I am well familiar with the Fountek John. My guess would have been either that or Aurum Cantus (who made the CSS of which i went thru a few)
dave
dave
Last edited:
...Are you saying this Richlite is not good cabinet material because it's too dense?
No. What i am saying is that the construction method to achieve such stiffness has the side effect of high density. Same with stranded/fossiized bamboo plywood. To get the stiffness they needed the density.
Perhaps of interest, the western red cedr µFonkenSET PAIR were about the same as one of the same box in Douglas Cedar. Performance was very similar. And it seems, the cedar is standing up to the “weather’ better. And consider the difference in shipping costs.
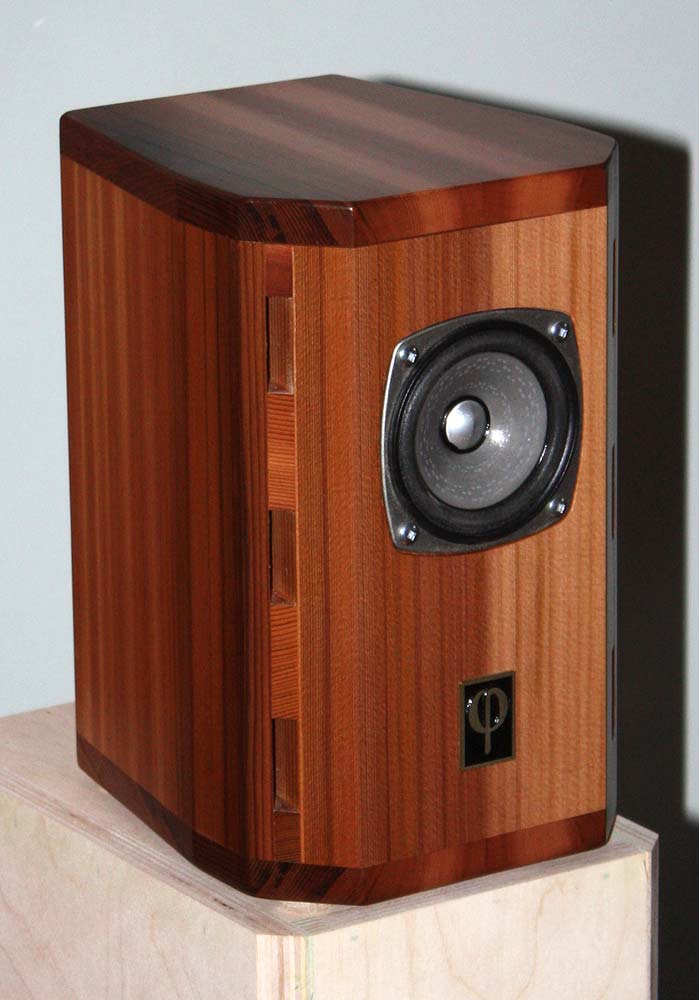
Not the ones of which i speak, Nick’s build, unlikely the same species of oak.
Now these are small, and that does make some difference.
dave
Hi, Just to clarify--I have never used Rainier. I used Richlite products for two loudspeaker prototypes, but only for the front panels, not the entire cabinet. Also, both those Richlite panels were composites with Richlite .125-in. skins on plywood cores--in one case a bamboo plywood core, and in the other case, a birch plywood core. Those choices were primarily because of my consulting clients' retail price and profit margin targets, but weight also was taken into account.I'm curious what the differences between these 2 materials is, I think they're very similar, if not the same just different colors. The Skatelite I mentioned earlier is the Richlite r50 (the same stuff), what the OP used is the Rainier. Are you saying this Richlite is not good cabinet material because it's too dense? Or that the r50 is different than the Rainier?...
https://www.richlite.com/collections/partial-sheets/products/partial-sheets-r50
https://www.richlite.com/collections/partial-sheets/products/partial-sheets-rainier
I love the Richlite Stratum Bamboo so much that I sent the panel out to a medal-winning master violin maker who applied seven hand-rubbed coats of oil violin varnish to the perimeter edge reveal. I also had a scrap piece gilded with gold leaf, but that was a bit much.
As far as I know, there is only one kind of solid Richlite--it is built up from layers of paper specially milled for the purpose, and between the layers of paper they spread thermosetting phenolic resin. The boards then go into a huge press that also heats, resulting in a solid product, as the resin totally infuses the paper.
My surmise is that the striated or layered color options such as Rainier are simply the result of using different pigments in the resin. In other words, my surmise is that structurally and functionally, the 1.25-inch Rainier product is identical to a 1.25-inch board in the r50 color, or in Blue Canyon blue.
My further guess is that the striated products exist because in many applications, such as high-end kitchens or university dining halls, the designers want the visual effect of a round-over or beveled edge reveal, to make whatever it is (a kitchen island or a room divider) more interesting.
ciao,
john
Last edited:
If you don't mind answering, what did you use to glue it?
