HK26147 said:Speaker Builder 3/86 p30
Damn! You're on top of it.
Never saw the black fiberglass ones. But I was living in the land of Focal at the time (Paris). Maybe they didn't do them in France?
Any particular Seas driver model number?
The H1333-08/06 T18RE/XFCTV2
The crossover for this poly cone driver will be challenging enough. I don't want to think about what it would take to get the mag cone version sounding good. For that matter, I'm not even sure I can get this one to my liking, but it sure will be fun to try.
I have yet to see that shape elsewhere to use to pattern off ( a mold ).
This picture you see is a 3D model, so I don't need a mold. The file will feed into a CNC milling machine which will do all the work.
There is discussion as to merits of any exotic curving shape beyond spherical or ovoid.
There is probably a lot to it that I haven't considered. I've been thinking of ways to shape the interior so that the concave surface does not create a central focus point. I've got a few ideas, but nothing solid.
The KEF 207/2 uses a slightly ovoid(?) enclosure for the 6.5" Mid/HF driver, the B&W 802 however looks slightly more elongated on it's Kevlar driver and much more so on the tweeter portion.
That's the part I'm having a hard time with. I don't know how to model it, or even consider it conceptually. Someone here mentioned a ripple tank. It seems like an interesting idea. I'm not sure if the results apply though. For instance, a ripple tank will let you visually track the wave, but what happens when you apply a set frequency instead of a single pulse?
Makes me want to buy a waterproof speaker and see what happens.
I'm hoping someone a whole lot smarter than me will chime in.
In the past I put a lot of effort into deadening the cabinet, but never thought much about undamped waves passing through the cone.
I have designed and built some pretty unique/effective racing mufflers in the past, but I am having a hard time applying the same concepts to a speaker.
Maybe this thread should turn into a discussion of killing what comes off the back side of the cone as opposed to just making a rigid non-resonant cabinet.
BTW, if you look at the top view of the enclosure, you will see that it rolls back rather abruptly where it meets the driver frame. I wonder if I should re-shape it so that the radius starts gradually right from the edge of the driver?
All of this stuff is easy to change at this stage so I will not start making sawdust until I have some confidence that the shape is correct both internally and externally.
Any input is appreciated.
PY
I re-designed the basic external shape to get a better blend with the driver face.
I also have less of a sphere, and I hope that this will make it easier to control reflections inside the cabinet.
Follow the link to see the new shape.
www.yawpower.com/seascoax.html
I also have less of a sphere, and I hope that this will make it easier to control reflections inside the cabinet.
Follow the link to see the new shape.
www.yawpower.com/seascoax.html
injectordynamic
Some of the theoretical questions - including the advantages ( if any ) of complex curves vs simple curves has been discussed:
http://www.diyaudio.com/forums/showthread.php?threadid=136967
I envy your access to a CNC; for me, that is not an option.
I have had to resort to hand fabrication.
On the plus side after close to 20 years of making stage props and instruction in mask making, has provided me with some other options.
Casting and Mold making using plater is inexpensive and low tech.
So If I can find an existing shape ( there are a lot more now), it is very easy to make plaster negatives and positives of a shape and modify it as desired.
Labor intensity - like creating a concept car prior to being copied for replication. But it is about as cheap as possible and can be done entirely without sophisticated tools. Limited to the hand skills of the builder.
panomaniac:
Curved enclosures have been an interest of mine since I became aware of diffraction..
Originally as part of a project I did on the use of polarized light in stress analysis. When diffraction became a topic of discussion in SB:
SB 2/84 p34 "The Egg and I" and the SB 3/86 issue which also has another article called "The Unbox Enclosure".
Both of the authors had chose the "stacked wood rings" technique and sanded down the "raster" to smooth shape.
While the exterior is smooth, the interior surface remains "stair-cased" which may/or may not have an effect.
IMO: the appropriate internal dampening will have a greater effect than the subtle differences in the internal shape.
