Hahahah, I see you've got the itch. Like almost everyone here -)))
I would definitely like to try the silicone belt that you are using on your LP12. Where can I find such? Are they already made or do I have to get a certain length and then cut and glue accordingly?
Thanks
P.
P.S. Once I've built the Lenco plinth (out or corian and birch ply), with a lot of cutting and drilling, everything else seems not that difficult. I am afraid that my Xerxes plinth will undergo some drilling and cutting, too. And eventually, I may build a brand new plinth for the Xerxes, too.
I would definitely like to try the silicone belt that you are using on your LP12. Where can I find such? Are they already made or do I have to get a certain length and then cut and glue accordingly?
Thanks
P.
P.S. Once I've built the Lenco plinth (out or corian and birch ply), with a lot of cutting and drilling, everything else seems not that difficult. I am afraid that my Xerxes plinth will undergo some drilling and cutting, too. And eventually, I may build a brand new plinth for the Xerxes, too.
Thanks Niffy.
As an aside, this weekend it was a public holiday in China - International Labour Day - so we went “Glamping” (Glamour Camping, where everything is laid-on, including an air-cond tent) for an overnight treat.
I powered-down our new LHY AUDIO LINEAR POWER SUPPLY. We were only away from home for about 30-hours - enough time for the LHY LPS to get stone cold.
Sure enough, upon our return home today, I fired-up the LP12 - gave the system 15-mins to warm-up - and sat down for a serious listen.
In short, it sounded like rubbish - like I have a broken cartridge - just like it sounded when the LHY LPS was brand-new.
[It’s definitely not our tube amp, which comes on-song every morning, in just 5-mins…)
So, a bit more intel around what makes for good LP play-back.
It seems traditional toroidal LPS PSUs need considerable time to warm-up, settle-down, to drive a DC motor at its very best.
Has anyone else experienced this phenomena with PSUs?
As an aside, this weekend it was a public holiday in China - International Labour Day - so we went “Glamping” (Glamour Camping, where everything is laid-on, including an air-cond tent) for an overnight treat.
I powered-down our new LHY AUDIO LINEAR POWER SUPPLY. We were only away from home for about 30-hours - enough time for the LHY LPS to get stone cold.
Sure enough, upon our return home today, I fired-up the LP12 - gave the system 15-mins to warm-up - and sat down for a serious listen.
In short, it sounded like rubbish - like I have a broken cartridge - just like it sounded when the LHY LPS was brand-new.
[It’s definitely not our tube amp, which comes on-song every morning, in just 5-mins…)
So, a bit more intel around what makes for good LP play-back.
It seems traditional toroidal LPS PSUs need considerable time to warm-up, settle-down, to drive a DC motor at its very best.
Has anyone else experienced this phenomena with PSUs?
Hi Panos,Continuing my previous post, perhaps a way to reduce the forces on the platter main bearing is to place an idler pulley completely opposite to the motor (see attachment). That would increase the contact area of course.
The likelihood of the belt slipping is going to be down to a combination of factors. The belt tension, the angle of the belt relative to the line between the motor and the main bearing, the coefficient of friction between belt and pulley/subplatter and bearing friction.
When up to speed the tension on the belt is going to be pretty much even all the way round (unless you have a very high friction bearing)
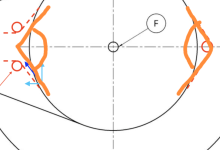
As long as the angles (badly) marked in orange are the same the side forces on the bearing should be cancelled. Using two idlers and the motor positioned at 120° around the main bearing will give the best results but one idler opposite at 180° will be almost as good.
In my deck I have the belt making 90° turns at the pulley and idlers. This left the belt (when using the single belt) making 30° contact with the sub-platter in 3 sections totaling 90°. I never suffered belt slip on the sub-platter with this configuration. The belt would slip a bit on start up so I always spun up to speed manually. Having said that, my bearing is very low friction so your milage may vary.
With my current setup each belt still makes 90° of contact with the pulley or idler but now makes 270° with the sub-platter.
If you decide that you want to limit the side force on the motor, to say 1N as I have, then the angle the belt makes with the pulley will determine the belt tension.
If the pulley makes contact with the belt for 180°, as in your idler example, the maximum belt tension would have to be 0.5N.
If it has a 90° contact the tension would be 0.7N. If 60° the tension would be 1N.
Niffy
Absolutely. I leave everything powered up permanently. I find with most components it takes a couple of days to warm back up.Has anyone else experienced this phenomena with PSUs?
My Purifi 1et400a based power amps with Hypex switching supplies don't need any warm-up. Sweet as a nut from the go.
I would definitely like to try the silicone belt that you are using on your LP12. Where can I find such? Are they already made or do I have to get a certain length and then cut and glue accordingly?
Thanks
P.
