There are a large number of threads on different forums discussing all of the pro's and cons, I suggest a google search using the terms synergy horn, unity horn, multiple entry horn, Danley etc.
Yeah, I'm trying.. Hard to keep up with over a decade of information. Already spend more than a week reading the midrange topic 😉
About the specific kit Chris is making: what kind of moulding technique will be used? You mentioned that you wanted to already put in the woofer holes because it would save on material. Note that this will very likely make the mould more complex, and therefore much more expensive. I don't know how many pieces you would like to make, but in the end it might be more beneficial to not pre-hole the horn.
Yeah, I'm trying.. Hard to keep up with over a decade of information. Already spend more than a week reading the midrange topic 😉
I would guess I spent about 3 months all up reading all the synergy related threads I could find some time ago so you still have a way to go yet, good luck 🙂
...About the specific kit Chris is making: what kind of moulding technique will be used? You mentioned that you wanted to already put in the woofer holes because it would save on material. Note that this will very likely make the mould more complex, and therefore much more expensive. I don't know how many pieces you would like to make, but in the end it might be more beneficial to not pre-hole the horn.
That portion of the task is far behind. Perhaps you didn't catch the post in this thread where I explained my rationale...and constraints. And the complexity of the mold is really controlled by the geometries of the woofer mounting pads. The woofer ports are really quite simple to capture once you find the right approach for the back mold construction/materials. Leaving the ports out actually leads to a more complex solution in the chosen approach.
Chris
I already have crites 15" cast woofers. What size is the throat, is it still for the same cd, the TAD 4001?
The throat size is the same as the K-402: 2" (50.8 mm). One of the best non-Be diaphragm drivers that I've heard is the Faital Pro HF20AT. The difference in sound between the TAD TD-4002s and the Faital Pros is very subtle.
That doesn't mean that more humble drivers won't also work. Even the low cost P.Audio BM-D750 series I sounds pretty good--with the only detectable differences in the top-most half octave (~14.8 kHz and above)--and you have to be listening carefully for those differences.
That doesn't mean that more humble drivers won't also work. Even the low cost P.Audio BM-D750 series I sounds pretty good--with the only detectable differences in the top-most half octave (~14.8 kHz and above)--and you have to be listening carefully for those differences.
And the complexity of the mold is really controlled by the geometries of the woofer mounting pads. The woofer ports are really quite simple to capture once you find the right approach for the back mold construction/materials. Leaving the ports out actually leads to a more complex solution in the chosen approach.
In that case, leave them in 🙂
Regarding weight: are you employing any techniques to get the weight down without sacrificing (to much) strength? If not, it might be interesting to take a look at that kind of stuff. For instance honeycombing the out of view structures of the horn. Look at for instance wat B&O does:
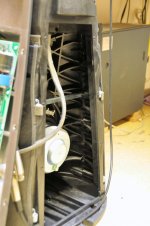
This will obviously make the mold much more complex and might increase initial cost.
Also, to keep the dimensions down you could even make the thing out of multiple identical parts. This will increase tolerances significantly and will not at all benefit your personal goal to make your horn, but will help with shipping since it will significantly decrease the volume needed.
The throat size is the same as the K-402: 2" (50.8 mm). One of the best non-Be diaphragm drivers that I've heard is the Faital Pro HF20AT. The difference in sound between the TAD TD-4002s and the Faital Pros is very subtle.
That doesn't mean that more humble drivers won't also work. Even the low cost P.Audio BM-D750 series I sounds pretty good--with the only detectable differences in the top-most half octave (~14.8 kHz and above)--and you have to be listening carefully for those differences.
What about the Radian 2" CD's?
Another interesting question: do you have any idea of the timeframe when there will be an actual kit? I know these things take time, but it would still be interesting to get a sense of timing.
I haven't heard a Radian (JBL) on the MEH horn or on a K-402. Perhaps Bob Crites can relate his experiences. I know a couple of guys using older JBL 2" drivers (2445-2446) that are very pleased with their performance. djk recommends JBL 2431(Al) or 2435(Be). But Bob has a lot of experience with Radian.
Timeframe: Now you're asking me to start lying...I've noticed that everything is taking 4x longer than it seems that it should. Lots of distractions (friend's tragedies, very ill old friends, too hot/humid weather, West Nile warnings from the city restricting working hours in the garage, successive A/C freeze-ups, etc. You name it--we've had it. It's like the 7 plagues.
Now that I've complained about the human condition in general...if things went as planned: a couple of months to have the horn fabrication under control and perhaps building boxes (flat or assembled--for those that would want one). The box is really simple--with slanted sides toward the rear. Veneered wood would look very nice, and perhaps Duratex for those with that bent.
Perhaps more two weeks to a month to fabricate and assemble five units for my listening space, and then figure out how to box/ship to a few US guys that have been "chomping at the bit" (...a local vernacular...they'd come after me with weapons if I didn't say that I'd service them first.)
Another month to work through the export issues (i.e., learning how to do it at least cost and greatest reliability, and learning the laws by country).
