Pin Bearing Details
Hi all,
As promised here's some more detailed photos and drawings of the bearings.
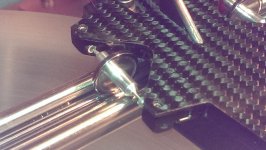
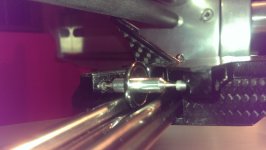
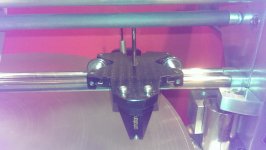
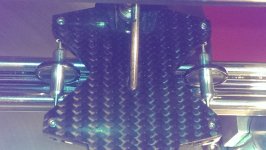
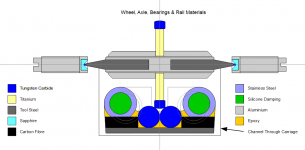
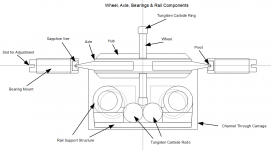
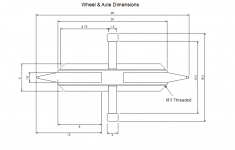
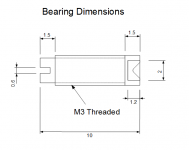
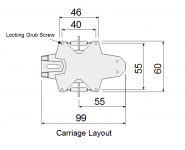
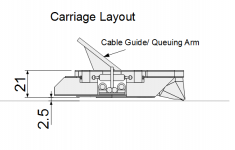
The exact dimensions that I have shown are just the ones that I have used and there is no reason that any of the dimensions or materials can't be changed. The rings that I am using are American ring size 2 that have an inside diameter of 13.2mm. These just happen to be the ideal size for me but are difficult to find. Ring size 4 is easy to find and has an inside diameter of 14.9mm and is also available in 1.5mm width. This may have an advantage if used with 3mm rods. Similarly the total axle length is 28mm pivot to pivot. Keeping the axle relatively long helps keep the bearings rigid. There's no reason not to make them 25 or 30mm. The wheels could just as well be made of aluminium or ceramic instead of titanium. The exact dimensions and materials will depend on your carriage design.
One important point. The pivots have a tip radius of 0.125mm and the vees a cup radius of 0.25mm. I would recommend not changing this.
The pivots were purchased from true point in GB. The vees were purchased from small parts, part of Amazon in the US. The vees are actually metric but are in inches on the Amazon website.
I hope this helps.
Niffy
Hi all,
As promised here's some more detailed photos and drawings of the bearings.
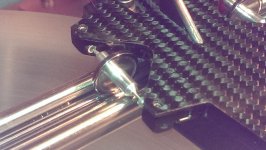
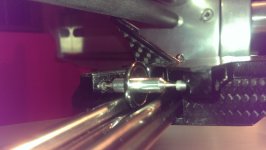
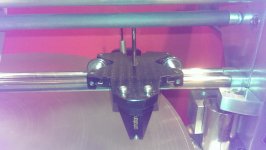
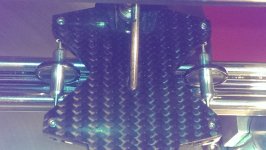
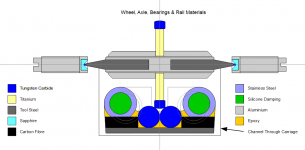
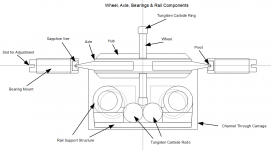
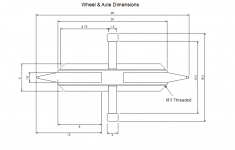
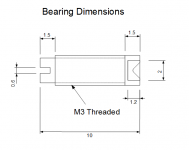
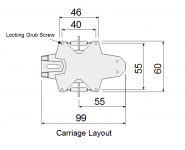
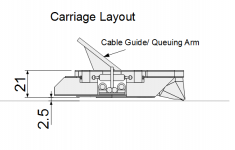
The exact dimensions that I have shown are just the ones that I have used and there is no reason that any of the dimensions or materials can't be changed. The rings that I am using are American ring size 2 that have an inside diameter of 13.2mm. These just happen to be the ideal size for me but are difficult to find. Ring size 4 is easy to find and has an inside diameter of 14.9mm and is also available in 1.5mm width. This may have an advantage if used with 3mm rods. Similarly the total axle length is 28mm pivot to pivot. Keeping the axle relatively long helps keep the bearings rigid. There's no reason not to make them 25 or 30mm. The wheels could just as well be made of aluminium or ceramic instead of titanium. The exact dimensions and materials will depend on your carriage design.
