Nope... I tried to cut them loose just as I tried to keep them tight - it simply didn't work for me - however, my bearings have a 3mm ID - can't fit anything inside, even if I'd have thinner bolts... OTOH, I'm trying to make this work on a polished 6mm dia steel shaft - tried to get some (round/tube) glass but no luck... Interesting enough, with the SKF LBBR6 - that same shaft seems to be smooth enough...
I didn't do one thing though - I was advised to clean the bearings in an "ultrasonic bath" but didn't get that far - so far...
What bothers me - or gets me into a confused state of mind is the fact that each and every single bearing got stripped from the steel covers (so, they're no more ZZ, just blank/open 623) degreased with brake degreaser/cleaner fluid (in spray) and they spin freely as if there is absolutely no resistance - once I place the needle into the groove, the trouble begins...
Sooner or later, I'll figure out where is the problem... Maybe I'm not too smart, but I'm persistant 🙂
I didn't do one thing though - I was advised to clean the bearings in an "ultrasonic bath" but didn't get that far - so far...
What bothers me - or gets me into a confused state of mind is the fact that each and every single bearing got stripped from the steel covers (so, they're no more ZZ, just blank/open 623) degreased with brake degreaser/cleaner fluid (in spray) and they spin freely as if there is absolutely no resistance - once I place the needle into the groove, the trouble begins...
Sooner or later, I'll figure out where is the problem... Maybe I'm not too smart, but I'm persistant 🙂
About the SKF LBBR6 bearing's behavior: At first I thought that the play on the shaft is caused by the lack of enough support from the outside. I press fitted it into a bronze bearing and tried it that way - however, the amount of play between the bearing and the shaft remained present. With THK LM6LUU bearings, such play is absent. Just in case anyone decides to go that way... Sort of FYI...
I also noticed that it's also not all the same what cartridge is used. For example, the NAD9200 (old ADC - sort of) seems to be so old that the small rubber that holds the needle has gone too soft - the Grado or the Ortofon OM5 can easily cope with the recommended stylus pressure - the old cartridge seems to be too sensitive to pressure levels over 1 gram, so it's maybe time to either replace the needle or quit using it for functionality tests... I use a small digital scale that measures into 1/100 of a gram - limited to 200grams max - ideal for this job...
I also noticed that it's also not all the same what cartridge is used. For example, the NAD9200 (old ADC - sort of) seems to be so old that the small rubber that holds the needle has gone too soft - the Grado or the Ortofon OM5 can easily cope with the recommended stylus pressure - the old cartridge seems to be too sensitive to pressure levels over 1 gram, so it's maybe time to either replace the needle or quit using it for functionality tests... I use a small digital scale that measures into 1/100 of a gram - limited to 200grams max - ideal for this job...
BTW- NAD9200 is an ADC cart.About the SKF LBBR6 bearing's behavior: At first I thought that the play on the shaft is caused by the lack of enough support from the outside. I press fitted it into a bronze bearing and tried it that way - however, the amount of play between the bearing and the shaft remained present. With THK LM6LUU bearings, such play is absent. Just in case anyone decides to go that way... Sort of FYI...
I also noticed that it's also not all the same what cartridge is used. For example, the NAD9200 (old ADC - sort of) seems to be so old that the small rubber that holds the needle has gone too soft - the Grado or the Ortofon OM5 can easily cope with the recommended stylus pressure - the old cartridge seems to be too sensitive to pressure levels over 1 gram, so it's maybe time to either replace the needle or quit using it for functionality tests... I use a small digital scale that measures into 1/100 of a gram - limited to 200grams max - ideal for this job...
Hello stein2,
I have been using a couple of ADC XLM style carts on my linear arm for some time now with outstanding results. Easily as good as if not better than my OM 40 with OM10 stylus. LT arm is 4 bearing on glass tube design. My ADC carts were inherited and arrived without styli. Bought a replacement stylus on Amazon.com for a bit over $10 USD. Go to Amazon.com and search on PM2237DE for details. I've no idea if they ship to your part of the world. There are lots more vendors selling ADC needles on the web, but I would try to avoid the Pfanstiehl (sp?) needles. That PM2237DE number fits all XLM style carts. It is diamond-eliptical needle.
