Just want to let you know guys, Neat Flex is fantastic. I order a couple of pieces for a job and it’s a timesaver. Great stuff for DIYs that are looking for exotic forms.
http://www.neatconcepts.com/
🙂
http://www.neatconcepts.com/
🙂
What it is is "kerf" cut lumber. I do it whenever I need to go around corners with my clients jobs when they come up. But I do it on my table saw. Fortunately, my vacuum system picks up almost all the dawdust.
But is it worth buying? How much does the stuff cost?
But is it worth buying? How much does the stuff cost?
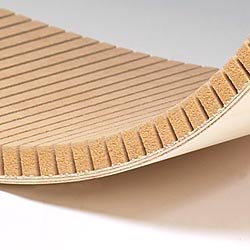
In US it cost about $120 for a 19mm 4x8. It’s a good deal for me because I am not looking to do 1000000 kerf cuts on the table saw. Uniformity of the bend is very good and as you noticed the outside is birch ply, which makes veneering a bliss.
John L said:
But is it worth buying? How much does the stuff cost?
R-Carpenter said:In US it cost about $120 for a 19mm 4x8. It’s a good deal for me because I am not looking to do 1000000 kerf cuts on the table saw. Uniformity of the bend is very good and as you noticed the outside is birch ply, which makes veneering a bliss.
The outside plywood layer is 5 really thin laminations, making the bend much smoother on the ouside. Avoids that "segmented" look you'll get with kerf cut regular plywood.
Saves a ship load of work on a big project too.
Nice find Roman.
Attachments
So,......what did you use to fill in the "kerf" cuts?
As it is, the wall is so thin that it will resonate easily. Remember, we are trying to acheive a sound dead enclosure here. How do you plan to deaden the walls?
As it is, the wall is so thin that it will resonate easily. Remember, we are trying to acheive a sound dead enclosure here. How do you plan to deaden the walls?
I don’t think you have to fill them in. A smooth surface will produce a reflection-standing wave. Kerf cuts may actually work as traps. In any event, you can sandwich this material to itself (cut side to cut side) and have your smooth surface. You could also sandwich 2 pieces with an extra piece of wiggleboard in between. Sandwiching different densities and thickness will quite down resonance of the walls significantly.
John L said:So,......what did you use to fill in the "kerf" cuts?
When I've used kerf cuts before (not for speakers), I ran beads of construction adhesive across and into the cuts to create points where it's solidly glued.
No need to completely fill IMO.
Like this:
Attachments
I used a mixture of sand and fibreglass resin to fill in the cuts but there are various other layers of materials inside that layer too. The outside of the cabinets is pretty dead but the outer layer of bendy MDF was really only designed to be something to attach the veneer to and to build up the other layers on the inside. the fibreglass resin also soaked into the MDF layer which I guess adds strength.
The pic shows the first layer of sand and resin.
The pic shows the first layer of sand and resin.
Attachments
quickshift said:I used a mixture of sand and fibreglass resin to fill in the cuts but there are various other layers of materials inside that layer too. The outside of the cabinets is pretty dead but the outer layer of bendy MDF was really only designed to be something to attach the veneer to and to build up the other layers on the inside. the fibreglass resin also soaked into the MDF layer which I guess adds strength.
The pic shows the first layer of sand and resin.
That's one good way to do it. Never thought of that. The way professional auto sound installers do it is to use Bondo type filler to fill in the kerf cuts. You mix up the compound and apply it inside the cracks while it is flat and then apply the curve. Once the curved side is attached, you can either scrape off the excess, or smooth it out, like with the sand and fiverglass above.
If you don't use a good filler the cabinet will resonate. I learned this watching a tape on how to construct contoured/rounded speaker cabinets for automotive application by professional installers.
John L said:
If you don't use a good filler the cabinet will resonate. I learned this watching a tape on how to construct contoured/rounded speaker cabinets for automotive application by professional installers.
I can't say that I agree.
Cabinets resonate regardless. Control of these resonances is the goal.
The structure of a curved panel when properly braced is very stiff and rigid, in every direction. Vastly stiffer than the same size, but thicker flat panel. Think about the inherent strength of an egg shell. Very thin, but strong due to the curved shape.
In a properly braced box with a curved panel, little will be gained by completely filling the kerf cuts.
But if it makes you feel better, do it. 🙂
MJL21193 said:
But if it makes you feel better, do it. 🙂
John, it does,.....and I shall. 😉
John L said:...I learned this watching a tape on how to construct contoured/rounded speaker cabinets for automotive application by professional installers.
Darn, what was I thinking?
How could I disagree with such a reliable source? 🙄
I am going to use these panels on my reference project that I haven’t even finished design yet. My plan is to use 2 kerf panels of different thickness with wiggleboard sandwiched in between. Perhaps I will add another kerf panel with the cuts facing to the inside of the speaker and working as difractors. This of cause dose not eliminate the need for bracing.
I think MDF is best to be glued with yellow glue and it’s not quite as messy as the epoxy but the point about using filler with the epoxy or polyester resign is very interesting. There’s a variety of powdered elastomers and rubbers available and testing different plastics just sparked a good deal of interest.

I think MDF is best to be glued with yellow glue and it’s not quite as messy as the epoxy but the point about using filler with the epoxy or polyester resign is very interesting. There’s a variety of powdered elastomers and rubbers available and testing different plastics just sparked a good deal of interest.

Have you tried Gorila glue? That is very strong. I use to use yellow glue, but this one is super strong. Could you place some links for powder rubbers and plastics please?
You would be surprised at the craftsmanship and level of detail serious highend car audio installers achieve.
MJL21193 said:
Darn, what was I thinking?
How could I disagree with such a reliable source? 🙄
winslow said:You would be surprised at the craftsmanship and level of detail serious highend car audio installers achieve.
I'm glad you said that. At least I'm not alone here when I state that the top of the line professional auto audio installers use T/S parameters and attempt to make only the best in quality. That tape I have shows the instructor to be top notch, and know as much about speaker buinding as the best out there.
- Status
- Not open for further replies.
- Home
- Loudspeakers
- Multi-Way
- Bendable plywood-mdf combination.