I've got some LAB12 speakers, wood, fasteners, MDF etc ready to go. I'm going to build one LAB12, and if I like it, I'm going to be building some more for a DrumNBass setup.
I have all the tools and necessary skills to build the thing and make it look great, but I'm not sure what to buy for a few things:
1. terminal plates for 1/4" plug (mono?)- where do I get the best terminals to connect 1/4" plug into and what gauge of wire should go between the terminal and the speaker? I was assuming 8-gauge, but I've seen images on the forums with skinny wires between the terminals and the speaker, doesn't look right to me.
2. What's a good heavy duty recessed handle? Do any of them allow you to lift something this heavy without cutting off the circulation to your fingertips? (like a thicker handle)
3. I was thinking about cutting off the back lower corner and putting wheels there where the Pi 12 has wheels - anyone ever drag these around with the wheels? Is it helpful, or just a PIA? Seems like, even thought more effort is required, one person on each side grasping a handle will have better control...
Thanks in advance, will post images once we get started.
-Bouki
I have all the tools and necessary skills to build the thing and make it look great, but I'm not sure what to buy for a few things:
1. terminal plates for 1/4" plug (mono?)- where do I get the best terminals to connect 1/4" plug into and what gauge of wire should go between the terminal and the speaker? I was assuming 8-gauge, but I've seen images on the forums with skinny wires between the terminals and the speaker, doesn't look right to me.
2. What's a good heavy duty recessed handle? Do any of them allow you to lift something this heavy without cutting off the circulation to your fingertips? (like a thicker handle)
3. I was thinking about cutting off the back lower corner and putting wheels there where the Pi 12 has wheels - anyone ever drag these around with the wheels? Is it helpful, or just a PIA? Seems like, even thought more effort is required, one person on each side grasping a handle will have better control...
Thanks in advance, will post images once we get started.
-Bouki
Oh yeah, and I want to be able to connect from one speaker to the next with these terminals, so that I can power 4 Horns with one amp. So maybe terminals with in and out, unless it's not recommended.
You shouldn't even bother.
In no particular order:
One Lab horn won't do squat, they're designed to be used in groups of four to eight per side.
No two people will be able to carry a Lab 12 made from MDF, and the glue joints will creak, crack, and pop. If you do make anything for portable use, use plywood.
Use of 1/4" plugs for this kind of power is not sane. Use Speakons. One cabinet is 2.15 ohms DC (maybe 3 ohms AC), don't even think you can drive more than one per channel.
If you're only going to build a few, try Danley's new tapped horn designs. For a smaller bulk they out-perform the traditional horn. If you have a tractor-trailer rig, forklift, a big crew, and lots of funds, go Lab 12.
In no particular order:
One Lab horn won't do squat, they're designed to be used in groups of four to eight per side.
No two people will be able to carry a Lab 12 made from MDF, and the glue joints will creak, crack, and pop. If you do make anything for portable use, use plywood.
Use of 1/4" plugs for this kind of power is not sane. Use Speakons. One cabinet is 2.15 ohms DC (maybe 3 ohms AC), don't even think you can drive more than one per channel.
If you're only going to build a few, try Danley's new tapped horn designs. For a smaller bulk they out-perform the traditional horn. If you have a tractor-trailer rig, forklift, a big crew, and lots of funds, go Lab 12.
Portable needs thick plywood.
Wheels work well when retracted into the chopped off corner.
One amp to each Labhorn. Or maybe even better with one amp to each driver using a 4pole Speakon.
12 Labhorns for flying in free space.
6 Labhorns for floor mounted.
3 Labhorns if two reflective surfaces gives effective quarter space loading.
Go and re-read Tom Danley's paper on designing the Labhorn. It is very instructive and explains what needs to be done to get the best out of these speakers.
Wheels work well when retracted into the chopped off corner.
One amp to each Labhorn. Or maybe even better with one amp to each driver using a 4pole Speakon.
12 Labhorns for flying in free space.
6 Labhorns for floor mounted.
3 Labhorns if two reflective surfaces gives effective quarter space loading.
Go and re-read Tom Danley's paper on designing the Labhorn. It is very instructive and explains what needs to be done to get the best out of these speakers.
