If that's a 3-phase motor it's horribly broken!Checking this motor, my Fluke meter tells me that there are only two combinations that yield any resistance.
Blue-----Yellow 200 ohms
Green-----Red 58 ohms
not what I was expecting?
My offhand semi-educated guess is that the 200 ohm winding connects directly to the power line, and the other one goes in series with the capacitor to the power line. The relative phase of the windings should determine rotation direction.
Will wonders never cease ?
I went down to the shop and rummaged around and found a fax from Feb 1993 from Elinco. It was pretty faded but I was able to pull this info out of it....
I went down to the shop and rummaged around and found a fax from Feb 1993 from Elinco. It was pretty faded but I was able to pull this info out of it....
An externally hosted image should be here but it was not working when we last tested it.
O.K., sorry for steering you wrong.
That's the first two phase hysteresis synchronous motor I've seen.
Not a problem. I'm sure you didn't try to mislead.
At any rate...."discovery" is the reason I pursue most of the interests/hobbies that I have.
I did find a 3uF running cap down at the packrat-a-torium (the shop) so I was able to get it running yesterday afternoon. The bearings are very noisey, but I was able to find a couple nos replacements on fleabay.
and the beat goes on.....
I'll be interested in what people come up with for a 60Hz motor controller, since I can't afford the VPI SDS for my table. Another question, my o-ring belt finally broke and I was going to replace it, but I never liked the idea of a rubber belt. My VPI motor is no longer in the base, it sets off to the side in a aluminum case, so I no longer need the isolation from a rubber belt. I was thinking of silk or kevlar thread, any recomendations? I may also add a second motor since I use a MKIII plater that is heaver than the HW19 stock platter. Anyone try this?
thingap
rgds
jms
The ThinGap® Advantage
ThinGap’s patented electromotive coil technology improves motor performance by eliminating the need for wire-wound stators with slotted laminations. Instead, precision-machined copper sheets provide the coil with structure, replacing the copper magnet wire and slotted laminations used in conventional motors. This allows higher copper packing density and a higher ratio of copper to total coil volume, while virtually eliminating the magnetic detents (cogging) caused by slotted laminations.
No Hysteresis Torque
By replacing the stationary laminated stack with a rotating solid steel return path hysteresis losses are eliminated. Since slotted laminations are unnecessary, the magnetic detents they cause are eliminated. This combination of features virtually eliminates cogging, in turn minimizing velocity and torque ripple.
No Cogging Torque
Eliminating slotted laminations eliminates cogging torque caused by slot interaction with magnets. Since the coils are constructed without iron, and all iron parts either rotate (i.e., brushless motor) or remain stationary (i.e., brush motor), cogging torque and hysterisis drag torque are virtually non-existent.
Smooth and Quiet Operation
Harmonic variation of torque and voltage are reduced by eliminating lamination slots. Additionally, since an AC field does not exist in the iron components, AC excitation of acoustic noise from the iron is eliminated. The only detectable noise comes from bearings, air turbulence around the coil and vibration caused by non-sinusoidal current waveforms.
Sinusoidal Back EMF Waveform
The motors contain very low voltage harmonics because of the precise location of the coil elements and inherent smoothing of the waveform due to the coil configuration in the air gap. This provides exceptionally smooth constant torque independent of rotor angle with sinusoidal drives and controllers. This characteristic is especially useful for slow-moving objects (e.g., telescopes, optical scanners, and robotics) and precision surface machining, where smooth motion control is crucial.
rgds
jms
I'll be interested in what people come up with for a 60Hz motor controller, since I can't afford the VPI SDS for my table.
Get the December issue of AudioXpress.
Last edited:
Nanook,
Thanks for the link. It looks interesting and easy enough to build, but I'm wondering if the micro and display are still available (2006 design). I also have no way to program the micro (no software or hardware). Anyone out there have the ability to program Microchip parts (or the parts from the AudioXpress design)? Also I would like see if I can get a reprint of the AudioXpress article (but wil have the same programming problem)?
