I have read most of the threads on this subject so although no new ground will probably be broken here, here is my start at a DIY bearing methods.
3 pieces I have or I have ordered.
View attachment 1333040
0.375 Ream
The drill rod is precision ground, -0.0002 to 0 tolerance.
I will attempt to bore and ream the bronze rod on my 80 year old Southbend lathe.
Will attempt to polish with my hillbilly wet fine grit sandpaper on a foam mandrel. I will try that first before investing in a hone.
This will just determine if I can machine a tight tolerance smooth running bearing in the radial direction.
Do I have any hope of success?
I have built a few TT bearings now including modifying the mighty Technics SP10mk2. My first inverted bearing SP10 motor used 12mm Silver Steel rod polished with diamond paste to 0.5 microns. M2 will do a good job too. For the journals I used Vesconite HiLube with a very tight running clearance once the journal has run for a 10-20 mins it becomes extremely quiet even though there is no oil film. I did use a thin film of oil initially.
I tested this bearing with a contact microphone on the bottom of the housing against an LP12 Cirkus bearing for noise and the Vesconite was significantly quieter even though the LP12 was hydrodynamic.
Here is a photo of the modified Technics SP10mk2 motor. The journal is BS-1407 Silver Steel with a 5mm SI3N4 ball. You can see the bottom journal sleeve in the rotor. The thrust pad is also Vesconite Hilube.
As you have the capability to bore in situ this is the way I would recommend to achieve a great TT bearing. Because it's a non clearance running fit with less than 0.0004" clearance the platter rotates with increased stability.
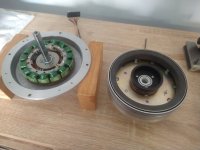
As you have the capability to bore in situ this is the way I would recommend to achieve a great TT bearing. Because it's a non clearance running fit with less than 0.0004" clearance the platter rotates with increased stability.
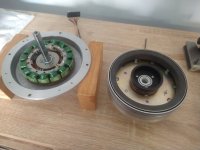
I used 15mmOD 7mmID bushing rod. Machine the OD 0.07mm interference fit then bore the ID in situ with a PCD boring bar.
Hi,
attached is a pdf sketch of an inverted bearing idea which I took from the bearing of the SAC Girati Grande.
I like the idea of the combined use of the bearing ball for the vertical and the horizontal bearing.
Might also make manufacturing easier.
What Do You think?
jauu
Calvin
attached is a pdf sketch of an inverted bearing idea which I took from the bearing of the SAC Girati Grande.
I like the idea of the combined use of the bearing ball for the vertical and the horizontal bearing.
Might also make manufacturing easier.
What Do You think?
jauu
Calvin
Attachments
Last edited:
Pierre Lurne used this bearing arrangement in the early 80's for the Audiomecca turntables. I tried it for the SP10 motor but ended up using upper and lower sleeves. Due to the close internal tolerances I deemed it too risky. Pierre used Acetal for the lower sleeve ring.
Or, you could just take an lp12 bearing and arrange mag lev to remove the contact noise from the thrust pad. Easily done with a decent ring magnet and a disc filled with small disc magnet inserts as the opposing element.
I have considered maglev and have already picked out ring magnets to try. I was going to try that as an experiment to see which sounds better. As a mechanical engineer I prefer the concept of an exact contrained solution where the position of the platter relative to the tonearm base is determinate. But I acknowledge that ideal can't be achieved even with a fixed z-platter with real world records.
Could you elaborate more: tutorials how to do it, videos, B. O. M. and where to buy it, I own and old LP12, thanks.Or, you could just take an lp12 bearing and arrange mag lev to remove the contact noise from the thrust pad. Easily done with a decent ring magnet and a disc filled with small disc magnet inserts as the opposing element.
A friend has one on his, though it's not in an lp12 chassis, it's in a laminated multilayer carbon nomex sandwich, but uses pre circus and linn subplatter. He's the guy who designed the original Tranquility for Tiger Paw.
https://www.tiger-paw.com/tranquility
As its a commercial device I'm not at liberty to give away the specifics of parts, sizes and magnet strength.
https://www.tiger-paw.com/tranquility
As its a commercial device I'm not at liberty to give away the specifics of parts, sizes and magnet strength.
