Finishing up a preamp project. One of the items on the punch list is that the Volume pot works fine on its own, but when the shaft from the pot located on the rear near the input jacks is run through a brass bushing on the front panel it no longer has enough torque to turn. The knob turns rather smoothly, but apparently the added drag is too much to overcome. Voltage applied to the motor is ~4.5v. Any suggestions? This is a genuine Alps pot from Mouser, real RK27 A taper motorized pots do not seem to be a thing. I have tried sanding, lube, etc. Suggestions?
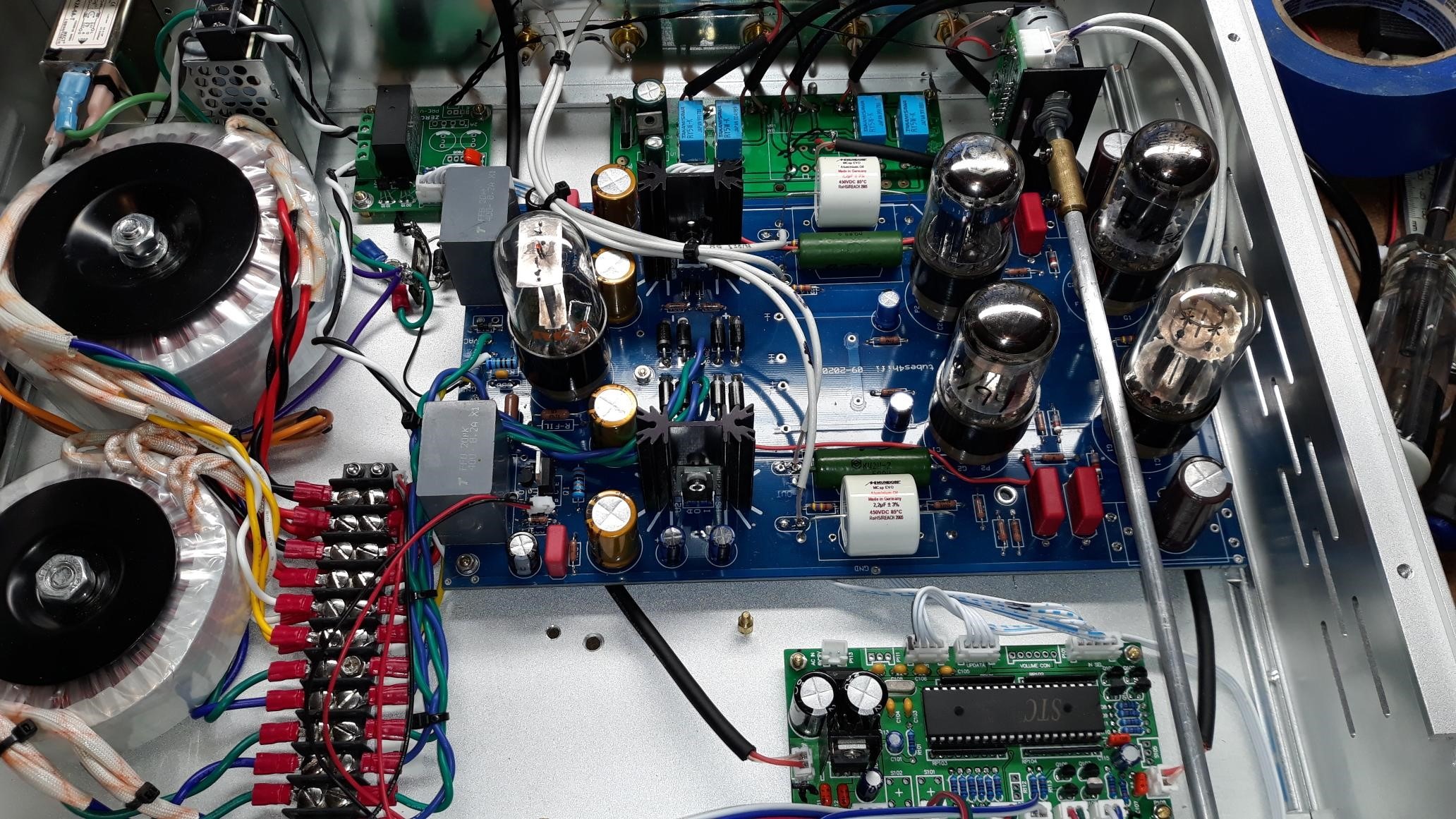
Electronic volume control, or a higher torque motor.