Thanks for the link. It looks interesting and easy enough to build, but I'm wondering if the micro and display are still available (2006 design). I also have no way to program the micro (no software or hardware). Anyone out there have the ability to program Microchip parts (or the parts from the AudioXpress design)? Also I would like see if I can get a reprint of the AudioXpress article (but wil have the same programming problem)?
I have gotten the new bearings installed and it runs smoothly now. I think this motor has other issues though.
It gets too hot to touch!
I ran it all day a couple of days and it runs fine it just gets really hot.
I have tried both 3uF caps I had with the same results.
Does this indicate a problem in the windings?
It gets too hot to touch!
I ran it all day a couple of days and it runs fine it just gets really hot.
I have tried both 3uF caps I had with the same results.
Does this indicate a problem in the windings?
Straight Tracker: "it has become apparent that a simple way to do that would be to use a motor from a used direct drive turntable as has been suggested by many others. But instead of driving from a direct drive turntable to a DIY turntable with a belt, why don't you take the extra step of removing the motor from the direct drive turntable and make a free standing housing for it in the Micro Seiki style? A number of years ago I obtained two direct drive motors from Matsushita as samples to experiment with. but I never got around to that.Yesterday I looked at the motors and found that the idea with the bail is feasable. This approach would take up half the space and would look pleasing to the eye. What do you think?"
I have made similar approach a year ago by taking two identical motor and platters from two Pioneer PL-L1000 direct-drive turntables and belt-driving each other. I used VHS tape as the belt. I even used an idler wheel to replace the tape/belt as interface and got that "idler sound" tonal characteristic - lush and robust. This approach allows me to try three drive systems, direct-drive, belt-drive, and idler-drive. The Pioneer motor is their Stable Hanging Rotor (SHR) design, inverted bearing on a DD motor and the magnet housing, rotor, acting as the subplatter and I believe it can be used as a pulley driving the other rotor. It's fun using two turntables but they do take up a lot of space.
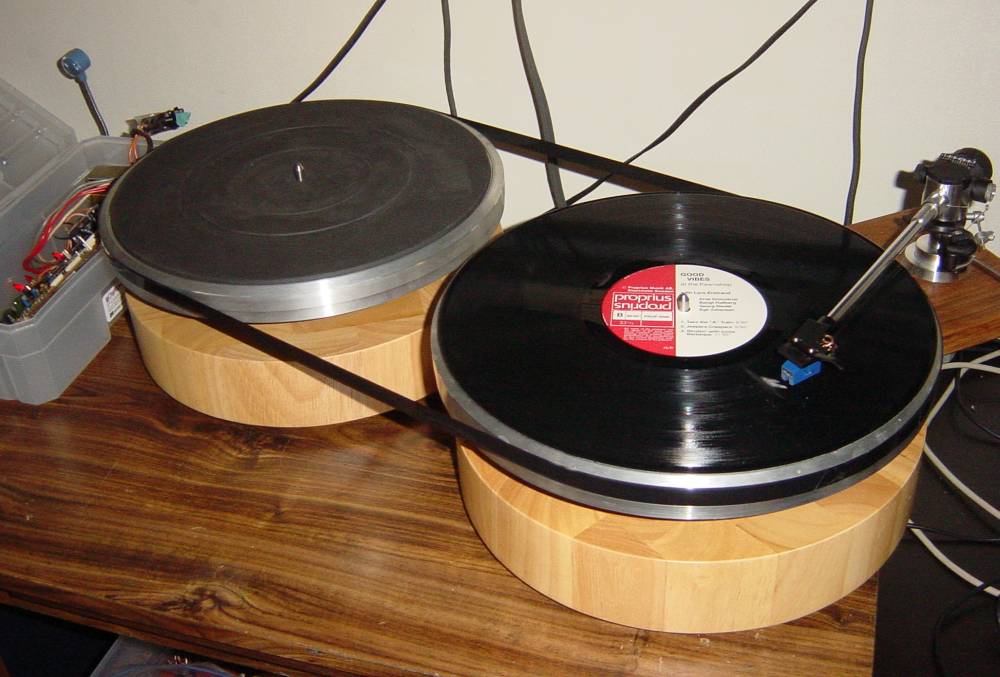
.
cygnus...ideas for a belt...
sorry for the "late idea. Try mylar tape or typical cassette tape. I have used an upholster's nylon thread as a drive belt to good effect. It is very tough, yet pliable.