I most definitely will 'bother'.
However, thanks for the answers. We're building 4 by the way - just building one to start off with. (I thought I made that clear in the original post.) My buddy plans to power them (remember - 4, as in FOUR) with one Crown 5000 watt amp.
Plywood for sure. I need a link because I can't find Danley's paper on the labhorn. I have only found the schematics so far. Any links to info on the 2nd generation labhorn would be great.
However, thanks for the answers. We're building 4 by the way - just building one to start off with. (I thought I made that clear in the original post.) My buddy plans to power them (remember - 4, as in FOUR) with one Crown 5000 watt amp.
Plywood for sure. I need a link because I can't find Danley's paper on the labhorn. I have only found the schematics so far. Any links to info on the 2nd generation labhorn would be great.
Using a Crown vz5000?
Each woofer in the Lab 12 is about 5R2 at 40hz, so one cabinet with the drivers in parallel will be 2R6 and the amp will go into ODEP driving two cabinets in parallel (a 1R3 load).
Also, the Lab12 woofer will go into meltdown with that kind of power on dance music with its 50% duty cycle in the bass.
Have fun.
Each woofer in the Lab 12 is about 5R2 at 40hz, so one cabinet with the drivers in parallel will be 2R6 and the amp will go into ODEP driving two cabinets in parallel (a 1R3 load).
Also, the Lab12 woofer will go into meltdown with that kind of power on dance music with its 50% duty cycle in the bass.
Have fun.
Hey, that's great, so what would YOU use to power them?
I was on another forum where averyone was recommending this amp to run four labhorns. I assumed that several unanimous people couldn't be wrong.
I was on another forum where averyone was recommending this amp to run four labhorns. I assumed that several unanimous people couldn't be wrong.
BTW, there's no need to be so arrogant.
This is a forum where people come and ask questions, and knowledgable people, like yourself, answer them. I looked at your other posts - all informative and helpful. Why did you waste your time on me? If my question's not worth your time, then ignore the freaking post.
This is a forum where people come and ask questions, and knowledgable people, like yourself, answer them. I looked at your other posts - all informative and helpful. Why did you waste your time on me? If my question's not worth your time, then ignore the freaking post.
Go to prosoundweb.com and you will find all the information and help needed to build and use Labhorns.
Thanks, I'll go to prosoundweb.
If an administrator sees this message, please delete this thread. I'm sorry to have wasted you guys' time. I'm obviously just an annoyance here.
If an administrator sees this message, please delete this thread. I'm sorry to have wasted you guys' time. I'm obviously just an annoyance here.
Hi boukisan,
No need to delete the thread. Many members pointed you in the proper direction.
You asked questions and got responses from some knowledgeable people. I happen to agree with djk and the others. They are experts among many here.
What you proposed to do with one amp is not reasonable if your speakers are all in parallel. 1/4" jacks and plugs are useless for this purpose. I've repaired tons of amps over the years because people persist in using a signal connector that is prone to shorting, for high current applications. These simple facts tell everyone here that your setup is not being done properly.
I gather you didn't hear what you wanted to hear. It is possible that you have not phrased your question so it was not understood.
-Chris
No need to delete the thread. Many members pointed you in the proper direction.
You asked questions and got responses from some knowledgeable people. I happen to agree with djk and the others. They are experts among many here.
What you proposed to do with one amp is not reasonable if your speakers are all in parallel. 1/4" jacks and plugs are useless for this purpose. I've repaired tons of amps over the years because people persist in using a signal connector that is prone to shorting, for high current applications. These simple facts tell everyone here that your setup is not being done properly.
I gather you didn't hear what you wanted to hear. It is possible that you have not phrased your question so it was not understood.
-Chris
I agree, I understand about 1/4 inch plugs - not doing that. I am using speakons, I ordered the plugs yesterday. Don't let that distract from my main topic - wiring my labhorns.
To rephrase my question, do I need to wire them series or parallel?
Basically, since so many of my assumptions (and advice collected from this and other forums) are turning out to be wrong: what do I need to do to run four labhorns as far as wiring and amp selection is concerned?