Hi Panos,
I purchased a new SILICONE BLUE BELT from a PINK FISH MEDIA member: MIKE P (Trade: Pickwell Audio) in the UK. These SILICONE BLUE BELTS are seamless and come in standard or custom sizes. Just ask for what you need.
£25.00
PLUS
£4.20 Royal Mail International Standard (non tracked economy postage)
or
£9.70 via Royal Mail International Tracked and Signed
After I placed the order, another forum contact suggested the same belt could be had for less $$$ from here:
DINDIKI SILICONE BLUE BELT & MISC.
I can't vouch that they are the same belt, but it seems a reasonable conclusion.
Actually, DINDIKI is quite a nice site for all kinds of interesting bits and pieces.
Enjoy!
That's exactly what I did with my DIY turntable. I am using a large Papst 3 phase motor, but the idler setup is just the same.When up to speed the tension on the belt is going to be pretty much even all the way round (unless you have a very high friction bearing)
View attachment 1170029
As long as the angles (badly) marked in orange are the same the side forces on the bearing should be cancelled. Using two idlers and the motor positioned at 120° around the main bearing will give the best results but one idler opposite at 180° will be almost as good.
Niffy
I used the bearing from a 3 1/2 inch disk drive; it's completely silent and extremely high quality, it has a diameter of 25mm so runs a bit slower than
the motor.
Attachments
Sondeknz, Niffy,Origin Live sell a couple of different pulleys, a short one and a long one that looks like the metal one from your photo. The current OL pulleys are made from plastic, I believe that they are Delrin. They cost around £30 plus postage.
if you are looking for pulley(s) to be used as idler ones, I would recommend to find pulleys with bearings. Then you will only need bolts for the plinth. The Origin Live pulleys are intended for motor application, where they have to be fixed on the shaft, so they would not work for the idler application. Perhaps I may have misunderstood what you are trying to do, though.
My two cents...
Cheers,
Panos
Hi Sondeknz,If you get the chance, it would be great to get some pics up - to get a clear view of your rig and how you have approached the particular design challenges involved.
Here are some more photos of my "vector" drive.
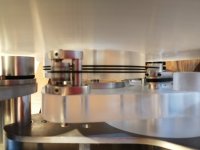

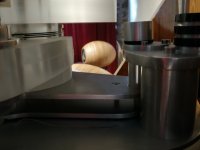
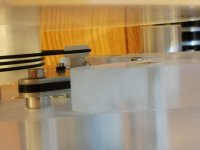
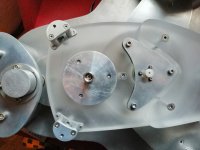
The first 4 try to show how the separate belts run, the 5th is a vertical view with the platter removed.
The top belt goes around the motor, the middle belt goes around the idler at the rear of the deck and the bottom goes around the idler at the front.
The design of my deck is halfway between a solid plinth deck with a dedicated isolation platform built in and a suspended sub-chassis design.
The motor is mounted on the sub-chassis if viewed as a suspended design. Very similar to the Pink triangle in this respect. The centre of suspension of the motor is congruent with the centre of suspension of the isolation platform.
Niffy
The idler wheels have frame with a bearing both above and below the wheel.
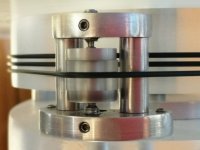
The axle has 1.5mm diameter stubs made from roller bearing elements. These stubs fit into hollowed grub screws mounted into the frame. The grub screws have Teflon lining the hole with a delrin ball acting as the trust element. These grubs are locked in position with a further grub screw in the front of the frame. The frame also has grubs at the rear that allows for a little bit of tilt adjustment.
I went through several design iterations before I came up with these. These are absolutely silent in operation and super low friction. Add in the isolation proffered by the belt and I think these are going to be transferring nothing to the platter.
The Pink Triangle idler wheels are much simpler in design. They have a 3mm axle sticking up from the sub-chassis. The idler wheel is a single piece of Delrin with a blind hole that sits over this axle.
Niffy
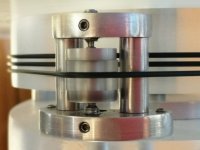
The axle has 1.5mm diameter stubs made from roller bearing elements. These stubs fit into hollowed grub screws mounted into the frame. The grub screws have Teflon lining the hole with a delrin ball acting as the trust element. These grubs are locked in position with a further grub screw in the front of the frame. The frame also has grubs at the rear that allows for a little bit of tilt adjustment.
I went through several design iterations before I came up with these. These are absolutely silent in operation and super low friction. Add in the isolation proffered by the belt and I think these are going to be transferring nothing to the platter.
The Pink Triangle idler wheels are much simpler in design. They have a 3mm axle sticking up from the sub-chassis. The idler wheel is a single piece of Delrin with a blind hole that sits over this axle.
