I have used the technique of coupling a bass driver in a sub with the back of the cabinet in hopes of holding the driver as a whole in place, not so much structurally but making a connection to a higher mass for the purpose of draining excess vibration.
Are there no drivers on the market, actually made for this? Just a captive nut on the back would be useful. Most of us have rear access through the terminal plate. Ample to spin some lockrings. Thinking ahead further.. I could retrofit a height adjustable kitchen cupboard leg. Or something like.
I guess if you want a driver off the front baffle, it would be easier to just have two front ones. In a typical build, we wouldn't recess the driver, we would surface mount. Perhaps even on a spacer ring. Then add a second baffle ahead of the first, that is air-gapped from it. That seems easier, as you still get a good hold of the driver. The new front could be machined a bit like a shallow (few millimeter) horn. It wouldn't take a lot to make up such a baffle and hold it to an existing speaker, to see if box noise was meaningfully reduced.
I guess if you want a driver off the front baffle, it would be easier to just have two front ones. In a typical build, we wouldn't recess the driver, we would surface mount. Perhaps even on a spacer ring. Then add a second baffle ahead of the first, that is air-gapped from it. That seems easier, as you still get a good hold of the driver. The new front could be machined a bit like a shallow (few millimeter) horn. It wouldn't take a lot to make up such a baffle and hold it to an existing speaker, to see if box noise was meaningfully reduced.
Coaxial drivers for cars usually have a hole through the center pole piece that can be used to mount the driver, or bolt it to a brace or weight. I did manage to drill and tap a hole in the back of a driver, purely as an experiment.
Careful, if the magnet is hanging off the back of the basket you have to be very careful you don’t start pullimg it off the basket with a bolt thru the pole-piece.
dave
dave
Not for off the shelf sales normally.Are there no drivers on the market, actually made for this?
B&W FST midrange drivers are fx.
Magico xxhave seen a few older drivers with thread in the back.
One can also clamp/magnet mount it.
\
Or decouple the woofer frome baffle, with appropriate gaskets and fasteners.
Yet make it contact the bracing in the back when mounted under tension. Use a "CLD" material in a sandwich behind it to rest against, firm anchor at bracing yet still decoupled.
Or clever use of CLD bracing.
Did you ever use a screw to lock a door? Just screwing it in the gap, so the treads cut both the frame and door.
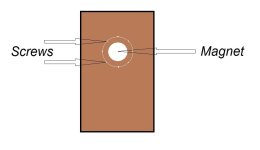
The pic is a center baffle/brace. Access through a port or terminal plate would be needed for this idea. The magnet cutout should be a bit too big. Allowing the driver to compress it's front gasket system to no specific size. The magnet will find where it wants to be in the cutout. Then comes the quite permanent sealant applied through the terminal plate. Shims if you like. This sort of solid gluing solution, once all is in place should mean nothing is being pulled on, pushed on, or left to move about. The twist to this story, is the driver can still be removed. It's basically been glued into a ring, and the ring can be unscrewed, and come out with the driver.
Really low precision needed. The ring can be done with a jigsaw. The kerf being missing, doesn't really matter. The screws need it.
If it was removed and replaced, the screws would need going back the same, to avoid unwanted leverage. Or bust the glue off, and maybe even make a new ring. Making the use of hole saws a consideration, to repeat manufacture easily.
My minds not really on decoupling from the brace. The speaker has to attach to something. Anything I take away from the brace, will move to the front baffle. Or lead to movement in the driver. I do want to hold it tight, don't I ?
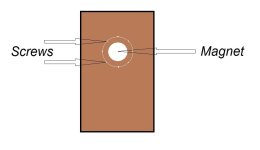
The pic is a center baffle/brace. Access through a port or terminal plate would be needed for this idea. The magnet cutout should be a bit too big. Allowing the driver to compress it's front gasket system to no specific size. The magnet will find where it wants to be in the cutout. Then comes the quite permanent sealant applied through the terminal plate. Shims if you like. This sort of solid gluing solution, once all is in place should mean nothing is being pulled on, pushed on, or left to move about. The twist to this story, is the driver can still be removed. It's basically been glued into a ring, and the ring can be unscrewed, and come out with the driver.
Really low precision needed. The ring can be done with a jigsaw. The kerf being missing, doesn't really matter. The screws need it.