Some of the theoretical questions - including the advantages ( if any ) of complex curves vs simple curves has been discussed:
http://www.diyaudio.com/forums/showthread.php?threadid=136967
I envy your access to a CNC; for me, that is not an option.
I have had to resort to hand fabrication.
On the plus side after close to 20 years of making stage props and instruction in mask making, has provided me with some other options.
Casting and Mold making using plater is inexpensive and low tech.
So If I can find an existing shape ( there are a lot more now), it is very easy to make plaster negatives and positives of a shape and modify it as desired.
Labor intensity - like creating a concept car prior to being copied for replication. But it is about as cheap as possible and can be done entirely without sophisticated tools. Limited to the hand skills of the builder.
panomaniac:
Curved enclosures have been an interest of mine since I became aware of diffraction..
Originally as part of a project I did on the use of polarized light in stress analysis. When diffraction became a topic of discussion in SB:
SB 2/84 p34 "The Egg and I" and the SB 3/86 issue which also has another article called "The Unbox Enclosure".
Both of the authors had chose the "stacked wood rings" technique and sanded down the "raster" to smooth shape.
While the exterior is smooth, the interior surface remains "stair-cased" which may/or may not have an effect.
IMO: the appropriate internal dampening will have a greater effect than the subtle differences in the internal shape.
since you know how to make a mold you are a step ahead...
now to create the piece to make the mold is not that bad either...
these are pics taken from a car audio build done by Chris Yato...but you get the idea
now to create the piece to make the mold is not that bad either...
these are pics taken from a car audio build done by Chris Yato...but you get the idea
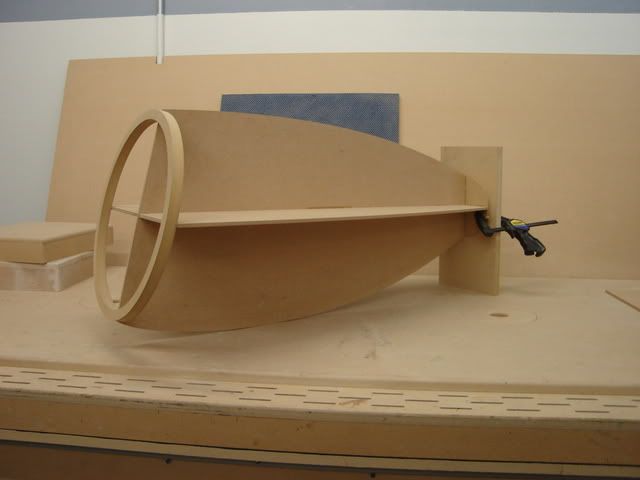
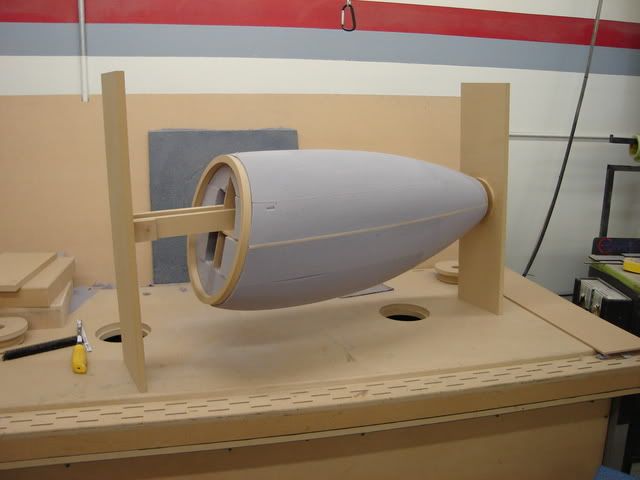


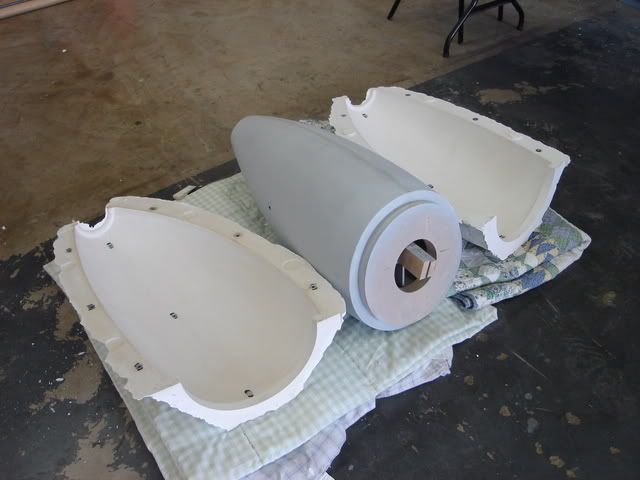
HK26147 said:injectordynamic
Some of the theoretical questions - including the advantages ( if any ) of complex curves vs simple curves has been discussed:
http://www.diyaudio.com/forums/showthread.php?threadid=136967
I envy your access to a CNC; for me, that is not an option.
