Good point, good point. The subjectivity of science in my own research lab and dealing with certain difficult personalities has gotten the best of me, I guess.
Based on your recent track record, that ignore list doesn't seem to mean what the standard definition of ignore list is.Thank you for defending me against DPH's post that I had not read, as he is in my ignore list.
I don't know about that because you've voiced your opinion on fairly regular bases even after saying "Goodbye".I go back to silence in this thread,
Ah, silencing those whom you disagree with. You sure can do that if you run your own forum. I've heard that it's not hard to start one these days.if i was a moderator, i would have immediately erased.

So true.I'm sure this is true, but sadly shows the state audio electronics design business. There's room for everybody, anybody can claim anything, including those that would not qualify as "designers" in any other electronics industry branches, due to the lack of EE101 knowledge.
Not a problem really.
It is easy to see here, who those are.
Then it comes handy to quickly see what is laughable or worth attention.
Let's have fun and pick pieces of knowledge from those who know what they are talking about.
What's the copper output ?...do you mean on the output sub pcbs ?.And yes Daniel I meant soldering directly to the copper output....probably best to scrape the gold plating at the soldering point?
If so, then do it like the pic, no scraping tracks etc, just cut the wires and solder them to the existing pcb pads at the points shown......you will need to remove the pcb temporarily to get enough heat into the board/joints during soldering.
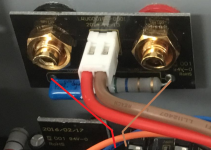
The above will give you a slightly different sound.
IMO better is to lose the pcb and solder connect everything directly to the binding posts as per Pavel's photo using new R and C as I described in another post.
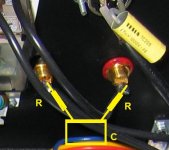
Bob, I suspect you are overthinking things, this should not be complicated.
Dan.
Last edited:
So true, but, happily, the sales figures and the cold objectivity of LTSPICE and measurements are there.I'm sure this is true, but sadly shows the state audio electronics design business. There's room for everybody, anybody can claim anything, including those that would not qualify as "designers" in any other electronics industry branches, due to the lack of EE101 knowledge.
More than this, I am not sure a (what is EE101 ?) engineer in any other electronics industry branches should be the best in audio. Are all EE101 graduated as arrogant than you ?
Just saying.
BTW: My ignore list has only 11 nicks. You included. Interesting, they are almost all Americans (speaking of arrogance ?) referring to an American degree as the only valid reference. Just try to think more deeply to that.
(No offence intended against americains, so many friends in this country, and even part of my very close family (with an us passport). But, btw, what is the name of your actual president ?).
YouTube
Sorry, but, for sure, this other example of aggressive behavior deserved an answer. EOT for me, for good this time.
Last edited:
BTW: My ignore list has only 11 nicks. You included. Interesting, they are almost all Americans (speaking of arrogance ?)
I stopped keeping a list but two of the three left are French, they both insulted my family for which there is no forgiveness (in fact I wish the screen could become a wormhole at times).
So true, but, happily, the sales figures and the cold objectivity of LTSPICE are there.
More than this, I am not sure a (what is EE101 ?) engineer in any other electronics industry branches should be the best in audio. Are all EE101 graduated as arrogant than you ?
Just saying.
BTW: My ignore list has only 11 nicks. You included. Interesting, they are almost all Americans (speaking of arrogance ?) referring to an American degree as the only valid reference. Just try to think more deeply to that.
(No offence intended against americains, so many friends in this country, and even part of my very close family (with an us passport). But, btw, what is the name of your actual president ?).
YouTube
Sorry, but, for sure, this other example of aggressive behavior deserved an answer. EOT for me, for good this time.
Wow, that didn't last long. 😱I go back to silence in this thread
EE101.
It means "introductory something". The allusion is to a college course with the course code 101, which in the American system and probably others indicates an introductory course, often with no prerequisites.
It means "introductory something". The allusion is to a college course with the course code 101, which in the American system and probably others indicates an introductory course, often with no prerequisites.
It’s cool Dan, I believe I’ve beaten it to death and have enough info to move forward on this part!
So true, but, happily, the sales figures
And yet another Audio Industry unique feature: equating sales figures with performance/quality/competency. The Wavac amplifier is there for anybody to look at (since purchasing is out of discussion, I would think 😛)
A gold plating protects until it is removed. Removing too much of the gold may leave a bare spot that would be subject to corrosion in future.
