I had been running with the 2mm EPDM belts for a week or so. Having done so many belt swaps I was in danger of loosing track of the differences I was hearing.
Up to this point my favourite belts had been the 1.5mm nitrile to which I had been directly comparing all the others. The main strength of the nitrile was dynamics with my listening notes mentioning that dynamics were "soft" with almost all the other belts. The 2mm EPDM seemed better in all aspects with the exception of dynamics. Having spent time with the EPDM I was starting to worry that it too lacked dynamics. Switching back to the 1.5mm nitrile eradicated these fears. The EPDM was as good at dynamics, just not better. Because the EPDM was better in all other areas the dynamics only seemed to suffered as it was the only aspect that didn't markedly improve.
This highlights the importance of living with a change for a while before making a decision. Short A-B comparisons, especially blind, just don't reveal the real differences.
The 2mm EPDM is my new reference belt....
Until the next post.
Niffy
Up to this point my favourite belts had been the 1.5mm nitrile to which I had been directly comparing all the others. The main strength of the nitrile was dynamics with my listening notes mentioning that dynamics were "soft" with almost all the other belts. The 2mm EPDM seemed better in all aspects with the exception of dynamics. Having spent time with the EPDM I was starting to worry that it too lacked dynamics. Switching back to the 1.5mm nitrile eradicated these fears. The EPDM was as good at dynamics, just not better. Because the EPDM was better in all other areas the dynamics only seemed to suffered as it was the only aspect that didn't markedly improve.
This highlights the importance of living with a change for a while before making a decision. Short A-B comparisons, especially blind, just don't reveal the real differences.
The 2mm EPDM is my new reference belt....
Until the next post.
Niffy
I have also finally gotten around to measuring and testing the polyester thread.
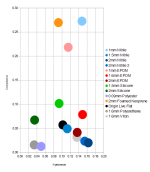
The thread was more difficult to measure than any of the others mainly due to it being almost Invisible except under direct strong light. The thread is not actually 0.04mm as advertised, it is 0.004". It is slightly thinner than this at 0.09mm.
It is by far the least compliant of any of the materials tested so far, and is shown on the chart in lilac. It also has one of the lowest hysteresis'. Being so thin it is extremely flexible.
Due to low compliance and my drive system the belts needed to be made to tight tolerances. After a couple of failed attempts I worked out the technique and got down to a fraction of a millimetre accuracy. A task made all the more difficult by the current heatwave. Sweaty hands did not help.
I think that I might have just found my new favourite belt material.
My benchmark 1.5mm nitrile scored a total 30 in my marking scheme. The 2mm EPDM bested it with a score of 34.
The polyester just blew that out of the water with a score of 39.
It is very clean and precise, super transparent. It has stunning dynamics, much better than even the 1.5mm nitrile.
Smooth and open with pin point imaging.
It's not quite as warm or as rich as the 2mm EPDM. More neutral? Or a little hard?
Surprisingly I can hear the knots as they passed over the pulley/idlers, but only from a couple of inches away. I cannot hear any hint of them through the speakers.
I'm going to have to live with the polyester monofilament for a while, as I did before, then swap back to the EPDM.
It would appear that low compliance is good for dynamics, imaging and detail.
Higher hysteresis seems to be good for tonal richness and warmth.
Greater flexibility is good for smoothness and openness.
I'm currently listening to a record by a very talented local artist, Ellie Ford. It's one of my favourite albums that I've listened to dozens of times. Detail, dynamics, separation, imaging all better than I've heard before.
It's remarkable how much difference there has been between the different belts.
The total amount of improvement wrought by upgrading my motor, controller, power supply and now belts has been quite a revelation.
Niffy
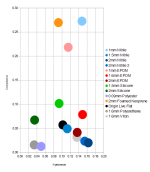
The thread was more difficult to measure than any of the others mainly due to it being almost Invisible except under direct strong light. The thread is not actually 0.04mm as advertised, it is 0.004". It is slightly thinner than this at 0.09mm.
It is by far the least compliant of any of the materials tested so far, and is shown on the chart in lilac. It also has one of the lowest hysteresis'. Being so thin it is extremely flexible.
Due to low compliance and my drive system the belts needed to be made to tight tolerances. After a couple of failed attempts I worked out the technique and got down to a fraction of a millimetre accuracy. A task made all the more difficult by the current heatwave. Sweaty hands did not help.
