Now I get it. I'm like that a lot. I read things differently than they were intended.
I actually used the idea of a long bolt from the back of a passive radiator to assist in mounting/bracing of a sub cabinet once. I do understand what you are referring to here, remembering KEF having done the same thing long ago... or was it Canton?
God, hardware, especially stainless and brass has become very high. Still I won't change unless there is an equal procedure that does the same thing, is convenient, and costs less.
I still think its a better way of supporting the driver's main mass & it also clamps the front & rear panels together......so double bonus!!...don't know why more manufacturers don't use it!
Stainless & brass screws/bolts are quite cheap over here I use these websites:-
https://www.accu.co.uk/
https://www.westfieldfasteners.co.uk/
Not in the case of the ones (WBT) that I bought...
The product description sounds good, but the science says the copper will migrate into the gold plating of the WBT plugs, reducing the resistance to corrosion over time.
Be assured that I'm not arguing with your choice. Your plugs do have the advantage of eliminating the ferromagnetic material, but I guess there is no such thing as a free lunch! 🙂
Yes, and in fact, the last sub that I built for myself used the same thinking by applying a thick bead of silicone in two places where the driver was very close to an existing MDF brace. Just made sense to connect that brace up to the very heavy driver frame.I still think its a better way of supporting the driver's main mass & it also clamps the front & rear panels together..
I did take a peek at your upgrading of those speakers and am happy to see your work is likely better than the original, parts included. Takes a lot more time to do something right, doesn't it?
I take it this is a bit of a tongue-in-cheek response. I agree that it's not necessary, and it may not even be sufficient. The big problem with this is keeping the metal above that temperature! When the temperature drops, it goes back to being ferromagnetic, and if it's in a magnetic field (such as on Earth), it will be slightly magnetized again as it's cooling.If you're really concerned, just heat the offending screw beyond its Curie temperature when it will lose its magnetism. For iron and steel, this is 770 degrees C.
Standard torch burners can give temperatures up to 800 degrees C. Please note that I am being scientifically correct and I really don't think the procedure is necessary! 🙂
But more generally, any kind of magnetic material near a wire, or even conducting the signal for a short distance, will be very unlikely to make an audible or measurable change. Recall that in tube power amplifiers, the WHOLE SIGNAL goes through a transformer - it gets converted totally into a magnetic field and goes into the iron from the primary, and then back to electricity in the secondary!
Going directly through a transformer DOES have an audible effect on the sound, but it's rarely horrible (only when the iron saturates, which is analogous to clipping). This sound is even desired by some. Small signal transformers, often used in recording studio equipment at microphone inputs and to isolate signal paths from ground loops, add a "sound" despite manufacturers trying to minimize it, and is often regarded as making the sound more pleasing.
I take it this is a bit of a tongue-in-cheek response.
You can take it that my tongue was very firmly in my cheek!

This can be seen after the warranty period when stains appear in the gold finish. Also the transparent plastic used on those WBT plugs will crack. I have the previous series of those here. The pressure system works perfectly but should not be overdone with some recent sockets. Expensive stuff gives no guarantee at all that it will last longer. On the contrary. Most "for audio" stuff is ready for the bin in a few years time.The product description sounds good, but the science says the copper will migrate into the gold plating of the WBT plugs, reducing the resistance to corrosion over time.
If one is busy with this gold plated stuff for some time one will appreciate stuff that shines less but lasts longer. It is a pity Hirschmann did not make connectors for somewhat thicker cabling. Silver plated "multi-spring" Hirschmann banana plugs and sockets were among the very best with regards to contact resistance and longevity. I have 30 years old ones that look and perform like new. Lab stuff but rarely seen in audio due to the maximum cable gauge.
My tip is to be cautious with all recently produced materials and check shiny "for audio" stuff with a magnet, do a destructive test with one of them (when it seems molded material/zamak) and only use plated brass parts. I was given "audiophile" RCA/cinch connectors that were gold plated steel!
Last edited:
I am hoping that this question is of relevance concerning connectors as such. With a twist on the idea of connecting I believe that good mechanical connections must be made beyond the input, or even output of a device. I value the idea about the importance of the best possible connection at either the input or output yet shake my head sometimes when I see the deficiency of such thinking has occurred after our intent to begin with. Some use solder, for example, as the basis of making a connection, yet it seems counterintuitive to me. I still wrap a connection when possible or 'lock' the leads of a resistor/component on a circuit board in order to have that physical connection first.
