1.5" is pretty thick unless you have a ~14" bandsaw for resawing (I don't recall the width of the Pencil).Any thoughts on this as a front baffle material? Perhaps for a Pensil 10.3 or FHXL? Pros. Cons.
Home Depot has it on sale for half price ($94)
I can't comment on the best properties for baffle, sides, braces, etc., but the Wood Database is one resource to compare woods once you have decided what your preferences are.
Although I don't see impacts of the construction material's material properties as off-topic in a thread about the "Physics of Speaker Cabinet", I would say trying to assess the properties from the name on the packaging is probably not worth the bother based on this:
https://www.wood-database.com/hardwoods/fabaceae/acacia/ said:Comments: Acacia is a very large and diverse genus, containing several hundred species, ranging from woods weighing less than black cherry (Prunus serotina)—such as mangium (Acacia mangium)—to some of the heaviest and hardest woods on earth—such as waddywood (Acacia peuce). Because of this great diversity within the genus, it is nearly impossible to typify a standard wood that is representative of the genus. Nevertheless, some wood merchants (particularly wood flooring retailers) are quite fond of using the “acacia” name despite its inherent vagueness.
what is the main source of vibration and coloration with those mid and bass drivers, please ?
Direct contact of the driver with the box, most of the reactive energy of the basket from the moving cone is transferred to the box. Much much less comes from the air space changes.
So the cabinet needs to dissapte the energy in such a manner that it turns to heat and not extraneous sounds.
dave
Thanks.
Bracing "only" solves stifness and and internal air mvt : standing wave and resonnance ?
Ok, so if a decoupled front baffle, it is better to tie the driver on the external baffle and decouple the baffle from the layer behind that is is attached to the box. 👍
Bracing "only" solves stifness and and internal air mvt : standing wave and resonnance ?
Ok, so if a decoupled front baffle, it is better to tie the driver on the external baffle and decouple the baffle from the layer behind that is is attached to the box. 👍
A brace pushes (potential) resonance up in frequency where the wavelength relative to box thickness is much smaller and this a greater chance of being damped out. If one can push the frequency iup high enuff that there is not enuff energy in the nusic to excite those. If they can be made hi-Q they are les slikely to be excited.
Air space resonance is a different thing, we have little to worry about in terms of what is happening inside the box making the outside of the box ring, it is airspace resonances that escape out thru the driver cone. One uses shape and damping to help deal with this.
The KEF 105 convinced me that isolating the driver from the box is not a good idea (except maybe tweeters, something i rarely use). The speaker may not measure better sounded better with the driver tightly coupled to the box they sounded better, with greater DDR and more of everything.
If the driver is isolated the entire reactive force is disapaited by the basket, which means it is moving and obscuring the really small details. I prefer to share that reactive energy over as much of the box material as possible so as to get maximum damping for any potential resonances that get excited so they never make it out of the box.
The holey driver brce also has the immediae benefit from shifting energy from the baffle (both the weakest piece and, if it starts moving the most audiable) to the back of the box where any resonanc ewould be less audiable.
dave
Air space resonance is a different thing, we have little to worry about in terms of what is happening inside the box making the outside of the box ring, it is airspace resonances that escape out thru the driver cone. One uses shape and damping to help deal with this.
The KEF 105 convinced me that isolating the driver from the box is not a good idea (except maybe tweeters, something i rarely use). The speaker may not measure better sounded better with the driver tightly coupled to the box they sounded better, with greater DDR and more of everything.
If the driver is isolated the entire reactive force is disapaited by the basket, which means it is moving and obscuring the really small details. I prefer to share that reactive energy over as much of the box material as possible so as to get maximum damping for any potential resonances that get excited so they never make it out of the box.
The holey driver brce also has the immediae benefit from shifting energy from the baffle (both the weakest piece and, if it starts moving the most audiable) to the back of the box where any resonanc ewould be less audiable.
dave
Ah, thanks for the explication more. I was thinking the bracing was bracing just the back waves of the driver and was to break thoses in air wave lengths because they see complex geometrical barriers . I didn't understand it was in fact a distribution of the wood vibrations into an internal structures (the braces panels). So in fact it is more distributed energy than breaking resonances and figth the pression of the back wave!
So in fact it is more distributed energy than breaking resonances and figth the pression of the back wave!