Here is a site (US) that supplies rare-earth ring magnets.
https://www.kjmagnetics.com/products.asp?cat=16&pg=7
In the process of selecting a magnet you can get the technical information, specifically repel force versus distance to determine 'hover' distance as a function of your platter weight. Example below.
https://www.kjmagnetics.com/largergraph.asp?CI=4&pName=RX8C4
https://www.kjmagnetics.com/products.asp?cat=16&pg=7
In the process of selecting a magnet you can get the technical information, specifically repel force versus distance to determine 'hover' distance as a function of your platter weight. Example below.
https://www.kjmagnetics.com/largergraph.asp?CI=4&pName=RX8C4
My diy bearing lifts my platter with approx 5kg easily. I did experiment with some ring magnets and the current implementation uses stacked 40mm x 25mm 5mm thick, N42.
I had to experiment a bit to find the perfect gap
I had to experiment a bit to find the perfect gap
I experimented with mag lift as my platter is 12kg but there was too much stray magnetic field on top of a 70mm thick platter, and the magnetic field is rotating. The magnets would need to be a long way below to reduce the field to negligible levels. I settled on Vesconite for the thrust pad, it is very quiet in the bearing housing and totally inaudible in the platter with a stethoscope.
Air bearings are great but the good ones are extremely expensive and IMO there must be a mechanical rotation point full floating is a no-no for me. The platter will bounce microscopically. The full floating platter and air pressure will form a spring mass damper with a resonant frequency.
Air bearings are great but the good ones are extremely expensive and IMO there must be a mechanical rotation point full floating is a no-no for me. The platter will bounce microscopically. The full floating platter and air pressure will form a spring mass damper with a resonant frequency.
Update. Home bore trial. I drilled and reamed a 0.375" hole in the bronze rod stock. The 0.375 precision drill rod did not fit. I removed material with a 240grit hone until the drill rod fit. Polished by hand up to 600 grit and got a nice running fit with lube. I estimate the total clearance is less that 0.0005. Felt good by hand but that is subjective. Next step is to polish bore to 1500-2000 grit. The precision drill guide bushing should be arriving today to see how that goes.
Ebay has 8mm Superlube bushings available relatively inexpensively. Would those be suitable instead of HiLube?I used 15mmOD 7mmID bushing rod. Machine the OD 0.07mm interference fit then bore the ID in situ with a PCD boring bar.
https://www.ebay.com/itm/2839863324...uid=XQOE7h6cQoG&widget_ver=artemis&media=COPY
Update 2: Received the drill guide in post #10 arrive and its a perfect fit with the drill rod. I mean perfect, no slop. Fit must be within a few 10ths clearance.
Vesconite Superlube is pink HiLube is white. I was talking to Vesco plastics last week about Superlube and if it was a better product for a TT bearing. The consensus of the conversation was to continue to use HiLube because it machines smoother. I'm building 3x SP10mk2 based TT's and I will be using HiLube for the sleeves and thrust pad. Bearing uses upper and lower bushes that are 12mm long spaced approx 100mm apart. The further apart the bushes the more stable is the journal.
In my first prototype inverted bearing I used 12mm linear shaft which worked well. This is a photo of the first iteration.
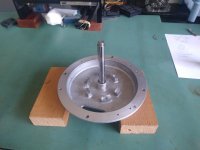
In my first prototype inverted bearing I used 12mm linear shaft which worked well. This is a photo of the first iteration.
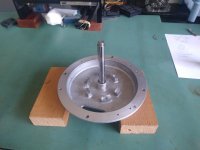
Ebay has 8mm Superlube bushings available relatively inexpensively. Would those be suitable instead of HiLube?
https://www.ebay.com/itm/2839863324...uid=XQOE7h6cQoG&widget_ver=artemis&media=COPY
When I bore the ID I use the journal shaft and match the shaft to the journal. It's time consuming but I get a better fit. I also set the compound to 5.7deg this gives 10:1 depth of cut. So 0.001" on the dial is 0.0001" depth of cut.
- Home
- Source & Line
- Analogue Source
- Another DIY turntable bearing thread