Have you measured the DC voltage across the smoothing capacitor of a AC to DC PSU?That is also true. But I doubt that you have 19V-DC when 1 or 2A are drawn.
Have you looked at the ripple using a scope set to AC input?
That is also true. But I doubt that you have 19V-DC when 1 or 2A are drawn.
You will have the '19V' if the transformer is rated / specified to suit.
There are detailed design considerations - derating / conduction angle etc.
But really, if you have a '15vac' output transformer and you are only getting 15Vdc after rectification and resevoir caps then something is wrong with the design and you need to turn it off sharpish.
In fact you can get issues where the transformer output voltage rises above the stated value when there is not enough load current. eg a typical 9V wall wart transformer rated @1A will likely give 11V / 12V under light load.
Rather than doubting or guessing please go and read and/or measure something relevant.
You misunderstood me. Of course you can ensure 19V at the charging cap, if you have a transformer with 15V and not draw much power. However, the 19V are not guaranteed when pulling the rated current of the transformer. Therefore 15V regulator -> 18V transformer.
You misunderstood me. Of course you can ensure 19V at the charging cap, if you have a transformer with 15V and not draw much power. However, the 19V are not guaranteed when pulling the rated current of the transformer. Therefore 15V regulator -> 18V transformer.
If you have a '15V' transformer and draw a small current wrt the rating you will get >15V (see Transformer Regulation)
If you consider the rated current then apply design considerations as applicable to the design - derating for rectifier circuit etc etc - the you should be able to get the '19V' result at that current.
If you don't then there's a problem with the design implementation.
Please read Andrew T's post - the one a few posts ago with derating consideration detail etc.
No, you are either not listening or not understanding.You misunderstood me. Of course you can ensure 19V at the charging cap, if you have a transformer with 15V and not draw much power. However, the 19V are not guaranteed when pulling the rated current of the transformer. Therefore 15V regulator -> 18V transformer.
Do the experiment.
Build a 15Vac supply into a bridge rectifier. Attach the smoothing capacitor. Now measure the DC voltage stored on the capacitor.
Measure the ripple voltage on the capacitor.
No, you are either not listening or not understanding.
Do the experiment.
Build a 15Vac supply into a bridge rectifier. Attach the smoothing capacitor. Now measure the DC voltage stored on the capacitor.
Measure the ripple voltage on the capacitor.
And what load?
To expand your experiment, try a variety of loads and measure the average DC voltage and the ripple voltage.
Start with infinite load, 100k, 33k, 10k, 3k3 and 1k0 (if the voltage does not over heat it).
Start with infinite load, 100k, 33k, 10k, 3k3 and 1k0 (if the voltage does not over heat it).
Good advice.
To look at this another way - if , after proper design / de-rating etc, you are getting less than DC voltage under load then you need a transformer with same output voltage but larger Current / VA rating.
The answer is not to go to a transformer with a higher voltage spec'. That would mean you were simply allowing for the voltage drop in the transformer itself = inefficient and hot !
To look at this another way - if , after proper design / de-rating etc, you are getting less than DC voltage under load then you need a transformer with same output voltage but larger Current / VA rating.
The answer is not to go to a transformer with a higher voltage spec'. That would mean you were simply allowing for the voltage drop in the transformer itself = inefficient and hot !
Hi, what kind of noise?I moved my PSU (original design) out of the preamp box which resulted in a very significant reduction of the floor noise (on my oscilloscope)on the output.
input selector pcb/idc cable
Hi,I'm in the middle of building the preamp and now I have a question about the input selector pcb. I soldered it first on the wrong side of the pcb but i have corrected this. But now the cable leaves in the wrong direction if i compare it with other builds. The red mark is from gd to gd marking on the silkscreen so that seems allright. Both notched point towards the numbers on the silkscreen. It could be that the cable i bought was folded the other way around, but i'm not sure what is standard. Please have a look at the picture then you see what i mean. So the question is if it will work OK like this. Thanks for your time.
Best wishes, Vincent
Hi,I'm in the middle of building the preamp and now I have a question about the input selector pcb. I soldered it first on the wrong side of the pcb but i have corrected this. But now the cable leaves in the wrong direction if i compare it with other builds. The red mark is from gd to gd marking on the silkscreen so that seems allright. Both notched point towards the numbers on the silkscreen. It could be that the cable i bought was folded the other way around, but i'm not sure what is standard. Please have a look at the picture then you see what i mean. So the question is if it will work OK like this. Thanks for your time.