Niffy
Absolutely so, Ralph. You had already implemented what I had I mind with my design.That's exactly what I did with my DIY turntable. I am using a large Papst 3 phase motor, but the idler setup is just the same.
I used the bearing from a 3 1/2 inch disk drive; it's completely silent and extremely high quality, it has a diameter of 25mm so runs a bit slower than
the motor.
Cheers
Panos
Hi Panos,Sondeknz, Niffy,
if you are looking for pulley(s) to be used as idler ones, I would recommend to find pulleys with bearings. Then you will only need bolts for the plinth. The Origin Live pulleys are intended for motor application, where they have to be fixed on the shaft, so they would not work for the idler application. Perhaps I may have misunderstood what you are trying to do, though.
My two cents...
Cheers,
Panos
What type of bearing do the pulleys have?
I did try using precision miniature ball-race bearings for my idler wheels but found them to be quite noisy.
Similar to the selection of motors and the decks main bearing I would recommend avoiding the use of ball race bearings.
Some variety of sleeve bearing will offer lower noise.
Niffy
@pkonstantinidis
Agree with you about the OL pulleys. Not quite right for my idler pulley needs, but maybe helpful if and when I need a motor pulley.
@niffy
So very impressive!
Your framed idlers have solved the concerns I had around dealing with the high belt tension required for low-stretch belts.
In my case, the L12 stock top-plate is not heavy and solid enough to place too much tension on the belt(s). That said, I will stick with a low-tension silicone belt.
One option - which might be easier - is to switch to a carbon fibre sheet for the top-plate and start over. I guess drilling will still be an issue, but I suspect that carbon fibre will offer a stronger and less flexible anchor for pulleys, than the current (bowed) 1mm stainless steel top-plate.
Some of the local suppliers here in China offer very affordable CAD milling of carbon fibre, so that may be the best option - if I can get it right with no errors.
Agree about the idler pulley bearings. I will avoid encapsulated race bearings, in favour of sleeve bearings. I will try to find some with PTFE linings, for quiet running.
Giving it all some thought.
Agree with you about the OL pulleys. Not quite right for my idler pulley needs, but maybe helpful if and when I need a motor pulley.
@niffy
So very impressive!
Your framed idlers have solved the concerns I had around dealing with the high belt tension required for low-stretch belts.
In my case, the L12 stock top-plate is not heavy and solid enough to place too much tension on the belt(s). That said, I will stick with a low-tension silicone belt.
One option - which might be easier - is to switch to a carbon fibre sheet for the top-plate and start over. I guess drilling will still be an issue, but I suspect that carbon fibre will offer a stronger and less flexible anchor for pulleys, than the current (bowed) 1mm stainless steel top-plate.
Some of the local suppliers here in China offer very affordable CAD milling of carbon fibre, so that may be the best option - if I can get it right with no errors.
Agree about the idler pulley bearings. I will avoid encapsulated race bearings, in favour of sleeve bearings. I will try to find some with PTFE linings, for quiet running.
Giving it all some thought.
From my experience I would say that the benefits of belt drive is a greater space and air, and better fine detail and nuance. The benefits of direct drive and idler drive is greater solidity, timing and attack.
Of course these are generalisations. There are direct drive decks with fine nuance retrieval and belt drive with excellent timing and attack.
I found that vectoring has the effect of making a belt drive sound very much like a direct drive in that it brings the solidity and attack. It also enhances the strengths of belt drive (especially with my sleeveless bearing) in that it really opens up the sound.
I would definitely recommend vectoring any belt drive turntable.
Niffy
Of course these are generalisations. There are direct drive decks with fine nuance retrieval and belt drive with excellent timing and attack.
I found that vectoring has the effect of making a belt drive sound very much like a direct drive in that it brings the solidity and attack. It also enhances the strengths of belt drive (especially with my sleeveless bearing) in that it really opens up the sound.
I would definitely recommend vectoring any belt drive turntable.
Niffy
Very interesting bearing, Ralph.That's exactly what I did with my DIY turntable. I am using a large Papst 3 phase motor, but the idler setup is just the same.
I used the bearing from a 3 1/2 inch disk drive; it's completely silent and extremely high quality, it has a diameter of 25mm so runs a bit slower than
the motor.
If I understand correctly, you have taken it from a hard disk drive? If yes, was it a 5400rpm or 7200rpm drive?
Thanks
Panos
Niffy,Hi Panos,
What type of bearing do the pulleys have?
I did try using precision miniature ball-race bearings for my idler wheels but found them to be quite noisy.
Similar to the selection of motors and the decks main bearing I would recommend avoiding the use of ball race bearings.
Some variety of sleeve bearing will offer lower noise.
Niffy
the bearings of my idler pulleys are nothing special. They come preinstalled in the pulleys. If one wants something better, I guess one can easily retrofit the bearings of their preference.