I would like to hear more about your lack of success with standard ball bearings rather than linear bearing designs. Once I gave up on polished steel rods and went to glass tubing my problems went away. Even 2 pieces of window glass arranged in a V proved to be way less a problem and the glass tube just sits there working. I have serious doubts about linear ball bearing designs but admit this is only gut feel for now.
Happy New Year,
BillG
Last edited:
BTW- NAD9200 is an ADC cart.
... LT arm is 4 bearing on glass tube design. <snip>... That PM2237DE number fits all XLM style carts. It is diamond-eliptical needle.
I would like to hear more about your lack of success with standard ball bearings rather than linear bearing designs. Once I gave up on polished steel rods and went to glass tubing my problems went away. Even 2 pieces of window glass arranged in a V proved to be way less a problem and the glass tube just sits there working. I have serious doubts about linear ball bearing designs but admit this is only gut feel for now.
Happy New Year,
BillG
Thanks bgruhn,
As for attempts with plain deep groove rolling bearings, I tried with metal guiding devices/rails, aluminum and SS - didn't get to the point to say I'm pleased with the results. Both either "soft" or "sticky" for the job. Didn't try with glass, though. I have a few mirror stripes from an old (Ricoh professional) photocopier, I guess the 23x188mm (5mm thick) pieces would be adequate - straight, clean and even surfaces/edges and I could align the two mirrors to form a "V" shaped rail - just have to decide first how to fix them into the desired position and a way to fix that contraption to some construction that would hold the arm... Currently in doubt, should I make a "T" shape or a "V" shaped rail. But I'll figure out...
As for the ADC XLM needle - found some quite cheap - 6.50€ but the shipping to Europe costs twice as much.
I will not bother with that now - have an Ortofon OM5 and a Grado Silver, plus, I just received my brand new Ortofon 2M Red. In the near future a Denon DL-103R should arrive - used, but not much - but that's OT now...
The basic idea is to have the rail above the tonearm - I made a quick mockup in my 3D engineering software - the rail is created from two aforementioned mirrors - I would add a piece of square tubing in front to reinforce the construction and to be able to fix it to the support...
Anyway, I wish a very Happy New Year to everyone 😉
Attachments
Just did another test, similar to Bill's, keeping in mind that the turntable is also a design of my own. Putting the stylus on a non rotating record yields noise at full volume mostly dominate by phono stage noise floor, but I am on a concrete foundation floor so it is quiet in itself. However if I put my ear to the top plinth with a spinning record and no volume I can hear sound transferred into the top plinth, very quiet though. This tells me that decoupling is working at drawing excess energy away from the cartridge vs sending energy to and smearing the detail retrieval, whatever energy the cart doesn't produce into sound we want drawn away anyways, right?.
Colin
Time for an update on my progress.
To all my friends on DIYAudio, Best wishes for a healthy, happy and fulfilling New Year, 2014.
Now here is an update on whatever progress has been made with my LTarm and TT over the past week or so. The test rig for a glass tube rail supported by an internal threaded metal rod and rubber washers on the ends gave such severe resonance problems that I have shelved it for the time being to see if I could determine and fix whatever things were bothering me with my cantilevered, sand filled, and solidly mounted glass tube design. None of these problems were bad enough to keep me from using and enjoying the arm and records.
First I did some testing to find out (if possible) how and where noise and vibration were entering the system.
