I can DIY my own cloth surround, but I would need to create a simple mold for it. Maybe next time, for now is off the shelf.
The paper is the most crucial part now which I need to explore more and find out more on the hardening methods.
Flour glue hardening is not giving me good results at the moment... 🙁
The paper is the most crucial part now which I need to explore more and find out more on the hardening methods.
Flour glue hardening is not giving me good results at the moment... 🙁
ghemmi,
What we read on the forums is that the general idea for ideal wide-band driver cone material is "light" and "rigid"... but in balanced way that there are not too many unwanted resonances throughout the frequency spectrum. Any type of glue/coating that is likely to over-damp the cone or add too much mass is unlikely to give you good results. Also materials that can make it too hard might result in too much resonance.
What do you want to achieve with the coating/doping of your speaker cones?
Good luck and keep up the good work. 🙂
What we read on the forums is that the general idea for ideal wide-band driver cone material is "light" and "rigid"... but in balanced way that there are not too many unwanted resonances throughout the frequency spectrum. Any type of glue/coating that is likely to over-damp the cone or add too much mass is unlikely to give you good results. Also materials that can make it too hard might result in too much resonance.
What do you want to achieve with the coating/doping of your speaker cones?
Good luck and keep up the good work. 🙂
ghemmi,
Great thread, I just found it today by accident. I also build my own drivers but I have not been trying to develop FR drivers. I can attest to the pain with working with the Neo magnet material, I use Mgoe 52 magnet sections and they are a real bear to work with. In my design I can't use uncharged magnets as it would be nearly impossible to post charge the magnets so finding solutions to install them is one of the tricks to all of this. I do use a copper sleeve on the pole piece and though I have thought about platting the center pole piece my construction is very different and that wouldn't work. The other problem with platting the copper is that it really needs to have a significant thickness to work well as an effective Faraday ring.
My cones are made of carbon and kevlar and some secret sauce. Nothing like anyone else has developed as I find most composite cones are much to rigid and actually cause some real problems with high "Q" cone breakup modes. It is a real balance between stiffness and damping qualities.
From my past speaking with friends who also work on the speaker side of things I do know that many of the paper cone materials out there aren't really just paper pulp but have other additives such as reticulated polyester fibers and cotton fibers and other trade secret ingredients. Most are made by a slush molding process with double screens and I am not privy to what they are using as a binder. If I was attempting to make a paper material harder I might look at some type of a water based acrylic resin for that purpose. Varnish really isn't all that rigid so for anything but sealing a paper material I don't think that would have much advantage.
I am impressed by your very neat work on both the speaker and the tooling. I have also had to make my own molds to create my cones but they are double sided closed molds so a bit different than what you are able to use. My first concern with your design was the overlaps of the main cone, that would place an uneven mass in the cone and I'm curious how that would affect the breakup modes of the actual cone. The way you attached the whizzer cone shouldn't cause any issues though I am not a big fan of any whizzers myself due to the uncontrolled radial modes of an unsupported edge in a whizzer.
Make sure that any foam surround you are using contains a UV inhibitor or you will find out later that any exposure to sunlight will eventually cause the foam to fall apart. JBL and many others never seem to learn this lesson. I use a very thin section thermo-formed TPU material that is made in the Philippines though I am looking at injection molding a similar material due to the fact that I am designing some rather strange shaped surrounds. I need much more excursion than you do and a standard 1/2 roll surround is a problem and increasing the diameter to get a larger excursion is a no go on my part.
On your spider I find that interesting. At the same time you should be aware that the standard cotton fiber spiders are doped with phenolic resin to make them actually work as a spring.
Steven
Great thread, I just found it today by accident. I also build my own drivers but I have not been trying to develop FR drivers. I can attest to the pain with working with the Neo magnet material, I use Mgoe 52 magnet sections and they are a real bear to work with. In my design I can't use uncharged magnets as it would be nearly impossible to post charge the magnets so finding solutions to install them is one of the tricks to all of this. I do use a copper sleeve on the pole piece and though I have thought about platting the center pole piece my construction is very different and that wouldn't work. The other problem with platting the copper is that it really needs to have a significant thickness to work well as an effective Faraday ring.