I always considered using the 0.25 Skatelite (Richlite r50) to attempt constrained layer damping, possibly using .5" baltic birch for another layer, but never really figured out what I'd use for the softer, middle layer, and also what to glue this all with (possibly a 2-part epoxy?). I also don't have an accelerometer, so short of a knuckle test, testing the reality of how effective that is would be very difficult.
I always considered using the 0.25 Skatelite (Richlite r50) to attempt constrained layer damping, possibly using .5" baltic birch for another layer, but never really figured out what I'd use for the softer, middle layer, and also what to glue this all with (possibly a 2-part epoxy?). I also don't have an accelerometer, so short of a knuckle test, testing the reality of how effective that is would be very difficult.
Last edited by a moderator:
Hi, I don't mind answering, but that specific answer is not relevant to your situation. But I do have suggestions to pass on that are relevant.
The carcass or shell of the loudspeaker cabinet with the Richlite (as in the brand name, not the product) Stratum with the Bamboo Plywood front panel was made from IIRC birch ply with maple faces or veneers, and the front panel was rabetted or dado'ed to be inset IIRC .5 inch all around.
So, that join was birch ply to bamboo ply and so I assume that Corwin Butterworth used whatever wood glue (Titebond?) he normally would have used.
I was cc'ed on an email between someone at Eco Supply Center and a professional loudspeaker builder who wanted to know about solid-Richlite-to-solid-Richlite glue-up, and the answer was:
Clear structural epoxy [System 3 T-88 or West Marine Epoxies are great, 24hr dry time] will glue faces and edges together.
My assumption is that the same will work for a dissimilar join such as solid Richlite to MDF or plywood.
Hope that helps.
As for a middle layer, I have used this product for constrained-layer surface damping on the inside of cabinets and under the crossover, but I see no reason it can't be used as a middle layer:
https://www.amazon.com/Sound-Fire-Rated-Acoustical-Putty/dp/B018WQ4D7O/
There are other options, but I have not tried them. I assume that the HILTI Firestop Pad is great, but it is a lot more expensive.
best of luck,
john
The carcass or shell of the loudspeaker cabinet with the Richlite (as in the brand name, not the product) Stratum with the Bamboo Plywood front panel was made from IIRC birch ply with maple faces or veneers, and the front panel was rabetted or dado'ed to be inset IIRC .5 inch all around.
So, that join was birch ply to bamboo ply and so I assume that Corwin Butterworth used whatever wood glue (Titebond?) he normally would have used.
I was cc'ed on an email between someone at Eco Supply Center and a professional loudspeaker builder who wanted to know about solid-Richlite-to-solid-Richlite glue-up, and the answer was:
Clear structural epoxy [System 3 T-88 or West Marine Epoxies are great, 24hr dry time] will glue faces and edges together.
My assumption is that the same will work for a dissimilar join such as solid Richlite to MDF or plywood.
Hope that helps.
As for a middle layer, I have used this product for constrained-layer surface damping on the inside of cabinets and under the crossover, but I see no reason it can't be used as a middle layer:
https://www.amazon.com/Sound-Fire-Rated-Acoustical-Putty/dp/B018WQ4D7O/
There are other options, but I have not tried them. I assume that the HILTI Firestop Pad is great, but it is a lot more expensive.
best of luck,
john
Thank you @johnmarianmarks! That epoxy is what I was assuming would work. I should try this on my next build 😎
As far as the acoustical putty you linked, curious how butyl rubber would work? I already have a bunch of the foil faced, butyl sound deadening. I could bond the sticky side of that to the r50, then try to epoxy the foil side to the birch or MDF. Need to research some options to find the best starting point 🙂
As far as the acoustical putty you linked, curious how butyl rubber would work? I already have a bunch of the foil faced, butyl sound deadening. I could bond the sticky side of that to the r50, then try to epoxy the foil side to the birch or MDF. Need to research some options to find the best starting point 🙂
My guess is that if you could get rid of the foil, you would get better adhesion. But why not just epoxy a sample, it might work. They use some kind of food-safe adhesive to adhere the foil inner seal on peanut-butter jars to the glass or plastic edge, so... it can be done.
ciao,
john
ciao,
john
Last edited by a moderator:
You can't remove the foil. But yes that's the plan, need to do a small test panel and just see what I end up with.
I have one bass guitar (not a Gibson, but a Squier 5-string) that has a Richlite fretboard. It looks sufficiently like ebony to fool most people, but it wears relatively rapidly where you press the strings down onto it.Today, Gibson Guitars uses Richlite for most of its fretboards
I bought my bass second-hand (but it was quite new, well cared for, and lightly used). There were already small groves in the Richlite fretboard where the strings contacted the fretboard when they were pressed down.