Perhaps November/December? I wouldn't guess sooner, but hope springs eternal...
Okay, there's your lies.
Right now I'm all in on doing the single-piece horn. When you have one in your hands playing music at 100+ dB with woofers and compression drivers in its box, perhaps you'll understand my rationale. The idea of multiple piece horns are definitely "down the road a bit", but it's an interesting challenge to think about, nevertheless.
I've been working on ideas for a totally new horn subwoofer design that would serve as a base to raise the MEHs. It's pretty cool--and nothing like you've ever seen before, but there are technical manufacturing challenges to work through.
Chris
Timeframe: Now you're asking me to start lying...I've noticed that everything is taking 4x longer than it seems that it should. Lots of distractions (friend's tragedies, very ill old friends, too hot/humid weather, West Nile warnings from the city restricting working hours in the garage, successive A/C freeze-ups, etc. You name it--we've had it. It's like the 7 plagues.
Now that I've complained about the human condition in general...if things went as planned: a couple of months to have the horn fabrication under control and perhaps building boxes (flat or assembled--for those that would want one). The box is really simple--with slanted sides toward the rear. Veneered wood would look very nice, and perhaps Duratex for those with that bent.
Perhaps more two weeks to a month to fabricate and assemble five units for my listening space, and then figure out how to box/ship to a few US guys that have been "chomping at the bit" (...a local vernacular...they'd come after me with weapons if I didn't say that I'd service them first.)
Another month to work through the export issues (i.e., learning how to do it at least cost and greatest reliability, and learning the laws by country).
Perhaps November/December? I wouldn't guess sooner, but hope springs eternal...

Okay, there's your lies.
Right now I'm all in on doing the single-piece horn. When you have one in your hands playing music at 100+ dB with woofers and compression drivers in its box, perhaps you'll understand my rationale. The idea of multiple piece horns are definitely "down the road a bit", but it's an interesting challenge to think about, nevertheless.
I've been working on ideas for a totally new horn subwoofer design that would serve as a base to raise the MEHs. It's pretty cool--and nothing like you've ever seen before, but there are technical manufacturing challenges to work through.
Chris
Okay, there's your lies.
Thanks for that 🙂 . These things always take up more time than expected and it seems to me that the timeframe is indeed fairly optimistic. The winter time frame would suit me just fine though, since I don't have any time to start any project right now anyway. Anyway: good luck with those plagues 😱
So what exactly will the kit entail? We know about the horn, but now you also talk about boxes (which earlier you said could be fabricated locally)? That will definitely add time to the project. If you would like to do that as well I would recommend doing so as a second step. Might even be a good idea to first validate the potential of such an undertaking before putting in time, effort and money.
I've been working on ideas for a totally new horn subwoofer design that would serve as a base to raise the MEHs. It's pretty cool--and nothing like you've ever seen before, but there are technical manufacturing challenges to work through.
Sure, divide you time up even more.. that will help the timeline 🙄
By chance...have you ever worked as a scheduler or PM? You have a definite knack for it. 
I'll need 5 boxes for my own listening room--which I mentioned above will come first. After building those, I thought it would probably be pretty easy to build a few more.
The sub thing is merely something that I've been thinking about for some time. When I placed the MEH in the center, suddenly there was a lot more bass authority and more even coverage--nominally due to placement at a room anti-node (similar to Geddes' subwoofer placement thing). It occurred to me that placing a LF horn-loaded sub under each MEH would supplant the need for the TH-SPUDs in the front corners and distribute infrasonic bass co-located with the surround MEH channels. It's a neat idea, but fabricating it economically and getting the packaging right are the challenges.
I found that thinking about those kind of design challenges over time works a lot better than diving in with the first alternative that comes to mind--and iteratively failing successively. That's how the present K-402-based MEH came into being: thinking about the problem until it became a simple almost-trivial solution.
Chris

I'll need 5 boxes for my own listening room--which I mentioned above will come first. After building those, I thought it would probably be pretty easy to build a few more.
The sub thing is merely something that I've been thinking about for some time. When I placed the MEH in the center, suddenly there was a lot more bass authority and more even coverage--nominally due to placement at a room anti-node (similar to Geddes' subwoofer placement thing). It occurred to me that placing a LF horn-loaded sub under each MEH would supplant the need for the TH-SPUDs in the front corners and distribute infrasonic bass co-located with the surround MEH channels. It's a neat idea, but fabricating it economically and getting the packaging right are the challenges.
I found that thinking about those kind of design challenges over time works a lot better than diving in with the first alternative that comes to mind--and iteratively failing successively. That's how the present K-402-based MEH came into being: thinking about the problem until it became a simple almost-trivial solution.
Chris
time line
Any idea when these horn kits will be available? I was mulling over Jeff Bagby's Titans @ Diy Sound Group when I stumbled across this thread.
Bert
Any idea when these horn kits will be available? I was mulling over Jeff Bagby's Titans @ Diy Sound Group when I stumbled across this thread.
Bert
Are you referring to the 90 x 60 degree coverage horn, i.e., the one that looks similar to the Klipsch K-402, or are you talking about some other angular coverage horn?