I think that I might have just found my new favourite belt material.
My benchmark 1.5mm nitrile scored a total 30 in my marking scheme. The 2mm EPDM bested it with a score of 34.
The polyester just blew that out of the water with a score of 39.
It is very clean and precise, super transparent. It has stunning dynamics, much better than even the 1.5mm nitrile.
Smooth and open with pin point imaging.
It's not quite as warm or as rich as the 2mm EPDM. More neutral? Or a little hard?
Surprisingly I can hear the knots as they passed over the pulley/idlers, but only from a couple of inches away. I cannot hear any hint of them through the speakers.
I'm going to have to live with the polyester monofilament for a while, as I did before, then swap back to the EPDM.
It would appear that low compliance is good for dynamics, imaging and detail.
Higher hysteresis seems to be good for tonal richness and warmth.
Greater flexibility is good for smoothness and openness.
I'm currently listening to a record by a very talented local artist, Ellie Ford. It's one of my favourite albums that I've listened to dozens of times. Detail, dynamics, separation, imaging all better than I've heard before.
It's remarkable how much difference there has been between the different belts.
The total amount of improvement wrought by upgrading my motor, controller, power supply and now belts has been quite a revelation.
Niffy
THE BIG DISCLAIMER
All of the conclusions I've come to regarding belt materials are specific to my deck and may not necessarily transfer to others.
My bearing and drive system were designed much more as a single unit than as separate components, as is more common. With the bearing being sleeveless the runout of the platter is controlled by the belts. Lower compliance belts will control runout better than high compliance. This will have some influence on sound quality but I do not think that it is significant. Even with high compliance belts runout was very well controlled. With a sleeved bearing the compliance of the belt will have no effect on runout.
The best way of quantifying bearing friction is to look at the amount of energy that the bearing dissipates. With a more conventional design of bearing the sleeve is responsible for 95-98% of the energy dissipated. By removing the sleeve my bearing dissipates less than 2mW. By comparison I tested a Cirkus bearing of a new Linn Sondek at a friendly dealer. It dissipated between 200-250mW. My old systemdec dissipated around 100mW.
The difference in the tension before and after the drive pulley will be much lower with my deck than with virtually any other, air-bearing not withstanding. The ideal mechanical properties of belts could very well be very different depending on the energy dissipation of the bearing.
In general the thicker belts of the same material sounded better. The best two rubber materials were nitrile and EPDM. At 1mm and 1.5mm nitrile sounded better. At 2mm the EPDM took the lead. This is very likely due to the nitrile being less flexible. If a larger diameter pulley was used the 2mm nitrile would likely have kept it's lead. Again, a flat belt will probably be a better option in most cases.
The polyester bucks this trend due to its much lower compliance and small diameter. If it were 1.5mm in diameter it would be way too stiff. Perhaps a similar material to the polyester but with higher hysteresis would be better than the polyester itself.
For now I'm going to live with the polyester for a while then swap back to the 2mm EPDM to make sure that the improvements I have heard are truly improvements. Is the greater warmth of the EPDM a colouration? Is the polyester more neutral?
Niffy
All of the conclusions I've come to regarding belt materials are specific to my deck and may not necessarily transfer to others.
My bearing and drive system were designed much more as a single unit than as separate components, as is more common. With the bearing being sleeveless the runout of the platter is controlled by the belts. Lower compliance belts will control runout better than high compliance. This will have some influence on sound quality but I do not think that it is significant. Even with high compliance belts runout was very well controlled. With a sleeved bearing the compliance of the belt will have no effect on runout.
The best way of quantifying bearing friction is to look at the amount of energy that the bearing dissipates. With a more conventional design of bearing the sleeve is responsible for 95-98% of the energy dissipated. By removing the sleeve my bearing dissipates less than 2mW. By comparison I tested a Cirkus bearing of a new Linn Sondek at a friendly dealer. It dissipated between 200-250mW. My old systemdec dissipated around 100mW.
The difference in the tension before and after the drive pulley will be much lower with my deck than with virtually any other, air-bearing not withstanding. The ideal mechanical properties of belts could very well be very different depending on the energy dissipation of the bearing.