Breaking the connection between the tonearm mount and the top plinth resulted in very reduced noise of all sorts in the system. This was done with a rubber backed mouse pad. Then I removed the pad and went to the TT platter. Lifting the stylus off the nonrotating platter killed the noise contribution even more. Next I went to the Corian platter with no rubber TT mat. For isolation I chose 8 of those little (1/4" dia) felt stickyback feet used to protect furniture from scratches. Placed them around the top outside edge of the platter. Put a record on the platter and weighed it down with a center weight. Put the stylus on the nonrotating record. Again, all the extraneous noise disappeared. So, to me and my noise problems, they were caused by vibrations being conducted through the TT and its mountings including the ambient house noises into the record and then to the stylus and generator of the audio signal.
Next some thumping and bumping on the underside of the 2 layer shelf revealed this loosely coupled one plywood shelf sitting on top of another plywood shelf was contributing massive amounts of sonic disturbances, resonances and microphonics. Put a double layer of sticky backed snow and ice shield (roofing material) between the two shelf layers, sticky side to the wood both layers. Massive improvement. Noise severely attenuated! Got to do a bit more on the plinth mountings yet, but that will come a bit later. Made a small isolator from the snow and ice shield to go between the cartridge and the headshell. That was too much. Let it go with a triple layer of black electricians vinyl tape. More to report later.
Now to the tonearm. It had been previously determined that there were resonances of the glass tube and its mounting block. The total assembly had a very low frequency resonance. There were also other resonances and modes audible. The primary low frequency resonance was not being affected by the sand damping inside the glass tube. A big chunk of putty on the free end lowered the frequency and damped it some as well. Holding the free end tightly in my hand was most effective. So I decided to build an overhead mounting beam between the main mounting block and the free end of the tube. The photo shows how that was done. The support beam is a 3/4" dia aluminum tube filled with fine sand. There is an aluminum sleeve bored to provide a smooth slip fit over the glass tube. A bar connects this to the overhead tube. The connection bar is enough shorter so there is a constraint of the glass tube but not enough to damage it.
