I am at the point of re-foiling my Audiostatic's ES 300's. Right now I am hesitating between using "ER audio coating" or 'Statclear" (Edson Electronics). Can anybody advise me about the use of one of these coatings? (stability, how to apply best) Thanks in advance.
I used the ER coating for my latest Audiostatic rebuild and I can recommend it. Very easy application, does "wet" the film very well, I used a foam brush (was included in the shipment). I diluted it according to Rob's instructions to get higher surface resistance. Didn't measure the surface resistance afterwards but the panels charge in a few seconds so it should be in the right ballpark.
This rebuild was only two years ago so I can't tell how long it lasts. So far it had been very stable.
I choose ER because it has a very good reputation and the rebuild is quite time consuming, so better get it right the first time. I found several sources online that expressed doubts about long term stability of the various antistatic products. So I went for what was in my opinion the safest option. But I have no experience with Statclear.
This rebuild was only two years ago so I can't tell how long it lasts. So far it had been very stable.
I choose ER because it has a very good reputation and the rebuild is quite time consuming, so better get it right the first time. I found several sources online that expressed doubts about long term stability of the various antistatic products. So I went for what was in my opinion the safest option. But I have no experience with Statclear.
I've not used either coating you referenced so I'm no help for a recommendation.
I'm just curious to know how the stators are held together in your speaker. If they are mechanically fastened together, rather than bonded, that would be the best scenario.
There is no functional reason why stators would have to be bonded together. They need only be constrained together in intimate contact, to play.
Assuming the stators are not bonded together but merely constrained together with screws or a molding, it would then be easy to dis-assemble the panel, leaving the diaphragm intact. In this case, you could just pick a coating and don't worry about it would be an easy fix if it went bad-- dis-assemble the panel, wipe the old coating off with acetone and then re-coat the diaphragm again.
It's a pet peeve of mine that many ESL manufacturer's bond the stators together so that it's impossible to separate the stators without damaging the diaphragm. Just wondering how Audiostatic does it...
I'm just curious to know how the stators are held together in your speaker. If they are mechanically fastened together, rather than bonded, that would be the best scenario.
There is no functional reason why stators would have to be bonded together. They need only be constrained together in intimate contact, to play.
Assuming the stators are not bonded together but merely constrained together with screws or a molding, it would then be easy to dis-assemble the panel, leaving the diaphragm intact. In this case, you could just pick a coating and don't worry about it would be an easy fix if it went bad-- dis-assemble the panel, wipe the old coating off with acetone and then re-coat the diaphragm again.
It's a pet peeve of mine that many ESL manufacturer's bond the stators together so that it's impossible to separate the stators without damaging the diaphragm. Just wondering how Audiostatic does it...
Last edited:
They glue everything. They used several types of glue over the years, some are very easy to disassemble, some are very difficult.
After disassembly I drill holes so I can use M3 screws (nylon) to keep the stators together. Makes the next rebuild so much easier. Still the membrame has to be glued to one stator. My experience with sticky tape isn't good, it looses tension over time.
But in general the construction of the Audiostatic panels is excellent. I think it's one of the easiest commercial ESL to rebuild.
After disassembly I drill holes so I can use M3 screws (nylon) to keep the stators together. Makes the next rebuild so much easier. Still the membrame has to be glued to one stator. My experience with sticky tape isn't good, it looses tension over time.
But in general the construction of the Audiostatic panels is excellent. I think it's one of the easiest commercial ESL to rebuild.
In Holland Martin Jan Dijkstra also member of diY provided me with his own coating. i used it for my own Audiostatics. This was about two years ago and I’m still very content with the result. About bonding the panels i‘m using spring clips to hold them together. These are the same clips Quad are using in the esl63.
Last time I contacted MartinJan about his coating, he told me he no longer provides it. But maybe he will join in here himself.
It was indeed a good coating, lasted over 10 years on my Audiostatics and my Quads are still up and running after 15 years. But the Audiostatics are daily used while the Quads have been in storage most of the time
It was indeed a good coating, lasted over 10 years on my Audiostatics and my Quads are still up and running after 15 years. But the Audiostatics are daily used while the Quads have been in storage most of the time
Because of the 'open' and unprotected structure, Audiostatics are sensitive to accumulation of dirt and particles. These may form conductive discharge pathways over time. My advice is to add a switch and only power them when listening to music. This way it should last even longer than 10 years. A switch was not included in most of the audiostatics because they needed long time to charge up.