My cones are made of carbon and kevlar and some secret sauce. Nothing like anyone else has developed as I find most composite cones are much to rigid and actually cause some real problems with high "Q" cone breakup modes. It is a real balance between stiffness and damping qualities.
From my past speaking with friends who also work on the speaker side of things I do know that many of the paper cone materials out there aren't really just paper pulp but have other additives such as reticulated polyester fibers and cotton fibers and other trade secret ingredients. Most are made by a slush molding process with double screens and I am not privy to what they are using as a binder. If I was attempting to make a paper material harder I might look at some type of a water based acrylic resin for that purpose. Varnish really isn't all that rigid so for anything but sealing a paper material I don't think that would have much advantage.
I am impressed by your very neat work on both the speaker and the tooling. I have also had to make my own molds to create my cones but they are double sided closed molds so a bit different than what you are able to use. My first concern with your design was the overlaps of the main cone, that would place an uneven mass in the cone and I'm curious how that would affect the breakup modes of the actual cone. The way you attached the whizzer cone shouldn't cause any issues though I am not a big fan of any whizzers myself due to the uncontrolled radial modes of an unsupported edge in a whizzer.
Make sure that any foam surround you are using contains a UV inhibitor or you will find out later that any exposure to sunlight will eventually cause the foam to fall apart. JBL and many others never seem to learn this lesson. I use a very thin section thermo-formed TPU material that is made in the Philippines though I am looking at injection molding a similar material due to the fact that I am designing some rather strange shaped surrounds. I need much more excursion than you do and a standard 1/2 roll surround is a problem and increasing the diameter to get a larger excursion is a no go on my part.
On your spider I find that interesting. At the same time you should be aware that the standard cotton fiber spiders are doped with phenolic resin to make them actually work as a spring.
Steven
ghemmi,
What we read on the forums is that the general idea for ideal wide-band driver cone material is "light" and "rigid"... but in balanced way that there are not too many unwanted resonances throughout the frequency spectrum. Any type of glue/coating that is likely to over-damp the cone or add too much mass is unlikely to give you good results. Also materials that can make it too hard might result in too much resonance.
What do you want to achieve with the coating/doping of your speaker cones?
Good luck and keep up the good work. 🙂
I have mulberry papers that are not harden when i got them. I testing out various methods of paper hardening using starch glue or other glues commonly used by manufacturers.
ghemmi,
Great thread, I just found it today by accident. I also build my own drivers but I have not been trying to develop FR drivers. I can attest to the pain with working with the Neo magnet material, I use Mgoe 52 magnet sections and they are a real bear to work with. In my design I can't use uncharged magnets as it would be nearly impossible to post charge the magnets so finding solutions to install them is one of the tricks to all of this. I do use a copper sleeve on the pole piece and though I have thought about platting the center pole piece my construction is very different and that wouldn't work. The other problem with platting the copper is that it really needs to have a significant thickness to work well as an effective Faraday ring.
My cones are made of carbon and kevlar and some secret sauce. Nothing like anyone else has developed as I find most composite cones are much to rigid and actually cause some real problems with high "Q" cone breakup modes. It is a real balance between stiffness and damping qualities.
From my past speaking with friends who also work on the speaker side of things I do know that many of the paper cone materials out there aren't really just paper pulp but have other additives such as reticulated polyester fibers and cotton fibers and other trade secret ingredients. Most are made by a slush molding process with double screens and I am not privy to what they are using as a binder. If I was attempting to make a paper material harder I might look at some type of a water based acrylic resin for that purpose. Varnish really isn't all that rigid so for anything but sealing a paper material I don't think that would have much advantage.