One last item is the replacement of the AC Synchronous motor that was giving noise and other problems with the $2.50, 7.5 degree, 24 volt stepper motor driven by CD with 2 phases 60hz sinewave and an audio amp. Pic show how it is set up for now. Working great, thank you Charles Altman.
Pictures should be self-explanitory relative to the text. The results of all this are clearly audible and very nice!
Note: Black rubber TT mat removed from pic for clarity.
BillG
Attachments
Last edited:
I could align the two mirrors to form a "V" shaped rail - just have to decide first how to fix them into the desired position and a way to fix that contraption to some construction that would hold the arm... Currently in doubt, should I make a "T" shape or a "V" shaped rail.
Can you use a V-groove bearing for the rollers and use a knife edge as the rail, which is the inverse method of your concept?
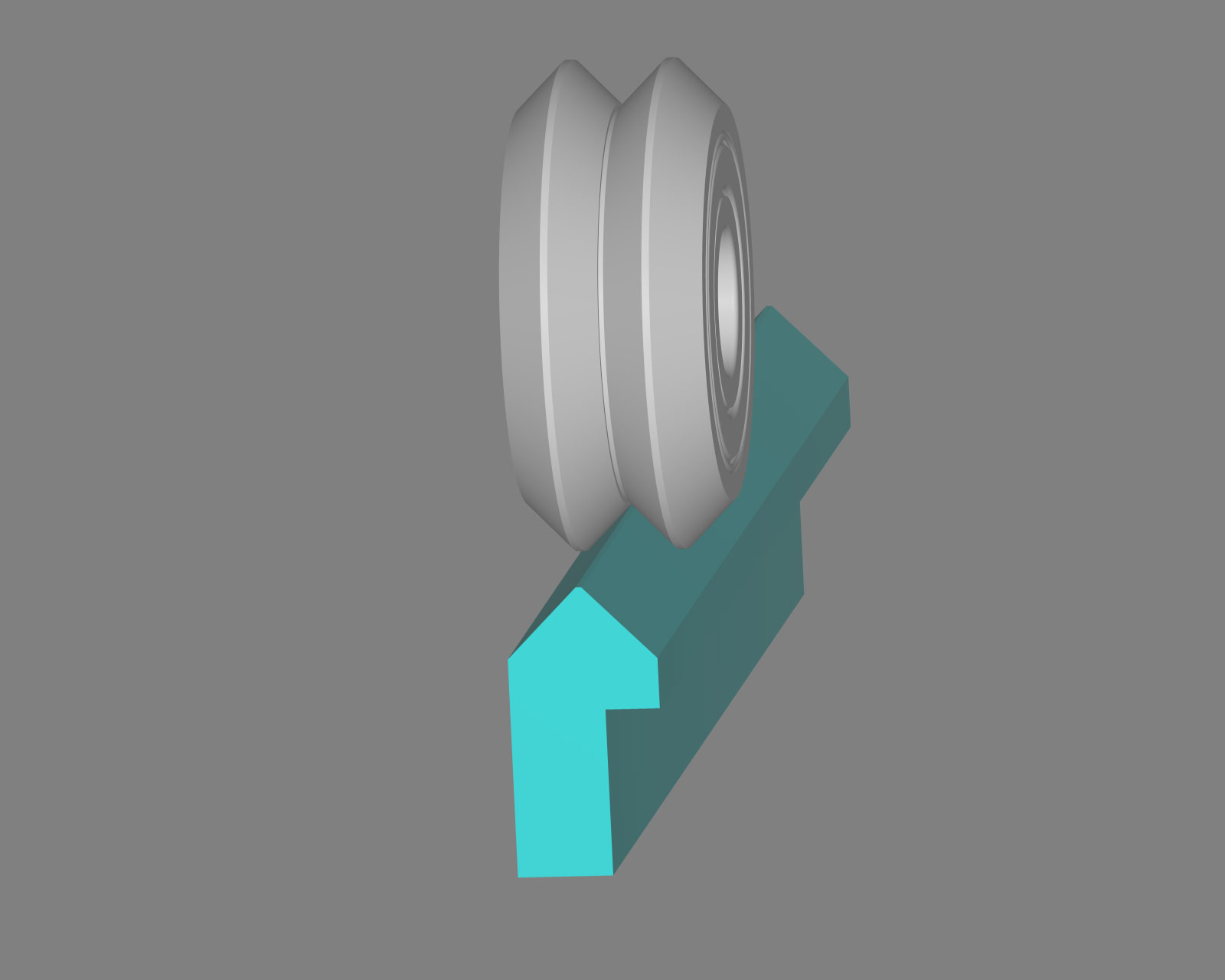
Can you use a V-groove bearing for the rollers and use a knife edge as the rail, which is the inverse method of your concept?
I don't have such bearings - neither they are widely available 'round here. I opted for the 623 bearing because it was easy to find - however, I do have some other sizes/types, but those are either coming from video players/recorders (VHS) or similar but all these are just plain roller bearings. I'm currently looking at ceramic bearings on ebay - but that will take time - those are not cheap nor easy to find and I have to make a decision first what I really want... But I did think about it - still, I'm not ready to pay US$ 63.90 each plus US$ 38 for shipping (165.80) http://tinyurl.com/kfuczmv
It Seems to me with the knife edge we are reinventing the wheel that even opus left behind, and even clearaudio has given up the theory of a freed vertical pivot and gone the way of opus. One thing I've learned with this arm, it's hard to get a design working right, once done its far worth it, but also I've learned it's even harder to convince others I've done the hard yards and offered an easy opportunity for a fabulous arm 🙂.
Colin
Colin
I finally found a proper piece of glass tube. 10mm OD, it was a quartz heater element. Will take it to be cut to desired length... and so on...
I finally found a proper piece of glass tube. 10mm OD, it was a quartz heater element. Will take it to be cut to desired length... and so on...
Great idea !
I have a lot of that somewhere.
Great idea !
I have a lot of that somewhere.
It came to me out of nowhere - I was initially looking at lab equipment, but that's really hard to find where I live, so I started looking at alternatives, thermometers, neon/fluo lights (there are some quite thin ones), fishtank heater housings... and then it just came to me...
