This treatise on hornmath by W.H. Geiger includes the following statement:
"Bottom line: the tractrix flare is useful for designing the bells of mid and high frequency horn mouths. For the design of horn necks as well as entire low frequency horns, its use is contraindicated. Alternatively, use of a Salmon family horn flare (that includes exponential flare) is preferred. By setting, tangent angles equal at the junction of the Salmon horn neck and tractrix bell, a near ideal mid- or high-frequency horn design may be achieved provided other design issues have been properly and successfully addressed."
"Bottom line: the tractrix flare is useful for designing the bells of mid and high frequency horn mouths. For the design of horn necks as well as entire low frequency horns, its use is contraindicated. Alternatively, use of a Salmon family horn flare (that includes exponential flare) is preferred. By setting, tangent angles equal at the junction of the Salmon horn neck and tractrix bell, a near ideal mid- or high-frequency horn design may be achieved provided other design issues have been properly and successfully addressed."
Nothing so elaborate, unfortunately 😀. I find this superior to starting with a round opening, where there is no pre-existing throat, ie a cone driver without a JBL style phase plug, subject to the right circumstances.Your description reminds me of Funktion One's Axe-Head
Attachments
Last edited:
Yes, seems so according to the sims ro808 just posted.I guess maybe better to say along the outside.

After 35 years of working with large speaker horns, I've come to the conclusion that multi-cell is the thing for me. Having gotten such good results from so many, in so many different venues - I have decided to be lazy and stick to what works well for me. Multi-cell. (always fun to read about other horns, tho)
After 35 years of working with large speaker horns, I've come to the conclusion that multi-cell is the thing for me. Having gotten such good results from so many, in so many different venues - I have decided to be lazy and stick to what works well for me. Multi-cell. (always fun to read about other horns, tho)
And what makes them special to you Pano ( what you don't find in other kind in a pure subjective way)?
I have to admit iv'e not heard a lot of them and mostly in bad conditions ( acousticaly speaking).
But EV9040 is 1,3" the 2450SL is 1,5", right?
Does this work?
Yes the HR's throat is actually measured 1.4". I have used Altec 1.4 JBL 1.5 Celestion 1.4 Faital 1.5 EV 1.3 and others with these horns.
http://xlrtechs.com/dbkeele.com/PDF/Keele (1975-05 AES Preprint) - Whats So Sacred Exp Horns.pdf
And what makes them special to you Pano ( what you don't find in other kind in a pure subjective way)?
I have to admit iv'e not heard a lot of them and mostly in bad conditions ( acousticaly speaking).
I am curious as well...I thought multicell was in need of HF support? I don't think its come up as a suggestion on my signal elitist mission.
Compared to the Jericho trumpet I like the progressive expansion T horns a lot more. it has the same base parameters but constantly increases the T factor:
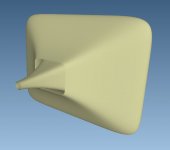
View attachment drba_swh_160_sq_pe_rb.zip
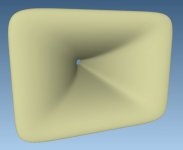
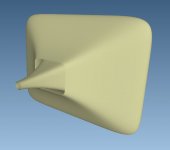
View attachment drba_swh_160_sq_pe_rb.zip
I tried loading these into fusion360 and it doesn't recognize the file type.
So I have no idea how to tell (yet) the actual size of these horns.
It seems several people prefer the squarish horns over round...Why?
My bottom line, regardless of T factor, is a horn that will be proper for 200hz production.
So I have no idea how to tell (yet) the actual size of these horns.
It seems several people prefer the squarish horns over round...Why?
My bottom line, regardless of T factor, is a horn that will be proper for 200hz production.
If you load the model into that webpage I posted earlier: Creators 3D
To the right of that browser screen there is a barely visible green line saying: Download as OBJ
That will save it in OBJ format and is readable with Fusion:
Maybe docali can save in other formats as well, but this is a quick work-around.