Best wishes, Vincent
Attachments
Hi,I'm in the middle of building the preamp and now I have a question about the input selector pcb...
Best wishes, Vincent
Vincent,
The easiest way to check to your cable is to use a multimeter to verify that you have plus 12 volts on the pin pair that is marked '+V' on the switch PCB silk screen. If you do you should be good. If you don't your cable is backwards. The easiest way to fix that is to nibble a slot on the long edge of the IDC connector (opposite side if the switch) that you have soldered to the switch PCB. That will allow you to reverse the ribbon cable on the switch end.
Thanks Carl, I'll check tomorrow, it's getting late on this side of the ocean. The pcb's are a real pleasure to work with b.t.w.Vincent,
The easiest way to check to your cable is to use a multimeter to verify that you have plus 12 volts on the pin pair that is marked '+V' on the switch PCB silk screen. If you do you should be good. If you don't your cable is backwards. The easiest way to fix that is to nibble a slot on the long edge of the IDC connector (opposite side if the switch) that you have soldered to the switch PCB. That will allow you to reverse the ribbon cable on the switch end.
Thanks Carl, I'll check tomorrow, it's getting late on this side of the ocean. The pcb's are a real pleasure to work with b.t.w.
Great! Be sure to let me know if you need help.
Question for Carl -
What is the pitch and row spacing of the B5K Alpha pots used on the pcb? I've tried looking up the data sheets for them but can't find anything that matches. They're too small for me to measure reliably with anything I have in my toolbox.
I'm considering panel mount pots to allow more front panel design options and would like to mount connectors on the board to keep the wiring neat. Assuming I can find something that matches the pitch and row spacing on the pcb.
Thanks!
What is the pitch and row spacing of the B5K Alpha pots used on the pcb? I've tried looking up the data sheets for them but can't find anything that matches. They're too small for me to measure reliably with anything I have in my toolbox.
I'm considering panel mount pots to allow more front panel design options and would like to mount connectors on the board to keep the wiring neat. Assuming I can find something that matches the pitch and row spacing on the pcb.
Thanks!
Question for Carl -
What is the pitch and row spacing of the B5K Alpha pots used on the pcb? I've tried looking up the data sheets for them but can't find anything that matches. They're too small for me to measure reliably with anything I have in my toolbox.
I'm considering panel mount pots to allow more front panel design options and would like to mount connectors on the board to keep the wiring neat. Assuming I can find something that matches the pitch and row spacing on the pcb.
Thanks!
The PCB pinout that I used is an industry standard for thru board pots. There are 2 rows of 3 pins.
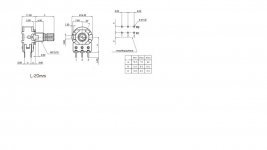
The pins in each row are spaced 5mm apart and the two rows are spaced 6mm apart.
I hope this is what you are looking for. Let me know if you need more.
The PCB pinout that I used is an industry standard for thru board pots. There are 2 rows of 3 pins.
The pins in each row are spaced 5mm apart and the two rows are spaced 6mm apart.
I hope this is what you are looking for. Let me know if you need more.
That's what I was looking for. I figured it was something basic like that - But was having trouble locating it. Thanks Carl!
KAD Adjustable Power Supply Details ...
For those of you building the kit with the supplied 'KAD Adjustable Power Supply' here is a zip file containing additional details to make your build easier.
KAD Adjustable Pwr Supply Zip file to download
For those of you building the kit with the supplied 'KAD Adjustable Power Supply' here is a zip file containing additional details to make your build easier.
KAD Adjustable Pwr Supply Zip file to download
Hi, my preamp has started to act funny time to time. It has occurred a couple of times that when I turn on the preamp one channel is really load and the other very quit (almost completely dead). The volume control does not work at all, affecting neither the load channel or the dead channel. After running around 10 minutes the pre-amp starts to work as it should again.
What can cause a symptom like this? I was thinking maybe the balance potentiometer is broken?
What can cause a symptom like this? I was thinking maybe the balance potentiometer is broken?
- Home
- Source & Line
- Analog Line Level
- Doug Self Preamp from Linear Audio #5