So, the question is, why bother with a good connection if what happens after it is compromised?
So, the question is, why bother with a good connection if what happens after it is compromised?
Oh yes, how many thousands of wire wraps have I made? Round wire on a square post. 4 1/2 wraps minimum per the spec. That certainly is not easily bested. I agree as well that solder makes it better, and of course permanent. Beyond that, I am inclined to wonder which solder is best qualified. It's content and physical/chemical properties do have merit. I have ended up using only Wonder Solder for my purposes, mostly because of its ease of use and decent reputation.
I suppose that it is a whole 'nother topic when it comes to mechanical connections and their benefits over other methods.
I suppose that it is a whole 'nother topic when it comes to mechanical connections and their benefits over other methods.
Used such cable by mistake not so long ago. The amplifier just did not sound right.
Same happened to me years ago with Belden 9454. It looked great for audio, with foam polyethylene
dielectric, but had a hard brightness in the upper midrange. After reading the data sheet more carefully,
it turns out the inner conductor was tinned copper clad steel. Never again.
https://edesk.belden.com/products/techdata/english/pdf/9454.pdf
rayma,
Yes. I cannot state the difference in sound since I did not use this example of wire for signal, but there was this wire that I tried once for power connections that was used at NASA. Ok, Let's just see what this wire is like. Didn't stop to question the requirements needed by the space program for this wire. When it came, what I had was some of the hardest wire that I ever have had to work with! Very stiff stranded wire with insulation that was fireproof (read nearly impossible to strip). Springy and not as easy to solder, I soon figured that whoever used this wire in practice had a different tool set than I did. In short it wasn't worth much too me. Hmm. I should put a magnet near it just for kicks.
Yes. I cannot state the difference in sound since I did not use this example of wire for signal, but there was this wire that I tried once for power connections that was used at NASA. Ok, Let's just see what this wire is like. Didn't stop to question the requirements needed by the space program for this wire. When it came, what I had was some of the hardest wire that I ever have had to work with! Very stiff stranded wire with insulation that was fireproof (read nearly impossible to strip). Springy and not as easy to solder, I soon figured that whoever used this wire in practice had a different tool set than I did. In short it wasn't worth much too me. Hmm. I should put a magnet near it just for kicks.
Suspect the results will be magnetic.I should put a magnet near it just for kicks.
Have always used 63/37 solder, and never any problems, even with heat and decades of use.Oh yes, how many thousands of wire wraps have I made? Beyond that, I am inclined to wonder which solder is best qualified.
Lots of wire wrapping under my belt as well, back in the era before cheap and easy pcbs for prototypes.
Oh J-P, on another forum you jumped on me for dissing the use of coax with steel in the braid for audio... and suggested I use DBT to sort it out.Used such cable by mistake not so long ago. The amplifier just did not sound right. The cable was airplane cable with teflon isolation etc. but the core turned out to be iron/steel and magnetic.
Here it seems you actually do trust your ears, at least sometimes.
Same with the Belden models that had polyprop insulation and foil shield with drain wire. Horrible for audio, hard and brittle upper mids. Yet many recording studios back in the 70's and 80's were wired with thousands of feet of the stuff.Same happened to me years ago with Belden 9454.
Not surprising, considering the sound on some of the LPs of that era.
It had nice low capacitance, too. Oh well.
It had nice low capacitance, too. Oh well.
"dammed if you do, damned if you don't"..springs to mind!.. 🤣The product description sounds good, but the science says the copper will migrate into the gold plating of the WBT plugs, reducing the resistance to corrosion over time.
Be assured that I'm not arguing with your choice. Your plugs do have the advantage of eliminating the ferromagnetic material, but I guess there is no such thing as a free lunch! 🙂
This can be seen after the warranty period when stains appear in the gold finish. Also the transparent plastic used on those WBT plugs will crack. I have the previous series of those here. The pressure system works perfectly but should not be overdone with some recent sockets. Expensive stuff gives no guarantee at all that it will last longer. On the contrary. Most "for audio" stuff is ready for the bin in a few years time.