Both of the first 2, the last a nice side-effect if damping added (in a reflex, a sealed or filled TL will already be well covered).
dave
... ummmm again, aside from the the particular wood, acacia. As I said they had other specie.
The butcher block caught my eye because it was double thick and, perhaps, "complex" due to the glued-up nature. And at the "pointed end" of the source of the excitement (the driver).
I had had the idea of double planking the front baffle, adding a wood face that would cover the front edges of the side baffle and facilitate rounding over with a large parabolic (thumbnail) bit. Maybe that's still the better way? With bracing too.
The butcher block caught my eye because it was double thick and, perhaps, "complex" due to the glued-up nature. And at the "pointed end" of the source of the excitement (the driver).
I had had the idea of double planking the front baffle, adding a wood face that would cover the front edges of the side baffle and facilitate rounding over with a large parabolic (thumbnail) bit. Maybe that's still the better way? With bracing too.
If you were planning on doubling up on the front baffle anyway, then the thickness would be an advantage to you. So I withdraw all concerns.
Not the authoritative woodworking source, but the butcher block construction should help with warping concerns, although TTBOMK it generally doesn't really prevent unequal expansion/contraction (movement) concerns like plywood does. So you might at least think through wood movement concerns.
Sorry if it seemed piling on about the type of wood. Honestly, speakers are made with everything from XPS foam, particle board, MDF, and all grades of plywood, to solid wood. You aren't using some super exotic plasmatic-phase-shifting titanium alloy here. So unless you are looking for wringing the last bit of performance out with specific density, strength, elasticity, and other parameters and know what the target values are for durometer, moisture meter, etc. measurements to verify what you have in hand is what you are looking for, then I wouldn't worry about the type of wood beyond asking my wife her opinion. That's what I was trying to say, if clumsily.
So I would say, give it a try!
Absent the admonishment about shipping wood around the world, I looked to see if it was on sale here in the states...
Not the authoritative woodworking source, but the butcher block construction should help with warping concerns, although TTBOMK it generally doesn't really prevent unequal expansion/contraction (movement) concerns like plywood does. So you might at least think through wood movement concerns.
Sorry if it seemed piling on about the type of wood. Honestly, speakers are made with everything from XPS foam, particle board, MDF, and all grades of plywood, to solid wood. You aren't using some super exotic plasmatic-phase-shifting titanium alloy here. So unless you are looking for wringing the last bit of performance out with specific density, strength, elasticity, and other parameters and know what the target values are for durometer, moisture meter, etc. measurements to verify what you have in hand is what you are looking for, then I wouldn't worry about the type of wood beyond asking my wife her opinion. That's what I was trying to say, if clumsily.
So I would say, give it a try!
Absent the admonishment about shipping wood around the world, I looked to see if it was on sale here in the states...
the butcher block construction should help with warping concerns
All of the solid wood enclosures Bernie or Scott have done start with the building of 'butcher-block’ panels. Makes for some nice cosmetic possibilities.
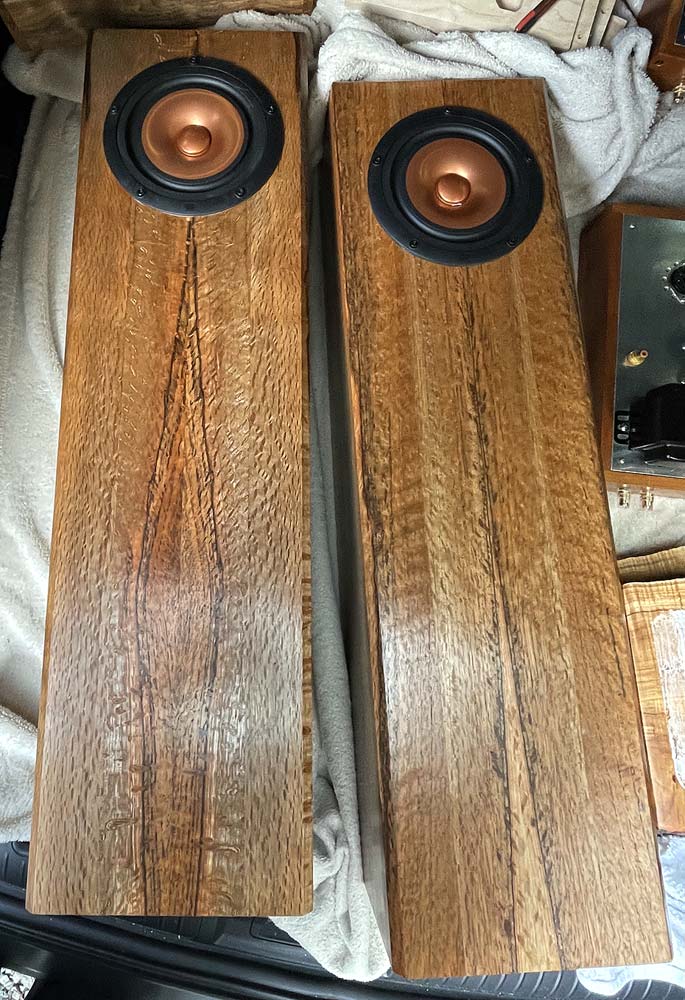
Bamboo Plywood is a “butcher-block” with a surface ply on each side.