I am impressed by your very neat work on both the speaker and the tooling. I have also had to make my own molds to create my cones but they are double sided closed molds so a bit different than what you are able to use. My first concern with your design was the overlaps of the main cone, that would place an uneven mass in the cone and I'm curious how that would affect the breakup modes of the actual cone. The way you attached the whizzer cone shouldn't cause any issues though I am not a big fan of any whizzers myself due to the uncontrolled radial modes of an unsupported edge in a whizzer.
Make sure that any foam surround you are using contains a UV inhibitor or you will find out later that any exposure to sunlight will eventually cause the foam to fall apart. JBL and many others never seem to learn this lesson. I use a very thin section thermo-formed TPU material that is made in the Philippines though I am looking at injection molding a similar material due to the fact that I am designing some rather strange shaped surrounds. I need much more excursion than you do and a standard 1/2 roll surround is a problem and increasing the diameter to get a larger excursion is a no go on my part.
On your spider I find that interesting. At the same time you should be aware that the standard cotton fiber spiders are doped with phenolic resin to make them actually work as a spring.
Steven
Thanks for the info
One reason why i choose paper due to its self damping and rigidity. I have thought of carbon fibre, but difficult to control the thickness and weight as i need to come with the toolings, so i stick to paper for the moment.
Copper plating for Faraday's ring is one of the method i saw in voxavit fullrange. But for my fullrange the xmax is small the Faraday's ring might not be have much effects.
Got my fabrications... but.... 🙁 I forgotten the take the whizzer cone inner diameter into account. Now I have to redo the phase plug🙁🙁🙁
But I can start the bind post and do some measurements.
An externally hosted image should be here but it was not working when we last tested it.
But I can start the bind post and do some measurements.
An externally hosted image should be here but it was not working when we last tested it.


Binding post soldered and TS parameters measured using WT3
* f(s)= 68.64 Hz
* R(e)= 3.80 Ohms
* Z(max)= 100.40 Ohms
* Q(ms)= 9.522
* Q(es)= 0.375
* Q(ts)= 0.361
* V(as)= 15.860 liters (0.560 cubic feet)
* L(e)= 0.78 mH
* n(0)= 1.30 %
* SPL= 93.25 1W/1m
* M(ms)= 7.17 grams
* C(ms)= 0.75 mm/N
* BL= 5.60
i hang my head in shame... i have a hard time with woodworking but have always longed to make my own drivers this thread makes me realize i've a long way to go....
I find woodworking difficult for me, literally. Always end up a big mess when trying to assemble my speaker enclosure 🙁
Maybe you should try building your own drivers too, bit of research, create the supporting tools and try smaller drivers like 4" or 6" 🙂
Maybe you should try building your own drivers too, bit of research, create the supporting tools and try smaller drivers like 4" or 6" 🙂
i have a set of fifteen inch drivers that have cones that are damaged my thought was to remove the cones and attempt to use the coil and spider assembly as a driver for an attempt at a flat panel.
or i could try making my own cone to rebuild them...
or i could try making my own cone to rebuild them...
An externally hosted image should be here but it was not working when we last tested it.
How did you design the phase plugs? How do you deside on their lenght, angle and so on? I will be designing phase plugs for the humble Visaton BG20, and need to do some reading. It proved hard to find any theoretical articles online...
i have a set of fifteen inch drivers that have cones that are damaged my thought was to remove the cones and attempt to use the coil and spider assembly as a driver for an attempt at a flat panel.
or i could try making my own cone to rebuild them...
15" is pretty big, but if you can find the cone and voice coil replacement it will be a good chance to learn out how to glue and apply the surround/spider to the cone. 🙂
How did you design the phase plugs? How do you deside on their lenght, angle and so on? I will be designing phase plugs for the humble Visaton BG20, and need to do some reading. It proved hard to find any theoretical articles online...
I just use a rough design from AutoCAD, I have no idea how this phase plug will perform. But I believe the type of materials for the phase plug is more important. I'm also trying to use phenolic for the phase plug, or maybe carbon fiber materials 😀
Last edited:
I also figured it's hit and miss somehow... That's why I plan to model phase plugs with changeable parameters, 3d print a shitload of them and measure response. PLA should be both hard and dense enough for prototyping.