One important point. The pivots have a tip radius of 0.125mm and the vees a cup radius of 0.25mm. I would recommend not changing this.
The pivots were purchased from true point in GB. The vees were purchased from small parts, part of Amazon in the US. The vees are actually metric but are in inches on the Amazon website.
I hope this helps.
Niffy
I would like to ask why you thought that assembly in the picture above was to heavy...I too am designing a linear (no air) tonearm but my question is how much 0f an effect horizontal moving mass has on the performance of a linear arm if friction is negligible in the linear path?...Considering that the centre hole is reasonably centered.Cancelled the second one, mass is getting too high!. I've gone back to building a second copy of the first arm 🙂. This will be for a turntable project build!. Thank you for all the interest in this project and I'd urge anyone to give it a go 🙂, its worth it and easy to build.
Colin
Niffy
Thanks for sharing!
What is the total mass of the carriage including everything?
Jim
55g
Niffy
I would like to ask why you thought that assembly in the picture above was to heavy...I too am designing a linear (no air) tonearm but my question is how much 0f an effect horizontal moving mass has on the performance of a linear arm if friction is negligible in the linear path?...Considering that the centre hole is reasonably centered.
Hi Stuart,
I'm not sure if the question was aimed at me or Colin. We haven't heard from Colin in a while. Hello Colin are you still following? I don't know what your level of knowledge is so I'll start from basics and work up.
Unfortunately you can't assume that linear friction is negligible. With mechanical linear tracking tonearms the level of friction is proportional to the mass of the arm, if you double the mass of the arm the friction also doubles. The level of friction is related to the mass by the coefficient of friction (cof) where:
Mass x cof = friction
The level of friction is the amount of force required to push the carriage sideways. In these arms this force comes from the record groove pushing against the stylus. If you push the stylus from the side it will move relative to the cartridge. The amount the stylus moves is dependent upon how hard you push it and the cartridge compliance. The higher the compliance the further it will move. As the stylus moves the cantilever it rotates slightly causing the stylus to become slightly twisted in the groove misaligning it. This results in a reduction in sound quality.
Therefore lower friction results in higher sound quality.
I'll use my arm as an example. I'll round off all the numbers to make life easier.
My arm weighs 50g and my ball race bearings have a coefficient of friction of 0.006. The amount of force required to move the carriage is therefore 0.3g. This will result in a tracking misalignment, with my cartridge, of 0.75°. Which is quite a lot.
If I halve the carriages mass to 25g and still use the same bearings the force will also halve to 0.15g and the tracking error will reduce to 0.375°.
I didn't want to reduce my carriage mass but I did want to reduce the tracking misalignment. This is one of the reasons why I started investing better bearings.
With the 50g carriage but using the pin bearings with a coefficient of friction of 0.0017 the force is only 0.085g and the tracking misalignment is now reduced to 0.21°.
Having the groove pressing harder on one side of the stylus also means that the tracking force will be different for the left and right channels. If the force is much too high it may make the stylus skip out of the groove.
Higher carriage mass has several advantages.
First there is more mass to control the cartridge especially in the bass. A heavier carriage will tend to give a more solid sound. Have a look at the discussion about effective mass from page 207.