John, that reminds me, you can get gold-plated PCBs from China fairly inexpensively these days. What are your thoughts on using them for audio? Metallurgy is not one of my stronger points.
BTW: My ignore list has only 11 nicks. You included.
Are you inferring I should care about the size and content of your ignore list? Flashnews, I couldn't care less 😀.
John, that reminds me, you can get gold-plated PCBs from China fairly inexpensively these days. What are your thoughts on using them for audio? Metallurgy is not one of my stronger points.
If you ask me, the cheap ENIG is a cosmetic thing with zero impact (or even negative, see below) on the PCB performance.
- The gold on the soldering pads vanishes at the first contact with the hot lead-tin alloy. Therefore, no improved electrical contacts.
- Corrosion protection is a non issue, the solder mask takes good care of that anyway.
- The frequency response of ENIG PCBs is degraded significantly over bare or tinned copper; true, this is at frequencies well over what audio is usually concerned. Explanation is that there's always a thin layer of Nickel between the copper and the gold (Electroless Nickel Immersion Gold) for the sake of adherence; without it, the very few atoms thick layer of gold will flake away immediately. Nickel is a rather resistive material, that does not make an eutectic with the SnPb alloy. As such, the current is confined in the very thin gold layer, that the bulk copper cannot short efficiently, due to the nickel resistive barrier. Due to the skin effect, the higher the frequencies, the higher the losses in the ENIG PCB traces, these losses can reach a few dBs at UHF and low microwave. Bare or tinned copper does not have this issue, also hard gold (very expensive) is ideal. The combination of hard gold and no solder mask is ideal, but definitely cannot be justified for audio applications.
The only advantage of ENIG that I can think of is board planarity, HASL always leads to a relief on the soldering pads. That would matter for BGA ICs assembly, not exactly the audio realm either. So stay away from ENIG PCBs, it's eye candy only, not worth the extra cost.
Last edited:
Huh, we had a couple boards made up for work of ENIG, albeit someone decent and I was happy with them. Can't remember the vendor, but probably didn't skimp with the gold over Ni, even if it wasn't up to a hard gold standard. There was a desire for the corrosion resistance in that case.
For me, cheap HASL works just fine.
For me, cheap HASL works just fine.
I exhibited a headphone amp yesterday at the Burning Amp Festival in San Francisco, using 1971 era semiconductors. Specifically the LH0033, which was/is a Linear Hybrid device. Today we'd probably call it a multi chip module. It's a ceramic substrate upon which discrete JFETs, BJTs, and resistors are die-attached and wire-bonded to a metallization pattern. Exactly like a 1 layer SMD printed circuit board, except (a) bare die instead of packaged parts; (b) wire bonded instead of reflow oven soldered, and (c) ceramic substrate instead of FR4.
OMG. A blast from the past.
We used them in our equipment to test the inner enclosure of nuclear reactors
with ultrasonics. What a pile of s++t they were! Noisy, and completely different
behaviour for rising and falling edges! Maybe they can work for audio, but as soon
as Comlinear rolled out their first CFB amplifiers, the LH* were history within weeks.
What a progress! And cost did not matter in this field at the time. "When you need
to contaminate a PDP11, it does not matter if we can resume normal operation
a day earlier." Or "You think you could use a 2nd TEK 7K sampling unit, then
order one!"
But then, they celebrate here on diyAudio the magic of Ge transistors. Exotic and
out of production always helps building myths.
I think I still could help out with some LH*
regards, Gerhard
If you ask me, the cheap ENIG is a cosmetic thing with zero impact (or even negative, see below) on the PCB performance.
- The gold on the soldering pads vanishes at the first contact with the hot lead-tin alloy. Therefore, no improved electrical contacts.
- Corrosion protection is a non issue, the solder mask takes good care of that anyway.
- The frequency response of ENIG PCBs is degraded significantly over bare or tinned copper; true, this is at frequencies well over what audio is usually concerned. Explanation is that there's always a thin layer of Nickel between the copper and the gold (Electroless Nickel Immersion Gold) for the sake of adherence; without it, the very few atoms thick layer of gold will flake away immediately. Nickel is a rather resistive material, that does not make an eutectic with the SnPb alloy. As such, the current is confined in the very thin gold layer, that the bulk copper cannot short efficiently, due to the nickel resistive barrier. Due to the skin effect, the higher the frequencies, the higher the losses in the ENIG PCB traces, these losses can reach a few dBs at UHF and low microwave. Bare or tinned copper does not have this issue, also hard gold (very expensive) is ideal. The combination of hard gold and no solder mask is ideal, but definitely cannot be justified for audio applications.
