amount of torque applied to the nuts, as well as heat and duration with soldering tools
with some creativity, these might work on the Dayton plates- and satisfy the criteria or low mass (at much lower price than the Eichmanns)
An externally hosted image should be here but it was not working when we last tested it.
Mini Insulated Binding Post Pair Gold 320-3375
For the builder who must have the Eichmann pods, the mounting plates wouldn't be hard to make with the correct c-c spacing to accommodate the fancy binding posts. They could be made larger for those who spend lots of time pumping iron at the gym.😉 Powder coat them your favorite colour too.
jeff
jeff
I like these. They are waaaay too big to get anything close to "standard" spacing.
2 Pairs CMC Speaker Binding Post 878L SE Lock Function | eBay
I don't know if they sound better or not. Don't care. They are great for us senior citizens with failing grip and arthritis.
2 Pairs CMC Speaker Binding Post 878L SE Lock Function | eBay
I don't know if they sound better or not. Don't care. They are great for us senior citizens with failing grip and arthritis.
Much ado about nothing, but i already have a stock of CablePods.
The CablePods can be used with without their plastic mounting plate. Only and assuming they'll fit the Dayton plate post hole, they don't have the little key slot off the hole of the Dayton plate to hold them in place.
The Pods have a 5/16" threaded shaft with two opposing sides flattened which in cross section would look like a ice hockey rink oval. Without that shape i'd be concerned the post would work itself loose.
The CablePods can be used with without their plastic mounting plate. Only and assuming they'll fit the Dayton plate post hole, they don't have the little key slot off the hole of the Dayton plate to hold them in place.
The Pods have a 5/16" threaded shaft with two opposing sides flattened which in cross section would look like a ice hockey rink oval. Without that shape i'd be concerned the post would work itself loose.
- Home
- Loudspeakers
- Full Range
- Pensils for Alpair 10.3 & Alpair 10p