I would guess I spent about 3 months all up reading all the synergy related threads I could find some time ago so you still have a way to go yet, good luck 🙂
There's kind of a funny story, about how I got into Unity horns:
During the tail end of the dotcom crash, I was working for a tech company that basically had no customers. We all knew we were doomed, but we showed up for work every day, waiting for the inevitable layoff. No exaggeration: in the span of a year, we probably did a total of 100 hours of work, or about one hour per week on average. There were entire months with zero work. About half the staff goofed off all day, the other half pretended to work. I fell into the latter group. I basically read patents for something like 10-20 hours a week for nearly a year. The rest of the day I studied LAMP stack.
IMHO, someone could pick it up a lot quicker these days. But it felt like the dark ages back then. We didn't have hornresp, horns were largely ridiculed by the hifi community. About the only way to learn about them was to dig through AES papers and patents.
I'm piping up essentially to reiterate what I said in post 30. This would be great as a flat pack or minimal parts* kit - particularly for overseas buyers.
Here is a link to a nice DIY effort, a K402 clone that makes it look easy**, and it would be easier still if the sizes and cut angles were all available on a blueprint / file + and the tricky parts could be purchased in a compact, easily mailed pack.
Klipsch K402 replica build - DIY Audio Projects - StereoNET
Klipsch K402 replica build - DIY Audio Projects - StereoNET
* which could be as little as a set of cut sheets + instructions, and a bag of custom built (3D printed?) parts, such as angle brackets to brace & hold the throat together while the glue dries.
** I've already linked this in other threads, but why not - it is a great project - particularly for an Austalian, who would have to pay six jillion dollars to bring a real set of K402 horns across the ocean.
Here is a link to a nice DIY effort, a K402 clone that makes it look easy**, and it would be easier still if the sizes and cut angles were all available on a blueprint / file + and the tricky parts could be purchased in a compact, easily mailed pack.
Klipsch K402 replica build - DIY Audio Projects - StereoNET
Klipsch K402 replica build - DIY Audio Projects - StereoNET
* which could be as little as a set of cut sheets + instructions, and a bag of custom built (3D printed?) parts, such as angle brackets to brace & hold the throat together while the glue dries.
** I've already linked this in other threads, but why not - it is a great project - particularly for an Austalian, who would have to pay six jillion dollars to bring a real set of K402 horns across the ocean.
Attachments
* which could be as little as a set of cut sheets + instructions, and a bag of custom built (3D printed?) parts, such as angle brackets to brace & hold the throat together while the glue dries.
Bill Waslo proposed something like that, basically a waveguide that can be 'scaled' to just about any size. Basically the first 15-20cm are 3D printed, and then the rest of the waveguide is a simple conical horn.
This is pretty clever, because arguably the throat is where you REALLY want precision. If you're off by a millimeter or two at the throat, it can make a real difference. But at the mouth? Or the center of the horn? It's no big deal.
Looked at getting possibly someone to 3d print the small section of my SH project also. So these threads are always good to see. Although my transition will be from a rectangle (TPL-150) and not a circle such as a CD. Still helpful when I have to still build the rest of the horn.
Looked at getting possibly someone to 3d print the small section of my SH project also. So these threads are always good to see. Although my transition will be from a rectangle (TPL-150) and not a circle such as a CD. Still helpful when I have to still build the rest of the horn.
A TPL 150 would make an absolutely beastly Unity horn. In these designs, the output of the tweeter is basically the weak link. And due to the conical walls of the horn, that means that our maximum output from 15-20khz is "just" 110dB or so.
This is because compression drivers have a falling response; they may be 109dB efficient at 2khz, but by 20khz, that's fallen to around 90dB.
The TPL 150 appears to be about 100dB efficient at 20khz, so that really ups the ante on how loud the design can get.
Bill Waslo proposed something like that, basically a waveguide that can be 'scaled' to just about any size. Basically the first 15-20cm are 3D printed, and then the rest of the waveguide is a simple conical horn.
This is pretty clever, because arguably the throat is where you REALLY want precision. If you're off by a millimeter or two at the throat, it can make a real difference. But at the mouth? Or the center of the horn? It's no big deal.
I've made the plastic pieces for that, have them sitting around (got some for PB too). Haven't put them into a full horn yet, though, my table saw is out in the cold shed. Plan to make a set of humongo Synergy horns, but not sure I really will. Don't need or have room for them, and don't know what I'd do with them after they're made...
Something like this...
I did do a test fit with an early version, but managed to cut the panel corners wrong.... Really easy to assemble, though.
http://libinst.com/SynergyDIY/Assy%20Pics.pdf
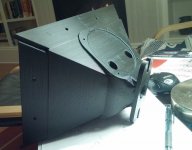
Don't expect kits (from me anyway). Patent Fear-Uncertainty-Doubt too much for this retired guy.
Last edited:
Bill, the obvious solution is that you'll just have to build them into the wall of your living room 🙂
- Home
- Loudspeakers
- Multi-Way
- Full-Range Synergy Kit Questions