Try soaking the bush in oil at least overnight, then grease up and fit.
I use front axle grease these days, and 20W40 engine oil, sewing machine and front fork oil also work.
Try soaking the bush in oil at least overnight, then grease up and fit.
I use front axle grease these days, and 20W40 engine oil, sewing machine and front fork oil also work.
This is where I can not express what I mean in English but I will try. The connection of the axle is rigid/fixed and the axle is quite long. It is connected at both front panel side and potentiometer side so these should be 100% aligned which is nearly impossible in the real world. Any difference in lining (skewed?) and any deviation of the axle will have influence and will cause friction/higher resistance. Even lifting the chassis at 1 corner and different temp coefficients of the used materials will be of influence. So a flexible connection or one specially made for this purpose is the real solution. There were various old fashioned and mechanically impressive solutions for that but where to find these? The industry does not like these parts as they are only extra costs. The ones I found came from old hifi made in the seventies and old defective oscilloscopes complete with the bearings and the axles, all made to last and reusable. Brass bushings, stainless steel axles, beautiful couplers that resemble car transmission... That is why the answer is always "yes" when someone asks me if I would like to receive defective old equipment.
In chinglish the recent version is called elastic coupler. It is a cheap version of the old quality stuff but it works.
BTW make sure the axle goes through the front plate with a brass bearing. I do this for quite some time now and it became a sport to drill these holes at exactly the right spot 😀 Slight lubrication is mandatory in all cases but it is not the solution when stuff is out of lining. Please note that the beloved larger and extra heavy solid aluminium knobs have no place in a setup like yours. My compliments for the tidy build!
In chinglish the recent version is called elastic coupler. It is a cheap version of the old quality stuff but it works.
BTW make sure the axle goes through the front plate with a brass bearing. I do this for quite some time now and it became a sport to drill these holes at exactly the right spot 😀 Slight lubrication is mandatory in all cases but it is not the solution when stuff is out of lining. Please note that the beloved larger and extra heavy solid aluminium knobs have no place in a setup like yours. My compliments for the tidy build!
Attachments
Last edited:
That is going to a page that cannot be found...
What you could do is a miniature constant velocity joint, possibly from a model supplies source, that will give you a lot of leeway in alignment. it is a two yoke and slider assembly, the kind that drives the rear wheels of cars with independent suspension.
The front wheels need to steer, that joint is called a Rzeppa joint...
NTN Americas | Automotive & Industrial Constant Velocity Joints (CVJs)
Drivetrains & Driveshafts - RC Car Action
Constant-velocity joint - Wikipedia
What you could do is a miniature constant velocity joint, possibly from a model supplies source, that will give you a lot of leeway in alignment. it is a two yoke and slider assembly, the kind that drives the rear wheels of cars with independent suspension.
The front wheels need to steer, that joint is called a Rzeppa joint...
NTN Americas | Automotive & Industrial Constant Velocity Joints (CVJs)
Drivetrains & Driveshafts - RC Car Action
Constant-velocity joint - Wikipedia
Last edited:
The page can not be found and sometimes it can be found. Strange. Anyway here is the datasheet:
https://www.megatron.de/fileadmin/user_upload/Datenblaetter/Zubehoer/DS_MAK_MSK_M495_ESM_en.pdf
https://www.megatron.de/fileadmin/user_upload/Datenblaetter/Zubehoer/DS_MAK_MSK_M495_ESM_en.pdf
Thank you, that look promising. That pot has very little torque. Maybe increasing the 4.5v to 12v will help 😉
If the motor is specified to require 12 V and you're running it at 4.5 V you're certainly setting yourself up for trouble.
Those motorized pots have a clutch that will slip when the pot reaches the end stop. If the clutch is slipping but the shaft is not turning and the pot is not against the end stop, I'd add one of those shaft couplers.
If running the motor at the specified voltage results in too fast pot rotation, I would pulse-width modulate the motor drive voltage. Just run the PWM outside the audible frequency range and you'll be fine.
Tom
Those motorized pots have a clutch that will slip when the pot reaches the end stop. If the clutch is slipping but the shaft is not turning and the pot is not against the end stop, I'd add one of those shaft couplers.
If running the motor at the specified voltage results in too fast pot rotation, I would pulse-width modulate the motor drive voltage. Just run the PWM outside the audible frequency range and you'll be fine.
Tom
The potentiometer probably has a “Slip coupler”
depending on silicon grease. Ah I see tomchr already replied.
depending on silicon grease. Ah I see tomchr already replied.