I have had to resort to hand fabrication.
On the plus side after close to 20 years of making stage props and instruction in mask making, has provided me with some other options.
Casting and Mold making using plater is inexpensive and low tech.
So If I can find an existing shape ( there are a lot more now), it is very easy to make plaster negatives and positives of a shape and modify it as desired.
Labor intensity - like creating a concept car prior to being copied for replication. But it is about as cheap as possible and can be done entirely without sophisticated tools. Limited to the hand skills of the builder.
panomaniac:
Curved enclosures have been an interest of mine since I became aware of diffraction..
Originally as part of a project I did on the use of polarized light in stress analysis. When diffraction became a topic of discussion in SB:
SB 2/84 p34 "The Egg and I" and the SB 3/86 issue which also has another article called "The Unbox Enclosure".
Both of the authors had chose the "stacked wood rings" technique and sanded down the "raster" to smooth shape.
While the exterior is smooth, the interior surface remains "stair-cased" which may/or may not have an effect.
IMO: the appropriate internal dampening will have a greater effect than the subtle differences in the internal shape.
While there is plenty of information available for designing the correct size rectangular speaker enclosures, I haven't seen able find anything for spheres.
Does anyone know if there is an optimum diameter of sphere for a particular size driver and what about the internal volume? Use the recommended volume for a sealed rectangular enclosure or what?
I have a couple of 6 1/2 inch Kef Uni-Q drivers which want to build spheres for. Any suggestion regarding what size I should build the spheres?
Does anyone know if there is an optimum diameter of sphere for a particular size driver and what about the internal volume? Use the recommended volume for a sealed rectangular enclosure or what?
I have a couple of 6 1/2 inch Kef Uni-Q drivers which want to build spheres for. Any suggestion regarding what size I should build the spheres?
I posted a link to SpeedCrunch...
This "calculator+" has some geometric solids already defined including Spheres:
Volume is volume regardless of the shape.
So it fairly straightforward to set up a spreadsheet for any solid provided you got the formula.
Volume of a sphere = (4*Pi*Radius^3)/3
Using Speedcrunch: a sphere 8" in diameter = 268 cu in.
a sphere 10" diameter = 523.6.
A 12" 904.8, etc.
If you assume a 12" O.D. and choose a .5" wall thickness for instance.
Radius = 5.5" ( instead of 6" ) and volume is 696.9. cu in.
This "calculator+" has some geometric solids already defined including Spheres:
Volume is volume regardless of the shape.
So it fairly straightforward to set up a spreadsheet for any solid provided you got the formula.
Volume of a sphere = (4*Pi*Radius^3)/3
Using Speedcrunch: a sphere 8" in diameter = 268 cu in.
a sphere 10" diameter = 523.6.
A 12" 904.8, etc.