There is airmail, there is PayPal so distance is not a problem.
No address nearby? No, not as far as I know.
You can search for a good coating solution yourself by trying out several candidates.
I think you must be very glad there is still something readily available to be purchased.
No address nearby? No, not as far as I know.
You can search for a good coating solution yourself by trying out several candidates.
I think you must be very glad there is still something readily available to be purchased.
I agree. There is no other source of a ready to use proven reliable coating that I am aware of. In fact a lot of companies in Europe that offer rebuilds get their coatings from ER as well. Shipping to the Netherlands took about three weeks by standard mail in my case.
If the ER coating is not an option for you, then you might want to consider Stat Clear A50 from Edison Electronics. I haven't personally tried it but I've read positive reports from other ESL builders that it works quite well, and the manufacturer states that it's a permanent ESD coating.
The elegance of an even coating application on the mylar film might be something to strive for. If there is a perfectionist's hearth beating inside your chest. It's not a must however, because Quad hasn't, and theirs panels are functional despite quite irregular spreading of the coating on theirs membranes. Anyway. So for ally you perfectionists out there, may I re-iterate my very positive experience with melamine foam as an applicator media?
While reworking my Quad63s, I purchased several different sponge materials for testing the results on some samples first, before getting serious. With very different results. By far the very best were sponges made of melamine foam. Melamine foam is available as these white "magic" sponges, e.g. from 3M or others. Handling and working with this material is just marvellous: You can very easily cut melamine foam with a sharp knive to any form or shape you want. And when dipping the sponge into the coating liquid (in my case the one from ER Audio), it soaks with a fair amount of liquid, but never drops. And then, with each single stroke on the Mylar, the applyied layer of liquid is just perfect. It leaves an even, very thin film of coating liquid on the mylar. The resulting surface R showed mainly values around between 400M ... 600M which is in the perfect range. Try it out!
By the way, I wonder why the brush industry has no off-the-shelf melamine-foam equipped brushes. Such brushes might also more generally be perfect for any varnishing work with aqueous solutions on non-absorbing surfaces.
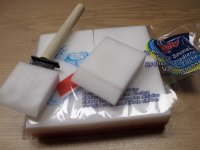
While reworking my Quad63s, I purchased several different sponge materials for testing the results on some samples first, before getting serious. With very different results. By far the very best were sponges made of melamine foam. Melamine foam is available as these white "magic" sponges, e.g. from 3M or others. Handling and working with this material is just marvellous: You can very easily cut melamine foam with a sharp knive to any form or shape you want. And when dipping the sponge into the coating liquid (in my case the one from ER Audio), it soaks with a fair amount of liquid, but never drops. And then, with each single stroke on the Mylar, the applyied layer of liquid is just perfect. It leaves an even, very thin film of coating liquid on the mylar. The resulting surface R showed mainly values around between 400M ... 600M which is in the perfect range. Try it out!
By the way, I wonder why the brush industry has no off-the-shelf melamine-foam equipped brushes. Such brushes might also more generally be perfect for any varnishing work with aqueous solutions on non-absorbing surfaces.
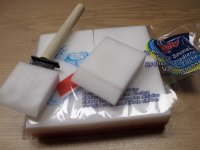
Last edited:
If there are companies that use this (which I very very very strongly doubt), they have not read the usage agreement on the website.I agree. There is no other source of a ready to use proven reliable coating that I am aware of. In fact a lot of companies in Europe that offer rebuilds get their coatings from ER as well. Shipping to the Netherlands took about three weeks by standard mail in my case.
What is your source that you can claim this?
The following kit is supplied for home use only and may not be used for commercial gain unless authorised by ER Audio in writing. All photographs, drawings and text contained in the kits are subject to copyright laws and may not be reproduced or copied in part or in full without written permission from E R Audio.