The round-wound outer wrap on the steel guitar strings has carved small groves, possibly worsened by typical guitar vibrato technique - you push down the string, pluck it, then vibrate fingertip and string transversely across the fretboard to produce the vibrato.
The grooves in the Richlite aren't deep enough to affect playability (yet), or to be noticed at a casual glance. But I have other guitars with real ebony fretboards, and they do not show the same kind of fretboard wear.
This shouldn't be a concern for the purposes of this thread (loudspeaker front panels). But if my experience is anything to go by, all those expensive Gibson guitars with Richlite fretboards are not going to last for decades and turn into heirlooms, as older all-wood Gibsons did.
-Gnobuddy
This is pretty funny... I was reading this thread and I was going to post something about using material called "Skatelite" for cabinets because it seems very similar to you were talking about. But one of the main issues with Skatelite is that it's only 1/4" thick. Then I looked deeper into this and is actually made by Richlite lol. I actually have a bunch and thought about using a 1/2" baltic birch layer, then figure out how to glue this to the inside of the cabinet, but I've never actually tried that.
Speaking of gluing it, one of the other issues is gluing this, @johnmarianmarks, not sure what you glued yours with, but I was under the impression that wood glue will not work. But I absolutely agree, this stuff is crazy dense- a 4x8 sheet of 1/4" Skatelite weighs about as much as a 3/4" sheet of MDF. FWIW, it's also fireproof.
Just FYI, for anyone that doesn't know, Skatelite is what's used for skateboard ramp sheeting. It's used because it's virtually indestructible so when a skateboard goes flying 10' in the air and the metal truck bounces off a half pipe, it doesn't damage the ramp. But also VERY expensive, a 4x8 sheet of 1/4" thick Skatelite is $190 😳.
https://www.skatelite.com/
hi Matt-
glad you made the connection between Skatelite and Richlite - i work for a Richlite distributor in VA, where we mill the Richlite with CNC routers as well - i thought i could help by giving you a few tips for gluing Richlite to itself [or another substrate] : the phenolic resin that saturates the paper in these panels does not play well with many adhesives, so 24hr cure structural epoxy is the go-to product to use [System 3 T-88 or West System epoxies are both great] - abrade the faces or edges you want to bond with 100 or 80 grit sandpaper to create a tooth, wipe the dust clean, spread epoxy on both faces & use screw clamps to bond tightly for the 24hr cure period. these epoxies are clear & there is no proprietary color filler to hide seams. you can add aniline dye to the epoxy if you wanted to however. NOTE: if you are bonding large faces to one another, you will need to consider panel balancing to prevent warpage - i can go into that scenario more deeply if anyone is interested - it's a pretty important concept to understand before gluing up expensive sheets! speaking of Richlite's expense, i would like to offer some free samples to this community to test for yourselves - you can message me here to get details on ordering. also, to keep costs down, we will be glad to sell smaller drops leftover from manufacturing, if what we have in the bins suits your needs. thanks for your interest & have fun. Al Schaub.
Thanks Al, PM sent!! And thank you for the epoxy instructions and recommendations, I have some West Systems I will try 😎
Last edited by a moderator:
Al, what size panel would you consider large? Would you be willing to go more in depth on this? Probably safe to assume most here have basic woodworking clamps, rather than a real press. In the past, when gluing larger panels of wood I have gotten creative using a few old car batteries I had around as a sort of hillbilly press that worked decently.NOTE: if you are bonding large faces to one another, you will need to consider panel balancing to prevent warpage - i can go into that scenario more deeply if anyone is interested
Hi Al,
Very generous offer to share your experience when gluing larger panels of Richlite. That would be highly appreciate.
Offering bits and pieces from your manufacturing leftovers for testing purposes is simply outstanding.
Very generous offer to share your experience when gluing larger panels of Richlite. That would be highly appreciate.
Offering bits and pieces from your manufacturing leftovers for testing purposes is simply outstanding.
Mattsk8 and SMABB:
Ie also appreciate finding appropriate venues to offer our drops, it's win-win, believe me.
Indeed - a "large" face-glued assembly will be relative to the thickness & stiffness of parts used of course- but let's say for example you are bonding with epoxy again - 5/16" Richlite to a sheet of 3/4" baltic birch - both pieces are pretty stiff already :
- this is achieved by gluing the same material to both faces of the substrate.
While on the topic of balanced panels:
The Stratum Birch panels available from Richlite [3/4 or 1" thickness at 47 x 95"] have 1/8" Richlite skins and cost about 40% less than a solid Richlite panel too of the same thickness & size. Here's what you should know about them:
They have Finnish birch cores with few if any voids - the cores are very attractive, but not waterprooof -
And these Stratum panels have more variance in thickness than 'regular' Richlite:
So- let's say for instance, you make a box out of Stratum - using miters to show off the sandwiched core - my suggestion is to make sure to mic to parts adjacent to one another before millwork - so you can employ self similar thicknesses for that feature.
