Yes, and these look a bit suspect to. Look how the solder has a grey ring circling the joint, as if its cracked.
Brand of solder shouldn't matter... its a long time since I bought any tbh. Something like this which is the high (relatively) flux content version and is also quite thick (1.2mm).
WARTON - Solder 2% 0.5KG - HARDCORE SOLDER 2% 18SWG 0.5KG | CPC UK
(I've just noticed we're in the Class D section. I'll move it over to 'Solid State')
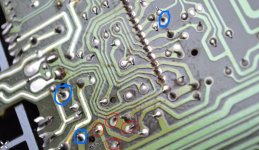
Brand of solder shouldn't matter... its a long time since I bought any tbh. Something like this which is the high (relatively) flux content version and is also quite thick (1.2mm).
WARTON - Solder 2% 0.5KG - HARDCORE SOLDER 2% 18SWG 0.5KG | CPC UK
(I've just noticed we're in the Class D section. I'll move it over to 'Solid State')
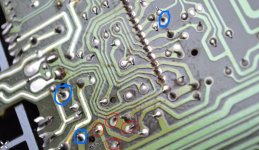
Yes, and these look a bit suspect to. Look how the solder has a grey ring circling the joint, as if its cracked.
Brand of solder shouldn't matter... its a long time since I bought any tbh. Something like this which is the high (relatively) flux content version and is also quite thick (1.2mm).
WARTON - Solder 2% 0.5KG - HARDCORE SOLDER 2% 18SWG 0.5KG | CPC UK
I see, thanks for the link. I'll get that one.
So it is, my mistake. Thanks for moving it.(I've just noticed we're in the Class D section. I'll move it over to 'Solid State')
The orange flux - I should Just leave that, then?
Last edited:
0.5kg of solder might be a lifetime buy. 😀
For reflow I would just apply some FSW-32 flux to the existing joints and reheat them. No need for additional solder.
For reflow I would just apply some FSW-32 flux to the existing joints and reheat them. No need for additional solder.
Last edited:
To answer your question, a pad is the area around a pin that solder flows on to.
Few things.
When reflowing it is easy to overheat components. So for ICs, do only one pin at a time, go elsewhere and come back later. Do not use refrigerants or other cooling methods, let joints cool naturally.
The picture I was referring to is the first one in post 15 on the thread. There is a big blue resistor that is partially obscured by a cable, to the right of the right channel driver chip. You've circled it in yellow. If you tell us the colour code we'll know what the value is. That is the one under which a lot of browning has occurred. Be very careful here as the tracks may be held to the board by nothing except hope.
I would replace that resistor with a higher wattage unit so it runs a bit cooler. I think it may be 2 watt unit, a 5 watt resistor will run a lot cooler.
While soldering, ensure you get good contact to the joint with a hot iron and flow a very small amount of solder onto the joint. Remove the solder before the iron and don't linger, but don't be ginger either. Most componets can handle 3 seconds at full soldering heat on each pin. Since this is a redo, I would normally get a bit of desoldering braid to remove a little of the older stuff. This will ensure a good flow other new solder.
Multi core and kester are what I would try to get, but usually any branded solder of decent quality would be good for this application. You will need about 25g of solder.
Few things.
When reflowing it is easy to overheat components. So for ICs, do only one pin at a time, go elsewhere and come back later. Do not use refrigerants or other cooling methods, let joints cool naturally.
The picture I was referring to is the first one in post 15 on the thread. There is a big blue resistor that is partially obscured by a cable, to the right of the right channel driver chip. You've circled it in yellow. If you tell us the colour code we'll know what the value is. That is the one under which a lot of browning has occurred. Be very careful here as the tracks may be held to the board by nothing except hope.
I would replace that resistor with a higher wattage unit so it runs a bit cooler. I think it may be 2 watt unit, a 5 watt resistor will run a lot cooler.
While soldering, ensure you get good contact to the joint with a hot iron and flow a very small amount of solder onto the joint. Remove the solder before the iron and don't linger, but don't be ginger either. Most componets can handle 3 seconds at full soldering heat on each pin. Since this is a redo, I would normally get a bit of desoldering braid to remove a little of the older stuff. This will ensure a good flow other new solder.
