Yes, there is a setting for the "honeycomb" (called 'infill' in 3D printing tools) which I think does tetrahedral patterns. There are a lot of interesting ones out there, "gyroid" is common (alternating pasta-like squiggle shapes) but "octet" is not far off from what I think you're describing and I've used it successfully in large prints.My thot was a chaotic foanm or a space filling structure based on tetrahedrons (nod to Bucky for that).
dave
That said, there's the stuff the 3D printer fills voids with, and then there are the voids you design into the shape that you can really fill with whatever. Lead shot, wood chips, broken pottery, expired mayonnaise, whatever seems suitable I guess... at the end of construction you seal two halves of the cabinet together by welding the plastic to itself, and with luck the material stays in there indefinitely.
Why is that? Sand is usually consider a good option. If you're printing, I'd try one with just sand. but don't compromise all your stiffness making room for it.I'm thinking the sand-filled layer will need to be thin-ish to get good damping,
Interesting. Is there a link that goes with it?This graph helps illustrate why you push resonances higher.
Interesting. Is there a link that goes with it?
It is a measure of the energy going into a box vrs frequency.
A 2nd order curve and a 4th order. The first 2 orders come straight out of the physics, the other 2 a bit more speculative. I concocted it whie reading thru a couple of the “ancient” tomes. Someday i might have to figure out exactly what each order is again. There might be a PhD paper that digs out all the math, does the tests, and see what real world looks like.
The basic take away is that the higher in frequency you can push the (potential) panel resonance up high enuff it is unlikely to get excited. A no-brainer in a woofer. Atkinson often implies similar when he is doing accelerometer tests.
dave
Exactly like ported and horn-loaded enclosures...Energy storage. Energy goes in, gets stored and then oozes out in a time-smeared mess.
dave
This triggers an old memory - I believe that a design was tried with a lightly skinned lump of very large void open-cell foam, but I do not remember what material was used for the blown foam. The Buckminsterfullerene-style approach is certainly within the scope of 3D printing and would probably work well for a small enclosure and also makes simpler coupling of the speaker chassis/magnet to the enclosure.My thot was a chaotic foam or a space filling structure based on tetrahedrons (nod to Bucky for that).
dave
I would assume that higher frequency resonances are therefore more receptive to conventional damping techniques.The basic take away is that the higher in frequency you can push the (potential) panel resonance up high enuff it is unlikely to get excited...
Is it the TL that doesn't collect as much energy due to the low output speed?Exactly like ported and horn-loaded enclosures...
BR has higher velocity in the pipe in comparison.
A transmission line is often essentially a 1/4 wave tube with damping, so there is still energy storage, but data is difficult to find. Suffice to say it possesses damping where BR and any horn-loaded arrangements typically do not. Settling times of large examples of these can run into hundreds of milliseconds.Is it the TL that doesn't collect as much energy due to the low output speed?
BR has higher velocity in the pipe in comparison.
Examples of 'extreme' subs with metal enclosures and metal cones. I have never seen anything like this!Of what?
Maybe that's why many people prefer OB because not so much energy is created. Allowing the diaphragm to move freely removes many "problems"?A transmission line is often essentially a 1/4 wave tube with damping, so there is still energy storage, but data is difficult to find. Suffice to say it possesses damping where BR and any horn-loaded arrangements typically do not. Settling times of large examples of these can run into hundreds of milliseconds.
Never actually used a metal box in a finished system, but we tested quite a few different drivers in mostly 12 ga industrial boxes that were in the recycle pile all the way up to 30+ ft^3/10 ga with thick angle iron bracing and if I were to build another HE/SQ system it would be made completely out of metal using the 'brightest' sounding drivers I could find and critically damped to 'taste'. One can always damp to 'taste', but never can add any full-range 'brilliance'.Examples of 'extreme' subs with metal enclosures and metal cones. I have never seen anything like this!
Guess being exposed to so many metal horns growing up with had a lasting impression on me as the huge damped wood WGs I ended up with just never sounded 'correct' to me even though I stiffened them up pretty good; maybe if I'd metal 'skinned' their insides..........
That kind of depends on how good of a job you do in showing it the door the first time around.and horn-loaded enclosures...
The box springyness is the same as the spider and surround springyness. If it didn't exist, there would be no fs, so OB has it too. OB also has more diffracted energy potential, and with a greater radiation space it is able to reach more surfaces for reflected energy.. but of course that's some of the intention.OB because not so much energy is created. Allowing the diaphragm to move freely removes many "problems"?
Very difficult to achieve subjectively I would say given all the variables. My preference is MDF purely on cost. Given a couple of diluted coats of PVA, I find it as good as anything.I would be so grateful if I could hear someone say the difference in sound between a box made of MDF and birch plywood? What do you get for the price difference? 4 times more cost.
I was referring to material properties rather than products. Metal cone subwoofers however are widely available -for e.g., Seas, Scan Speak, Dayton, Wavecor all produce aluminium cone subwoofer drivers. As for the boxes, a quick search on Google turned up a few; the old Krell LAT & Modulari series in essence used integrated / semi-integrated subwoofers for their floorstanders etc., while speakers like KEF's Muon use a similar integrated approach (stretching a point, but depends what you call an 'extreme' subwoofer, as that was not my phrase & no context was given. Either way -it's not unknown, but not especially common, largely, I assume, because most companies are geared up for working with woof-based products, and either tooling for metal types, or finding a subcontractor to do so is outside their usual range of experience, and likely to put the costs up. It was okay for Krell for e.g., since they were used it it & weren't geared up for wooden speaker production. AFAIK they didn't last though -it's a swine of a market to break into, and many commercial buyers tend to go with the logical (and many utterly nonsensical 😉 ) fallacies fed to them by the magazines.Examples of 'extreme' subs with metal enclosures and metal cones. I have never seen anything like this!
