I think the LS35a is not constrained, but single layer. Some similarities.
In any case, I'm sure it could. You wouldn't want to use material that is too thin, but then you wouldn't anyway.. but you can go thinner all the same.
One thing is that the more the material moves, the more damping occurs. Another thing is the higher frequencies are damped as well, without needing matrix style bracing.. because direct transmission to the walls from the basket is a problem.
In any case, I'm sure it could. You wouldn't want to use material that is too thin, but then you wouldn't anyway.. but you can go thinner all the same.
One thing is that the more the material moves, the more damping occurs. Another thing is the higher frequencies are damped as well, without needing matrix style bracing.. because direct transmission to the walls from the basket is a problem.
Last edited:
Coincidence Frequency. Stiff is good for low frequencies, dampened is needed for broadband/mid frequencies.I'm not disagreeing from that particular perspective, but it seems to be based on the assumption that a panel with high rigidity is a bad thing.
MDF bahves as wood and has not significant different damping behaviour.... MDF has very good dampening properties ...
Plexi (Acryl) glass has pretty good dampening characteristics but brings other problems.
I like to sandwich metal plates with elastic glue inside of a wooden cabinet - helps but is pretty heavy and a mess to produce.
Just use 40-50mm thick wood is a simple and good solution.
I've long thought that a speaker made from (clear) acrilic would look really cool, it would need a very neat crossover/cable layout though and an alternative to wadding to dampen internal sound reflections, I think those waterfall things had a slotted cup behind the drivers. Something like a small bookshelf.
Agreed, this is something a few of us have pointed out for years. MDF is fine for midrange and HF enclosures -not so great for LF. Can be done reasonably, albeit not an elegant solution in engineering terms.Coincidence Frequency. Stiff is good for low frequencies, dampened is needed for broadband/mid frequencies.
That being said -a decent material for LF is generally fine for midrange &c. purposes since with rising frequency there's relatively little energy to excite the high Q modes, and whatever is tends to be easily damped out. It's one reason CRS, aluminium &c. make good cabinets, if you're able to work with them (count me out on that one, but I'm the original gorilla 😉 ).
Last edited:
Going by fallible memory, the BBC's own early 'reference' LS3/5a boxes were 9mm, most later series production 12mm, apart from when Sterling, Falcon & probably a couple of others reintroduced the original thinner types with the screwed on rear as well as front baffle. TTBOMK though they're all lagged with car body / bitumen damping of differing thicknesses with location, then polyurethene foam (ditto) over the ensemble. Or the proper ones are anyway -goodness knows about the round million subsequent versions that either take or claim to take inspiration from it...I think the LS35a is not constrained, but single layer. Some similarities.
I said extreme units and i was thinking or Krell and Magico to name twoNow that, in my 40+ years in electroacoustics, I have never seen!
But you are right Not all top subwoofers come with metal cabinets Rel Velodyne etc. do not use metal for the cabinets
i think that car audio has surpassed hifi when extreme performance is the goalExamples?
Then just look at the most powerful woofers and their construction Woofers that can pass the 120VAC test Usually they have all metal diaphragms
If a concept is good for the extreme conditions it will be also fantastic for normal use
the BBC LS35a ... the Barbie's speaker ? my friend has a pair It is like listening to an old radio Put some heavy music on it and go around to find the cones in the house Nothing below 100Hz at decent levelWhen I was at school, I got hit on the head with a softball, I've been a soft dull thud ever since.
If we take the example of a flexible but damped enclosure of something like the BBC LS35a, is it possible that the flex could work like an aperiodic port, the movement may be tiny in comparison to the cone movement, but the surface area is so much larger, surely the tiny movement would be enough.
Then he added two very nice passive DIY subs ... now we were talking
Can you cover the outside of a box with a soft material? Know some use leather.
Sure. It is just a veneer.
dave
I would be so grateful if I could hear someone say the difference in sound between a box made of MDF and birch plywood? What do you get for the price difference? 4 times more cost.
