The LS3/5A is not a good example. It reaches only slightly below 100 Hz, a sub rarely above 100 Hz.
2 completely different scenarios.
Given the small size of the LS3/5A they have to work really hard to push resonances below 100Hz (where a woofer would definitly excite them), but the last pairs i heard stil sounded kinda boxy.
dave
2 completely different scenarios.
Given the small size of the LS3/5A they have to work really hard to push resonances below 100Hz (where a woofer would definitly excite them), but the last pairs i heard stil sounded kinda boxy.
dave
In a subwoofer one can sually keep the dimensions small enuff that there are no standing waves that will ever get excited. The issues are box vibrations and balooning.
dave
Hey Dave,
I would love to get your feedback (and criticism) of a solutution I;ve been using for the past 10 (or so) years.
Its been various iterations similar to this:
https://www.diyaudio.com/forums/att...1617302737t-sub-passive-radiator-speaker2-jpg
Its a small back wall, hence stiff
Curved side walls, stiff again
Very solid facia
The curved insides reduce standing wave and provide stiffness.
The build has a few steps, but its pretty easy.
I sketch the top & bottom in MS Viso. That also calculates the area for me, so x the hieght give me volume.
I print the top, full size and trace onto 1/2" MDF
Cut it out with the bandsaw and trim it up with the disc sander
Pin nail to the bench, put another MDF on top and trace it out with the router and a trim bit. Make 3 perfectly identical copies.
Cut the front of 1/2" BB. same for the back.
Build a skeleton, of front, back, top & bottom. Glued and pin nailed.
Once its dry, I wrap 1/4" mdf around the sides.
start at the front, pin nail it heavily, work it to the back. Lots of glue.
I leave an overhang.
Normally its 2 layers, laminated, of MDF = 1/2" of curved MDF for the sides.
Plenty strong.
I did 3 layers once, VERY strong.
Tops & bottoms get flushed up with the router trim bit.
Front and back with a belt sander. Another reason to use BB on the front and back.
Thats about it. Except that I usually add another 1/2" layer of BB on the front.
The finish is often real wood veneer (in this case black walnut), sometime funky melamine. A few times auto paint - I drop them off at a local shop that sprays them for me.
Then cut the openings for the drivers with a router.
The BB is nice because the screws really grab hard.
This yeilds a very strong stiff cabinet, reduced standing waves, easy build and it looks cool (not a ******* box) 🙂
I've built about 20 of these, sealed and ported.
Normally its an MTM configuration. I like the Scanspeak 8545, but have used other. A big surpise was the Peerless SDS line. Cheap, but pretty good.
Power is always bi-amp, normally pro audio. My favourite is Crown D75's with active crossover so I can play with the settings.
My latest challenge is the same configuration but with a Heil AMT1 as tweeter as an MTM. Its proving to be a tough build....
Attachments
PE had a box similar in shape & construction. 5-ply MDF plywood. Worked fairly well, but the MDF was real cheesy and pieces would chip off if you looked at them the wrong way.