Secondly a heavier carriage can be built more solidly better controlling vibration and resonance and in doing so increase sound quality.
If you are new to diy tonearm building I would recommend looking back over the last half of this thread and then copying Colin's latest version of his arm. He did a lot of testing and ended up with a very well sorted arm. This will teach a lot. Then start adapting it into your own creation.
Have fun building.
Niffy
Niffy,
First of all, congratulation for your excellent work. Have few questions! Somebody in early post here talked about having a group buy for this arm.
I would personally love to give a try to your tone-arm on my setup and my main question is: can I put this tone-arm on the salvation deck thus swapping the Terminator TP3 out to try your design in comparison?
Would there be the possibility to have a precision manufacturer maker for this parts? Would you have any leads?
Again, your work on this design is really incredible!
First of all, congratulation for your excellent work. Have few questions! Somebody in early post here talked about having a group buy for this arm.
I would personally love to give a try to your tone-arm on my setup and my main question is: can I put this tone-arm on the salvation deck thus swapping the Terminator TP3 out to try your design in comparison?
Would there be the possibility to have a precision manufacturer maker for this parts? Would you have any leads?
Again, your work on this design is really incredible!
Last edited:
Hi Stefano,
Thanks.
This arm was built as a one off. I never contemplated having more than one made and less still having anyone else built it. Building everything myself is a large part of the joy of this project. Everything was initially drawn up in detail but not all modifications made it back to the original drawing. Also not every drawing is dimensioned. The carriage construction would be partially difficult to follow. Also the arm and deck are designed as a single unit. I didn't compromise myself by sticking to a standard mounting position. The height of the arm is set to match my platter height and would fit very few decks. The lateral tracking angle adjuster actually sits below the sub-chassis where it is easily accessible. It might not be on another deck.
The entire base section of the arm would need to be completely redesigned to make it usable on a variety of decks, which it would have to in order to make a group buy feasible.
Building the carriage and rails from my plans and then designing your own base section is probably the best approach. Though my arm base is rather pretty so maybe base it on mine. Also my base was designed to be able to be built by me on a workmate in the corner of my kitchen. A fully equipped workshop may be able to make some of the components in a more efficient manner.
I have absolutely no idea who you could get to make the bits. (and there are a lot of bits)
I have absolutely no problem with anyone building a copy of my arm but it will take considerable work on my behalf to consolidate the plans and to write a description of how it's constructed.
First find out how many want in. It won't cost pennies. There's some exotic materials in there.
Niffy
Thanks.
This arm was built as a one off. I never contemplated having more than one made and less still having anyone else built it. Building everything myself is a large part of the joy of this project. Everything was initially drawn up in detail but not all modifications made it back to the original drawing. Also not every drawing is dimensioned. The carriage construction would be partially difficult to follow. Also the arm and deck are designed as a single unit. I didn't compromise myself by sticking to a standard mounting position. The height of the arm is set to match my platter height and would fit very few decks. The lateral tracking angle adjuster actually sits below the sub-chassis where it is easily accessible. It might not be on another deck.
The entire base section of the arm would need to be completely redesigned to make it usable on a variety of decks, which it would have to in order to make a group buy feasible.
Building the carriage and rails from my plans and then designing your own base section is probably the best approach. Though my arm base is rather pretty so maybe base it on mine. Also my base was designed to be able to be built by me on a workmate in the corner of my kitchen. A fully equipped workshop may be able to make some of the components in a more efficient manner.
I have absolutely no idea who you could get to make the bits. (and there are a lot of bits)
I have absolutely no problem with anyone building a copy of my arm but it will take considerable work on my behalf to consolidate the plans and to write a description of how it's constructed.
First find out how many want in. It won't cost pennies. There's some exotic materials in there.
Niffy
Niffy,
Thank you so much for your explanatory answer. Unfortunately, I just speak for myself, I don't personally have time nor the resources know-how, to start building this complicated arm like you do.
I really like the idea and I am curious to try it against the T3Pro.