In general the thicker belts of the same material sounded better. The best two rubber materials were nitrile and EPDM. At 1mm and 1.5mm nitrile sounded better. At 2mm the EPDM took the lead. This is very likely due to the nitrile being less flexible. If a larger diameter pulley was used the 2mm nitrile would likely have kept it's lead. Again, a flat belt will probably be a better option in most cases.
The polyester bucks this trend due to its much lower compliance and small diameter. If it were 1.5mm in diameter it would be way too stiff. Perhaps a similar material to the polyester but with higher hysteresis would be better than the polyester itself.
For now I'm going to live with the polyester for a while then swap back to the 2mm EPDM to make sure that the improvements I have heard are truly improvements. Is the greater warmth of the EPDM a colouration? Is the polyester more neutral?
Niffy
Hi Niffy,I have also finally gotten around to measuring and testing the polyester thread.
View attachment 1184884
...
It is very clean and precise, super transparent. It has stunning dynamics, much better than even the 1.5mm nitrile.
Smooth and open with pin point imaging.
It's not quite as warm or as rich as the 2mm EPDM. More neutral? Or a little hard?
Surprisingly I can hear the knots as they passed over the pulley/idlers, but only from a couple of inches away. I cannot hear any hint of them through the speakers.
I'm going to have to live with the polyester monofilament for a while, as I did before, then swap back to the EPDM.
It would appear that low compliance is good for dynamics, imaging and detail.
Higher hysteresis seems to be good for tonal richness and warmth.
Greater flexibility is good for smoothness and openness.
....
The total amount of improvement wrought by upgrading my motor, controller, power supply and now belts has been quite a revelation.
Niffy
you deserve everyone's congratulations for your commitment, persistence and scientific approach on finding the best belt material. To the best of my knowledge I am not aware of any similar effort in hifi. Well done!!
On a personal note, I am glad that you preferred the polyester thread for two reasons:
a) it confirms what I've heard, i.e. the improvement of the thread vs. the Origin Live belt I had on my Roksan Xerxes.
b) it frees me from new adventures with other belt materials in quest of the 'best'.
What has really impressed me with the polyester thread is that it's extremely thin, yet it provides the necessary grip to turn the platter without increasing belt tension.
I concur your findings about neutrality, lack of coloration, speed. The polyester thread had the least effect on the sound, if any. It's as if the platter were turned by an 'invisible' belt without any material properties.
If I may interpret the material properties in general, I think that higher compliance (stretchiness) and hysteresis provide coloration to the sound, which may be perceived as "tonal richness and warmth".
We are now expecting your impressions once you go back to the 2mm EPDM belt. I have a feeling of what you will find, but I am not saying anything, so that I do not bias the discussion.
Kudos for the great work, Niffy.
P.S. I am looking forward that Maxon finishes their investigation of my noisy motor, so that I can soon enjoy my improved Roksan Xerxes again.
I forgot to mention this bit.What has really impressed me with the polyester thread is that it's extremely thin, yet it provides the necessary grip to turn the platter without increasing belt tension.
I was a little concerned that, due to the surface of the thread being so smooth, the belt might slip. I made the lengths of the belts so that there would be a 0.75N side force on the motor, the same as with the other belts. There doesn't appear to any slip at all. This does confirm that contact area is not important.
Another observation is that the platter takes about 5 minutes to come to a halt after the power is switched off, not much less than with no belts attached. Normally the platter would stop within around a minute.
This would suggest that with the other belt materials the majority of the energy dissipated by the drive and bearing system is due to belt flexing.
As the polyester thread is very thin and has low hysteresis the losses with this belt is very low.
These losses would mainly result in the heating of the belts. I don't know how this effects sound quality but my intuition says that lower energy dissipation in the bearing and drive system is beneficial.
Niffy
Lower energy dissipation means lower energy requirements for the system to function and maintain its normal operation.
The polyester thread is a great belt material. And beyond its sound quality it's also so easy and inexpensive to use. Right?
I am sure you can confirm how much effort it took you to create a polyester thread belt vs. all other materials.
The polyester thread is a great belt material. And beyond its sound quality it's also so easy and inexpensive to use. Right?
I am sure you can confirm how much effort it took you to create a polyester thread belt vs. all other materials.
Furthermore, the very low mass of the polyester thread belt, as well as its flexibility and low tension may further reduce any potential vibration transfer from the motor to the platter, which may contribute to the clean, uncolored sound.
