Keeps being interesting - next day, back were the pops and gurgles, to a fair degree - another round of conditioning is required, will be interesting how far this can go ...Richard, since your thing is modulation noise, you'll find this quite interesting: this supposedly pretty spiffy Dell laptop I just started using recently was giving out quite grotty sound, and I mentioned that the tiny speakers were the cause - but with a unmentioned suspicion that it could also be the DAC. So, I was trashing the the speakers with a frequency sweep from 80 to 200Hz, non-stop for hours ... hmmm getting better, but still somewhat mucky - huge amount of gurgle, pops, spinning the tuning knob of a radio type crap ... okaaaay, this is sounding more and more like digital twittering ...
But, the fascinating bit of "newness" is that the speakers now will "do" well below 80Hz, yesterday there was zero sound below that frequency, now they start responding at about 30Hz on - bizarrely, even though nearly all is higher harmonics, the sound is subjectively cleaner at below than above 100Hz, at the moment - go figure!
What I'm playing with is this; https://www.youtube.com/watch?v=MMu6nPeIDOY - nice, slow frequency sweep - a real funny is that these dinky laptop speakers do better at this test than the crappy "Altec Lansing" PC speakers here, that I don't use ...
Hmmm ... I hadn't appreciated until now that this beast was quite pricey at the time - and got a pretty good rap - Dell XPS M1710 Review (pics, specs)
So, looks like it will be worth pushing this fella a bit - at the moment running a YouTube organ recital - and key elements are much better than normally heard, very nice depth to the sound ...
So, looks like it will be worth pushing this fella a bit - at the moment running a YouTube organ recital - and key elements are much better than normally heard, very nice depth to the sound ...
i(Re) is linearized, with higher Rs or current drive. This applies especially for resonance area.
😎🙂
THx-RNMarsh
John,
Just as you have spent a lifetime understanding the small details that give you the sound qualities you desire I have done the same with speaker drivers. Things that go unexplored like the sound of a Kapton vs paper or aluminum former and what happens when you damp that Kapton with another secondary layer of material. The differences between foam surrounds and rubber surrounds and the PU surrounds that I prefer are all small details that really do change the signature of the device. As was said earlier the cone shape also changes everything, and while I understand the thinking to make a cone as stiff as possible I have found that this is not always a good thing as any resonances that do occur can be very high Q in nature and very audible. I have found there is a very fine line with making the cone overly stiff vs some cone flexing and much lower Q of those cone breakup modes. There is much to the finer details that can make a speaker sound the way it does, everything including the shape of the frame behind the cone does affect the sound quality. One area that is highly overlooked is the adhesives used at each and every joint in the cone assembly, some are excellent adhesives with terrible acoustical properties but in most speaker assembly plants speed seems to take precedence over sound quality issues. Of course you have to look at vented pole piece and the shape of those vents and venting behind the voicecoil itself. I guess if it was easy we would have much better sounding devices by now, but alas that is not the case.
Just as you have spent a lifetime understanding the small details that give you the sound qualities you desire I have done the same with speaker drivers. Things that go unexplored like the sound of a Kapton vs paper or aluminum former and what happens when you damp that Kapton with another secondary layer of material. The differences between foam surrounds and rubber surrounds and the PU surrounds that I prefer are all small details that really do change the signature of the device. As was said earlier the cone shape also changes everything, and while I understand the thinking to make a cone as stiff as possible I have found that this is not always a good thing as any resonances that do occur can be very high Q in nature and very audible. I have found there is a very fine line with making the cone overly stiff vs some cone flexing and much lower Q of those cone breakup modes. There is much to the finer details that can make a speaker sound the way it does, everything including the shape of the frame behind the cone does affect the sound quality. One area that is highly overlooked is the adhesives used at each and every joint in the cone assembly, some are excellent adhesives with terrible acoustical properties but in most speaker assembly plants speed seems to take precedence over sound quality issues. Of course you have to look at vented pole piece and the shape of those vents and venting behind the voicecoil itself. I guess if it was easy we would have much better sounding devices by now, but alas that is not the case.
PMA,
What would be interesting is testing of two speakers of identical construction except for the differences in impedance of the voicecoil. Say a 4 ohm version vs a 16 ohm version where the voicecoil masses would be matched in weight so an apples to apples comparison could be made. Of course I realize that the current carrying abilities would ultimately be different at high SPL levels. With matched levels at lower output what would we see in the distortion profiles that would change?
What would be interesting is testing of two speakers of identical construction except for the differences in impedance of the voicecoil. Say a 4 ohm version vs a 16 ohm version where the voicecoil masses would be matched in weight so an apples to apples comparison could be made. Of course I realize that the current carrying abilities would ultimately be different at high SPL levels. With matched levels at lower output what would we see in the distortion profiles that would change?