The only advantage of ENIG that I can think of is board planarity, HASL always leads to a relief on the soldering pads. That would matter for BGA ICs assembly, not exactly the audio realm either. So stay away from ENIG PCBs, it's eye candy only, not worth the extra cost.
No, no, Enig is a good thing. Without the nickel barrier, the few gold atoms would diffuse
into the copper in no time, leaving a corroding Cu surface within a few days.
Yes, the magnetic Ni hurts the board behaviour for microwaves quite badly.
There is next to no gold in ENIG boards. Just an atom layer or two as a protection
against oxygen and that it looks good. If there was a lot of gold, it would have to be
removed b4 soldering or it would make the tin brittle. For our space-bound boards,
we have to remove the gold first from the wires of diodes, transistors and ICs in
a small tin bath. But then, I'm not qualified to solder that myself.
An SC-70 IC looks funny on a HASL board. Like between the craters on the moon.
I usually take solder wick to rectify that on the lab scale. Works quite good, but
not for production.
Last edited:
Huh, we had a couple boards made up for work of ENIG, albeit someone decent and I was happy with them. Can't remember the vendor, but probably didn't skimp with the gold over Ni, even if it wasn't up to a hard gold standard. There was a desire for the corrosion resistance in that case.
For me, cheap HASL works just fine.
1oz. copper board has 35um thick copper. Typical ENIG is 2 um thick, over 120um of nickel, on top of the copper. Corrosion - ENIG helps protecting the pads before soldering the parts, after soldering there is no ENIG left.
I wasn't clear on the operations of our PCB, as we were using it as inexpensive electrochemical electrode arrays, and I only needed to solder jumper wires off the edge, where the solder stuck nicely to the nickel layer. (I went and looked at the order from Advanced Circuits)
We did ask to sit in the bath for extra gold, but that probably brought us out to 500 nm rather than the usual 50-150nm. Ni is on the order of 3-6 um if one follows IPC rules. Given we didn't see major electrochemical attack, the Au coating must have achieved full coverage. I really wanted a conformal Pd layer, but that wasn't in the cards.
I probably should go back and edit my prior post because of mis-remembering exactly what was done, but hopefully these corrections get us there.
We did ask to sit in the bath for extra gold, but that probably brought us out to 500 nm rather than the usual 50-150nm. Ni is on the order of 3-6 um if one follows IPC rules. Given we didn't see major electrochemical attack, the Au coating must have achieved full coverage. I really wanted a conformal Pd layer, but that wasn't in the cards.
I probably should go back and edit my prior post because of mis-remembering exactly what was done, but hopefully these corrections get us there.
Last edited:
So ENEPIG Printed Circuit Boards are actually Nickel plated boards with a flash of Gold and/or Palladium to stop corrosion of the nickel layer whose purpose is to protect the copper pads during storage before soldering processing....and to look nice.We did ask to sit in the bath for extra gold, but that probably brought us out to 500 nm rather than the usual 50-150nm. Ni is on the order of 3-6 um if one follows IPC rules. Given we didn't see major electrochemical attack, the Au coating must have achieved full coverage. I really wanted a conformal Pd layer, but that wasn't in the cards.
Avid digital audio consoles that I have serviced run what looks like silver plated boards and are unusual sounding and unusually good sounding imo/ime.
I didn't check pricing but 6oz Heavy Copper Circuit Boards are good for welders and solar inverters, should be good for audio too !.
These epic Extreme Copper Printed Circuit Boards are the next level.
IME/IMO pcb platings have effect on sound of audio gear and Au/Ni looks nice but has signature not to my liking, silver plating causes clear good sound without empasis, tin plated pcb has another sound, perhaps slightly dull/damped (70's/80's US gear).
I reckon plain copper board with tin/copper solder works really well and this reduction of layers of metallic connections works out to be sonically preferrable imo, with clear conformal coating as long term protection.
Dan.
Last edited:
- Status
- Not open for further replies.
- Home
- Member Areas
- The Lounge
- John Curl's Blowtorch preamplifier part III