Enclosed you can find some close-up photos. In one of them I have also included a USB-C terminator, so that you appreciate the size.
Attachments
Today I decided to test my newly acquired Maxon motor (RE-max 226764). After mounting it on my Xerxes, with two rubber pulleys (one on top of the other, see photo) that I simply glued on the motor shaft, I was confronted with two rather sad observations:
a) the motor is rather noisy. It right out of the box, not run in at all, but sounds like its bearings are worn out. I had not pressed the shaft at all, as I had not press-fitted the pulleys.
b) the maximum speed that I could achieve with my Origin Live controller (after turning the trimmer at maximum) was only 32.09rpm.
I will let the motor run the whole night, just to see whether it improves overnight. But to be honest, I am not so optimistic about the results. 🙁
Any thoughts or advice, please? Thanks in advance.
Panos
P.S. My Premotec runs so quietly that cannot be heard even from one cm distance...!!
a) the motor is rather noisy. It right out of the box, not run in at all, but sounds like its bearings are worn out. I had not pressed the shaft at all, as I had not press-fitted the pulleys.
b) the maximum speed that I could achieve with my Origin Live controller (after turning the trimmer at maximum) was only 32.09rpm.
I will let the motor run the whole night, just to see whether it improves overnight. But to be honest, I am not so optimistic about the results. 🙁
Any thoughts or advice, please? Thanks in advance.
Panos
P.S. My Premotec runs so quietly that cannot be heard even from one cm distance...!!
Attachments
Another observation is that turning in one direction (clockwise) is much noisier than turning in the other direction (which again is not absolutely quiet). The motor is turning with any load for the moment, so it's not any lateral force on the motor shaft that's causing the noise... -((
On the other hand, I can feel the hight torque of the motor, as it's not easy to stop it by pressing the shaft with my fingers.
On the other hand, I can feel the hight torque of the motor, as it's not easy to stop it by pressing the shaft with my fingers.
Last edited:
Hi Panos,
That is disappointing news.
I had expressed my concern that the controller might not have a high enough maximum output voltage for the configuration that you were proposing and that the motor might run slow. This is relatively easy to remidy. If you double the diameter of your pulleys you will halve the required motor speed and voltage. You will then have a maximum speed of 64rpm, easily enough to accommodate both 33 and 45s. The larger pulleys will also have the advantages of lowering both rolling resistance and rolling noise. As the motor would be running slower it would also be running more quietly.
Of greater concern is the motor noise.
My Premotec motor was also pretty quiet. Straight out of the box my Maxon was quieter. I had to use a mechanics stethoscope to clearly hear either. The Maxon has quietened further with use.
How noisy is it? The Maxon I had with knackered bearings was audible from across the room.
I hope you easily resolve these issues.
Niffy
That is disappointing news.
I had expressed my concern that the controller might not have a high enough maximum output voltage for the configuration that you were proposing and that the motor might run slow. This is relatively easy to remidy. If you double the diameter of your pulleys you will halve the required motor speed and voltage. You will then have a maximum speed of 64rpm, easily enough to accommodate both 33 and 45s. The larger pulleys will also have the advantages of lowering both rolling resistance and rolling noise. As the motor would be running slower it would also be running more quietly.
Of greater concern is the motor noise.
My Premotec motor was also pretty quiet. Straight out of the box my Maxon was quieter. I had to use a mechanics stethoscope to clearly hear either. The Maxon has quietened further with use.
How noisy is it? The Maxon I had with knackered bearings was audible from across the room.
I hope you easily resolve these issues.
Niffy
Hi Niffy,
you are right about the motor noise. That's definitely the biggest concern. After more careful inspection, I've realized that the noise comes from the bottom bearing. When I turn the motor upside down, it runs almost without any noise at all. Bad luck.
I think I must return the motor to Maxon and ask for a replacement. It's rather strange (and disappointing) and Maxon's quality control did not pick up the problem.
Panos
you are right about the motor noise. That's definitely the biggest concern. After more careful inspection, I've realized that the noise comes from the bottom bearing. When I turn the motor upside down, it runs almost without any noise at all. Bad luck.
I think I must return the motor to Maxon and ask for a replacement. It's rather strange (and disappointing) and Maxon's quality control did not pick up the problem.
Panos
Definitely a 3.5 disk drive, but I'm not sure if it's 5400 or 7200; I've stripped many older 3.5 inch disk drives. What I am aware of is that the bearings are preloaded and exceedingly high quality. The best ones I've recovered come from older drives with several platters.Very interesting bearing, Ralph.
If I understand correctly, you have taken it from a hard disk drive? If yes, was it a 5400rpm or 7200rpm drive?
Thanks
Panos
- Home
- Source & Line
- Analogue Source
- 12VDC motor for the turntable. Power, torque, PCB questions