If you can, just shift the thing to the front panel, run the connections with flat cable, no joint issues.
But running a 12 v motor at 4.5, then complaining that it lacks torque, that should have been checked first.
You can also find a motor that runs slower.
Best is use a electronic volume control, long term no wear problems, and you can possibly use it with a remote, but I think that is what the motorized pot is for.
But running a 12 v motor at 4.5, then complaining that it lacks torque, that should have been checked first.
You can also find a motor that runs slower.
Best is use a electronic volume control, long term no wear problems, and you can possibly use it with a remote, but I think that is what the motorized pot is for.
The page "can not be found" if it detects you got there from another site (here). If you copy and paste the URL (watch for "diyaudio" on the end) it works OK. This rejection of outside links is occasionally useful (stops some content-stealing) but not in this case (it's good free publicity).
1/4" fuel hose. You may not need clamps, at least to try. Not as precise as the sawed-up metal but how exact is a volume knob?
1/4" fuel hose. You may not need clamps, at least to try. Not as precise as the sawed-up metal but how exact is a volume knob?
Last edited:
You can even use an old speedometer cable...or a braided hose, the kind used in pneumatic tools.
There is no limit in cheap and that's OK but some take pride in how things are executed. As said, I gathered a small lot of such quality stuff and it is a joy to look at and it has a kind of quality feel. The analog challenge can be to keep connections short and close to the input connectors, use very good relays and a hardware (stepped) volume control as most semiconductor volume IC's are less good. When I finally bought a Khozmo years ago I was impressed by the high quality both mechanically and sonically. All history and in preservation as I use FDA nowadays.
Last edited:
Cardan shaft is another name for something like a rear wheel drive shaft...
Apart from vehicles, common in milling machines and other mechanisms.
Measure and then search for one.
Only thing is you need a baby sized one.
Apart from vehicles, common in milling machines and other mechanisms.
Measure and then search for one.
Only thing is you need a baby sized one.
Found this affordable one for 6 mm axles (bought one to try it out).
Uxcell Nieuwste Draaibare Kruiskoppeling 4 6mm Boring Rvs Stuuras U Gezamenlijke Koppeling Koppeling Connector 23 x 11mm|Shaft Couplings| - AliExpress
Uxcell Nieuwste Draaibare Kruiskoppeling 4 6mm Boring Rvs Stuuras U Gezamenlijke Koppeling Koppeling Connector 23 x 11mm|Shaft Couplings| - AliExpress
Last edited:
I got this (mostly) working. I got a 6mm flexible coupler as linked by Jean Paul from Amazon. It helped a little. I then sanded the bushing and shaft with 600 grit, and used silicone lube. Still one sticky spot but it is outside the usable range. I will look for other solutions but I want to listen to it for a while.... I got these. Since I have 2 I will put the other one at the knob end of the shaft and report back...https://smile.amazon.com/dp/B07YDG25JX
For extra smoothness. go buy finer paper, up to 2000 grit, or least use 800 / 1000 grit, sand in different directions, (criss cross directions), it helps a lot. Clean off abrasive residue before fitting.
The motor now takes the load?
Good you have a solution.
The motor now takes the load?
Good you have a solution.
Last edited:
1/4" shaft in bushings--- put the shaft in your power drill and spin it in the bushing a while.
I have polished snug-fit telescopic brass tubing to spin freely for a tone-arm this way. Severe drag suggests toothpaste as an abrasive.
I have polished snug-fit telescopic brass tubing to spin freely for a tone-arm this way. Severe drag suggests toothpaste as an abrasive.
Severe drag suggests toothpaste as an abrasive.
Heh. That's a pretty neat idea. Alternatively: Car polish.
Tom
I used toothpaste as the final polishing stage, it works, and it was a substitute for Simichrome polish, which is now $30 or more here for about 50 grams.
You can use valve lapping paste, too, for slightly rougher finish, if you need to remove more metal than what tooth paste can, and abrasive car polish, the kind used after painting, would be in between.
Better work the shaft, easier, and the adapter may be case hardened or otherwise heat treated.
You can use valve lapping paste, too, for slightly rougher finish, if you need to remove more metal than what tooth paste can, and abrasive car polish, the kind used after painting, would be in between.
Better work the shaft, easier, and the adapter may be case hardened or otherwise heat treated.
- Home
- Source & Line
- Analog Line Level
- Alps RK168 rotational torque