A first attempt, simialr to yours but using thin ply did not work out well and was burned.
Next up 2 layers rubber ply plus a thin layer of something smooth for extra stiffeness and to host the veneer, some expoxy/glue and a vacuum bag. Very stiff, fairly light, a lot of work.
We used these pieces to make 2 differen tloudspeakers, one much like yours in shape.
dave
A first attempt, simialr to yours but using thin ply did not work out well and was burned.
Next up 2 layers rubber ply plus a thin layer of something smooth for extra stiffeness and to host the veneer, some expoxy/glue and a vacuum bag. Very stiff, fairly light, a lot of work.
We used these pieces to make 2 differen tloudspeakers, one much like yours in shape.

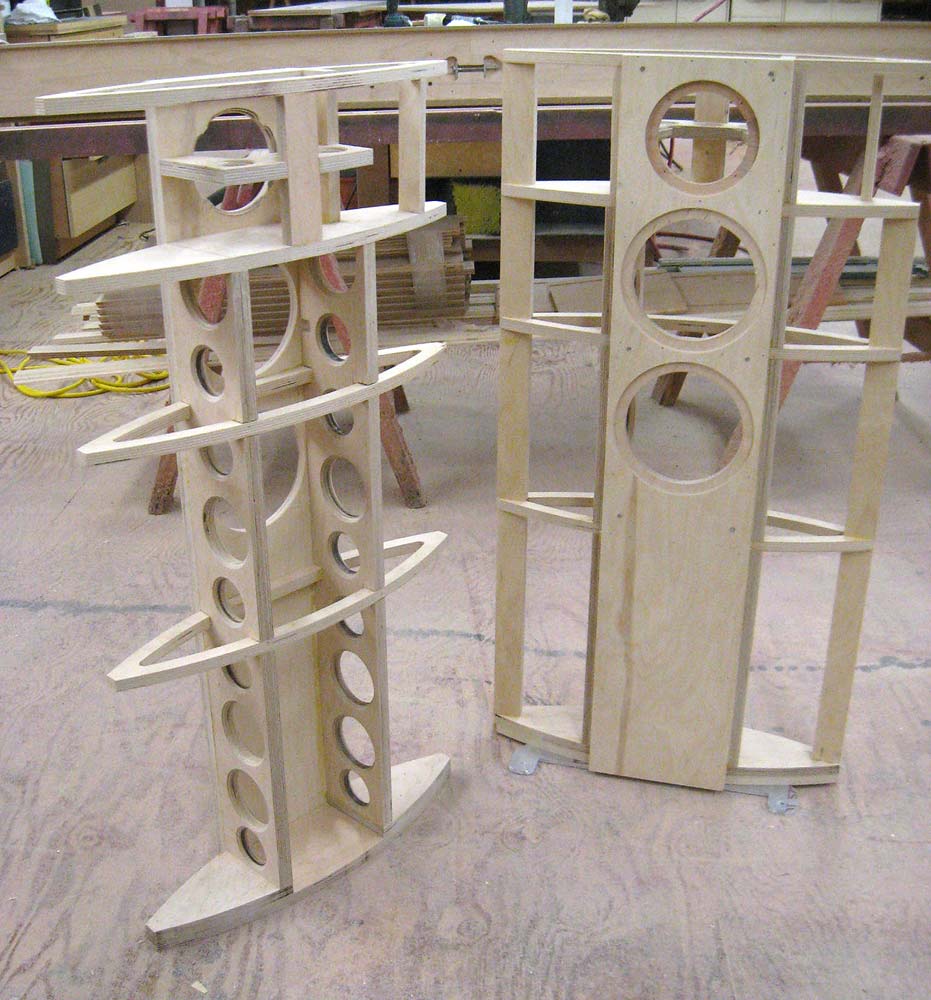
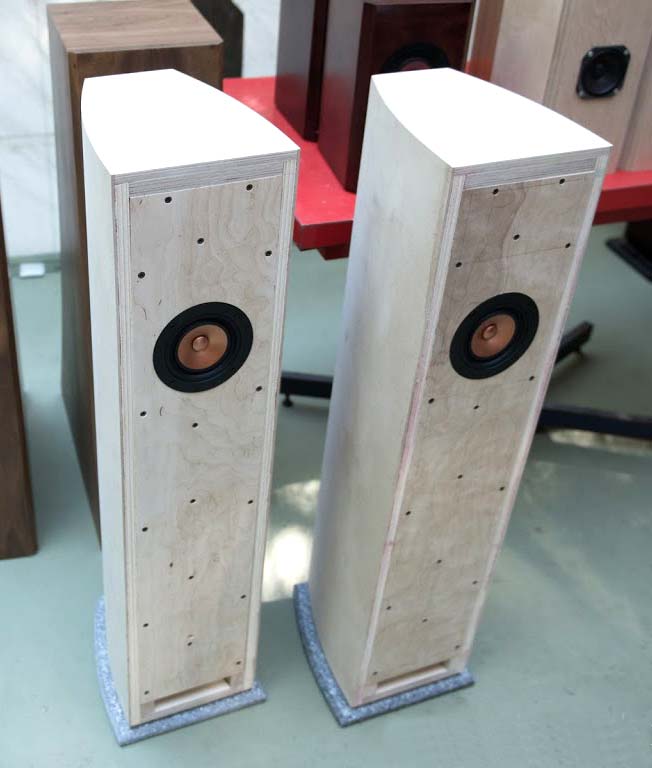
dave
Incredibly inspiring. Something to aim for as the top of an iceburg. Youre not only above buoyant here. Youre the side of the pendulum swinging opposite everything else!! Wow😱
Last edited by a moderator:
The whole reason i am on this journey is to listen, learn, inspire, and coach. Incredibly satisfying.
Thanx.
dave
Thanx.
dave
Seems to be some confusion here between standing waves (interior bounce) and panel vibrations (modified by construction factors).
Standing waves are simple to address with a million options from stuffing with a pile of old clothes to high-tech foam.
Despite the endless ink spilled on panel vibration, prolly not worth worrying about for anything over half-inch braced plywood.
What about this Ben? (Btw i like the sequestered long monster pipe very much but it also lead to finding the ‘others?)), hence the idea: why kill the standing wave if its an exact piece of the full wave in the pipe and the pipe is driven in its own pressure node? The exit of the pipe fed by its own self inflicted 90 degrees off (affectively) from a polar opposite fed from that distance in 90 degrees of its own to exit. Clearly a PITA to consider. But only for the imediate area to a few (?) 1/4,3,5,7,9 versions of the fournier stacks of them??) out to 7200 degrees ? Okay, 900?
(Maybe refer to direct radiator vs qw vent at Fb as a start (90 outa phase at exit)) but then fold it twice and the first fold is at the pressure null of the full length ‘pipe’ as is the driver entry.. and then its 165 cm fold at driver entry, 150 and 150 at the exit with 15 cm to look at as after.... kindof like the yellow depicts in the picture. Horn response then yields the vas and Qes required CSA at length for Fs/Fb.
Thr result is ?
Attachments
Seems to be some confusion here between standing waves (interior bounce) and panel vibrations (modified by construction factors).
Standing waves are simple to address with a million options from stuffing with a pile of old clothes to high-tech foam.
Despite the endless ink spilled on panel vibration, prolly not worth worrying about for anything over half-inch braced plywood.
The whole reason i am on this journey is to listen, learn, inspire, and coach. Incredibly satisfying.
Thanx.
dave
Please dont ever stop🙂
- Home
- Loudspeakers
- Subwoofers
- Standing wave down firing square base sub