Acceptance of any kit implies acceptance of these terms
There are several options that have been claimed to work great in some group, forum or website over and over again.If the ER coating is not an option for you, then you might want to consider Stat Clear A50 from Edison Electronics. I haven't personally tried it but I've read positive reports from other ESL builders that it works quite well, and the manufacturer states that it's a permanent ESD coating.
On the top of the list without a doubt is Licron Crystal, but there is also
Antistatik 100
Scothkote
Statclear A50
Piccomat
Staticide
ACL
MG Chamicals 844
Hand soap
Water shower (very popular among ML owners)
And of course Graphit33 with or without additives
etc. etc.
Most of them claim 10^7 - 10^9, but most are lower when applied
"Quality" is most of the time based on the measured resistivity per square (measured with 2 coins and a standard volt meter)
Of these coatings Statclear A50 is the only one that is water based AFAIK, but I could be (very) wrong. As ER Audio ships round the globe it must be water based too or very mild chemical wise.
Since 9/`11 there are very strict and strong rules about shipping chemicals and the costs for shipping are very high. You must supply CAS numbers, have trained staff etc. Compressed air cans is even impossible, that is why Licron Crystal was unavailable for a long time in Europe.
Other coating suppliers in the past like @MJ Dijkstra, Reromanus, Audio4, MT Audio and maybe more I don't know or forgot to mention, all had the same rule: "not for commercial use".
Last edited:
Melamine foam:The elegance of an even coating application on the mylar film might be something to strive for. If there is a perfectionist's hearth beating inside your chest. It's not a must however, because Quad hasn't, and theirs panels are functional despite quite irregular spreading of the coating on theirs membranes. Anyway. So for ally you perfectionists out there, may I re-iterate my very positive experience with melamine foam as an applicator media?
While reworking my Quad63s, I purchased several different sponge materials for testing the results on some samples first, before getting serious. With very different results. By far the very best were sponges made of melamine foam. Melamine foam is available as these white "magic" sponges, e.g. from 3M or others. Handling and working with this material is just marvellous: You can very easily cut melamine foam with a sharp knive to any form or shape you want. And when dipping the sponge into the coating liquid (in my case the one from ER Audio), it soaks with a fair amount of liquid, but never drops. And then, with each single stroke on the Mylar, the applyied layer of liquid is just perfect. It leaves an even, very thin film of coating liquid on the mylar. The resulting surface R showed mainly values around between 400M ... 600M which is in the perfect range. Try it out!
By the way, I wonder why the brush industry has no off-the-shelf melamine-foam equipped brushes. Such brushes might also more generally be perfect for any varnishing work with aqueous solutions on non-absorbing surfaces.
View attachment 1253133
Properties
The open-cell foam is microporous and its polymeric substance is very hard, so that when used for cleaning it works like extremely fine sandpaper, getting into tiny grooves and pits in the object being cleaned. On a larger scale, the material feels soft because the reticulated foam bubbles interconnect. Its structure is a 3D network of very hard strands.
Very likely you damaged the Mylar on a microscopic level.
Some producers exclude commercial usage of their coating. I did this too. First it is to protect yourself against claims of clumsy refurbishers. Some of them just want to make money while they dont know what they are doing. They may lack any form of measurement equipment and will just replace the mylar expecting this will solve all problems. Some wont even change the Mylar at all and brush coating right on the old coating. When the speaker fails after a certain time those 'repair' men can go blaming the supplier of coating and even threatening him to pay for their "losses". This happened to me unfortunately. I could prove by measurements that the coating was working flawlessy as well that they ignored the instruction guide on critical parts. But still the conversations were nasty and for me not worth the few bucks I can earn with the coating. Second is the fact that making coating out from the basic chemical materials is very time consuming in my case. On such small scale it is inefficiënt. Limited shelf life of components as well as the finished product wont help either For commercial use it is too cheap.
At last I recognize those foam pads. I received one from Arend-Jan before his fatal accident. I think it works great I am not afraid to make 'scratches'. If that would occure those artefacts would be filled up with coating anyway.
At last I recognize those foam pads. I received one from Arend-Jan before his fatal accident. I think it works great I am not afraid to make 'scratches'. If that would occure those artefacts would be filled up with coating anyway.
- Home
- Loudspeakers
- Planars & Exotics
- ESL Diaphragm coating