Also you can use different sized pulleys to get the speed correct, as long as there is some speed adjustment available already.
directdriver:looks very good, but the need for 2 identical decks may limit some.
sorry for the "late idea. Try mylar tape or typical cassette tape. I have used an upholster's nylon thread as a drive belt to good effect. It is very tough, yet pliable.
Also you can use different sized pulleys to get the speed correct, as long as there is some speed adjustment available already.
directdriver:looks very good, but the need for 2 identical decks may limit some.
.
I just happened to have two identical ones but I have also used several turntables with speed adjustment such as the PL-570. Basically, any turntable with flat rim platter and speed adjustment will work. Models to recommend are Technics SL-M3, JVC QL-F6, Pioneer PL-570 & PL-550, etc... Or you can always add a plate on top of another turntable acting as a pulley, in this case the ubiquitous Technics SL-1200Mk2 will work great as a turntable "motor-pod." Get one at second hand price and it will beat most fancy motor-pods costing an arm and a leg. And it will make you pay attention to motor quality and realize all this attention to fancy shiny blig bling thick platters is misguided. Get the source of rotation, the motor, right and with quality, the sound will benefit. The two turntable approach saves me the trouble and money to find a high speed motor with proper speed control electronics - too much hassle for me. I am quite satisfied with the result.
In this picture, I put a Technics SL-1400Mk2 with a broken tonearm to goo use. I added flat rim platter, a salvaged part, on top of the Technics platter acting as a pulley. You can even add an idler wheel in between the two turntables. The passive platter is from an Empire 208 belt-drive turntable.
.
Nanook: looks very good, but the need for 2 identical decks may limit some.
I just happened to have two identical ones but I have also used several turntables with speed adjustment such as the PL-570. Basically, any turntable with flat rim platter and speed adjustment will work. Models to recommend are Technics SL-M3, JVC QL-F6, Pioneer PL-570 & PL-550, etc... Or you can always add a plate on top of another turntable acting as a pulley, in this case the ubiquitous Technics SL-1200Mk2 will work great as a turntable "motor-pod." Get one at second hand price and it will beat most fancy motor-pods costing an arm and a leg. And it will make you pay attention to motor quality and realize all this attention to fancy shiny blig bling thick platters is misguided. Get the source of rotation, the motor, right and with quality, the sound will benefit. The two turntable approach saves me the trouble and money to find a high speed motor with proper speed control electronics - too much hassle for me. I am quite satisfied with the result.
In this picture, I put a Technics SL-1400Mk2 with a broken tonearm to goo use. I added flat rim platter, a salvaged part, on top of the Technics platter acting as a pulley. You can even add an idler wheel in between the two turntables. The passive platter is from an Empire 208 belt-drive turntable.