Chris & i did 2 identical boxes FR125s ML-TLs, the plywood enclosure allowed for more expression of detail, DDR, the low level stuff on the MDF pair was not there, swamped by the ooze of stored energy slowly bleeding out of that box (last bit is how i rationize what was heard).
The LS3/5A was 9mm BB, purposely a bump just before it rolled off just below 100 Hz, and was very difficult to get to mate with woofers. One can do much better today with modern drivers… the last pair of LS3/5A i restored (someone made a real mess of the pair), i compared with a set of mFonken *(our last pair), the LS3/5A sounded very boxy.
dave
Empty box, relatively speaking? 'Thud' Vs very sharp 'thud' with 'thud' definition being a function of object's material's specs used (rounded side of a ball peen hammer). Non damped box w/Jensen LS15 = dull, too resonant to my then youthful ears.I would be so grateful if I could hear someone say the difference in sound between a box made of MDF and birch plywood? What do you get for the price difference? 4 times more cost.
The LS3/5a was designed as a nearfield [primarily vocal] broadcast monitor for vans and small regional studios.the BBC LS35a ... the Barbie's speaker ? my friend has a pair It is like listening to an old radio
Absolutely. It was not designed for that use and is not well suited to it at all.Put some heavy music on it and go around to find the cones in the house
Nothing below 100Hz at decent level
No. It wasn't designed to have (and doesn't).
That helps. Personally, I'd just chose a different speaker for home audio. The LS3/5 and LS3/5a were for the time excellent for the task they were designed to perform. And they're still very good at it, though driver technology has moved on, and IMO there's little reason to use them now other than nostalgia. Assuming the substitutes are equally well designed, to similar target curves of course.Then he added two very nice passive DIY subs ... now we were talking
It's basically a 'robbing Peter to pay Paul'/'chasing your tail' scenario, so depends on the app and in speaker design a generally good plan is to raise its stiffness above the ~500 Hz - down BW and 'push' its resonance to below ~500 Hz for the rest of the BW.Would not be better using just two materials
one that provides stiffness and the other that provides dampening ?
For multi-ways with sealed back mids/tweeters, then easiest to just make it sufficiently rigid or cheapest with the softest material construction practical, allowing the box to damp the generally cheaper higher Qt drivers; otherwise finding the mean of the (unsealed) driver's total BW as a starting point frequency to ~tune to for doing the fancy multiple layer hybrid panels that worked well enough for me, then added removable mass (often a potted fake/real plant) to further 'plant' 😉 it wherever 'it' was planned.
Given that the speed of sound in wood is roughly 10x of that in air, I wonder if 'slowly bleeding out' comports with the physics? 😉 But given that I don't have a sense of how much loss there is from travel in the wood (maybe rather little) it might make sense in a way.the ooze of stored energy slowly bleeding out of that box (last bit is how i rationize what was heard).
I am thinking of 3D printing enclosures designed with sealed voids inside the cabinet walls. These can be filled with whatever as they'll be more or less air/watertight.
My first thought was concrete. Easy enough and very stiff.
Then I thought that I'd like to add damping. So add another void inside the concrete one and fill it with sand. I'm thinking the sand-filled layer will need to be thin-ish to get good damping, but I have no sense of exact dimensions. Anyone know what makes sense there?
Then my brain got even stupider, and I started to think about adding a layer with actual liquids. I mean, why not? Aside from the numerous excellent reasons why not... it's technically possible.
So if you were to add a fluid layer to the inside of a speaker cabinet, what would work well, better than water?
I started to think that a non-newtonian fluid would do something acoustically relevant, but 1) I don't know of any except the thick cornstarch stuff, which will rot, and 2) I am not sure if the 'stiffening under impact' property is helpful or harmful when it comes to acoustics. Also, if it depends on suspended particulate, it will all settle over time and ruin the effect, if one exists.