Once I got the hang of tieing the knots it was quite easy. The main issue is that due to the very low compliance the belts have to be made to very high tolerance. A millimetre out could cause a half Newton of difference in motor loading. I think I got the accuracy to around 1/4 mm.I am sure you can confirm how much effort it took you to create a polyester thread belt vs. all other materials.
The most difficult (and expensive) belts to make were the silicone which is kinda ironic as the 1.5mm silicone was the worst sounding.
Niffy
Well, I am glad it has worked out well for you with the polyester thread. For me, I do not think I will ever go back to any other material, unless the thread does not work for the intended application. I am also considering of abandoning my rim drive test, since the sound quality with the polyester thread is very high in my opinion.
Maybe you would also be willing to share your method of creating polyester belts with such accuracy. That would be interesting and helpful. Thanks.
Maybe you would also be willing to share your method of creating polyester belts with such accuracy. That would be interesting and helpful. Thanks.
I basically used the same method as used in the video you linked. I used pins of 0.8mm diameter at both ends, rather than a drawing pin at one end. I calculated the exact distance the pins would have to be apart and then used my vernier caliper to exactly position the pins to 0.1mm accuracy. A big block of balsa was essential, luckily I have one.
Due to its low compliance the polyester thread doesn't stretch much as each of my measuring weights are added. The length of thread I used was about 700mm long and this only stretched by around 10mm in total. The ruler I was using is 750mm so I was limited to this length. I believe that the compliance I calculated is pretty accurate. The resolution might be a bit low for getting a good accuracy of the hysteresis, the loop avenging less than a millimetre across. I'm going to have a go at making a much longer measure, hopefully around 3m in height. This should improve resolution.
I'm also going to try some monofilament nylon. I don't think that I can go any lower in compliance as this would require even higher accuracy of belt manufacture. Nylon is about 20% more stretchier than polyester so if I use a filament 10% greater in diameter I should get about the same compliance. The flexibility will be slightly lower but still very flexible. Hopefully the nylon will have very different hysteresis so I can confirm if higher hysteresis is beneficial as I currently suspect.
Niffy
I'm also going to try some monofilament nylon. I don't think that I can go any lower in compliance as this would require even higher accuracy of belt manufacture. Nylon is about 20% more stretchier than polyester so if I use a filament 10% greater in diameter I should get about the same compliance. The flexibility will be slightly lower but still very flexible. Hopefully the nylon will have very different hysteresis so I can confirm if higher hysteresis is beneficial as I currently suspect.
Niffy
I've just received note from Maxon, who said that my RE-max motor was on spec, with all bearings, etc. working fine, as expected. The slight noise that was audible was nothing extraordinary. Furthermore, they did not have any such model on stock, so that they could see if that was quieter.
In any case, there is nothing they can do from their side. So, they will send the motor back to me. Let's hope it becomes quieter over time, as it is used. I have to admit though that it has greatly improved since the very beginning, when I initially thought that it was damaged.
I will keep you informed.
In any case, there is nothing they can do from their side. So, they will send the motor back to me. Let's hope it becomes quieter over time, as it is used. I have to admit though that it has greatly improved since the very beginning, when I initially thought that it was damaged.
I will keep you informed.
I hope that it is just a case of needing to be run in.
My Maxon was notably quieter than the Premotec it replaced right from the start. The Premotec itself quietened over the years. The Maxon seems to have continued to quietened as well. With the polyester thread belt I could hear the knot passing over the pulley from a short distance but could not hear the motor itself. Hopefully your motor will run in to a similar extent.
My Maxon was notably quieter than the Premotec it replaced right from the start. The Premotec itself quietened over the years. The Maxon seems to have continued to quietened as well. With the polyester thread belt I could hear the knot passing over the pulley from a short distance but could not hear the motor itself. Hopefully your motor will run in to a similar extent.
Niffy,
indeed the Maxon has quietened substantially since the fist time I put it in use, after say 50-70 hours or so. Sometimes it's completely quiet, better than my Premotec, which seems to have some cogging, while the Maxon runs more smoothly. Sometimes, however, the Maxon still produces some bearing noise although that does not seem to translate to vibrations.
I'll monitor it and hope it improves over time, sooner than later.