However, this is probably answered by doing research. I didn't want to spend 3 hours reading old threads, but I will do that if you think I should. Like i said, I don't want to waste anyones time here - because I don't feel like reading retorts, whether there's a half-answer in there or not.
To rephrase my question, do I need to wire them series or parallel?
Basically, since so many of my assumptions (and advice collected from this and other forums) are turning out to be wrong: what do I need to do to run four labhorns as far as wiring and amp selection is concerned?
However, this is probably answered by doing research. I didn't want to spend 3 hours reading old threads, but I will do that if you think I should. Like i said, I don't want to waste anyones time here - because I don't feel like reading retorts, whether there's a half-answer in there or not.
If my memory serves me right, the LAB12 drivers in the Labhorn are wired in parallel. I think it results in an impedance of about 3.2ohms. There are quite a few people who use four cabs in series/parallel mode, driven with bridged QSC PL series amps.
Alternately, you could have a look at 12Pi, a derivative of the Labhorns, done by Wayne Parham. These have an impedance of 6ohms per cab using the same dual LAB12 speakers. However, they are more difficult to build, requiring Heat pipes/sinks to be machined out in a lathe.
djk, who replied in this thread earlier, gave the numbers to do a tapped horn using Eminence LF3015 drivers, but I couldn't figure out as to how exactly the box dimensions would have to be laid out. If you can figure that out from the Tapped Horn Collaborative thread, you will have a much easily built and great performing bass cab.
Alternately, you could have a look at 12Pi, a derivative of the Labhorns, done by Wayne Parham. These have an impedance of 6ohms per cab using the same dual LAB12 speakers. However, they are more difficult to build, requiring Heat pipes/sinks to be machined out in a lathe.
djk, who replied in this thread earlier, gave the numbers to do a tapped horn using Eminence LF3015 drivers, but I couldn't figure out as to how exactly the box dimensions would have to be laid out. If you can figure that out from the Tapped Horn Collaborative thread, you will have a much easily built and great performing bass cab.
"If my memory serves me right, the LAB12 drivers in the Labhorn are wired in parallel. I think it results in an impedance of about 3.2ohms. There are quite a few people who use four cabs in series/parallel mode, driven with bridged QSC PL series amps."
Wayne's graphs on his 12Pi show an impedance minima of less that 2R6 at 40hz and just over 3R at 65hz.
"Alternately, you could have a look at 12Pi, a derivative of the Labhorns, done by Wayne Parham. These have an impedance of 6ohms per cab using the same dual LAB12 speakers. However, they are more difficult to build, requiring Heat pipes/sinks to be machined out in a lathe."
The heatsinks are not required. If you use them the driver will handle twice the power, this applies to any Lab 12 driver (or HL-10C).
"djk, who replied in this thread earlier, gave the numbers to do a tapped horn using Eminence LF3015 drivers, but I couldn't figure out as to how exactly the box dimensions would have to be laid out. If you can figure that out from the Tapped Horn Collaborative thread, you will have a much easily built and great performing bass cab."
The 4015LF would be a better driver to pound on, its rated for 700W.
Here is one Lab 12 with parallel wired drivers (less than 3R) vs two 4015LF parallel wired in a tapped horn of slightly more bulk (3R minimum):
Wayne's graphs on his 12Pi show an impedance minima of less that 2R6 at 40hz and just over 3R at 65hz.
"Alternately, you could have a look at 12Pi, a derivative of the Labhorns, done by Wayne Parham. These have an impedance of 6ohms per cab using the same dual LAB12 speakers. However, they are more difficult to build, requiring Heat pipes/sinks to be machined out in a lathe."
The heatsinks are not required. If you use them the driver will handle twice the power, this applies to any Lab 12 driver (or HL-10C).
"djk, who replied in this thread earlier, gave the numbers to do a tapped horn using Eminence LF3015 drivers, but I couldn't figure out as to how exactly the box dimensions would have to be laid out. If you can figure that out from the Tapped Horn Collaborative thread, you will have a much easily built and great performing bass cab."
The 4015LF would be a better driver to pound on, its rated for 700W.
