Is the waveguide unbaffled? That will make the edge treatment critical and not actually give the best results. A baffle makes things much better.
Reminds me of doing FEA in the old days. I never liked all that tedious meshing - we didn't have auto meshing then.
Reminds me of doing FEA in the old days. I never liked all that tedious meshing - we didn't have auto meshing then.
Try the second one then 🙂... Had a quick look at the round OSWG and it works like a charm.
As Fredrik says it's in an infinite baffle. Otherwise it would be a disaster as you say. It would be possible to run it that way however (been there), it would take much more computation time as the back side would also need to be modeled - it can't do sheets of zero thickness. I will definitely add an option of a box as an alternative to IB condition. Yeah, Gmsh makes the modeling a piece of cake.Is the waveguide unbaffled? That will make the edge treatment critical and not actually give the best results. A baffle makes things much better.
Attachments
Try the second one then 🙂
Works perfectly, and the response looks really good! Better than the round OSWG which still show some irregularity in the 0-20 degree area.
Round mabat- OSWG curves:
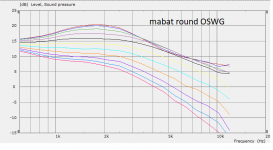
Rectangular mabat design (ATH-15)
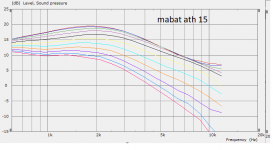
My 10" device which is not a OSWG, but more of a OSWG throat merged to a lage radius from throat to mouth:
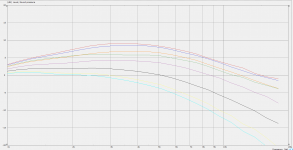
One ABEC specific question; I see that you are using a curved/spherical interface at the horn mouth.
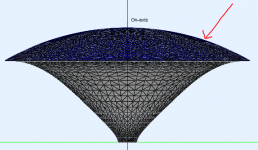
Why is that? I have so far only used a flat mesh for the interface:
Last edited:
Your solution looks also very smooth Fredrik. When I try to squeeze my horn to 10" (256 x 236 mm actually) I get to these results (polars are 0 - 75; step 7.5°) -
More on the interface later...
More on the interface later...
Attachments
Nice! Your design seems to have better control over directivity at the lower end of the passband.
Will your tool allow for altering the throat diameter and throat entry angle?
Will your tool allow for altering the throat diameter and throat entry angle?
Last edited:
For sure, otherwise it would be useless. This is an excerpt from the definition script (the horn just shown), all can be changed:
It seems to me that in case of a rectangular shape the available mouth area (for a fixed enclosure width) can actually be utilized better. Just my impression.
Code:
ThroatDiameter = 25.4 ; [mm]
ThroatAngle = 0 ; [deg]
Coverage_Horizontal = 95 ; [deg]
Coverage_Vertical = 90 ; [deg]
Depth = 90 ; [mm]
Depth.ConicSectionPart = 0.5 ; 0.5
Shape = raw2rect ; raw | raw2rect
Shape.FixedPart = 0.2 ; 0.2
Shape.CornerRadius = 38.0 ; [mm]
SEExp = 2.3 ; superellipse exponent
Termination = baffle ; baffle | free-air
;Termination.Angle = 90.0 ; (for baffle; default = 90 deg)
It seems to me that in case of a rectangular shape the available mouth area (for a fixed enclosure width) can actually be utilized better. Just my impression.
Link https://www.diyaudio.com/forums/multi-way/103872-geddes-waveguides-283.html#post1851004Large termination like in K402. Do you remember Gorge Soong work?
here are the basic STLs that would fit into Jacek's machine, you can look.
(online STL viewer: Free online STL viewer)
Marcel,
what is xover frequency for this WG? And what driver?
I don't know the particular driver. I got throat size, entry angle and the size limit so I came with this OSWG which is about 15.3" (6.3" depth) and "ATH" which is 17.3" x 15" (7"). Since the throat is for 1.4" I would expect the xover around 700 Hz without issues. Maybe a bit lower with the ATH. Depends on the driver and the woofer used. The request was also for 80x80° coverage which may complicate things a bit. Personally I would make it wider.
Last edited:
It seems to me that in case of a rectangular shape the available mouth area (for a fixed enclosure width) can actually be utilized better. Just my impression.
Just to be difficult, I don't see how the mouth area increase is an advantage. It's not like a direct radiator where cone area is a big factor. With a waveguide as the area gets larger, the velocity drops keeping the total volume velocity constant regardless of shape. The only effect of the mouth shape is on the diffraction in the far field, which will be different, but in my experience not necessarily any better.
A foam plug, which IMHO is a bigger asset than mouth diffraction, would be very hard to make in the squarish shape that you show.
Just my 2 cents.
It may be the language. Let me rephrase: it seems to me that for a given baffle width a somewhat better beamwidth control can be achieved with a squarish shape (as Fredrik also noticed, but that may be due to something else). When I think about it I don't really see the reason why, but it's the impression I get from the simulations I do. No big deal.
Regarding the foam plug, it can be allways milled on a CNC. But I really woudn't insist on the foam. Why are you so convinced it is that important?
Regarding the foam plug, it can be allways milled on a CNC. But I really woudn't insist on the foam. Why are you so convinced it is that important?
Regarding the foam plug, it can be allways milled on a CNC. But I really woudn't insist on the foam. Why are you so convinced it is that important?
I agree that there does not seem to be any analytical reason that shape has much effect.
Anything can be done with enough money - I don't own a CNC mill! And it most likely would not work very well on the foam since it has to be cut with a hot wire.
I believe in the foam because of hundreds of happy customers and my own experience. It makes a big difference.
That's a very good question, I have asked myself this same thing many times.