I also understand your building process and this only fits your setup in order not to compromise any build quality (just like a F1 car).
I also assume, that if I do understand this aspect correctly, many others do as well...i.e. this tone-arm will cost some money due to the expensive materials involved. It would still be interesting and worth to make a rough cost of the arm (parts and estimate labor) prior to start any initiative.
Maybe your suggestion to find out first how many people would be interested to do a group buy is spot on. Nevertheless, even if there were 10-15 people interested in this, how would we solve the problem to make this tone-arm "universal" and would there be detail drawings to pass to the maker?
If there was no possibility to manufacture it to hit this target so that everybody, at least in the group buy, could easily use it on their TT, then it seems pointless to even hope for a group buy...if you know what I mean and if it makes any sense to you.
I also understand that you might not feel inclined to do any extra work such as adjusting and/or creating drawings for manufacturing...but I think it would must also be exciting for you if other people get to try your wonderful idea as well and maybe can share their opinion...maybe I am wrong 🙂
Thank you so much for your explanatory answer. Unfortunately, I just speak for myself, I don't personally have time nor the resources know-how, to start building this complicated arm like you do.
I really like the idea and I am curious to try it against the T3Pro.
I also understand your building process and this only fits your setup in order not to compromise any build quality (just like a F1 car).
I also assume, that if I do understand this aspect correctly, many others do as well...i.e. this tone-arm will cost some money due to the expensive materials involved. It would still be interesting and worth to make a rough cost of the arm (parts and estimate labor) prior to start any initiative.
Maybe your suggestion to find out first how many people would be interested to do a group buy is spot on. Nevertheless, even if there were 10-15 people interested in this, how would we solve the problem to make this tone-arm "universal" and would there be detail drawings to pass to the maker?
If there was no possibility to manufacture it to hit this target so that everybody, at least in the group buy, could easily use it on their TT, then it seems pointless to even hope for a group buy...if you know what I mean and if it makes any sense to you.
I also understand that you might not feel inclined to do any extra work such as adjusting and/or creating drawings for manufacturing...but I think it would must also be exciting for you if other people get to try your wonderful idea as well and maybe can share their opinion...maybe I am wrong 🙂
Hi Stefano,
It would be nice to see the arm get out into the world. Feedback from fellow audiophiles would be great. The sight of visitors jaws hitting the floor is all well and good but most of them have never heard a decent system.
I had considered a rip off of the clearaudio TT2 arm base that swivels up rather than sliding as a method of getting the arm to fit any deck. Care would need to be taken to keep the weight down so that it could be used on suspended chassis turntables.
There yo see, you've got me thinking already.
Niffy
It would be nice to see the arm get out into the world. Feedback from fellow audiophiles would be great. The sight of visitors jaws hitting the floor is all well and good but most of them have never heard a decent system.
I had considered a rip off of the clearaudio TT2 arm base that swivels up rather than sliding as a method of getting the arm to fit any deck. Care would need to be taken to keep the weight down so that it could be used on suspended chassis turntables.
There yo see, you've got me thinking already.
Niffy
You are a genius!
Regarding the clearaudio method of getting the arm out of the way, will this be detrimental to the sound, given that you have a lot of moving parts assembled?
The T3Pro is not very handy to use and lots of care needs to be excerpt when removing the vinyl and it would be certainly nice to have a way of getting the arm out when removing the vinyl, but if this comes to a price for the sound, I am not sure it would be worth the extra complexity.
If then you are excited to produce drawings and have other people experience your design and have valuable feedbacks, then how do you think would be best to proceed? Do we want to ask here how many people would be part of a group buy or opening a separate thread?
Regarding the clearaudio method of getting the arm out of the way, will this be detrimental to the sound, given that you have a lot of moving parts assembled?
The T3Pro is not very handy to use and lots of care needs to be excerpt when removing the vinyl and it would be certainly nice to have a way of getting the arm out when removing the vinyl, but if this comes to a price for the sound, I am not sure it would be worth the extra complexity.