Multi core and kester are what I would try to get, but usually any branded solder of decent quality would be good for this application. You will need about 25g of solder.
Last edited:
0.5kg of solder might be a lifetime buy. 😀
That's a good point and actually the reason why I haven't bought any for about 25 years. Lol, when it was the day job, well you kind of gather the stuff 😉
0.5kg of solder might be a lifetime buy. 😀
For reflow I would just apply some FSW-32 flux to the existing joints and reheat them. No need for additional solder.
Oh right, would the solder not be too old?
Sent from my iPad using Tapatalk
To answer your question, a pad is the area around a pin that solder flows on to.
I see, thanks.
[/QUOTE]
Few things.
When reflowing it is easy to overheat components. So for ICs, do only one pin at a time, go elsewhere and come back later. Do not use refrigerants or other cooling methods, let joints cool naturally.
The picture I was referring to is the first one in post 15 on the thread. There is a big blue resistor that is partially obscured by a cable, to the right of the right channel driver chip. You've circled it in yellow. If you tell us the colour code we'll know what the value is. That is the one under which a lot of browning has occurred. Be very careful here as the tracks may be held to the board by nothing except hope.
I would replace that resistor with a higher wattage unit so it runs a bit cooler. I think it may be 2 watt unit, a 5 watt resistor will run a lot cooler.
While soldering, ensure you get good contact to the joint with a hot iron and flow a very small amount of solder onto the joint. Remove the solder before the iron and don't linger, but don't be ginger either. Most componets can handle 3 seconds at full soldering heat on each pin. Since this is a redo, I would normally get a bit of desoldering braid to remove a little of the older stuff. This will ensure a good flow other new solder.
Multi core and kester are what I would try to get, but usually any branded solder of decent quality would be good for this application. You will need about 25g of solder.
[/QUOTE]
Understood - thanks for the tips.
I'll check the resistor.
Sent from my iPad using Tapatalk
Last edited:

Not sure weather that second band is blue or black.
I think it's black.
You combine the first two digits and multiply them by the value of the third, correct? And then the fourth is tolerance.
Last edited:
Which resistor are you worried over ? Is it the stand up one near where it says Q809.
That's it, the blue one.
Sent from my iPad using Tapatalk
Those are 1k ohm metal oxide types and are specified where a 'safety component' is required. Safety here means that in the event of a fault they are flameproof and wont produce much smoke... which tends to frighten the punters 😉
These look perfect and its normal for them to discolour slightly when run near their maximum rating (and these look fine) and its also very normal to see paxolin and resin type circuit boards such as these to discolour badly where hot running components are fitted. That's just the way that type of board reacts to heat, you can't change that. These days its more normal to use fibreglass type board which is more temperature resistant.
These look perfect and its normal for them to discolour slightly when run near their maximum rating (and these look fine) and its also very normal to see paxolin and resin type circuit boards such as these to discolour badly where hot running components are fitted. That's just the way that type of board reacts to heat, you can't change that. These days its more normal to use fibreglass type board which is more temperature resistant.
Those are 1k ohm metal oxide types and are specified where a 'safety component' is required. Safety here means that in the event of a fault they are flameproof and wont produce much smoke... which tends to frighten the punters 😉
These look perfect and its normal for them to discolour slightly when run near their maximum rating (and these look fine) and its also very normal to see paxolin and resin type circuit boards such as these to discolour badly where hot running components are fitted. That's just the way that type of board reacts to heat, you can't change that. These days its more normal to use fibreglass type board which is more temperature resistant.
Alright, thanks for the tips. Just ordered the solder so hopefully all goes well!
Sent from my iPad using Tapatalk
Solder won't get "too old", just needs new flux for resolder.
Fair enough, thanks.
Sent from my iPad using Tapatalk
- Status
- Not open for further replies.
- Home
- Amplifiers
- Solid State
- Problem with amp: Crackling?