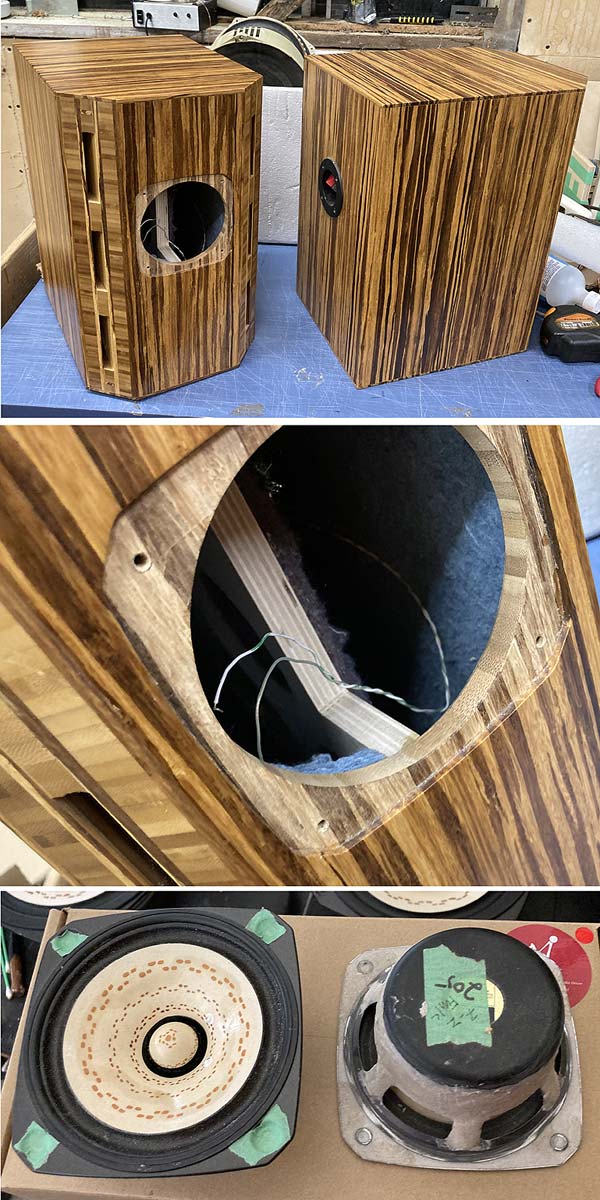
dave
I see others have already suggested plywood. Not only is it much harder, resulting in a higher internal speed of sound, but lossy materials actually create distortion. So it's a balancing act between avoiding ringing, and avoiding harmonics and intermodulation from hysteresis if the bulk part of the speaker driver "sinks into" an overly soft foundation.I'm using 22mm thick MDF
To take a serious look at fixing the issue at the source, maybe a second speaker could be fitted inside to precisely cancel out the forces? Kind-of brute force though, not elegant.
Also, the sound radiated from the wooden surface of the box isn't necessarily 'bad', in much the same way that the anti-phase sound emanating from behind a dipole speaker isn't bad. The source of the vibration will the magnet, and (ideally) these waves will smoothly travel out across the surface of the box and gradually lose energy to the surrounding air. So another thing you could look at is smoothing out the acoustic impedance. E.g.: I think Dave suggested making the bracing vertical. So as the waves spread out from the driver, they shouldn't hit big changes in the mass, like a flat panel that suddenly splits off into two flat panels at right angles. If the box is tall and narrow, then vertical braces would provide a more consistent path for the waves to travel along. I would go further and suggest trying a hollow box with very minimal ribs for bracing, or big sweeping curves. I wouldn't worry so much about the magnitude of the ripples so much, but focus on keeping the wave coherent.