Last edited:
Yes, the higher in frequency, the less damping tends to be required to suppress a mode).I would assume that higher frequency resonances are therefore more receptive to conventional damping techniques.
One day I will try birch plywood. Right now it's way too expensive.Very difficult to achieve subjectively I would say given all the variables. My preference is MDF purely on cost. Given a couple of diluted coats of PVA, I find it as good as anything.
I'm a bit of an audiophile and I want the sound to be balanced. Maybe MDF suits me best, maybe not. I'll probably get the answer at some point.
Given that the speed of sound in wood is roughly 10x of that in air, I wonder if 'slowly bleeding out' comports with the physics? 😉 But given that I don't have a sense of how much loss there is from travel in the wood (maybe rather little) it might make sense in a way.
I am thinking of 3D printing enclosures designed with sealed voids inside the cabinet walls. These can be filled with whatever as they'll be more or less air/watertight.
My first thought was concrete. Easy enough and very stiff.
Then I thought that I'd like to add damping. So add another void inside the concrete one and fill it with sand. I'm thinking the sand-filled layer will need to be thin-ish to get good damping, but I have no sense of exact dimensions. Anyone know what makes sense there?
Then my brain got even stupider, and I started to think about adding a layer with actual liquids. I mean, why not? Aside from the numerous excellent reasons why not... it's technically possible.
So if you were to add a fluid layer to the inside of a speaker cabinet, what would work well, better than water?
I started to think that a non-newtonian fluid would do something acoustically relevant, but 1) I don't know of any except the thick cornstarch stuff, which will rot, and 2) I am not sure if the 'stiffening under impact' property is helpful or harmful when it comes to acoustics. Also, if it depends on suspended particulate, it will all settle over time and ruin the effect, if one exists.
Overall, fluids or no, I'm optimistic about the prospects of a multi-layered 3D printed enclosure. If you do 2 voids per cabinet, you get:
(from the inside out)
Plastic | Plastic/air honeycomb | plastic | sand | plastic | plastic/air honeycomb | plastic | concrete | plastic | plastic/air honeycomb | plastic
Plastic layers tend to be 1.5-3mm thick, (any thicker takes ages) the plastic-air honeycomb sections tend to be 90-60% air with very thin (0.3mm) walls of the honeycomb 'cells'. (even 75% air takes ages)
The construction method inherently adds a ton of layers and therefore boundary losses (is that the right term?). Concrete should provide the same stiffness as MDF at a fraction of the thickness, although you might as well let the cabinet get heavy if you're going to go to the trouble of 3D printing it.
What do y'all think?
Given that the speed of sound in wood is roughly 10x of that in air, I wonder if 'slowly bleeding out' comports with the physics? 😉 But given that I don't have a sense of how much loss there is from travel in the wood (maybe rather little) it might make sense in a way.
I am thinking of 3D printing enclosures designed with sealed voids inside the cabinet walls. These can be filled with whatever as they'll be more or less air/watertight.
My first thought was concrete. Easy enough and very stiff.
Then I thought that I'd like to add damping. So add another void inside the concrete one and fill it with sand. I'm thinking the sand-filled layer will need to be thin-ish to get good damping, but I have no sense of exact dimensions. Anyone know what makes sense there?
Then my brain got even stupider, and I started to think about adding a layer with actual liquids. I mean, why not? Aside from the numerous excellent reasons why not... it's technically possible.
So if you were to add a fluid layer to the inside of a speaker cabinet, what would work well, better than water?
I started to think that a non-newtonian fluid would do something acoustically relevant, but 1) I don't know of any except the thick cornstarch stuff, which will rot, and 2) I am not sure if the 'stiffening under impact' property is helpful or harmful when it comes to acoustics. Also, if it depends on suspended particulate, it will all settle over time and ruin the effect, if one exists.
Overall, fluids or no, I'm optimistic about the prospects of a multi-layered 3D printed enclosure. If you do 2 voids per cabinet, you get:
(from the inside out)
Plastic | Plastic/air honeycomb | plastic | sand | plastic | plastic/air honeycomb | plastic | concrete | plastic | plastic/air honeycomb | plastic
Plastic layers tend to be 1.5-3mm thick, (any thicker takes ages) the plastic-air honeycomb sections tend to be 90-60% air with very thin (0.3mm) walls of the honeycomb 'cells'. (even 75% air takes ages)
The construction method inherently adds a ton of layers and therefore boundary losses (is that the right term?). Concrete should provide the same stiffness as MDF at a fraction of the thickness, although you might as well let the cabinet get heavy if you're going to go to the trouble of 3D printing it.
What do y'all think?
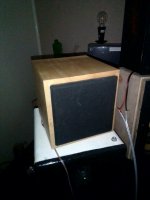
A few years ago, wooden boxes were the fashion in kitchens, so I got two biscuit boxes and put car full range drivers in them, the advantage of the biscuit boxes is that they have a plastic inner box (to make them more hygenic) so they have a double wall construction, helping to prevent the internal sound leaking out, if you were to 3D print speakers this would be easy to implement .The front baffles are held on by tension springs against a foam gasket, helping to damp them.
Attachments
Last edited by a moderator:
- Home
- Loudspeakers
- Full Range
- Cabinet material Measurement