If one is busy with this gold plated stuff for some time one will appreciate stuff that shines less but lasts longer. It is a pity Hirschmann did not make connectors for somewhat thicker cabling. Silver plated "multi-spring" Hirschmann banana plugs and sockets were among the very best with regards to contact resistance and longevity. I have 30 years old ones that look and perform like new. Lab stuff but rarely seen in audio due to the maximum cable gauge.
My tip is to be cautious with all recently produced materials and check shiny "for audio" stuff with a magnet, do a destructive test with one of them (when it seems molded material/zamak) and only use plated brass parts. I was given "audiophile" RCA/cinch connectors that were gold plated steel!
I agree with you that the WBT Banana plugs do look "fragile" compared to my previous ones which look similar but are from a different brand (Fisual). I was careful on insertion & tightening in both cable into plug & plug into Amp sockets.
I only purchased these as I am trying to eliminate all extraneous metal from the signal chain, & improve the quality of the metal that is left in the chain. Compared to my previous set (Fisual "deluxe"), these have quite a bit less metal in them & the metal is gold plated (nickel free), copper, whereas the other set is gold plated brass (& the plating has presumably got nickel in it). However the WBT ones are about x4 the price of the Fisual ones!!
Fisual top, WBT bottom:-
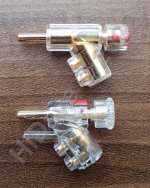
I agree with the use of "Test/measurement" leads, connectors, plugs, etc. as the quality is good enough to to be used on the equipment that is used to "test/measure" Hi-fi..!!
In my rebuild of the speakers, for the back panel of the speaker cross-over box I used MC/Staubli shrouded, test/measurement, gold plated brass plugs & matching, 4mm diameter back panel sockets (with 6.3mm push tabs). Unfortunately they don't do a version with a 45deg angle like my Fisual & WBT plugs for the back of the Amp, otherwise I would have purchased those instead!
Fisual straight 4mm banana plugs left, & MC/Staubli on the right. Again, much less metal, & better sprung "grips" on the MC/Staubli.
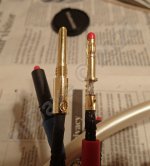
Unlikely as I am not on any other forum. Fake news and somewhat personal as well 🙂Oh J-P, on another forum you jumped on me for dissing the use of coax with steel in the braid for audio... and suggested I use DBT to sort it out.
Here it seems you actually do trust your ears, at least sometimes.
If you read my post in this thread carefully you'll see I diss myself for using steel based coax cable. With steel based core that is, not the braid.
The right one has the worst contact system of all. Separate part with meagre spring force and twice a contact resistance. Cheap construction. Point being that the quality that I like can hardly be found anymore. Almost anything recent is cheaply made and sold for small prices or it is cheaply made and sold for premium prices. One does hardly see or notice differences between A and B or C brands as all is about the same. BTW I don't see the relevance of having less metal if the metal is of known good reputation/conductivity like brass/copper.Fisual straight 4mm banana plugs left, & MC/Staubli on the right. Again, much less metal, & better sprung "grips" on the MC/Staubli.
View attachment 1117319
Out of curiousity I looked up availability of the Hirschmann banana plugs and noticed these seem to have evolved to a modernized/updated/connector 2.0 gold plated "for audio" version (oh oh) suited for 2.5mm2 cable and hopefully not produced in the country whose name we should not say. The specs say these have 3 milliOhm contact resistance and 30V AC rating. We used the old verion with 230V AC and never had any issues.
https://www.reichelt.de/de/nl/banaa...ding-verguld-buela-30k-au-sw-p160514.html?r=1
https://cdn-reichelt.de/documents/datenblatt/D100/BUELA_30_K_930727XXX.pdf
Last edited:
The right one has the worst contact system of all. Separate part with meagre spring force. Cheap construction.
I don't see the relevance of having less metal if the metal is of known good reputation/conductivity like brass/copper.
Spring force in their matching sockets it very good!!
I look at like this:- Worrying about trying to get a perfect cable/twist/material, & amp construction, source construction etc...then you go & have a big lump of metal as a connector!
I know I have "a big lump of metal" in the air cored inductors, but they are doing a specific function that requires the long copper wire....connectors do not require a big lump of metal.
- Home
- Design & Build
- Parts
- magnetic parts, and where to avoid them?