If you assume a 12" O.D. and choose a .5" wall thickness for instance.
Radius = 5.5" ( instead of 6" ) and volume is 696.9. cu in.
HK26147 said:I posted a link to SpeedCrunch...
Thanks for the reply but working out the volume of a sphere I can already do and that is not the problem.
The problem is what size to make the sphere in the first place. After all for example, I could put a 6 inch driver into any size of sphere that it would fit into, an 8 inch, 10 inch, or even a 36 inch sphere for that matter.
What I am really asking is what is the optimum size sphere for a particular sized driver that will enable the external curve to minimise diffraction as much as possible?
One could imagine a 6 inch driver in a 6 inch sphere there would be practically no curve, it would be all speaker. Similarly the same driver in a 36 inch sphere would practically be all curve and very little speaker. There must be some optimum external size surely.
Has anyone done any studies of this and come up with some recommendations do you know?
For the internal volume I will just make it the same as what is recommended in a speaker enclosure design programme. I can do this independently of the exterior diameter by just making the walls thicker or something.
The general rule is that obstacles capable of diffracting (bending) sound must be large compared to the wavelength of the sound involved.
500Hz has 27" wavelength
1125Hz has a 13.5" wavelength
1.5" - a typical round-over radius = 9Khz.
6" = 2250 Hz
12" =1125 Hz
At what point ( wavelength size vs radius ) that the effects starts to manifest, or if it has been quantified - I don't know.
Curves on the scale we are talking about would have to considered in the range of HF, if the above applies.
500Hz has 27" wavelength
1125Hz has a 13.5" wavelength
1.5" - a typical round-over radius = 9Khz.
6" = 2250 Hz
12" =1125 Hz
At what point ( wavelength size vs radius ) that the effects starts to manifest, or if it has been quantified - I don't know.
Curves on the scale we are talking about would have to considered in the range of HF, if the above applies.
HK26147 said:The general rule is that obstacles capable of diffracting (bending) sound must be large compared to the wavelength .
OK thanks, so there doesn't appear to be any quantitative information available. You seem to have a good grasp of these things, for my 6 1/2 inch drivers what do you think the diameter of the sphere should be?
Please give me your best guesstimate.
I have got an 8 inch ball which I was going to make a mould from, perhaps it should be bigger, I don't know. What do you think?
My reading of the B&W Nautilus design is they are using a small possibly elliptical horn behind the speaker to ensure that all of the rear wave energy keeps going down the tube and can't be reflected. Then it is absorbed by stuffing.injectordynamic said:In the past I put a lot of effort into deadening the cabinet, but never thought much about undamped waves passing through the cone.
I have designed and built some pretty unique/effective racing mufflers in the past, but I am having a hard time applying the same concepts to a speaker.
Maybe this thread should turn into a discussion of killing what comes off the back side of the cone as opposed to just making a rigid non-resonant cabinet.
B&W Nautilus
Just clone that. I reckon it could be done nearly as effectively using an approximated elliptical flare made from flat sheet similar to what is done with front horns used for midbass.
Someone else has been here too.
http://home.wanadoo.nl/dezaire/ultiem/ultimate.htm
cirrus18 On page 296, 297 of
Loudspeakers By Philip Newell, Philip Richard Newell, Keith Holland
Are graphs 9.23 & 9.24 showing the vertical directivity and cepstrum analysis of a cab with the tweeter 7cm from a baffle edge.
As noted a problem @ .4 ms, the reciprocal of this period indicates a 2500Hz frequency ( see the dips @ 2500Hz and another @ 5Khz in fig 9.23 ).
7cm = 1/2 wavelength of 2500Hz.
I'd be tempted to reverse engineer what KEF has already done.
Otherwise my best guess would be no smaller than 8".
