We are all thinking roughly the same. I'm deliberately making a small version, so I'm going to be a bit stubborn: I'm thinking about 2040, but 4040 is too big for me at this stage.
This looks like what I have in mind:
https://vslot-poland.com/en_US/p/MANIPULATOR-KARTEZJANSKI-XYZ-ROBOT/7014
But of course a U in one plane and I only need 2 steppers.
This looks like what I have in mind:
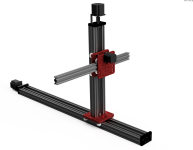
https://vslot-poland.com/en_US/p/MANIPULATOR-KARTEZJANSKI-XYZ-ROBOT/7014
But of course a U in one plane and I only need 2 steppers.
Someone had mentioned having the moving part of the contraption on the ceiling, that would provide an easy way to have a low speaker platform without the need to maneuver around all the moving parts when placing the speaker, but that idea does of course create its own set of challenges.For my uses I will indeed be having a very close to the ground platform and a taller roughly mid height platform. Otherwise it is not a practical design for me as Erin pointed out in his review. Not an exciting prospect lifting a large expensive loudspeaker onto a platform nearly 4 feet high. I have one client that designs loudspeakers that are in the multiple hundreds of pounds, and that we are doing prototype work for currently. A perfect example of what you cannot do with a Klippel system.
As far as potential hardware designs, I have attached a CAD sketch of the concept that @Dave Zan had years back in this thread... just to make things more complicated.
It's a simple sketch, but if anyone thinks it's worth pursuing the design, then by all means, please provide some comments, input, or suggestions.
Attachments
It’s not stubbornness to make something that suits your purposes. The whole DIY thing would be kinda silly if we all felt compelled to rigidly end up with the same result! Besides, I think the smaller aluminum profile makes more sense for a small test rig so I think your plan makes good sense.We are all thinking roughly the same. I'm deliberately making a small version, so I'm going to be a bit stubborn: I'm thinking about 2040, but 4040 is too big for me at this stage.
Continuing the theme of sharing current thinking, with the understanding that I have no interest in dictating what anyone else does:
Rather than trying to find a large and expensive gear for driving the rotation of the mic, I’m inclined to use a belt with its teeth facing outward, wrapped around a plywood “wheel” to form a gear. If the right type of belt is chosen, another loop of the same type of belt, with teeth facing inward, can mate with the “gear” and convey the torque applied by a stepper. The gear would be mounted above or below the lazy Susan bearing I mentioned previously.
I’m increasingly convinced that the hardware for this thing need not be expensive or complicated. Making it work, and manipulating the data, may be another matter. All part of the fun!
Few
If anyone wants the Hafele Lazy Susan Gear I opened an account with Hafele. The industry cost is not too bad. I showed a few gents over private message. Not trying to resell, just making it available at my cost. Slight chance to even drop ship. I'm in Canada so drop shipping is a lot smarter than shipping two times.Rather than trying to find a large and expensive gear for driving the rotation of the mic, I’m inclined to use a belt with its teeth facing outward, wrapped around a plywood “wheel” to form a gear.
You actually don't need the teeth facing out. The plywood circle of the right size is enough by itself for the teeth of the belt to grip on. MTG90 has a large turntable made that way. I bought myself a 2m long GT2 10mm belt to do the same thing. Some belts are designed to mesh with themselves but for simplicity there is no need.Continuing the theme of sharing current thinking, with the understanding that I have no interest in dictating what anyone else does:
Rather than trying to find a large and expensive gear for driving the rotation of the mic, I’m inclined to use a belt with its teeth facing outward, wrapped around a plywood “wheel” to form a gear.
Knowing how cheap and easily available parts are for similar constructions, it most certainly doesn't have to be.I’m increasingly convinced that the hardware for this thing need not be expensive or complicated. Making it work, and manipulating the data, may be another matter. All part of the fun!
I personally would first make up the design, either a simple sketch or in CAD, get an understanding where all the important parts and sections are and than come up with what to get.
That sounds like me. However...
This time I'm doing things differently. I'm getting some stuff and will find out in real life. The cost of actual stuff doesn't outweigh the time (and frustration...) I would need to spend on CAD. For other people this balance might be different.
I've ordered some profiles, gantries and small parts. I will find out how much of a problem e.g. bending and play is.
I'm starting to warm up to the direct drive/ (POM) rack teeth idea. Any good and cheap ones from suppliers in Europe?
This time I'm doing things differently. I'm getting some stuff and will find out in real life. The cost of actual stuff doesn't outweigh the time (and frustration...) I would need to spend on CAD. For other people this balance might be different.
I've ordered some profiles, gantries and small parts. I will find out how much of a problem e.g. bending and play is.