If then you are excited to produce drawings and have other people experience your design and have valuable feedbacks, then how do you think would be best to proceed? Do we want to ask here how many people would be part of a group buy or opening a separate thread?
Excellent workmanship and design. I was wondering do the wheels moving on track add to friction ? Also since the concentric grooves make the tonearm move would adding some biasing mechanism be helpful ?
Thanks and regards.
Thanks and regards.
Hi Hiten,
The total amount of friction is made of two components. The friction of the pins rotating in the vee cups and the rolling resistance of the wheels rolling on the track. About 20-25% of the total friction is due to the pin bearings and the remaining 75-80% is due to the rolling resistance. By using the best possible materials and design I have reduced the level of friction from each component to an absolute minimum. I doubt that it is possible to reduce the total friction in a mechanical linear bearing much further.
Unfortunately most records are not perfectly concentric so the carriage has to constantly move back and forth. Any biasing system would have to constantly sense which direction the bias was needed in and change the direction of that bias back and forth. Several manufacturers of linear tracking arms have built such arms, they are known as active linear tracking tonearms. Unfortunately the sensing and bias mechanisms normally create more problems than they solve. There are a couple of exceptions but they are all in the mega bucks price range.
It is possible to make a purely passive bias system, it does make changing records a phaf but has benefits beyond just biasing. It also requires precision manufacture well beyond my current capabilities.
Niffy.
The total amount of friction is made of two components. The friction of the pins rotating in the vee cups and the rolling resistance of the wheels rolling on the track. About 20-25% of the total friction is due to the pin bearings and the remaining 75-80% is due to the rolling resistance. By using the best possible materials and design I have reduced the level of friction from each component to an absolute minimum. I doubt that it is possible to reduce the total friction in a mechanical linear bearing much further.
Unfortunately most records are not perfectly concentric so the carriage has to constantly move back and forth. Any biasing system would have to constantly sense which direction the bias was needed in and change the direction of that bias back and forth. Several manufacturers of linear tracking arms have built such arms, they are known as active linear tracking tonearms. Unfortunately the sensing and bias mechanisms normally create more problems than they solve. There are a couple of exceptions but they are all in the mega bucks price range.
It is possible to make a purely passive bias system, it does make changing records a phaf but has benefits beyond just biasing. It also requires precision manufacture well beyond my current capabilities.
Niffy.
Hi Stefano,
The carriage was developed specifically with the ortofon 2M black in mind. This is quite a low mass cartridge and is high compliance. Using the carriage with similar cartridges would work well unless that cartridge is less than 18mm high. I googled several different cartridge specs. Most of the cartridges in the price range that I would envision being used would require a higher effective mass. I didn't have long so I didn't check every make. The ortofon quintet series work be just about ok. The audio technica oc series was way out with a vertical cantilever resonance of 15hz.I'll have to put some of their specs into my analysis spread sheet and see what I get. A small carriage redesign may be necessary to make it more broadly compatible.
Niffy
The carriage was developed specifically with the ortofon 2M black in mind. This is quite a low mass cartridge and is high compliance. Using the carriage with similar cartridges would work well unless that cartridge is less than 18mm high. I googled several different cartridge specs. Most of the cartridges in the price range that I would envision being used would require a higher effective mass. I didn't have long so I didn't check every make. The ortofon quintet series work be just about ok. The audio technica oc series was way out with a vertical cantilever resonance of 15hz.I'll have to put some of their specs into my analysis spread sheet and see what I get. A small carriage redesign may be necessary to make it more broadly compatible.
Niffy
I personally use:
1) ZYX 4D
2) Clearaudio Titanium V2
3) Clearaudio Goldfinger Statement
..which I don't think they have similar characteristics to yours (maybe similar medium compliance in common?).
Do you have any height/VTA adjustment? I assume since you have tailored it to your specific needs, you have omitted this adjustment for now. Would it possible or a good idea to include simple mechanism? This would sort out the variable of different height for different cartridges.