Here is one Lab 12 with parallel wired drivers (less than 3R) vs two 4015LF parallel wired in a tapped horn of slightly more bulk (3R minimum):
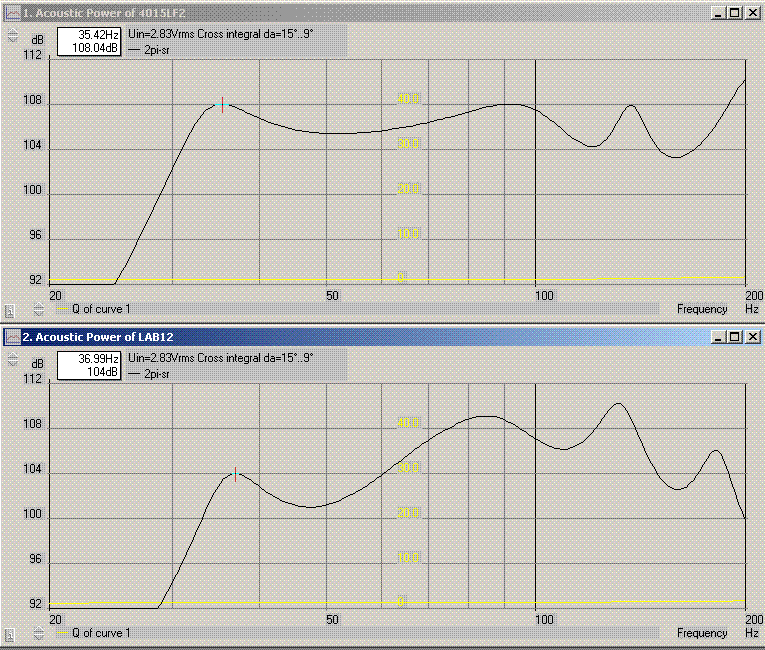
Boukisan,
I used 12 ga wire on my LABhorns,each driver has a set of terminals,so that I have the option of wiring them series or parallel.In your case,I would recommend wiring them series-parallel,two cabinets/ch.The amp will then see an impedance equal to one cabinet/ch.
5000 w into four cabinets seems quite reasonable,many people have been using 1600-2000w/cabinet with no problems.A 30 hz HP filter is recommened,however.
Although the LAB12 driver is spec at 400w,it is considerably higher when used in multiple cabinets,plus a very large portion of the total power is going out of the horn as acoustical power.
If you make them out of plywood,they will weigh about 230 Lbs ea.
MDF will weigh about 300 lbs,or so,and have little strength or moisture resistance.
Unfortunately,the info on the LABhorns is kind of disjointed,being spread out in posts over the course of almost a year(2002) on the prosoundweb.com/lsp/ Do a search in the archives for Tom Danley.
Good Luck,and post pics if you can.
I used 12 ga wire on my LABhorns,each driver has a set of terminals,so that I have the option of wiring them series or parallel.In your case,I would recommend wiring them series-parallel,two cabinets/ch.The amp will then see an impedance equal to one cabinet/ch.
5000 w into four cabinets seems quite reasonable,many people have been using 1600-2000w/cabinet with no problems.A 30 hz HP filter is recommened,however.
Although the LAB12 driver is spec at 400w,it is considerably higher when used in multiple cabinets,plus a very large portion of the total power is going out of the horn as acoustical power.
If you make them out of plywood,they will weigh about 230 Lbs ea.
MDF will weigh about 300 lbs,or so,and have little strength or moisture resistance.
Unfortunately,the info on the LABhorns is kind of disjointed,being spread out in posts over the course of almost a year(2002) on the prosoundweb.com/lsp/ Do a search in the archives for Tom Danley.
Good Luck,and post pics if you can.
Thanks, I finally saw the link on the bottom of the prosound page with the diagrams. I've been to that page a million times. More emphasis should be put on the link to the LABhorn part of that forum. I'll spend a few hours there.
Also, thanks for the truly informative posts. I'll have to contribute something in return, hopefully more than pictures.
I ordered the speakon plates with two plugs so that we would have more wiring options. Series-parallel wiring like this makes sense to my buddy who's wiring it, so it sounds good to me. Hopefully, we can wire it so that multiple configurations are possible as we scale up - that's why I got the two-plug plates.