I'm starting to warm up to the direct drive/ (POM) rack teeth idea. Any good and cheap ones from suppliers in Europe?
https://www.systeal.com/en/pinions-and-racks/1834-gear-rack-internal.htmlI'm starting to warm up to the direct drive/ (POM) rack teeth idea. Any good and cheap ones from suppliers in Europe?
Here's an attempt to clarify what I tried to describe back in post 1338. I'm not pushing anyone in this direction, I just figured I'd post the images since I now have them. The mic would be inserted in the end of the blue cylinder, which extends from an aluminum V-extrusion that rides on four wheels for radial motion of the mic. Another four wheels (see second drawing) provide vertical motion along the green extrusion. Angular motion is centered around the red lazy Susan which supports a piece of plywood. The other end of the plywood is supported by two small red wheels. A belt driven by a stepper motor wraps around a plywood disk concentric with the lazy Susan. A pedestal of suitable height could fit through the hole in the lazy Susan and plywood.
Few
Few
I didn't start out envisioning a plywood platform but came around to it when trying to keep open the possibility of some tensioned wires to keep the vertical post from wobbling. Only a test assembly will determine if those wires will be necessary; aluminum extrusions throughout would certainly look more elegant!
I have an idea that may or may not be helpful. For the radial movement, have two arms connected to the vertical piece, one holding the microphone, the other holding a weight that weighs the same as the mic. When the mic moves in, the other arm would move out the same distance. This keeps the total weight on the vertical piece at the same place, thus it will not bend or change position due to the mic changing position.That sounds like me. However...
This time I'm doing things differently. I'm getting some stuff and will find out in real life. The cost of actual stuff doesn't outweigh the time (and frustration...) I would need to spend on CAD. For other people this balance might be different.
I've ordered some profiles, gantries and small parts. I will find out how much of a problem e.g. bending and play is.
I had to look up POM, yet another TLA. I'm familiar with the brand name Delrin.I'm starting to warm up to the direct drive/ (POM) rack teeth idea. Any good and cheap ones from suppliers in Europe?
https://en.wikipedia.org/wiki/Polyoxymethylene
UK Makerstore has it, you can get it from Aliexpress if a few week wait on shipping is OKI'm starting to warm up to the direct drive/ (POM) rack teeth idea. Any good and cheap ones from suppliers in Europe?
https://makerstore.co.uk/products/gear-rack-internal-mod1
PS I really hate the V-Wheels and eccentric spacer tension system. I bought a CNC kit with those and swapped to linear rails and bearing blocks. The wheels work but the linear rails and bearing blocks are so much better.
I have an Openbuilds Blackbox which is basically an Arduino underneath
https://openbuilds.com/builds/blackbox-motion-control-system.8320/
I can't tell you how well it works as getting it running is still in the todo list
A basic 3D printer board seems like a good option too, Marlin would be a cheap way to go. I like Klipper and the fluidd web interface myself, a Big Tree Tech Manta 4 would run it with their own Pi knock off board which plugs in.
https://openbuilds.com/builds/blackbox-motion-control-system.8320/
I can't tell you how well it works as getting it running is still in the todo list
A basic 3D printer board seems like a good option too, Marlin would be a cheap way to go. I like Klipper and the fluidd web interface myself, a Big Tree Tech Manta 4 would run it with their own Pi knock off board which plugs in.
So we need one that is commonly available, has the current capability to drive the motors we want, and the fancy TI chip that allows silentish operation? Cause I know FDM printers are damn noisy with those steppers.A basic 3D printer board seems like a good option too, Marlin would be a cheap way to go. I like Klipper and the fluidd web interface myself, a Big Tree Tech Manta 4 would run it with their own Pi knock off board which plugs in.
Actually motor noise is probably going to be our largest problem after all other dragons are vanquished.
The motor for the vertical motion would have to stay on to maintain position unless there is a well-balanced counter-weight to fight gravity. Not having a weight swinging on a string would be nice, if possible. A brake is another option, but that's another complication that would be nice to avoid. A motor that can hold its position quietly seems simplest.
Regarding the V-wheels vs. linear rails: for a CNC router, with all the cutting forces, heavy spindle, and need for accuracy down to tens of microns, V-wheels would sure seem inadequate (I'm surprised such systems persist on the market). But to hold a mic in position, and locate things within a couple of mm? Seems like the much lower weight and cost of V-wheels and Al extrusions are a good option.
Few.
Regarding the V-wheels vs. linear rails: for a CNC router, with all the cutting forces, heavy spindle, and need for accuracy down to tens of microns, V-wheels would sure seem inadequate (I'm surprised such systems persist on the market). But to hold a mic in position, and locate things within a couple of mm? Seems like the much lower weight and cost of V-wheels and Al extrusions are a good option.
Few.
- Home
- Design & Build
- Software Tools
- Klippel Near Field Scanner on a Shoestring