buy their whole stock?
My bad, I typed the number from memory, skipped one digit.
Schwingungsdämpfer - Bauelemente / Bauteile - Mechanische Bauelemente - Montagematerial - Pollin Electronic
(My common routine, yes. In this case, 4-5 years ago, they had more than I'd ever have use for)
Jacco,
Though I don't read German I could understand enough wording and read the measurements to see its size and that it is recommended for motor isolation and other isolation applications. What do you use these for, mounting a circuit board above a chassis or mounting a transformer?
Though I don't read German I could understand enough wording and read the measurements to see its size and that it is recommended for motor isolation and other isolation applications. What do you use these for, mounting a circuit board above a chassis or mounting a transformer?
I've been building with subchassis for a long time, and I modify if so desired, e.g. by drilling holes in the rubber.
The red ones I've used as two-side supports for the heatsinks of the ExtremA power amps I built. (the internal heatsink in each amp weighs ~14lb, fans included)
The second image is of a stand-off to dampen e.g. relays, 9/8'' total length, M3 thread, regular cost ~$7.50 each, ex tax.
Difficult to obtain new nowadays, also sell NOS sometimes for a few quarters each.
Just examples I pinched from something I posted a few years ago.
http://www.diyaudio.com/forums/soli...plifier-i-have-ever-heard-39.html#post2935337
The red ones I've used as two-side supports for the heatsinks of the ExtremA power amps I built. (the internal heatsink in each amp weighs ~14lb, fans included)
The second image is of a stand-off to dampen e.g. relays, 9/8'' total length, M3 thread, regular cost ~$7.50 each, ex tax.
Difficult to obtain new nowadays, also sell NOS sometimes for a few quarters each.
Just examples I pinched from something I posted a few years ago.
http://www.diyaudio.com/forums/soli...plifier-i-have-ever-heard-39.html#post2935337
MLCC capacitors can sing in SMPSs, usually when they go into burst mode and hit the resonant frequency of the cap, this it seems can be a problem in notebook and laptop supplies, Murata have a note on it that has been published on DIYAudio before:
Found it:
http://murata.ttieurope.com/MLCC for acoustic noise rev1.pdf
Found it:
http://murata.ttieurope.com/MLCC for acoustic noise rev1.pdf
Is this why I see a lot of silicone goop poured on everything like syrup when I look in computer PSUs?
Generally silicone is used to hold down the larger components and provide some protection against differential vibration between the component and the PCB, usually spotted on large (and SMD) electrolytic's (these are the components you tip out of your enclosure after vibration or shock testing, large body small legs).
I would like to say that they design the PSU so you don't get this problem, but they don't! basic PC power supplies are designed to a very stringent cost, so will use the lower class MLCCs (X5R..) and cheaper components...
I would like to say that they design the PSU so you don't get this problem, but they don't! basic PC power supplies are designed to a very stringent cost, so will use the lower class MLCCs (X5R..) and cheaper components...
It's typically not silicone but some thermoset or epoxy material afaik
I've seen both, but clear silicone seems to be prevalent. I'd worry about outgassing acetic acid however, that's not very nice to electronics, but don't know if it comes out of silicones.
jn
(knew I spelled acetic wrong...)
Last edited:
It's typically not silicone but some thermoset or epoxy material afaik
mainly silicone I have seen in production departments, sets quickly and is easily administered.
Better than the "corrosive brown goo..."
Anyone know what it was? It was used in equipment from the 80s to the 90s. It started out white, but heat gradually darkened and hardened it. And as it darkened, it turned conductive and corrosive and could eat right through component leads.
Anyone know what it was? It was used in equipment from the 80s to the 90s. It started out white, but heat gradually darkened and hardened it. And as it darkened, it turned conductive and corrosive and could eat right through component leads.
Don,
That was more than likely an epoxy resin that was changing color due to just the heat of the components. One of the other resins commonly used would have been urethane but that would be highly unlikely to be white when first applied, more commonly a sickly brown or green is what that would look like. The white color is commonly just titanium dioxide added for color.
That was more than likely an epoxy resin that was changing color due to just the heat of the components. One of the other resins commonly used would have been urethane but that would be highly unlikely to be white when first applied, more commonly a sickly brown or green is what that would look like. The white color is commonly just titanium dioxide added for color.
What does it imply if your amplifier circuit
is dead quiet with the input shorted, but
hums louder and louder as the input Z increases ?
is dead quiet with the input shorted, but
hums louder and louder as the input Z increases ?
It could be a bad CCS in the input stage, excessive ripple, mains wiring close to the input?
It is (was) standard yellow contact glue.Better than the "corrosive brown goo..."
Anyone know what it was? It was used in equipment from the 80s to the 90s. It started out white, but heat gradually darkened and hardened it. And as it darkened, it turned conductive and corrosive and could eat right through component leads.
With time and temperature (and maybe out-gassing from phenolic pcb's ?), it turns brown, and brittle, and conductive, and sometimes quite highly conductive.
Somewhere in that decomposition process it also becomes corrosive, or maybe exudes corrosive substances ?.
This 'time bomb' property has been known for a very long time, however it is still used in modern consumer equipment.
The much preferred alternative is neutral cure silicones the likes of Dow Corning 738.
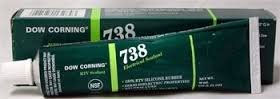
Dan.
Last edited:
I have considered the same question.....most likely ignorance and/or stupidity.Is this how they implement the automatic warranty-expiry timer?
IMO, engineers and production managers should do weeks/months in a consumer electronics service department......there is much to be learned that is not in any text books that I know of.
Dan.
You do not go far enough. Engineers should spend 3 or 4 years in the production department, learning how to actually build what they design, and learning how to explain to the production workers how to build their product.I have considered the same question.....most likely ignorance and/or stupidity.
IMO, engineers and production managers should do weeks/months in a consumer electronics service department......there is much to be learned that is not in any text books that I know of.
Dan.
When I detail how I want something built, my best techs typically say "would you please demonstrate it for us". While sometimes a PITA, it is always good for keeping me based in reality.
jn
With so much out-sourcing theses days the production dept. is likely on the other side of the world!
Not only engineers, but a lot of PCB designers I meet would benefit from some hands on production experience. I have been lucky, most of the firms I worked with for the first 26 years of doing PCBs had production departments that I worked closely with or ran in some cases, practical experience that cannot be gleamed from a book.
In these days of remote assembly house, most designs using SMD components and IPC-7351 footprints this is not as important as production engineers can sort most things, and as long as designers follow the IPC-7351 footprints and a few basic rules there is generally not many problems...
Not only engineers, but a lot of PCB designers I meet would benefit from some hands on production experience. I have been lucky, most of the firms I worked with for the first 26 years of doing PCBs had production departments that I worked closely with or ran in some cases, practical experience that cannot be gleamed from a book.
In these days of remote assembly house, most designs using SMD components and IPC-7351 footprints this is not as important as production engineers can sort most things, and as long as designers follow the IPC-7351 footprints and a few basic rules there is generally not many problems...
With so much out-sourcing theses days the production dept. is likely on the other side of the world!
Not only engineers, but a lot of PCB designers I meet would benefit from some hands on production experience.
As the other countries raise their standard of living, it becomes less and less an outsourcing world.
Companies I've worked for have outsourced production to Mexico, Taiwan, China...they use one area until the labor costs go above some threshold, them they move to another country.
It's getting to the point where I begin to suspect that the makerspace model may be one of the best ways for our young to learn how to make things.
jn
- Status
- Not open for further replies.
- Home
- Member Areas
- The Lounge
- John Curl's Blowtorch preamplifier part II