Kindhorman, one thing that has piqued my curiosity, at times, is the impact of the lead wires, from the terminals to the voice coil - any research on whether altering aspects of how that is done makes any difference?
Thanks for that, Richard. It looks to be consistent with Pavel's data also.
Still, it looks to me like the motional feedback is positive.
😎
The lowered thd is much more substantial.
Positive FB: The measured drop in thd was with a moderate gnfb circuit. With a really high gnfb circuit (such as opamp front end) with 100-120dB low freq OL gain, 20dB pos fb would not affect the over-all thd in any significant way. Just reduce the OLG by 20dB. The full 20dB is applied to reducing the distortion... so maybe 1/10 thd. I dont recall how much I used in the prototype but was being very conservative.
The phase shift as you near the speaker low-freq resonance is changing towards neg fb...... max'ed at Fr. The total change is 180 degree shift..... so what then appears with just a series R actually changes to nfb with a resonant speaker. There is no significant series power loss this way, either. The drop in thd isnt just at the resonance freq -- like you get with a tuned/reflex port -- but the whole bass range.... right where the greatest thd occure. To get such lowered thd from just the driver alone would be very costly -- larger magnets, improved motor structure, etc etc.
I might specualte that if the Q is low, the decrease in thd will begin well before resonance, as the phase starts to shift earlier.
I have always like the minimalist or fundamentalist approach to improvements. It's just one resistor for a really nice effective and efficient reduction in distortion. Can I get an Amen. Or a Hallelujah, brother !
🙂
Try it. You'll like it. Make it work better...... there are ways.
THx-RNMarsh
Last edited:
You can always get the Amen or Hallelujah from me, Richard. But I can't
help suspecting that there is more to this than meets the eye.
😎
help suspecting that there is more to this than meets the eye.
😎
You can always get the Amen or Hallelujah from me, Richard. But I can't
help suspecting that there is more to this than meets the eye.
😎
🙂
John,
Just as you have spent a lifetime understanding the small details that give you the sound qualities you desire I have done the same with speaker drivers. Things that go unexplored like the sound of a Kapton vs paper or aluminum former and what happens when you damp that Kapton with another secondary layer of material. The differences between foam surrounds and rubber surrounds and the PU surrounds that I prefer are all small details that really do change the signature of the device. As was said earlier the cone shape also changes everything, and while I understand the thinking to make a cone as stiff as possible I have found that this is not always a good thing as any resonances that do occur can be very high Q in nature and very audible. I have found there is a very fine line with making the cone overly stiff vs some cone flexing and much lower Q of those cone breakup modes. There is much to the finer details that can make a speaker sound the way it does, everything including the shape of the frame behind the cone does affect the sound quality. One area that is highly overlooked is the adhesives used at each and every joint in the cone assembly, some are excellent adhesives with terrible acoustical properties but in most speaker assembly plants speed seems to take precedence over sound quality issues. Of course you have to look at vented pole piece and the shape of those vents and venting behind the voicecoil itself. I guess if it was easy we would have much better sounding devices by now, but alas that is not the case.
True and very vise, the membrane Q must be very low while the membrane must be very stiff for the stiff cone can work, this is why our membranes are multi layered with very very hard and compared to the skin layers very soft materials, everything else but the flexing cone works in my book too. flexing and material absorption is a very unliniar process that in general makes the driver sound dull unresolved and nervous. Now this is based on the membranes types that are industrial standards and can be bought from the common industrial vendors and not knowing what you work with.
The lowered thd is much more substantial.
.....
I have always like the minimalist or fundamentalist approach to improvements. It's just one resistor for a really nice effective and efficient reduction in distortion.
..
Try it. You'll like it. Make it work better...... there are ways.
THx-RNMarsh
Richard,
I tried it and it works, in the bass area. The simple V/I amplifier based on old improved Sinclair Z30 (long live old sir Clive), as per attached drawing. Shown as as well distortions with voltage and current drive. It is not only limited to resonance peak, but it works in the area of frequencies below some 100Hz.
Regards,
Pavel
Attachments
Last edited:
There is a real improvement with current drive that reflects in decreased distortion. No question. Of course we need to equalize frequency response then.
Attachments
Last edited:
I'm sitting here a few feet from the equipment, so I took my desktop Jordan
J92's (nice speakers by the way) in sealed boxes and hooked one up driven
by a voltage source at 1 watt (2.8V) at 50 Hz and snapped the distortion
waveform (about 3%) and its FFT.
Then I put 32 ohms in series with the speaker and set it at the same acoustic
level, and measured it again. I think from the accompanying photos you
will see there is some alteration, but not improvement in the THD.
😎
What are audible differences?