If only I know which frequencies "originate" from what part of the whizzer cone... That would make things a bit simpler.
If only I know which frequencies "originate" from what part of the whizzer cone... That would make things a bit simpler.
i've some experience with doing recones with both pre-assembled and separate component re-cone kits so gluing and assembly/aligning chops are fair.
but making those things, cone, coils, spider and surrounds... i am humbled by your abilities.
spiders and pleated surrounds are a black art to me currently.
but making those things, cone, coils, spider and surrounds... i am humbled by your abilities.
spiders and pleated surrounds are a black art to me currently.
I also figured it's hit and miss somehow... That's why I plan to model phase plugs with changeable parameters, 3d print a shitload of them and measure response. PLA should be both hard and dense enough for prototyping.
If only I know which frequencies "originate" from what part of the whizzer cone... That would make things a bit simpler.
The cons of using 3D printing, from my experience the surface is not smooth and the material type is limited.
The freq behavior from my knowledge, can only know from measuring using Freq analyzer.
But too much of a hassle for me at the moment, but will go into that bit more detail after I have the basic measurement out by this month. 😀
i've some experience with doing recones with both pre-assembled and separate component re-cone kits so gluing and assembly/aligning chops are fair.
but making those things, cone, coils, spider and surrounds... i am humbled by your abilities.
spiders and pleated surrounds are a black art to me currently.
Making cones and voice coil you might need a few types jig which you can see from picture I posted earlier.
But I would say one thing, just try. I made many mistake while designing this fullrange ending up many phenolic spider and speaker baskets. Only then we got the experience and know how.
The cons of using 3D printing, from my experience the surface is not smooth and the material type is limited.
Is totally smooth surface of a phase plug a must? I imagine that treble "happens" no matter what the position of the cone when playing an underlaying bass note, thereby treble reflecting off of the phase plug at random angles. I hope I'm not geting something totally wrong here, but if I imagine stuff right, the gentle roughness in 0,2mm print resolution should mean... well... nothing?
I would really like to read about your experience, though. I've never printed anything audio related before, so why not saving some filament instead of printing useless stuff?😛
Is totally smooth surface of a phase plug a must? I imagine that treble "happens" no matter what the position of the cone when playing an underlaying bass note, thereby treble reflecting off of the phase plug at random angles. I hope I'm not geting something totally wrong here, but if I imagine stuff right, the gentle roughness in 0,2mm print resolution should mean... well... nothing?
I would really like to read about your experience, though. I've never printed anything audio related before, so why not saving some filament instead of printing useless stuff?😛
In 3D Printing, the roughness is very visible and some degree of smoothness probably helps in redirecting the acoustic travel.
There isn't much in depth studies and research paper available, matter of fact from what I discovered the phase plug are used for compression tweeter like this picture below:
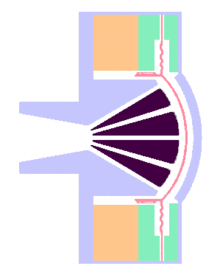
So to think how to actually applies this theory into cone based speakers, my guess would the phase plug probably need to be design to work on acoustic traveling path like the picture, which is along the voice coil former.
I will do up a simple design on my AutoCAD tonight to explain what I am trying to say here.
aczern,
Have you tried to load the AxiDriver software on a Win7 system, from the webpage it looks like this software hasn't been updated since Vista and that was a long time ago? It looks interesting for looking at some simple simulations, obviously they made the program simplistic for real reasons that I understand. I hate to have to go backwards to one old desktop I've kept running XP and the website doesn't even list that OS.
Have you tried to load the AxiDriver software on a Win7 system, from the webpage it looks like this software hasn't been updated since Vista and that was a long time ago? It looks interesting for looking at some simple simulations, obviously they made the program simplistic for real reasons that I understand. I hate to have to go backwards to one old desktop I've kept running XP and the website doesn't even list that OS.
- Home
- Loudspeakers
- Full Range
- Custom DIY 6.5" Fullrange Driver