Love all these very creative DIY linear tracking arms.
I have a question however, or a concern.
Most of these designs have the 'tonearm' pivot point quite a distance above the platter,record,stylus. If the record is perfectly flat no problem , but in the real world there is inevitably some record warp and it seems to me that the arc of the arm would produce a slight for and aft movement of the stylus over warps. I would have thought that in theory anyway, the pivot point should be on the same plane as the stylus.
Is this likely to be an issue, or is this one of those situations where it might be correct in theory but in practice is irrelevant.
Just curious.
Graham.
I have a question however, or a concern.
Most of these designs have the 'tonearm' pivot point quite a distance above the platter,record,stylus. If the record is perfectly flat no problem , but in the real world there is inevitably some record warp and it seems to me that the arc of the arm would produce a slight for and aft movement of the stylus over warps. I would have thought that in theory anyway, the pivot point should be on the same plane as the stylus.
Is this likely to be an issue, or is this one of those situations where it might be correct in theory but in practice is irrelevant.
Just curious.
Graham.
Graham,
I understand your concerns and I had some as well. However, in the 21st century I have a megaton of lossless albums, a very good CD player and I buy only those records that deserve to be placed on the platter. After all, my record player cost me much more than my CD player - I even paid more just for the cartridge/pickup than what I paid for the CD (Acoustic Advance MCD 203MkII - with balanced tube output) so, I carefully pick my records - no "Spanish dance/flamenco skirts" in the collection... So, the problem is eliminated even before it occurs - only flat and well preserved records. Those which are not perfect, but can be flattened with a clamp, may pass - the rest of them doesn't even come near my platter 🙂
I understand your concerns and I had some as well. However, in the 21st century I have a megaton of lossless albums, a very good CD player and I buy only those records that deserve to be placed on the platter. After all, my record player cost me much more than my CD player - I even paid more just for the cartridge/pickup than what I paid for the CD (Acoustic Advance MCD 203MkII - with balanced tube output) so, I carefully pick my records - no "Spanish dance/flamenco skirts" in the collection... So, the problem is eliminated even before it occurs - only flat and well preserved records. Those which are not perfect, but can be flattened with a clamp, may pass - the rest of them doesn't even come near my platter 🙂
Fair enough, I also only play flat well preserved records on my Oracle Delphi and the original screw down clamp takes care of any slight warps.
I can't help thinking however that the arm/cartridge would perform better with the pivot at or near to stylus contact height.
I notice many uni-pivot arms have this same condition, with the pivot well above the record surface.
I know I am probably trying to solve a problem that doesn't exist !!!!!
Graham.
I can't help thinking however that the arm/cartridge would perform better with the pivot at or near to stylus contact height.
I notice many uni-pivot arms have this same condition, with the pivot well above the record surface.
I know I am probably trying to solve a problem that doesn't exist !!!!!
Graham.
I know I am probably trying to solve a problem that doesn't exist !!!!!
Graham.
No Graham, you are not!
Diy'ers should at least try to put the pivot in appr. the same plane as the stylus.
Steen
Yep, a problem that does exist, but diminished substantially with good dimensioning 🙂. Can you make a short arm pivot in line with the stylus?, no you can't. To be at level with the stylus the pivot must clear the platter which makes for a longer arm. With mechanical bearings this doesn't work so well, then why not air bearing?, yes it's done but a different set of issues due to a floating mechanical ground, so like everything in audio, it's a compromise, at the end of the day I chose to mimic the Neumann lathe dimensions more than I guess standard turntable practice 🙂.
Colin
Colin
I did some math and the lowest point where the tonearm could be supported on a steel or nylon string is around 2-3mm above the record surface - therefore very close to be in-line with the stylus, otherwise the 40-60mm effective length of the tonearm would have to be increased to over 150mm...
- Home
- Source & Line
- Analogue Source
- DIY linear tonearm