I admire their work every time I see it! I really want one of those trapezoid onkens, first I need some wall mounted TV speakers and I already bought a set of Dayton PC83-4 before I knew anything.All of the solid wood enclosures Bernie or Scott have done start with the building of 'butcher-block’ panels. Makes for some nice cosmetic possibilities.
...
Bamboo Plywood is a “butcher-block” with a surface ply on each side.
...
dave
maybe a second speaker could be fitted inside to precisely cancel out the forces?
That is called push-push but the second driver is also radiating. Very useful with woofers.

This also covers bipoles (a push-push FR).
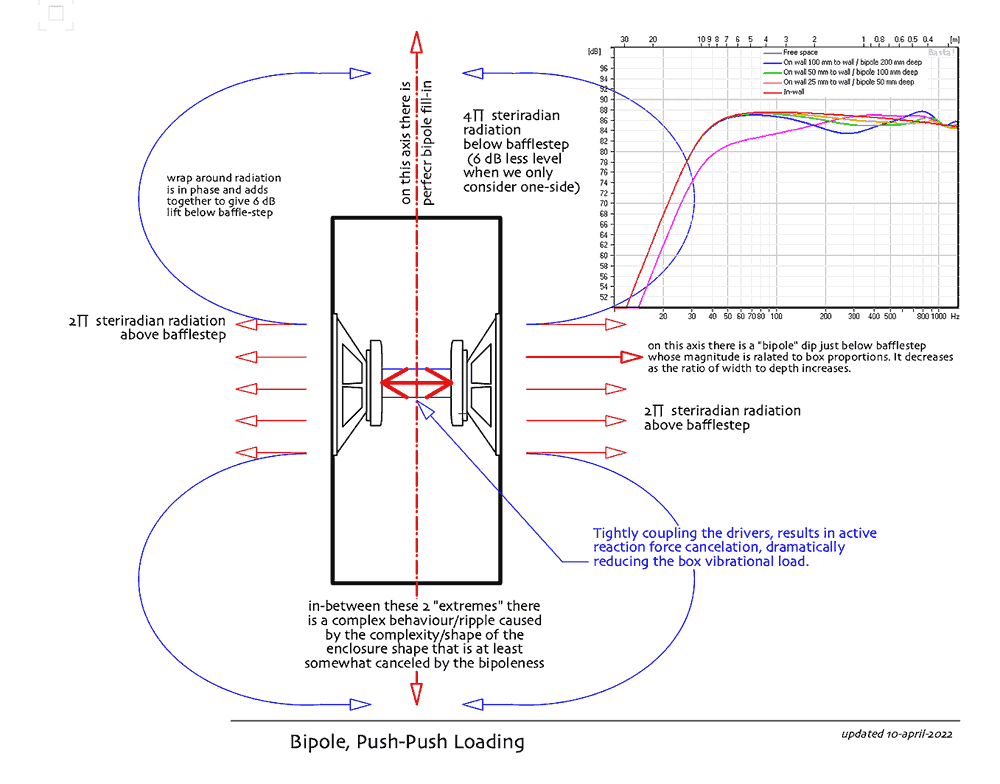
I did do a drawing of an isobarik version that is also push-push but it has significan tissue s(coupling chamber becoes too large).
dave
Another subject 'beat to death', yet lives on unabated 
Recommend using MOE to compare how thick different materials must be to substitute:
https://www.diyaudio.com/community/threads/what-mdf-thickness-is-acceptable.39991/#post-464294

Recommend using MOE to compare how thick different materials must be to substitute:
https://www.diyaudio.com/community/threads/what-mdf-thickness-is-acceptable.39991/#post-464294
btw, because of the war in Russia Birch ply is impossible to find down here, so i moved to Beech as i know some stocks of very high quality beech plywood in my area. And it does the job perfect. I rebuild a cabinet of a Dynaco A25 in december for someone in 18mm 13 layer BB beech ply, and that wood is as good as Birch i think. And like said, there is probally more good wood like that, with that kind of properties. I'm using it now in my actual build (a semi-retro 2way mini "weight & treble" reggae soundsystem) again.If you were planning on doubling up on the front baffle anyway, then the thickness would be an advantage to you. So I withdraw all concerns.