I've been eyeing Wayne Parham's design for about two months now, and my favorite takeaway is the heat diffuser. I'm going to incorporate my slightly modified version of the heat diffuser from the Pi12 cabinet into this LABhorn. I'm installing heatsinks for insurance, not to push more wattage through them (for now). I'm not sure if anyone has tried this - problems, warnings? It looks like clearance is the only problem, and I know I don't want to change the dimensions of the horn throat. I'm machining them from the same type of aluminum, but I'm going to change the design to have more surface area contact with the aluminum plate, and I'm using thermally-conductive silicon paste to transfer the heat more efficiently.
Here's my only concern: Groups of 4 LABhorns go lower/louder than one or two together - is this achieved by the horn mouths being exactly flush, as opposed to almost flush? I mean to say, do you think an additional 1-2" of space between each horn mouth will dampen the effect? However, I understand from what I've read on the forum that basswaves are longer, slower waves - so they aren't dependant on extremely accurate acoustics like higher frequency sounds - so maybe an inch or so won't matter... (This way we can have our heatsink insurance.)
As far as weight is concerned, we decided to get some heavy duty casters and mount them on the back like so many others have done - seems like the best way to go. We are considering the idea of designing a rack system to mount to the back of the lab that works with a special fork. We would cut the foot off of an industrial hand truck and attach this slightly longer reinforced fork in its place. (I'm thinking about 230lbs, and stairs.)
Thanks again...
Also, thanks for the truly informative posts. I'll have to contribute something in return, hopefully more than pictures.
I ordered the speakon plates with two plugs so that we would have more wiring options. Series-parallel wiring like this makes sense to my buddy who's wiring it, so it sounds good to me. Hopefully, we can wire it so that multiple configurations are possible as we scale up - that's why I got the two-plug plates.
I've been eyeing Wayne Parham's design for about two months now, and my favorite takeaway is the heat diffuser. I'm going to incorporate my slightly modified version of the heat diffuser from the Pi12 cabinet into this LABhorn. I'm installing heatsinks for insurance, not to push more wattage through them (for now). I'm not sure if anyone has tried this - problems, warnings? It looks like clearance is the only problem, and I know I don't want to change the dimensions of the horn throat. I'm machining them from the same type of aluminum, but I'm going to change the design to have more surface area contact with the aluminum plate, and I'm using thermally-conductive silicon paste to transfer the heat more efficiently.
Here's my only concern: Groups of 4 LABhorns go lower/louder than one or two together - is this achieved by the horn mouths being exactly flush, as opposed to almost flush? I mean to say, do you think an additional 1-2" of space between each horn mouth will dampen the effect? However, I understand from what I've read on the forum that basswaves are longer, slower waves - so they aren't dependant on extremely accurate acoustics like higher frequency sounds - so maybe an inch or so won't matter... (This way we can have our heatsink insurance.)
As far as weight is concerned, we decided to get some heavy duty casters and mount them on the back like so many others have done - seems like the best way to go. We are considering the idea of designing a rack system to mount to the back of the lab that works with a special fork. We would cut the foot off of an industrial hand truck and attach this slightly longer reinforced fork in its place. (I'm thinking about 230lbs, and stairs.)
Thanks again...
Attachments
pics, finally:
Finally built them all. Our custom heat sink is not ready, but they can run without them. Also need to do a little touch-up paint in the mouth area, but the speaker coating that was recommended on the lab forums is awesome! Took this photo in a well-lit hangar, so it wasn't much to isolate them and splice two shots together to show how we configured the handles and such.
I really wanted to anodize the metal plates black, because anodized aluminum will transfer heat better than aluminum coated in black paint. I'll just keep my eyes out for anybody that can black anodize 8, 16"x 3/16" thick round plates, but I think they are so large that it will take a professional (expensive) amount of voltage to make it work...
I've got a QSC powerlight to run the LABs on, and the midtop and amp setup that my buddy is already using, plus a DSP DR-260 to manage the crossover and delay.
If I can figure all the wiring stuff out tonight, we'll light them up for the first time tomorrow - can't wait!
Finally built them all. Our custom heat sink is not ready, but they can run without them. Also need to do a little touch-up paint in the mouth area, but the speaker coating that was recommended on the lab forums is awesome! Took this photo in a well-lit hangar, so it wasn't much to isolate them and splice two shots together to show how we configured the handles and such.
