Still the spring part is a separate part.
I think you mean that the barrel shaped spring section spins around when the plug is not inserted into the socket.
But isn't it squashed and held tight against the barrel of the plug when it is inserted?
Hi Benz.Recall that in tube power amplifiers, the WHOLE SIGNAL goes through a transformer - it gets converted totally into a magnetic field and goes into the iron from the primary, and then back to electricity in the secondary!
I'm just a novice with very basic experience so I might be off the mark.
In terms of iron in the path with tube power amplifiers, aren't they reputed to have a warm coloured sound?
A sound some are attracted to. A sound which has been engineered.
A builder of many crossovers over the years taught the importance of physically twisting the wires of components together first, to ensure the best conductivity in the path, and then use solder to immobilize the parts & protect them from oxidation. Thus you limit or remove exposure to possible conductivity issues associated with the solder itself.Oh yes, how many thousands of wire wraps have I made? Round wire on a square post. 4 1/2 wraps minimum per the spec. That certainly is not easily bested. I agree as well that solder makes it better, and of course permanent. Beyond that, I am inclined to wonder which solder is best qualified. It's content and physical/chemical properties do have merit. I have ended up using only Wonder Solder for my purposes, mostly because of its ease of use and decent reputation.
I suppose that it is a whole 'nother topic when it comes to mechanical connections and their benefits over other methods.
When the metal parts are wrapped tightly together the electrical connection is made.
The solder stops the wires twisting, vibrating or loosening over time.
It also prevents oxygen and moisture getting to the parts thus avoiding resistance caused by corrosion.
The use of shrink wrap where practical was also recommended to further reduce oxidation issues.
He also advocated the ditching, wherever possible of spade connectors and the like, preferring to solder the wiring to Driver terminals.
He'd first use the little hole found in terminal tabs to firmly wrap wiring in place in order to create the electrical bond, and follow this with solder.
I'm just a novice with very basic experience so I might be off the mark.
In terms of iron in the path with tube power amplifiers, aren't they reputed to have a warm coloured sound?
A sound some are attracted to. A sound which has been engineered.
Yes, the output transformer certainly has its own effects on the sound, both audible and measurable.
CliffR52,
That is exactly the way that I feel about most every connection and the use of solder. The exception wouldn't be in audio so much but in power where if you are using the proper crimping tool (usually unlikely as I have witnessed it), the connection can be made very well. Having said this, either using a form of antioxidant or an adhesive double wall heat shrink is advised. Although I am not as big of a fan of twist on connectors (again because of what I have witnessed them being used incorrectly) other forms of wire twisting and then heat shrink over that can be perfectly fine.
That is exactly the way that I feel about most every connection and the use of solder. The exception wouldn't be in audio so much but in power where if you are using the proper crimping tool (usually unlikely as I have witnessed it), the connection can be made very well. Having said this, either using a form of antioxidant or an adhesive double wall heat shrink is advised. Although I am not as big of a fan of twist on connectors (again because of what I have witnessed them being used incorrectly) other forms of wire twisting and then heat shrink over that can be perfectly fine.
Yes you probably notice that Englisch is not my language.I think you mean that the barrel shaped spring section spins around when the plug is not inserted into the socket.
But isn't it squashed and held tight against the barrel of the plug when it is inserted?
Anyway the plugs with solid connection at one end and a cover like end cap have better properties in my experience (so personal stuff, not necessarily scientifically approved fact by audio professors). The testing with very high current is fun and makes matters clear. The one solid pin types with only one sideways mounted spring are also not very good. The types with cross like cutting (4 contacts) made of zamak with gold plating suffer from "lazy" spring contacts quite soon and can not be taken seriously. Sorry but even audio brands make mediocre stuff if you have simple basic requirements. Apparently many are satisfied when the looks of the connectors and sockets are OK. It is jewelry sometimes not even applying basic principles.
1. conductivity
2. current rating
3. contact resistance (also over time)
4. corrosion resistent
5. retention mechanism (if applicable/possible) -> USB, HDMI are examples of not having that.
Those fake (at least that is what I think) Nakamichi banana plugs sold literally everywhere are not bad at all. To my surprise they turned out to be OK. These are fully conductive so care must be taken that they are not used in amplifiers with sockets very close to each other. They are the opposite of those terrible BFA 🙂
Last edited:
Very good to use & non magnetic. (no ferrous) 👍Those fake (at least that is what I think) Nakamichi banana plugs sold literally everywhere are not bad at all. To my surprise they turned out to be OK. These are fully conductive so care must be taken that they are not used in amplifiers with sockets very close to each other. They are the opposite of those terrible BFA 🙂
Just so everyone knows, this was my bad. For several years I have assumed that J-P on this forum was one and the same person as one by the same name on another forum. From a distance, the similarities and coincidences are remarkable.Unlikely as I am not on any other forum. Fake news and somewhat personal as well 🙂
If you read my post in this thread carefully you'll see I diss myself for using steel based coax cable. With steel based core that is, not the braid.