I can measure the difference and it does what I would want it to do and that is it compacts the impulse response, (this data was shown some 15 years ago) decreasing any holdover ringing that often occurs with horns and the like.
Subjectively it is much harder to quantify as anyone who knows me knows that cursory listening tests are seldom valid. But I have listened to many systems with and without the foam and the ones without it always sound harsher - which is exactly what I would expect from what I want the foam to do and what I have measured it does.
But doing subjectively valid tests are not within my capabilities to do. So it's just an opinion, but one given based on 50+ years of experience and some data.
I can measure the difference and it does what I would want it to do and that is it compacts the impulse response, (this data was shown some 15 years ago) decreasing any holdover ringing that often occurs with horns and the like.
Subjectively it is much harder to quantify as anyone who knows me knows that cursory listening tests are seldom valid. But I have listened to many systems with and without the foam and the ones without it always sound harsher - which is exactly what I would expect from what I want the foam to do and what I have measured it does.
But doing subjectively valid tests are not within my capabilities to do. So it's just an opinion, but one given based on 50+ years of experience and some data.
Thank you Earl, this is the honesty we all love you for 🙂
BTW, I was assured by a friend who actually does the CNC milling that the foam is no problem. It only needs a higher cutting speed. And I think these machines are getting affordable, I know maybe of five guys who have it in my surrounding.
BTW, I was assured by a friend who actually does the CNC milling that the foam is no problem. It only needs a higher cutting speed. And I think these machines are getting affordable, I know maybe of five guys who have it in my surrounding.
OK, gentlemen, as I promised - here it is: https://www.diyaudio.com/forums/multi-way/338806-acoustic-horn-design-easy-ath4.html#post5813825
I'm sorry for polluting this thread, as you actually can't buy my horns. You would have to build them.
I'm sorry for polluting this thread, as you actually can't buy my horns. You would have to build them.
I'm sorry for polluting this thread, as you actually can't buy my horns. You would have to build them.
This is both awesome and appropriate given that the topic has been deviated from already. Thank you for your work here!
Thank you Earl, this is the honesty we all love you for 🙂
BTW, I was assured by a friend who actually does the CNC milling that the foam is no problem. It only needs a higher cutting speed. And I think these machines are getting affordable, I know maybe of five guys who have it in my surrounding.
I simply cut mine with a scissors:
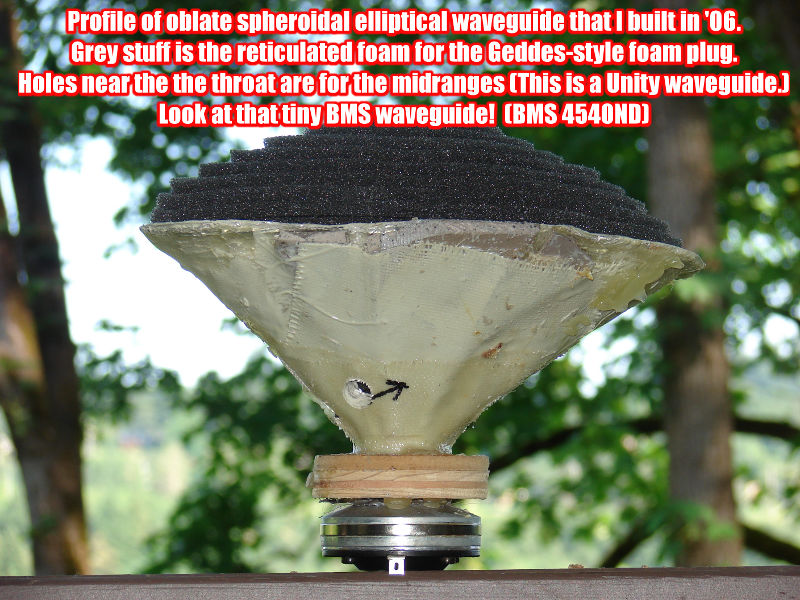
I suppose you could glue the layers together, but I didn't bother. I wrapped the whole thing in spandex nylon and the compression held it all together.
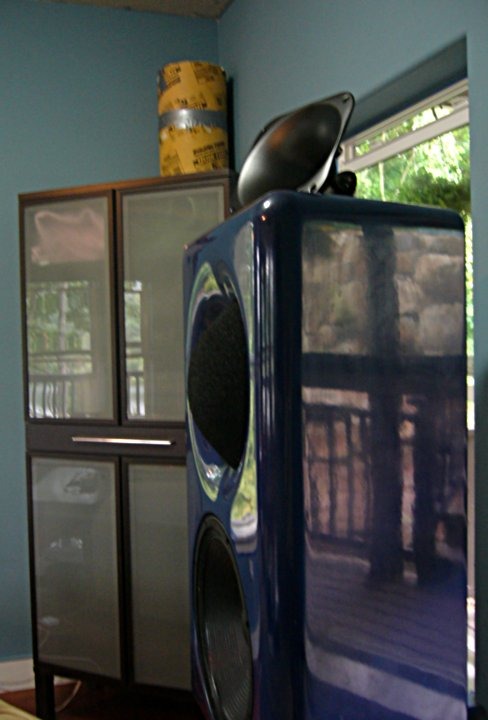
For comparison's sake, here are my Summas, which had a solid plug milled using a hot wire by Geddes.
Yes, I have used a hot wire in the past. I'm not completely new to the foam plugs. I wouldn't do it again. 🙂
BTW, does anyone cut to the exact waveguide shape (which is in fact possible with a straight wire), or just a cone?
BTW, does anyone cut to the exact waveguide shape (which is in fact possible with a straight wire), or just a cone?
- Home
- Loudspeakers
- Multi-Way
- 1.4" or 2" throat large constant directivity horns you can actually buy!