Overall, fluids or no, I'm optimistic about the prospects of a multi-layered 3D printed enclosure. If you do 2 voids per cabinet, you get:
(from the inside out)
Plastic | Plastic/air honeycomb | plastic | sand | plastic | plastic/air honeycomb | plastic | concrete | plastic | plastic/air honeycomb | plastic
Plastic layers tend to be 1.5-3mm thick, (any thicker takes ages) the plastic-air honeycomb sections tend to be 90-60% air with very thin (0.3mm) walls of the honeycomb 'cells'. (even 75% air takes ages)
The construction method inherently adds a ton of layers and therefore boundary losses (is that the right term?). Concrete should provide the same stiffness as MDF at a fraction of the thickness, although you might as well let the cabinet get heavy if you're going to go to the trouble of 3D printing it.
What do y'all think?
This graph helps illustrate why you push resonances higher.
The shapes are right, the knee point is an educated guess.
dave
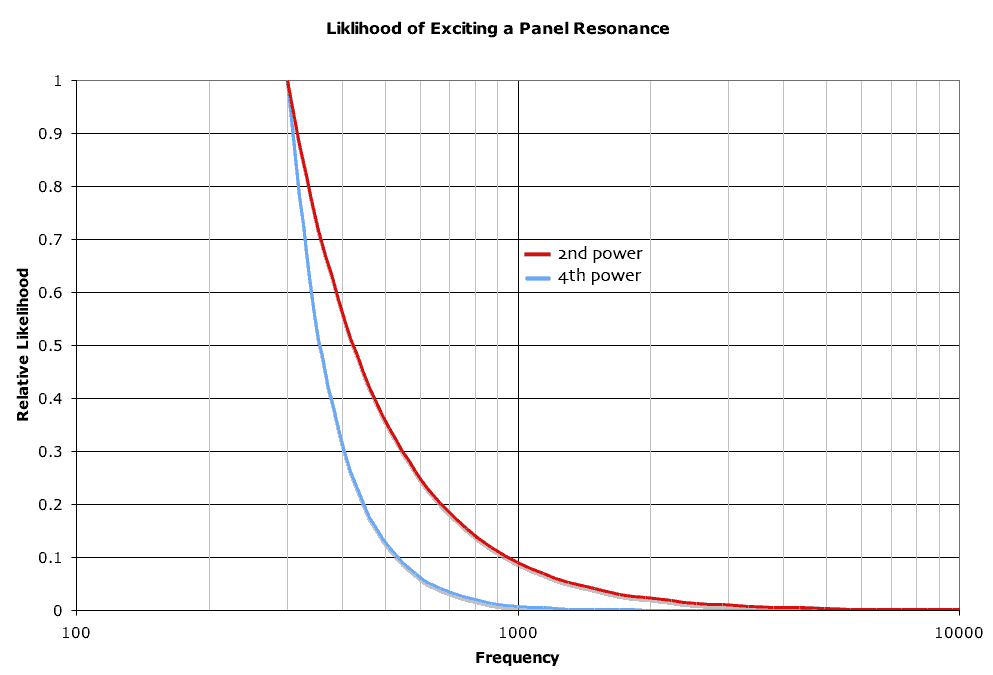
The shapes are right, the knee point is an educated guess.
dave
Energy storage. Energy goes in, gets stored and then oozes out in a time-smeared mess.I wonder if 'slowly bleeding out' comports with the physics?
dave
These can be filled with whatever
My thot was a chaotic foam or a space filling structure based on tetrahedrons (nod to Bucky for that).
dave
I think my lack of understanding is in how long the 'storage' might last. But subjectively (thinking about knocking on wood) it seems like it could be audible for as long as 50+ ms?Energy storage. Energy goes in, gets stored and then oozes out in a time-smeared mess.
dave
- Home
- Loudspeakers
- Full Range
- Cabinet material Measurement