But it was a wrong assumption. I have apologized to J-P in private.
Thanks, no problem. I did not realize I had a Doppelgänger. I just hope the other chap is more friendly 😉
Ok, so now we are dating ourselves when it comes to wire wrapping. Most of mine was done when I worked for the Bell System. Now I have to ask what soldering tool do you use? I found that until I stepped up to a decent tool, my work was embarrassing.Have always used 63/37 solder, and never any problems, even with heat and decades of use.
Lots of wire wrapping under my belt as well, back in the era before cheap and easy pcbs for prototypes.
Also, the soldering of steel contacts must take a higher temp, no?
And lastly, some of the solder rework that I do is still a bit frustrating because of the high melting temperature of the newer solder used.
Ok, sorry. Done side stepping this thread.
Some use solder, for example, as the basis of making a connection, yet it seems counterintuitive to me. I still wrap a connection when possible or 'lock' the leads of a resistor/component on a circuit board in order to have that physical connection first.
So, the question is, why bother with a good connection if what happens after it is compromised?
Oh yes, how many thousands of wire wraps have I made? Round wire on a square post. 4 1/2 wraps minimum per the spec. That certainly is not easily bested. I agree as well that solder makes it better, and of course permanent. Beyond that, I am inclined to wonder which solder is best qualified. It's content and physical/chemical properties do have merit. I have ended up using only Wonder Solder for my purposes, mostly because of its ease of use and decent reputation.
I suppose that it is a whole 'nother topic when it comes to mechanical connections and their benefits over other methods.
I chose a "belt & braces" approach when doing my Cross-overs
Where possible, components were connected directly to each other by hooking the leads together & then soldering. Solder used is lead free silver solder (tin/silver/copper by Shenmao).
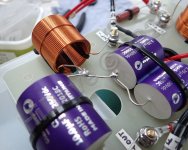
Any cables were terminated with a eye or push tab type termination. Wire tinned, then terminal/eye crimped, then soldered & heat shrink over.
Comparison of some different versions (some soldered, others not, final version was soldered) I made:-
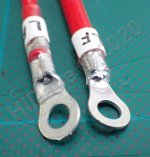
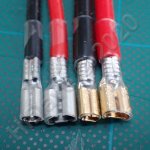
When a cable had to be joined to the board the lead of the last component was wound once around the brass "post" & then the cable eye was placed over it & then a serrated nut. Washer was placed over bolt before the component lead was wound once, brass bolts & stainless nuts/washers were used. Direct compressed contact between the eye & the component lead.
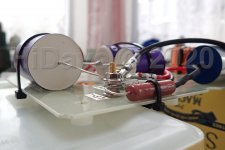
I've always used Weller closed loop stations. The tips last forever, and also have plenty of heat capacity.Now I have to ask what soldering tool do you use? I found that until I stepped up to a decent tool, my work was embarrassing. Also, the soldering of steel contacts must take a higher temp, no?
And lastly, some of the solder rework that I do is still a bit frustrating because of the high melting temperature of the newer solder used.
Would never recommend no-lead solder for DIY, only 63/37.
No doubt, we think alike. Here is my first cross over made only a short time ago. Like you, the wires are wrapped around the lead of an adjoining component. I think that is the number one way for me. OTOH, I wanted to be able to take the crossover out easily, as I may be changing some components, so I used stiff miniature spring connections for incoming and outgoing leads. The whole thing is supported by 1/2" Corian just because it was leftover in my shop and works easily.I chose a "belt & braces" approach when doing my Cross-overs
Where possible, components were connected directly to each other by hooking the leads together & then soldering. Solder used is lead free silver solder (tin/silver/copper by Shenmao).
View attachment 1117578
Any cables were terminated with a eye or push tab type termination. Wire tinned, then terminal/eye crimped, then soldered & heat shrink over.
Comparison of some different versions (some soldered, others not, final version was soldered) I made:-
View attachment 1117580
View attachment 1117581
When a cable had to be joined to the board the lead of the last component was wound once around the brass "post" & then the cable eye was placed over it & then a serrated nut. Washer was placed over bolt before the component lead was wound once, brass bolts & stainless nuts/washers were used. Direct compressed contact between the eye & the component lead.