Photoshop overlays of your FFT results:
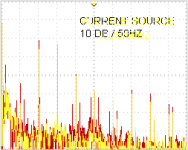
Condition with resistor clearly adds more distortion products.
Discontinuity at zero crossing is also more pronounced:
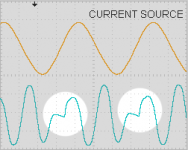
Andrew
Last edited:
Putting speaker in feedback loop does appear advantageous. What is envelope for 100Hz burst test, and peak voltage?
Seeing how it appears that adding the speaker to the feedback loop works and I imagine it would work for either a VFA or CFA type amplifier circuit is it as simple as it appears to implement as it appears or are there going to be other things that need to be done to make this a working system? Can I assume that this will work the same with a discrete amplifier design as well as an opamp based design? This looks like a worthwhile thing to do in something like the integrated self powered speaker that I am working on.
MIIB,
The cone material that I use is something that I developed myself with a friend who did all the acoustical testing. It is a composite material of multiple types of fiber reinforcement with a binder resin that is not known in the loudspeaker world and has never been used by anyone else to my knowledge. It is not only the materials that I am using but also the manufacturing method that is different than anything else. I have been involved in manufacturing for a long time and this is something that very few in the world would understand or know how to do even if I told you what method of manufacturing I used, it is an esoteric method only a few of us have really perfected. Composites was only a small part of the many areas of plastics and composites I have worked with. If I could not use this material I would fall back into traditional paper cones as they have proven their capabilities in many ways and with modern additives paper is a very well understood entity. Polypropylene cones were what made me take a look in the first place and a development by DuPont working with Kevlar and polypro was the impetus to do this development work as a challenge to me personally by my friend to replace the DuPont material that was not working consistently in their development, They could not produce consistent properties from cone to cone, the variations due to their processing was out of control. I am not using polypro in my composites but it is an area that could still be pursued but I don't think it would be as good as what I am doing. It would require different manufacturing methods and I don't work in that area of materials.
In other areas of composites I can not give away my knowledge as it is so little understood but by a very few of us in the entire world at this point. Believe me I have tried but the investment in capital equipment seems to stop people cold vs the attempts being made today. I was producing production parts using this method I developed over twenty five years ago and making finished composite parts in thickness up to 10mm thickness in as fast as 90 seconds and the current methods are taking at a minimum over 5 to 6 minutes to make a comparable part! I could revolutionize the automotive composites industry if someone would take there head out of their a*s long enough to listen and understand what a few of us developed for other industries long ago. I was making parts as large as 1500mm x 2400mm when I was doing this. So think what you could do with composites parts that large that could be molded in 90 seconds! This included all types of fiber materials and even organic fiber such as hemp and other natural fibers. Perhaps in the next twenty years I will again see someone rediscover what I already know?
The cone material that I use is something that I developed myself with a friend who did all the acoustical testing. It is a composite material of multiple types of fiber reinforcement with a binder resin that is not known in the loudspeaker world and has never been used by anyone else to my knowledge. It is not only the materials that I am using but also the manufacturing method that is different than anything else. I have been involved in manufacturing for a long time and this is something that very few in the world would understand or know how to do even if I told you what method of manufacturing I used, it is an esoteric method only a few of us have really perfected. Composites was only a small part of the many areas of plastics and composites I have worked with. If I could not use this material I would fall back into traditional paper cones as they have proven their capabilities in many ways and with modern additives paper is a very well understood entity. Polypropylene cones were what made me take a look in the first place and a development by DuPont working with Kevlar and polypro was the impetus to do this development work as a challenge to me personally by my friend to replace the DuPont material that was not working consistently in their development, They could not produce consistent properties from cone to cone, the variations due to their processing was out of control. I am not using polypro in my composites but it is an area that could still be pursued but I don't think it would be as good as what I am doing. It would require different manufacturing methods and I don't work in that area of materials.
In other areas of composites I can not give away my knowledge as it is so little understood but by a very few of us in the entire world at this point. Believe me I have tried but the investment in capital equipment seems to stop people cold vs the attempts being made today. I was producing production parts using this method I developed over twenty five years ago and making finished composite parts in thickness up to 10mm thickness in as fast as 90 seconds and the current methods are taking at a minimum over 5 to 6 minutes to make a comparable part! I could revolutionize the automotive composites industry if someone would take there head out of their a*s long enough to listen and understand what a few of us developed for other industries long ago. I was making parts as large as 1500mm x 2400mm when I was doing this. So think what you could do with composites parts that large that could be molded in 90 seconds! This included all types of fiber materials and even organic fiber such as hemp and other natural fibers. Perhaps in the next twenty years I will again see someone rediscover what I already know?
- Status
- Not open for further replies.
- Home
- Member Areas
- The Lounge
- John Curl's Blowtorch preamplifier part II