This still leaves you with a model build up with faces (surface model) that needs to be converted to a solid body. I see docali has made some adjustments as it is almost a full closed model already with an outer back shell present this time around. With some patch work you should be able to convert it into a full solid. Pretty sure Youtube will have Tutorials on how to do that in Fusion 360.
A question though, did we start with a good match between the Axi and this horn? Do the angles (exit/entrance) match?
To the right of that browser screen there is a barely visible green line saying: Download as OBJ
That will save it in OBJ format and is readable with Fusion:
Maybe docali can save in other formats as well, but this is a quick work-around.
This still leaves you with a model build up with faces (surface model) that needs to be converted to a solid body. I see docali has made some adjustments as it is almost a full closed model already with an outer back shell present this time around. With some patch work you should be able to convert it into a full solid. Pretty sure Youtube will have Tutorials on how to do that in Fusion 360.
A question though, did we start with a good match between the Axi and this horn? Do the angles (exit/entrance) match?
Attachments
Last edited:
My bottom line, regardless of T factor, is a horn that will be proper for 200hz production.
You may measure 200 hz at the mouth of a big horn like the big long western electrics with the field coil compression drivers but once you get back 6 feet or so they fall off below 300 in free space. The length and bends make them usable to 5K on the top end so you have 300 to 5K response.. If you wish a true 200 hz in room response it's best to use a cone driver not a midrange compression driver like the Celestion.. I find a cone loaded horn to 500-800 hz then handed to the upper range horn gives excellent results.
I was speaking of printing at home. Maybe use wood and concrete filament. I could still finish the outside surfaces with something else, if needed, and filling with sand, sounds like a great idea. I'm just worried about warping, it wouldn't matter if the horn was printed in ABS, if its filled with sand and the inside was finished with epoxy, or some various top/finish coat.
I never answered this question, did I?
What I meant is use 3D printing to create a plug of the horn you want to make/create. I don't particularly like the usual filaments for this Horn duty as an end product. One could print the plug and work on creating a horn from that, much like the Azurahorn is created: Azurahorn -Le Cleac'h Acoustic Horns - DIY Manafacture
With thanks to Martin Seddon:
for showing us howto...
The most time investing/difficult part would be substituted by 3D printing. All that would be left to do is laying up the resin/matt and the rest of that process shown on the Azurahorn page.
Attachments
Last edited:
Well I suppose I've been lucky enough to hear them in mostly good acoustic environments; well treated rooms, a mountainside theater, 40s vintage cinemas, a courtyard in a French monastery.And what makes them special to you Pano ( what you don't find in other kind in a pure subjective way)?
What I liked about them in the 1960s was how good they sounded. I didn't know much about speakers or Hi-Fi back then, just what I thought sounded great and what did not. Later research showed me that I had been listening mostly to Altec 1005 tar filled horns with 288 drivers.
A couple of decades later I experienced the multi-cell in a Hi-Fi setting and was amazed. With better than stock EQ and crossovers I've never heard speaker sound as natural, as true to life. I have heard more detail, but not more natural. Acoustic or studio, mono or stereo, all amazing. That got me hooked.
Now in the 21st century I simply get good results from the multi-cell whether it's in a listening room or on the side of a mountain. Wood or metal, tar filled or not. The coverage is clean, clear and even. The image is strong and stable. They work so well for me that I really don't need to pursue anything else. I hope that helps clarify my point of view.
The big ones usually are, so not really ideal for the two-way that you want. I have a pair with the BMS coaxial drivers and that helps the top end, but it's not perfect. Fortunately you can usually add just a super tweeter at 7-8K as things aren't as critical up there.I am curious as well...I thought multicell was in need of HF support?
That said, when I was young and my ears were fresh, I preferred the 1505 horn driven by a Westrex driver without the added tweeter. Yes, I could hear the added top end of the tweeter, but it sounded fake to me. These days and with these ears, tweeters don't sound as fake. 😱
I never answered this question, did I?
What I meant is use 3D printing to create a plug of the horn you want to make/create. I don't particularly like the usual filaments for this Horn duty as an end product. One could print the plug and work on creating a horn from that, much like the Azurahorn is created: Azurahorn -Le Cleac'h Acoustic Horns - DIY Manafacture
With thanks to Martin Seddon:
![]()
for showing us howto...