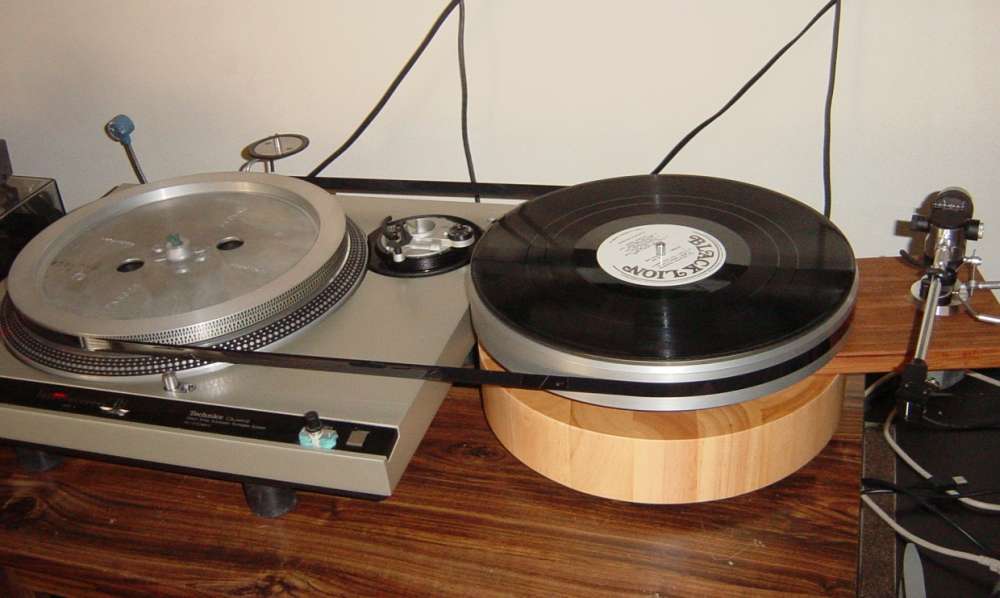
.
Last edited:
I recall that earlier thread featuring the VHS tape/belt drives.
I've got a Dual 1229 I've used for much of the last 15 years, and a 1219 sitting around - these both have tall, exposed, perfectly vertical platter sides just waiting for this to be done. I've heard that the ball-bearing based thrust bearing as used in Duals is less than ideal for a TT, but this has got to be big improvement over that subtle earthquake-in-the-background sound of idler wheel drive. Also, you're a proponent of DD TT's for doing the driving, I wonder how much vibration of a rim drive would be transmitted by the tape.
Is there some guide used to keep the tape/belt aligned on the platters? I don't see it offhand. It looks like it would fall off or ride up-and-off after a short time of running.
I've got a Dual 1229 I've used for much of the last 15 years, and a 1219 sitting around - these both have tall, exposed, perfectly vertical platter sides just waiting for this to be done. I've heard that the ball-bearing based thrust bearing as used in Duals is less than ideal for a TT, but this has got to be big improvement over that subtle earthquake-in-the-background sound of idler wheel drive. Also, you're a proponent of DD TT's for doing the driving, I wonder how much vibration of a rim drive would be transmitted by the tape.
Is there some guide used to keep the tape/belt aligned on the platters? I don't see it offhand. It looks like it would fall off or ride up-and-off after a short time of running.
I wonder how much vibration of a rim drive would be transmitted by the tape.
In order to stop vibrations in the direction of the moving tape in professional studio tape recorders, a device called a flutter or scrape filter was employed. It cosisted of a small flywheel in contact with the tape and driven by the same.
I have one from a Scully machine and I'll post a picture if anyone wants to see one.
Sincerely,
Ralf
.You can even add an idler wheel in between the two turntables.
If you wanted to use an idler. The perfect place for it would be the empty tone arm socket.
Sincerely,
Ralf
I wonder how much vibration of a rim drive would be transmitted by the tape.
VHS tape is not compliant and therefore not particularly forgiving in this respect. Better drive with a good source. From an engineering perspective I don't see the advantage of this setup. Perhaps someone could enlighten me.
Is there some guide used to keep the tape/belt aligned on the platters? I don't see it offhand. It looks like it would fall off or ride up-and-off after a short time of running.
With flat belt drives it is usual practice to put a slight crown on the pulleys to keep the belt in place. It will tend to climb to the top of the crown. This is how they did it in the good old days of flat leather drive belts for power transmission.
- Home
- Source & Line
- Analogue Source
- The Official Turntable Drive System/Motor Thread!