I'm a bit surprised that you mention the cantilever suspension as being a (substantial) heat conductor.
In general elastic polymers are not known for their good heat transfer.
Yes, butyl rubber is not a good thermal conductor, but it doesn't need to be in this situation. It is at least in reasonable contact, and, in addition to other losses, is where modest heat flows ensuring barely notable temp rises for the cantilever in practice. This concurs with what I found in a rough measurement some years ago.
LD
I do want to restate that all these extrapolations on the tip-side are to estimate how much heat is being transferred into the vinyl. Let's not lose track of the overarching goal--elucidating means to minimize surface noise. 😉
Just done a rough first pass spin down test on the Xerxes. Turning by hand with a very scientific count of 'one elephant, two elephant' to get a rough 2 second revolution took 200 seconds to come to a stop, although the last 45 seconds was very slow. But certainly a candidate for friction testing if I can work out a way to drive it to speed and then measure things accurately.
Oh and protect the veneer from dribbles!
Oh and protect the veneer from dribbles!
I do want to restate that all these extrapolations on the tip-side are to estimate how much heat is being transferred into the vinyl. Let's not lose track of the overarching goal--elucidating means to minimize surface noise. 😉
Yes. Thesis is that friction on the tip-side correlates with noise, especially crackle-pop type. So understanding, as best possible, what goes on at the interface can only help I figure.
LD
Just done a rough first pass spin down test on the Xerxes. Turning by hand with a very scientific count of 'one elephant, two elephant' to get a rough 2 second revolution took 200 seconds to come to a stop, although the last 45 seconds was very slow. But certainly a candidate for friction testing if I can work out a way to drive it to speed and then measure things accurately.
Oh and protect the veneer from dribbles!
Gutters. 🙂 I would think any simple sensor light/magnetic making a pulse that could be recorded on a sound card would give a pretty accurate run down count and even a radial velocity vs time. Could also do a reflected image of a strobe disk.
Last edited:
Somewhere at the beginning of this thread, it was mentioned that all LP manufacturers apply steep 30 Hz filtering to the audio signal.
A Paper from Channel D, called http://www.channld.com/aes123.pdf,
tells a different tale.
See figure below.
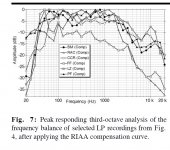
The lines represent frequency content of different recordings. Especially PF and RAC show no obvious signs of filtering.
It concerns Pink Floyd, whish you were there on Columbia and Svatioslav Richter, Rachmaninoff on MHS.
So when measuring resonance, one has to be careful measuring this while at the same time a spectral content, either white noise or music, is active.
Hans
A Paper from Channel D, called http://www.channld.com/aes123.pdf,
tells a different tale.
See figure below.
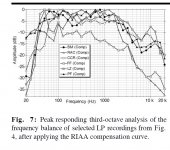
The lines represent frequency content of different recordings. Especially PF and RAC show no obvious signs of filtering.
It concerns Pink Floyd, whish you were there on Columbia and Svatioslav Richter, Rachmaninoff on MHS.
So when measuring resonance, one has to be careful measuring this while at the same time a spectral content, either white noise or music, is active.
Hans
Last edited:
Turning by hand with a very scientific count of 'one elephant, two elephant' to get a rough 2 second revolution
No no no Bil.
It’s ‘one elephant, one elephant’ for exact timing.
Use your fingers for counting

George
So when measuring resonance, one has to be careful measuring this while at the same time a spectral content, either white noise or music, is active.
To an extent, but the LF cutoff frequency for programme material is always obvious, and avoids the LF cart-arm resonance for self-evident reasons. In A/B tests such as wet-v-dry tests where spectrum of intentional content doesn't change but LF cart-arm spectrum does, this is especially obvious as in the several examples I posted on this thread.
Part of what makes vinyl special is that mastering engineers break rules, but they're not stupid !
LD
Gutters. 🙂 I would think any simple sensor light/magnetic making a pulse that could be recorded on a sound card would give a pretty accurate run down count and even a radial velocity vs time. Could also do a reflected image of a strobe disk.
That was the plan. Would be much easier on one of my technics as you both the strobe markings on the platter and the FC signal pickup. But anything I do will be helpful for other things I want to play with. Laser printers make this so much more easier than the old days (at least for those of us who didn't have HP plotters to hand. Although I still have days when I reckon a rubylith cutter would be useful...