Also:
Richlite can be sanded - it it a stack of colored, resin-saturated paper - so there is some room to sand before you burn through the top sheet & can see the next sheet peeking through. you can take it to a high polish if you like too - and you will see the way it wears over time by polishing further where it is handled & also getting light scratches that burnish out over time. You can also just leave it unsanded with the paper texture intact - and the little hills & valleys of the paper's surface will hide scratches a little bit better than a sanded piece after it starts being used. Either way, Richlite wears sort of the way a chemistry lab top does - so even the unsanded parts would wind up getting burnished & polished with years of use.
Finally:
the finish we recommend is a non-VOC oil that gets wiped on & wiped off as much as possible - 24hr dry time with a 72hr cure time. OSMO Poly X oil, also knows as Richlite Top Oil.
Cheers & have fun!
Ie also appreciate finding appropriate venues to offer our drops, it's win-win, believe me.
Indeed - a "large" face-glued assembly will be relative to the thickness & stiffness of parts used of course- but let's say for example you are bonding with epoxy again - 5/16" Richlite to a sheet of 3/4" baltic birch - both pieces are pretty stiff already :
- at 8x8" or 12 x12" , the 2-ply glue up face-to face may not ever yield any measurable curl from that imbalance.
- but a 24 x 24" of the same would very likely warp - at least a little bit - to give you a sense of scale.
- this is achieved by gluing the same material to both faces of the substrate.
a vacuum or panel press is best of course, but batteries & buckets of water also work for many..
While on the topic of balanced panels:
The Stratum Birch panels available from Richlite [3/4 or 1" thickness at 47 x 95"] have 1/8" Richlite skins and cost about 40% less than a solid Richlite panel too of the same thickness & size. Here's what you should know about them:
They have Finnish birch cores with few if any voids - the cores are very attractive, but not waterprooof -
And these Stratum panels have more variance in thickness than 'regular' Richlite:
there might be 1/32" difference in thickness from panel to panel, or even end-to-to end.
So- let's say for instance, you make a box out of Stratum - using miters to show off the sandwiched core - my suggestion is to make sure to mic to parts adjacent to one another before millwork - so you can employ self similar thicknesses for that feature.
Also:
Richlite can be sanded - it it a stack of colored, resin-saturated paper - so there is some room to sand before you burn through the top sheet & can see the next sheet peeking through. you can take it to a high polish if you like too - and you will see the way it wears over time by polishing further where it is handled & also getting light scratches that burnish out over time. You can also just leave it unsanded with the paper texture intact - and the little hills & valleys of the paper's surface will hide scratches a little bit better than a sanded piece after it starts being used. Either way, Richlite wears sort of the way a chemistry lab top does - so even the unsanded parts would wind up getting burnished & polished with years of use.
Finally:
the finish we recommend is a non-VOC oil that gets wiped on & wiped off as much as possible - 24hr dry time with a 72hr cure time. OSMO Poly X oil, also knows as Richlite Top Oil.
Cheers & have fun!
Attachments
Got my samples.
Richlite over block core bamboo, with plywood, with bamboo but different.
This stuff is impressive. Very smooth and solid surface.
Quick look suggests that a µMar-KenPlus derivative can be done with richlite baffle, back, top, bottom out of the samples, certainly have enuff 18mm BB for the sides, hopefully i can scare up some 12 or 15.
dave
Richlite over block core bamboo, with plywood, with bamboo but different.
This stuff is impressive. Very smooth and solid surface.
Quick look suggests that a µMar-KenPlus derivative can be done with richlite baffle, back, top, bottom out of the samples, certainly have enuff 18mm BB for the sides, hopefully i can scare up some 12 or 15.

dave
We did a set of mFonken tops with it, but Chris did not figure it that good a cabinet material.
You also have to have all the skills to work with it if you are doing anything more than our use as veneer.
dave
You also have to have all the skills to work with it if you are doing anything more than our use as veneer.
dave
good news, Dave! sorry those took a minute - they got refused/returned at the Canadian border the first time around. let me know if i can help with anything else & have a great morning. AlGot my samples.
Richlite over block core bamboo, with plywood, with bamboo but different.
This stuff is impressive. Very smooth and solid surface.
Quick look suggests that a µMar-KenPlus derivative can be done with richlite baffle, back, top, bottom out of the samples, certainly have enuff 18mm BB for the sides, hopefully i can scare up some 12 or 15.
![]()
dave
- Home
- Loudspeakers
- Multi-Way
- An Under-Appreciated Cabinet Material