I noticed that KEF uses what appears to be an ovoid ( not a perfect sphere ), which I would also be tempted to replicate. It's elongation allows some depth, so the sphere does not have to be as big
Loudspeakers By Philip Newell, Philip Richard Newell, Keith Holland
Are graphs 9.23 & 9.24 showing the vertical directivity and cepstrum analysis of a cab with the tweeter 7cm from a baffle edge.
As noted a problem @ .4 ms, the reciprocal of this period indicates a 2500Hz frequency ( see the dips @ 2500Hz and another @ 5Khz in fig 9.23 ).
7cm = 1/2 wavelength of 2500Hz.
I'd be tempted to reverse engineer what KEF has already done.
Otherwise my best guess would be no smaller than 8".
I noticed that KEF uses what appears to be an ovoid ( not a perfect sphere ), which I would also be tempted to replicate. It's elongation allows some depth, so the sphere does not have to be as big
HK26147 said:I'd be tempted to reverse engineer what KEF has already done.
Otherwise my best guess would be no smaller than 8".
[/B]
Well, I have made a couple of 8 inch spheres for my KEF speakers and now that they are completed they looked a little small to me. Not much curve relative to the size of the speaker.
Even so, I have tried them out and I am very pleased with the results. Can't notice any better frequency response in anyway, but definitely a much better soundstage. In fact an amazingly better one, which really adds life to the music. Hard to define exactly, but a very noticeable improvement.
I looked at the Nautilus design and they have a lot bigger sphere relative to the diameter of their driver. I measured it at approximately 2.35 bigger. Which equates to instead of only a 200 mm sphere which I have made but a 350 mm one. So the next project is to make some larger spheres and try them out.
The method of construction I used was fairly simple. I noticed in the supermarket they had different size plastic mixing bowls and I bought 4 220 mm ones. Only 99p each. So that definitely didn't break the bank.
From a supplier of fibreglass and resins and I got some 400 g chopped mat and a bag of Crystacast, a plaster casting powder.
I started off by spraying the INSIDE of the bowls black. Cut 2 circular plywood rings of the correct size to mount the speakers on, placed them inside 2 of the bowls and plastered the INSIDE of the bowls (one layer at a time) with two layers of chopped mat. Let the first layer dry for approximately threequarters of an hour before laying up the next layer.
Plastered up the remaining two bowls, with two layers of chopped mat.
When the bowls were dry, cut-off the now surplus bowls bottoms so as to be able to mount the speakers. I also cut off the bowls rims. Stuck the two halves together with No Nails. Made an elastic band from a bicycle inner tube to cover the bowls joints.
Working from the inside of the bowl leaves a professional shiny exterior that requires no finishing whatsoever.
Attachments
cirrus18 said:
I noticed in the supermarket they had different size plastic mixing bowls a
Attachments
Nice work and quick too.
I suppose those drivers are not cheap?
Like you said:
Since then I have been watching for spheres approx 12" diameter.
My wife ( knowing what I'm looking for ) found a flared standing lamp that included packing material that may provide a closer approx.
to the B&W shape.
I suppose those drivers are not cheap?
Like you said:
That reflects my opinion of the few sphericals and ovoids I tried.but definitely a much better soundstage. In fact an amazingly better one, which really adds life to the music. Hard to define exactly, but a very noticeable improvement.
Since then I have been watching for spheres approx 12" diameter.
My wife ( knowing what I'm looking for ) found a flared standing lamp that included packing material that may provide a closer approx.
to the B&W shape.
HK26147 said:
I suppose those drivers are not cheap?
Yes, I suppose if you bought these drivers direct from KEF they would be. But if you were interested in getting a pair of these drivers with their inbuilt tweeters, eBay might be the answer.
I've seen different models of the Q series going for ridiculously low prices. Might be worth picking up a pair, remove the drivers and install them in a sphere.
- Status
- This old topic is closed. If you want to reopen this topic, contact a moderator using the "Report Post" button.
- Home
- Loudspeakers
- Multi-Way
- Techniques and Materials for Spheres and Ovoids