Moreover, to work with a broader range of cartridges, it would also help to have little slots (3-4mm length) by the head-shell to be able to move the cart back and forth in order to find proper alignment.
If there are only a hand full of people interested (since I don't see much excitement about this so far, I assume not so many people will want to participate), my assumption is that there will likely be no shop available or willing to make 2-3 units at a decent price.
Would you be able/willing to replicate a very limited amount of arms and give pricing including cost of parts and your labor?
If there are more requests, at that point, a shop would definitely make more sense.
Let us know your thoughts.
1) ZYX 4D
2) Clearaudio Titanium V2
3) Clearaudio Goldfinger Statement
..which I don't think they have similar characteristics to yours (maybe similar medium compliance in common?).
Do you have any height/VTA adjustment? I assume since you have tailored it to your specific needs, you have omitted this adjustment for now. Would it possible or a good idea to include simple mechanism? This would sort out the variable of different height for different cartridges.
Moreover, to work with a broader range of cartridges, it would also help to have little slots (3-4mm length) by the head-shell to be able to move the cart back and forth in order to find proper alignment.
If there are only a hand full of people interested (since I don't see much excitement about this so far, I assume not so many people will want to participate), my assumption is that there will likely be no shop available or willing to make 2-3 units at a decent price.
Would you be able/willing to replicate a very limited amount of arms and give pricing including cost of parts and your labor?
If there are more requests, at that point, a shop would definitely make more sense.
Let us know your thoughts.
Last edited:
Isn't a very small coefficient of friction necessary at the wheel/rod interface? I haven't run the numbers (nor am I especially qualified to do so) but it would appear that as one approaches zero friction, the wheels would slide rather than rotate. It also seems to me that one would want slightly greater friction at the wheel/rod interface than at the pivot bearing. If true, then there is a very small, optimum coefficient but not zero.
Hi Seth.
For lateral motion the coefficient of friction between the wheels and rods is unimportant. The wheels do not slide laterally at all, they roll. Even if the coefficient of friction was a tenth as much the resistance to sliding would still be much higher than the resistance to rolling. The coefficient of friction between two pieces of polished tungsten carbide is 0.15. The total coefficient for the entire bearing system is only 0.00177. As long as the sliding resistance remains above the combined rolling resistance and torque due to the friction of the pin bearings no sliding will occur.
For vertical motion the wheels do slide on the rods. The relatively low cof of tc on tc combined with the very small amount of vertical movement at the bearing means friction is very low.
A small amount of friction is useful in that it acts to damp the motion of the carriage. However if you did have a zero friction bearing you could easily damp the carriage by other means.
Niffy
For lateral motion the coefficient of friction between the wheels and rods is unimportant. The wheels do not slide laterally at all, they roll. Even if the coefficient of friction was a tenth as much the resistance to sliding would still be much higher than the resistance to rolling. The coefficient of friction between two pieces of polished tungsten carbide is 0.15. The total coefficient for the entire bearing system is only 0.00177. As long as the sliding resistance remains above the combined rolling resistance and torque due to the friction of the pin bearings no sliding will occur.
For vertical motion the wheels do slide on the rods. The relatively low cof of tc on tc combined with the very small amount of vertical movement at the bearing means friction is very low.
A small amount of friction is useful in that it acts to damp the motion of the carriage. However if you did have a zero friction bearing you could easily damp the carriage by other means.
Niffy
Thank you very much for that crystal clear, concise explanation.
I have got to build this iteration!
Having participated in several group buys in the past, one can not predict interest based on initial response. It is only after a real product is put forth that one can put numbers to a project. The amount of leg work involved in getting this into even very limited production will be significant. However, there is a working prototype so that huge hurdle has been overcome. This is not vaporware.
I have got to build this iteration!
Having participated in several group buys in the past, one can not predict interest based on initial response. It is only after a real product is put forth that one can put numbers to a project. The amount of leg work involved in getting this into even very limited production will be significant. However, there is a working prototype so that huge hurdle has been overcome. This is not vaporware.