If it was removed and replaced, the screws would need going back the same, to avoid unwanted leverage. Or bust the glue off, and maybe even make a new ring. Making the use of hole saws a consideration, to repeat manufacture easily.
My minds not really on decoupling from the brace. The speaker has to attach to something. Anything I take away from the brace, will move to the front baffle. Or lead to movement in the driver. I do want to hold it tight, don't I ?
Absolutely, but a little resistive freedom can be useful. The thing is you don't want to let it rock against the baffle. If it needs to have some give, allow it to happen in primarily an axial direction for example.I do want to hold it tight, don't I ?
Just to take another example, pretty much the same basic principles apply.My minds not really on decoupling from the brace. The speaker has to attach to something. Anything I take away from the brace, will move to the front baffle. Or lead to movement in the driver. I do want to hold it tight, don't I ?
One should also rigidly mount a large machine with rotating parts, yet they are installed and leveled on anti vibratory machine feet for a reason.
Not to transmit and excite structural vibrations, and dampen the systems self resonant frequency so it is not excited and causes ringing both auditory and destructive for the equipment in some cases.
Do you think a 500-10 000kg machine assembly is not rigidly attached to the ground, because it is vibration damped with 'non rigid' materials between the two?
Who said you do not want to mount/hold it tight?
There are ways to do both.
"As we have seen from various experimental results the 'relative movement' of the frame is insignificant, as is the loss of output from the driver"
Without the decoupling all the energy is transferred into the baffle/bracing and will excite panel resonances of varying amplitude.
The earlier referenced document also shows what affect it has on the drivers mechanical system.
As the resonance frequency will 'make the magnet move' in relation to the VC.
See the linked thread below, plenty of good info. And posts #113, and #264 clarifies the previously linked document by the author himself.
A. Jones from when he was working for Pioneer/TAD on the coaxes and TAD reference series.
how much bracing i should do, is there any limitations for it?
which sort of bracing is effective and please provide me some picture of this?
any type of wood can be used for bracing?
how should i screw brace with speaker cabinet?
if i want to build speaker with 2 woofer then how much bracing is need and which position i should brace in the cabinet?
which sort of bracing is effective and please provide me some picture of this?
any type of wood can be used for bracing?
how should i screw brace with speaker cabinet?
if i want to build speaker with 2 woofer then how much bracing is need and which position i should brace in the cabinet?
- dipankar862
- Replies: 337
- Forum: Multi-Way
And still the best starting point for fx a bass driver is to make the cabinet stiff enough to have the resonance frequency outside of the bandwidth.
But that does not mean that driver induced vibrations can't excite panel resonances, not that everyone finds that objectionable though, some like the 'coloration' it adds even.
If you look here you can use the spreadsheet to 'approximate' the amount of energy generated by the driver, and some info on mounting options etc.
https://www.linkwitzlab.com/frontiers_2.htm
And still it is all a choice of compromises vs how much effort is worth putting into it.
The larger the panel surfaces are and the higher the drivers generated force is the more important it gets.
There is in some cases also generated high q resonances by the frame resonating due to construction/design and being tightly clamped to a baffle with no decoupling/damping as an example.
What is the 'better' solution i guess is still very much debatable.
Attachments
-
202moriyasu2043.pdf1.5 MB · Views: 28
-
AES_Convention_Paper_Construction_of_Lightweight_Loudspeaker_Enclosures.pdf1.4 MB · Views: 18
-
axpress 02-2008 Driver induced vibrations.pdf4.3 MB · Views: 26
-
Speaker-Builder-2000-03.pdf7 MB · Views: 29
-
Baffle Vibrations in Open Baffle Dipole Loudspeakers Kopie.pdf917.2 KB · Views: 25
Last edited:
One should also rigidly mount a large machine with rotating parts, yet they are installed and leveled on anti vibratory machine feet for a reason.
I suspect the machine itlf isas rigid as needed for thoisands of hoursof use. The feet are between the machine and what it sits on. This tends to be good for keeping the floor isolated from the box.
I am skepticall of using it as an analogy for mounting a woofer in its box.
The only time i can see decoupling the baffle is in things like the Fujitsu-10 Eclipses — were the driver is either acnchored to a heavy base, or looks like an elaborate absorber system — the OBs where the drivers are mounted on a verticle rear structure.
dave
- Home
- Loudspeakers
- Multi-Way
- Should bass driver rest on bracing?