Good plan. And if that doesn't do it, low profile bolts could be used to gain even more space. The forces on the wheels are pretty tiny.Second gantries how about reversing the bolts? Nuts on the other sides?Head of the machine bolt on the bearing inner race. That will stop your collision.
Another small update:
Added some code to work with the scanner. And some hardware changes:
Counterweight is working. Motors can be turned off, no more whining noise:
All it took were some standard nuts:
I mounted the (bulky) arduino box:
And used a banana plug thingy instead of my protoboard to get power to the CNC shield:
It's starting to clean up nicely (for a prototype).
Added some code to work with the scanner. And some hardware changes:
Counterweight is working. Motors can be turned off, no more whining noise:
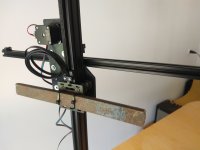
All it took were some standard nuts:
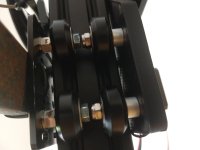
I mounted the (bulky) arduino box:
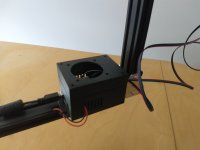
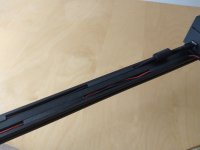
And used a banana plug thingy instead of my protoboard to get power to the CNC shield:
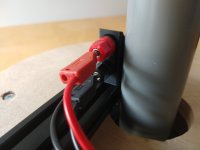
It's starting to clean up nicely (for a prototype).
I added a counter weight to the scanner. Untill now, the speaker had been acting as the counter weight.
Does anyone have any ideas about the servo and microphone cables? I would like to keep them under control and not drag them around (e.g. over the table). Depending on the position of them microphone I could have 1.4 meter of microphone cable hanging free/lying around.
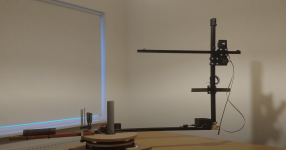
Does anyone have any ideas about the servo and microphone cables? I would like to keep them under control and not drag them around (e.g. over the table). Depending on the position of them microphone I could have 1.4 meter of microphone cable hanging free/lying around.
In the CNC world something like this is typical. They are designed for linear motion, though, so likely only a partial solution.
Maybe spiral cable wrap would be helpful as well.
Few
Maybe spiral cable wrap would be helpful as well.
Few
Of course you could do that. I would need (to buy) another microphone, microphone cable, audio interface, profiles, stepper motors, ...
Also, how do I say this... The position of a single mic is easily known relative to its starting position. A second mic would need its position known relative to the first one or one needs an algorithm to deduce that from measurements.
So using a piece of iron as a counterweight was a bit easier.
Also, how do I say this... The position of a single mic is easily known relative to its starting position. A second mic would need its position known relative to the first one or one needs an algorithm to deduce that from measurements.
So using a piece of iron as a counterweight was a bit easier.
I don't follow.Also, how do I say this... The position of a single mic is easily known relative to its starting position. A second mic would need its position known relative to the first one or one needs an algorithm to deduce that from measurements.
The second mic is just the same + 180 degrees (+ additional error correction at first setup).
Since both are connected to the same arm (beam) the relative error is basically non existent.
So it's actually quite simple.
That was my idea straight from the beginning (see couple of pages back).Just a thought, why not mirror the mic gantry so no counter weight is needed? Can also carry a second mic.
- Home
- Design & Build
- Software Tools
- Klippel Near Field Scanner on a Shoestring