But even if it remains like it is now, it definitely sounds better than my Premotec. Combined with the polyester thread and the Origin Live controller upgrade with the bigger Nichicon cap, the overall sound quality has greatly improved. Many thanks to Niffy and Sondeknz, as well as to anybody else, who has contributed with their feedback.
indeed the Maxon has quietened substantially since the fist time I put it in use, after say 50-70 hours or so. Sometimes it's completely quiet, better than my Premotec, which seems to have some cogging, while the Maxon runs more smoothly. Sometimes, however, the Maxon still produces some bearing noise although that does not seem to translate to vibrations.
I'll monitor it and hope it improves over time, sooner than later.
But even if it remains like it is now, it definitely sounds better than my Premotec. Combined with the polyester thread and the Origin Live controller upgrade with the bigger Nichicon cap, the overall sound quality has greatly improved. Many thanks to Niffy and Sondeknz, as well as to anybody else, who has contributed with their feedback.
I've remeasured the polyester monofilament thread using a strand 4 times the length of that used in my initial measurement, ~2.7m against ~0.7m. This should increase the resolution and accuracy by a similar degree.
As expected the fresh data shows that compliance is very similar to that previously measured. It is slightly lower, the belts would need to be 0.2mm longer to hit my 0.75N motor side force target. As this is at about the accuracy limit of my ability to make belts I not going worry about it.
My main reason for remeasuring was that the hysteresis figure previously calculated would be quite vague. The new data suggests that it is actually about 40% lower, quite a big difference.
I have also received some 0.11mm diameter nylon monofilament thread. Based on the Young's modulus of polyester and nylon I had expected this thread to have a similar compliance to the 0.09mm polyester. Unfortunately it's compliance was much higher, about 5 times higher. As hoped it's hysteresis was also higher. The measured compliance and hysteresis are very similar to those of the 1.5mm nitrile. The big difference is that the nylon is much more flexible. I might make a set of belts up anyway and directly compare to the 1.5mm nitrile just to see if they sound similar.
I may also order some thicker nylon monofilament, -0.25mm, as this will hopefully have a similar compliance to the polyester.
For now I'm just going to enjoy the sounds I'm getting with the polyester.
Niffy
As expected the fresh data shows that compliance is very similar to that previously measured. It is slightly lower, the belts would need to be 0.2mm longer to hit my 0.75N motor side force target. As this is at about the accuracy limit of my ability to make belts I not going worry about it.
My main reason for remeasuring was that the hysteresis figure previously calculated would be quite vague. The new data suggests that it is actually about 40% lower, quite a big difference.
I have also received some 0.11mm diameter nylon monofilament thread. Based on the Young's modulus of polyester and nylon I had expected this thread to have a similar compliance to the 0.09mm polyester. Unfortunately it's compliance was much higher, about 5 times higher. As hoped it's hysteresis was also higher. The measured compliance and hysteresis are very similar to those of the 1.5mm nitrile. The big difference is that the nylon is much more flexible. I might make a set of belts up anyway and directly compare to the 1.5mm nitrile just to see if they sound similar.
I may also order some thicker nylon monofilament, -0.25mm, as this will hopefully have a similar compliance to the polyester.
For now I'm just going to enjoy the sounds I'm getting with the polyester.
Niffy
Niffy,
have you had the chance to change back to one of the other belts, so that you compare the polyester thread with the 'competition'? Does your initial positive impression about the polyester thread still hold?
Cheers,
Panos
have you had the chance to change back to one of the other belts, so that you compare the polyester thread with the 'competition'? Does your initial positive impression about the polyester thread still hold?
Cheers,
Panos
I haven't swapped back yet. I'm going to live with the polyester for a bit longer before I do.
I wanted to get more accurate measurements of the polyester. I wasn't expecting the nylon to be an improvement, Tom Fletcher had already done the work finding the best thread.
I wanted to get more accurate measurements of the polyester. I wasn't expecting the nylon to be an improvement, Tom Fletcher had already done the work finding the best thread.
I hope motor noise continues to decrease once you get it refitted.
I'm very interested to know your opinion on how the retipped Cadenza compares to the original shibata stylus. The Cadenza Black is an outstanding cartridge, almost certainly the best in its price range.
I'm very interested to know your opinion on how the retipped Cadenza compares to the original shibata stylus. The Cadenza Black is an outstanding cartridge, almost certainly the best in its price range.
- Home
- Source & Line
- Analogue Source
- 12VDC motor for the turntable. Power, torque, PCB questions