Not the authoritative woodworking source, but the butcher block construction should help with warping concerns, although TTBOMK it generally doesn't really prevent unequal expansion/contraction (movement) concerns like plywood does. So you might at least think through wood movement concerns.
Sorry if it seemed piling on about the type of wood. Honestly, speakers are made with everything from XPS foam, particle board, MDF, and all grades of plywood, to solid wood. You aren't using some super exotic plasmatic-phase-shifting titanium alloy here. So unless you are looking for wringing the last bit of performance out with specific density, strength, elasticity, and other parameters and know what the target values are for durometer, moisture meter, etc. measurements to verify what you have in hand is what you are looking for, then I wouldn't worry about the type of wood beyond asking my wife her opinion. That's what I was trying to say, if clumsily.
So I would say, give it a try!
Absent the admonishment about shipping wood around the world, I looked to see if it was on sale here in the states...
But i still think plywood like Birch or Beech plywood is best. Wich doesn't mean you can't build great speakers from MDF or other materials off course. Some of the technical best speakers in this world are made from MDF and Aluminium (Neumann/K&H and Genelec). But it's hard to design it right with those so the disadvantages of the material are removed and it very often requires tools and resources most diy'ers don't have. And yes, i also build in MDF sometimes. My MLTLs with the CHN110 are still MDF, as it was a "proof of concept" build for my firt TL type design, and i did not want to spend much money on a test that could fail...
Last edited by a moderator:
Sorry, please excuse my babble (or admin reduce it). I just realized that after turning over my division/section at work I'm probably starved for purpose and adult conversation not about taking out the trash or pirate ninjas.Another subject 'beat to death', yet lives on unabated![]()
I was trying to be helpful from practical sense on thickness. I still have some rough cut mahogany I bought, realized I couldn't effectively resaw, and didn't want 1/4 of it turned into shavings over thickness (by hand, no planer). Happily, I just realized I can probably butcher block it with my little bandsaw with a lot less waste than the table saw (and probably should have done it from the start).
Without having read the entire thread:
Most people overlook the resonance behavior of the cabinet material. Wood materials, for example, resonate towards a flat, gray midrange. This is audibly very present. I would not overdamp a cabinet made of wood materials by means of bracing or filling material or too high wall thickness. I would counter the present gray, flat midrange with resonances of the cabinet in the bass.
And - a 12 " fullrange IS to modify and to clamp - at least(-:
Most people overlook the resonance behavior of the cabinet material. Wood materials, for example, resonate towards a flat, gray midrange. This is audibly very present. I would not overdamp a cabinet made of wood materials by means of bracing or filling material or too high wall thickness. I would counter the present gray, flat midrange with resonances of the cabinet in the bass.
And - a 12 " fullrange IS to modify and to clamp - at least(-:
Attachments
And:
I would always decouple drivers from the case. The materials used for this purpose serve to tune the sound. The result is also the shortest resonance time. Because the resonances are less, and more controllable (see above: materials), transferred to the case.
Thus, the best sound results are achieved even with 12" drivers.
Build your dream spekers;-)
I would always decouple drivers from the case. The materials used for this purpose serve to tune the sound. The result is also the shortest resonance time. Because the resonances are less, and more controllable (see above: materials), transferred to the case.
Thus, the best sound results are achieved even with 12" drivers.
Build your dream spekers;-)
I occasionally get a yuk or two reflecting on CRS or decent aluminium grade vis-a-vis MDF etc. (I wonder who put me on to that... 😉 ) Not that I can afford it, but you can always dream! And although not Krell's biggest fan, they did their boxes right... well, that bit anyway.Another subject 'beat to death', yet lives on unabated
Recommend using MOE to compare how thick different materials must be to substitute:
https://www.diyaudio.com/community/threads/what-mdf-thickness-is-acceptable.39991/#post-464294

Last edited:
Birch ply is impossible to find down here, so i moved to Beech as i know some stocks of very high quality beech plywood
Birch is not thw only decent plywood. Almost any works well if it has many plies (even MDF plywood worksbetter than MDF).
Poplar ply in the USA, the “pine” stuff in Oz for instance
dave
I would always decouple drivers from the case
And i would not (except maybe a tweeter. It is counterproductive.
dave
- Home
- Loudspeakers
- Full Range
- Physics of speaker cabinet