I really wanted to anodize the metal plates black, because anodized aluminum will transfer heat better than aluminum coated in black paint. I'll just keep my eyes out for anybody that can black anodize 8, 16"x 3/16" thick round plates, but I think they are so large that it will take a professional (expensive) amount of voltage to make it work...
I've got a QSC powerlight to run the LABs on, and the midtop and amp setup that my buddy is already using, plus a DSP DR-260 to manage the crossover and delay.
If I can figure all the wiring stuff out tonight, we'll light them up for the first time tomorrow - can't wait!
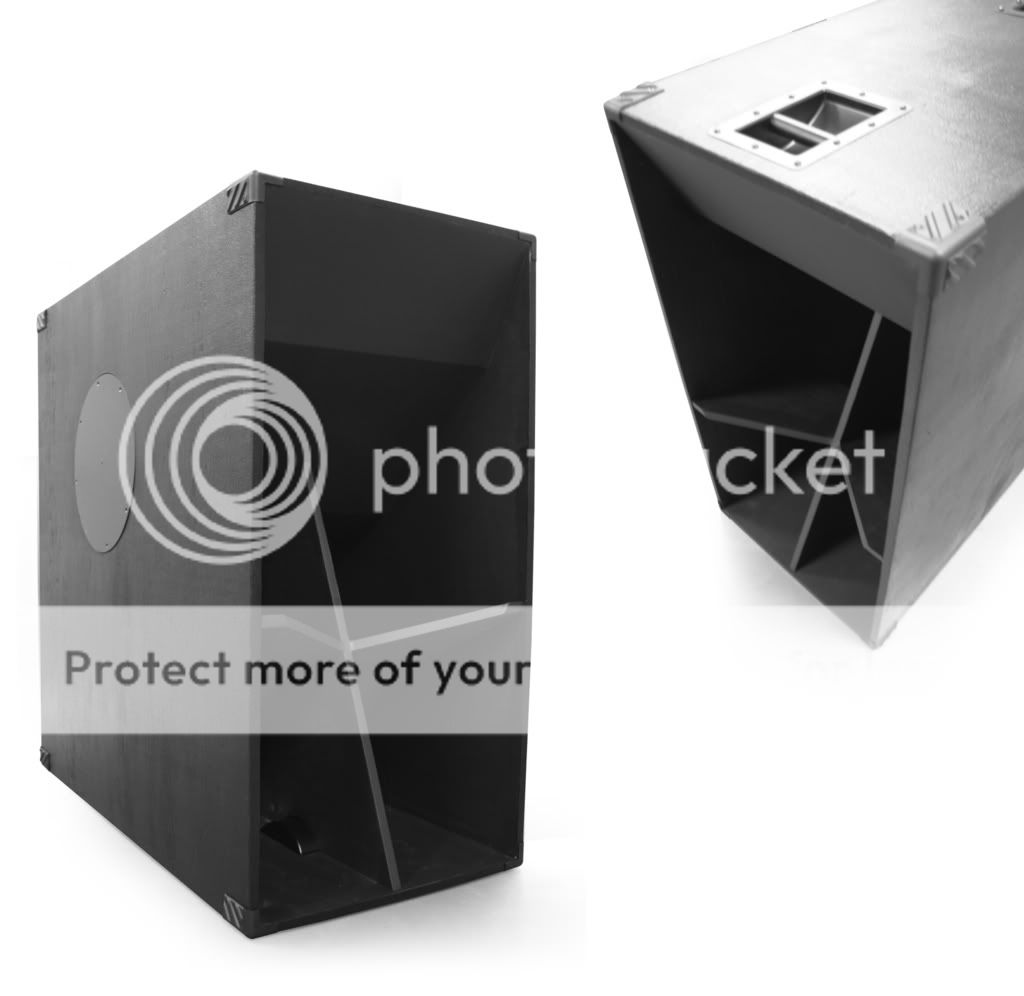
- Status
- Not open for further replies.
- Home
- Loudspeakers
- Subwoofers
- LABhorn build: wiring/hardware questions