Although I still have days when I reckon a rubylith cutter would be useful...
No! 😀
Just done a rough first pass spin down test on the Xerxes. Turning by hand with a very scientific count of 'one elephant, two elephant' to get a rough 2 second revolution took 200 seconds to come to a stop, although the last 45 seconds was very slow. But certainly a candidate for friction testing if I can work out a way to drive it to speed and then measure things accurately.
Oh and protect the veneer from dribbles!
Yes. Need to take care not to harm a perfectly good TT in the making of this movie, so to speak. Irony is TTs with good bearings and high inertia platters tend to be good turntables by definition.......
For platters with an inaccessible belt, I improvised a rim drive using a hand held motor with a rubber O ring over its drive pulley. Holding this against the rim of the platter span the platter to a definite, repeatable speed. It worked well. However, it was definitely a non-aim to scratch the rim of the platter, so the rubber O ring was essential !
Perhaps the best indirect thing to come out of it is a health check for yer spindle bearing, which already seems fit and well for your Xerxes, Bill.
File under M for misadventure !
LD
Can friction be tested/calculated if one can measure the current draw required with and without load of stylus on running platter ?
Regards.
Regards.
Can friction be tested/calculated if one can measure the current draw required with and without load of stylus on running platter ?
Regards.
Theoretically yes. But in practice there is so little power difference associated with stylus-groove friction, that it would seem impossible to resolve by measurement of motor current I think. The vast majority of TT motor input power goes toward losses in the motor itself, and this seems likely to swamp the tiny power associated with stylus-groove friction.
LD
Just done a rough first pass spin down test on the Xerxes. Turning by hand with a very scientific count of 'one elephant, two elephant' to get a rough 2 second revolution took 200 seconds to come to a stop, although the last 45 seconds was very slow. But certainly a candidate for friction testing if I can work out a way to drive it to speed and then measure things accurately.
Oh and protect the veneer from dribbles!
You should try to pick up one of the old idler wheel turntables and disengage the idler when up to speed.
A trip to the local dump could produce one but you will have to dig deep, down below the analog tv's , dial telephones and typewriters. You may also look for an old darkroom timer. 😉
What is the opinion as to whether ambient temperature makes a difference to surface noise ? I have never measured, but subjectively have sometimes wondered whether vinyl is quieter in the summer ?
LD
LD
What is the opinion as to whether ambient temperature makes a difference to surface noise ? I have never measured, but subjectively have sometimes wondered whether vinyl is quieter in the summer ?
LD
You probably need to deconvolve the change in the rest of the system with temperature/humidity. I've had speakers that changed dramatically with season.
Just supposing that the mind is not playing tricks and there is a reduction of surface noise when playing a wet vinyl disc. Could this be caused by HYDROPLANING, which may also reduce required groove information?
Just supposing that the mind is not playing tricks and there is a reduction of surface noise when playing a wet vinyl disc. Could this be caused by HYDROPLANING, which may also reduce required groove information?
It would have to be some trick! I acknowledge expectation bias, but there are limits beyond which effects have to be classed 'obvious' because they are just that IME. And in any event are backed by measurements, though fair enough Hans can't reproduce this in a one-off for reasons unkown.
Hydroplaning, sure perhaps. Frequency response, thd, IMD, trackability, pitch stability, noise floor either improve or aren't adversely affected (by measurement). For this to be true, a stylus has to better follow the locus of the groove base: it's as simple as that. A thin film of lubricant doesn't prevent this: groove dimensions aren't that tight versus stylus fit. But it does suggest any film must be very thin, or absent I think.
Perhaps a thin film is the lesser of two evils when it comes to stylus following the exact path of the groove base ?
LD
Perhaps a thin film is the lesser of two evils when it comes to stylus following the exact path of the groove base ?
LD
Then perhaps the perceived superior sound of vinyl is lost during wet playback?
Check the video below and just how crude it all is, Edison would have a good chuckle seeing how his 19th century invention still has followers.
https://www.youtube.com/watch?v=laIvjmdM0Ww Pay attention to the 33 1/3 segments.
The post has fizzled out, I guess the idea of hydroplaning was never considered in any of the equations?
- Home
- Source & Line
- Analogue Source
- Reducing Record Surface Noise - I want to know all Approaches