The most time investing/difficult part would be substituted by 3D printing. All that would be left to do is laying up the resin/matt and the rest of that process shown on the Azurahorn page.
Its funny you should say that, my engineering buddy thinks the same thing. To create a mold using 3d printing and then use soem type of material to create a cast. I'm not against that but, I'd be fully convinced if the end result was cheap and desirable. For example, my idea to print a shell, filled with sand...if done correctly, would be desirable given the potential inert properties of the successful construction of such. So what would be the this casting material that would produce this desireable product. Fiberglass/resin epoxy casts that are like autotech and Azurahorn, are acceptable but wood and concrete are better. The materials for such aren't expensive yet aren't cheap and involve multiple processes. Is there a sole material available that would also be desirable as a cast and finish process? I never found a display showing how the concrete jmlc horns were made. Potentially I could make a two part mold to cast mortar. Clay requires some serious baking, but there are different types of clay. Making it out of pure epoxy resin is expensive. I don't want to go through all this work and end up with just another white thin horn. Not to say that they aren't acceptable I just feel like I can do better somehow.
It wants to be solid as well.to print a shell, filled with sand...if done correctly, would be desirable given the potential inert properties of the successful construction of such
I find this superior to starting with a round opening, where there is no pre-existing throat, ie a cone driver without a JBL style phase plug, subject to the right circumstances.
The function of the knuckles/bulges in JBL Image Control Waveguides is somewhat similar to the Klipsch mumps.
This classic horn is another (extreme) example, except for the 'cut off lips'.
Not surprisingly, this horn was nicknamed "Bowtie".
Attachments
You may measure 200 hz at the mouth of a big horn like the big long western electrics with the field coil compression drivers but once you get back 6 feet or so they fall off below 300 in free space. The length and bends make them usable to 5K on the top end so you have 300 to 5K response.. If you wish a true 200 hz in room response it's best to use a cone driver not a midrange compression driver like the Celestion.. I find a cone loaded horn to 500-800 hz then handed to the upper range horn gives excellent results.
I am trying to digest what you've said. I am not really interested in the sato horns it was just kind of a side thought. The horns that you see Docali modeling are up for discussion. So the model he made called "Jericho" are of my inspiration, having longer throat length to assist in deep loading is my interest. I think Docali is being my devils advocate to make sure I'm not inducing unnecessary beaming by choosing a longer horn than is needed to accomplish 200hz production.
I'm making sure that the effort from everyone involved is actually actualized, by studying 3d printers as I prepare to purchase one with the conclusion that it is the tool needed. 3d printing is a deep solution. Meaning I may never print a horn or horn mold....I may end up printing a mechanical device that I use to make the horn some other way.
It wants to be solid as well.
Invention bred from necessity. I'm brain storming in front you, If you got ideas, I'm all ears! lol.
I could print a two part mold and fill it with concrete. Or just fill the shell with concrete instead of sand. I thought the sand was a better idea in light of the dual walled, sand filled enclosure. Maybe there is a doubt that between the adherence of the printed parts and layers of epoxy, solidarity will be achieved. Ok someone mention the fiberglass products. What about that? Maybe I can pour fiberglass resin into the shell? Maybe mix it with sand, or mix mortar sand and fiberglass resin, and do the outsides in epoxy resin.
OK never mind the fiberglass resin which is really polyester resin which the hardener is pretty dangerous stuff....I second GM's motion for concrete.
Last edited:
I don't want to go through all this work and end up with just another white thin horn. Not to say that they aren't acceptable I just feel like I can do better somehow.
Years ago, I was looking into casting with liquid wood, wich essentially consists of a wood-based filler (e.g. sawdust) mixed with natural resins/bio-based epoxies.
Some examples:



Last edited:
- Home
- Loudspeakers
- Multi-Way
- Is it possible to cover the whole spectrum, high SPL, low distortion with a 2-way?