Hi Stefano.
I'll check those cartridges out.
I do have a VTA adjustment. It has a range of about 7mm. So will cater for all cartridges. The carriage, however, is designed for an 18mm tall cartridge. This leaves only a 2.5mm gap between the carriage and the record. A shorter cartridge may cause the carriage to foul the record. A taller cartridge will slightly raise the pivot point which will worsen warp wow and tracking force variation. The amount it worsens would be very small unless the cartridge was much taller than any I've seen.
Slots are unnecessary. The cartridge is only a half millimetre narrower than the recess it sits in. Aligning the cartridge accuracy in the carriage is easy, in fact it is difficult to get it wrong. Simply rotate the entire arm until the cartridge is perfectly tangential. Of course there is a locking adjuster to do this.
I'll carry on investigating how easy a more universal carriage is. I have my eye perpetually drooling over the cadenza range. I'd have to build a different carriage specifically tuned to any different cartridge.
And sorry. I get precious few build days and always at least one project more than I have time for. If I ever built another arm it will be part of a completly new deck incorporating any new ideas I may have. A mark 2. And I'll be building it for me.
Niffy
I'll check those cartridges out.
I do have a VTA adjustment. It has a range of about 7mm. So will cater for all cartridges. The carriage, however, is designed for an 18mm tall cartridge. This leaves only a 2.5mm gap between the carriage and the record. A shorter cartridge may cause the carriage to foul the record. A taller cartridge will slightly raise the pivot point which will worsen warp wow and tracking force variation. The amount it worsens would be very small unless the cartridge was much taller than any I've seen.
Slots are unnecessary. The cartridge is only a half millimetre narrower than the recess it sits in. Aligning the cartridge accuracy in the carriage is easy, in fact it is difficult to get it wrong. Simply rotate the entire arm until the cartridge is perfectly tangential. Of course there is a locking adjuster to do this.
I'll carry on investigating how easy a more universal carriage is. I have my eye perpetually drooling over the cadenza range. I'd have to build a different carriage specifically tuned to any different cartridge.
And sorry. I get precious few build days and always at least one project more than I have time for. If I ever built another arm it will be part of a completly new deck incorporating any new ideas I may have. A mark 2. And I'll be building it for me.
Niffy
yes, you are right! Unfortunately price will vary greatly depending on volume.
In order to run numbers for people to determine whether they can afford it or not, we need number of samples to be built...it's like a dog that chases its tail 🙂
Anyway, I push the same question out: what is the best method to sense interest for this particular group buy?
Moreover, and probably most important for the people out there, will the arm be capable of accommodating various applications with different desks and different cartridges?
This is in my opinion a lot of work for Niffy that might understandably not be willing to do and go through with.
That is why I am putting these questions out.
In order to run numbers for people to determine whether they can afford it or not, we need number of samples to be built...it's like a dog that chases its tail 🙂
Anyway, I push the same question out: what is the best method to sense interest for this particular group buy?
Moreover, and probably most important for the people out there, will the arm be capable of accommodating various applications with different desks and different cartridges?
This is in my opinion a lot of work for Niffy that might understandably not be willing to do and go through with.
That is why I am putting these questions out.
Last edited:
Hi all.
I write most of my longer article type posts on the bus on my way to my work depot. I wrote the following post over the last week and it might have got a little out of hand. It is a bit long. I find writing the posts a good way of consolidating my thoughts and I have had new ideas triggered in doing so. I hope at least some of you find these posts interesting and hopefully sometimes useful.
Niffy
I write most of my longer article type posts on the bus on my way to my work depot. I wrote the following post over the last week and it might have got a little out of hand. It is a bit long. I find writing the posts a good way of consolidating my thoughts and I have had new ideas triggered in doing so. I hope at least some of you find these posts interesting and hopefully sometimes useful.
Niffy
- Home
- Source & Line
- Analogue Source
- DIY linear tonearm