View attachment 1117582
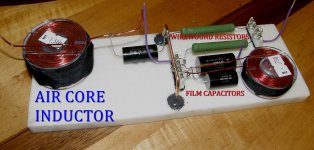
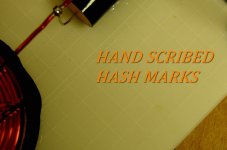
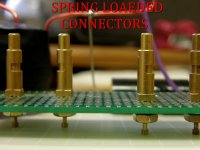
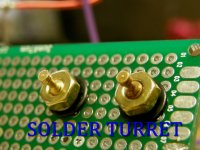
Your crossovers are worthy of being on display.Washer was placed over bolt before the component lead was wound once, brass bolts & stainless nuts/washers were used. Direct compressed contact between the eye & the component lead.
Pity the workmanship is hidden inside the box.
Just a minor question.
Why the stainless nuts/washers onto the brass bolt?
Does all brass have an issue?
While on this subject, &, as the forum is DIY focused, I was hoping to harness everyone's knowledge and creativity towards a related issue.
We appear to be in agreement that generally retail offerings of speaker related parts such as banana plugs, speaker terminals, wiring, fasteners, tabs, solder and sundry are on the whole of inferior quality (low grade copper, cheaply formulated alloys & solder, poor mechanical strength, come to mind) regardless of price.
There also appears to be general agreement (not all) that ferrous in the signal path should be avoided.
I was hoping for ideas to DIY design speaker terminals!
We appear to be in agreement that generally retail offerings of speaker related parts such as banana plugs, speaker terminals, wiring, fasteners, tabs, solder and sundry are on the whole of inferior quality (low grade copper, cheaply formulated alloys & solder, poor mechanical strength, come to mind) regardless of price.
There also appears to be general agreement (not all) that ferrous in the signal path should be avoided.
I was hoping for ideas to DIY design speaker terminals!
- Non ferrous,
- Use of repurposed/recycled parts/material made at a time when such parts were made to a standard.
- And/or utilize well priced off the shelf new parts of an acceptable quality.
- Simplicity of design, & aesthetically pleasing.
- Functional (low resistance, good mechanical strength & easy to use).
I don't see too much of an issue with brass, Cliff.
It's simply an alloy of copper and is not ferromagnetic.
Some of the atoms of copper in the metallic crystals are substituted by zinc atoms which are similar in size to copper atoms.
The end result is a material with an electrical conductivity about one third that of copper - not a problem when using brass in a small bolt or speaker plug.
It's simply an alloy of copper and is not ferromagnetic.
Some of the atoms of copper in the metallic crystals are substituted by zinc atoms which are similar in size to copper atoms.
The end result is a material with an electrical conductivity about one third that of copper - not a problem when using brass in a small bolt or speaker plug.
Non ferrous
I would say 'non-ferromagnetic'.
Ferrous indicates a compound or alloy containing iron.
Iron, cobalt and nickel are examples of ferromagnetic elements.
Your crossovers are worthy of being on display.
Pity the workmanship is hidden inside the box.
Just a minor question.
Why the stainless nuts/washers onto the brass bolt?
Does all brass have an issue?
Thanks!....& yes I have been thinking about a clear Perspex lid for the cross-overs!
Stainless steel is not as electrically conductive as brass....so any signal that is "stray" from the cable eye or component lead will only flow into the brass bolt/post & not the nuts/washers as it chooses the path of least resistance. As stainless steel is stronger then brass, the lowest washers under the component/eye will not deform when tightening up the nuts. Also the nuts have a wide flange which is serrated on the underside which grips & locks the cable eye wherever I rotate the eye to to, so it keeps its place & orientation to the brass bolt/post. I could not find the same design in brass.
While on this subject, &, as the forum is DIY focused, I was hoping to harness everyone's knowledge and creativity towards a related issue.
We appear to be in agreement that generally retail offerings of speaker related parts such as banana plugs, speaker terminals, wiring, fasteners, tabs, solder and sundry are on the whole of inferior quality (low grade copper, cheaply formulated alloys & solder, poor mechanical strength, come to mind) regardless of price.
There also appears to be general agreement (not all) that ferrous in the signal path should be avoided.
I was hoping for ideas to DIY design speaker terminals!
- Non ferrous,
- Use of repurposed/recycled parts/material made at a time when such parts were made to a standard.
- And/or utilize well priced off the shelf new parts of an acceptable quality.
- Simplicity of design, & aesthetically pleasing.
- Functional (low resistance, good mechanical strength & easy to use).
4mm Test/measurement sockets with 6.3mm push tabs on the rear by MC/Staubli is what I used:-
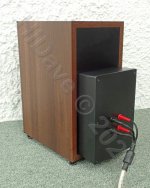
Last edited:
- Home
- Design & Build
- Parts
- magnetic parts, and where to avoid them?