Wonder whether this BMS could be an OS wave, or oval conical, or anything else
Is an OS waveguide at all superiour to others
I mean, the claim is that it needs the foam plug to work properly
So we may need to look at options fore the "foam-plug"
How about mounting this little waveguide behind a baffle, with mouth roundings
Mount some speaker cloth in between
Any kind of acoustic material could be used, and still look sweet
Is an OS waveguide at all superiour to others
I mean, the claim is that it needs the foam plug to work properly
So we may need to look at options fore the "foam-plug"
How about mounting this little waveguide behind a baffle, with mouth roundings
Mount some speaker cloth in between
Any kind of acoustic material could be used, and still look sweet
Attachments
John,
sounds complicated and introduces the same sources of error Earl has with his "pouring technique".
Using glass fiber reinforced plastic seems to be much easier, cheaper and faster if the shrinkage problem can be eliminated.
Best, Markus
sounds complicated and introduces the same sources of error Earl has with his "pouring technique".
Using glass fiber reinforced plastic seems to be much easier, cheaper and faster if the shrinkage problem can be eliminated.
Best, Markus
http://www.foambymail.com/Hi-FlowFoam.html
That is where I have bought 30 ppi reticulated foam in the past. Prices are fair, I think.
That is where I have bought 30 ppi reticulated foam in the past. Prices are fair, I think.
auplater said:
Copper EF
........
John L.
Thanks for the info !
Whether it is or is not the best process for this application, it is worth being familiar with.
edit:
Regarding the 'glassing method. How about laminating the throat portion first in more expensive epoxy resin - let cure - and following up with laminations over the whole thing in cheaper polyester?
Would the more stabile epoxy prevent the shrinkage where it matters? Would the polyester stick to the epoxy - I think so...
What part of "John's pulling your chain".. sounds civil and non-demeaning.
You're right. I shouldn't have said that. Normally I edit out personal stuff.
Look, I'm a skeptic but not about your competence. What would it cost, do you figure, for a DIYer to setup to electroform a waveguide?
Most DIyers don't have that sort of kit, do they?
How long, do you figure, is the learning curve before they successfully make one?
Or, are you selling your IP? Yes, it's personal, but it's not unreasonable to make that deduction from what you have posted, is it?
.............................
If he needs to charge $200 for 3 pieces of plastic....
Ahem. Two pieces of plastic. 😉
Nobody, but nobody, but nobody, sells a big, well designed waveguide for cheap, whether made of plastic or anything else. It's a premium item.
BTW, the waveguides/mounting plates he sold me are very good work. They fit perfectly and the interior of the guide is smoother than a baby's bum.
..................................
Not to mention the apologist stance for Dr. Geddes...
Rubbish. His problems are his problems. What puts me off is the unrealistic idea expressed here by some that he's supposed to take a risk and not be rewarded for it. Don't deny it - that is the implication and tenor of a number of recent posts.
He tried a lot of the techniques proposed here by some and they weren't successful for him due to material qualities. He said so. This seems to bother them and I don't understand it. Do they wish to make the same mistakes? That's the "thrashing around" I see.
It's ironic that he has posted his solution to that problem but the implications of it have been ignored.
.....................................
My happiness is irrelevant. You are going to do whatever you want.
..........................................
"Bloviating" - nice word. I've tucked it away for a rainy day. Thanks 😀
EF-ing
not sure where the error is. Remember, the exterior of the throat section would be mounted into the flange, not the interior. Holes can be drilled with pretty high precision pretty easily, much higher than what looks to be +/- mils with the OS stuff, otherwise, microwave waveguides woruld not work. presumably the driver mounting holes have a fixed relationship to the throat section of the driver. Besides, the mandrel can have a masked section extending into the throat of the driver not electroformed to serve as an alignment gauge. I don't see where the complexity or error occurs. it's done evry day in the microwave fabrication industry
But, whatever. I'm not preaching difference here for difference sake. Like I said, I don't want to do this for a living. If I can provide some alternative fab methods, I'm willing to do the explanations.
Maybe try googling electroforming. It's really not so difficult, dangerous, or expensive. I've retired from that line of work (in medicine now) so it's just an art/hobby with me. I'm gonna build some form of waveguide speaker myself, just to explore the technology using EF.
Frank... No, I'm not trying to sell anything. I'm not doing this much anymore, although I have a garage full of stuff in mothballs. Even if I was, the microwave stuff is much more lucrative than any audio applications could ever be.
here are a few more waveguides I've built over the decades..
http://en.wikipedia.org/wiki/Electroforming
All the best...
John L.
markus76 said:John,
sounds complicated and introduces the same sources of error Earl has with his "pouring technique".
Using glass fiber reinforced plastic seems to be much easier, cheaper and faster if the shrinkage problem can be eliminated.
Best, Markus
not sure where the error is. Remember, the exterior of the throat section would be mounted into the flange, not the interior. Holes can be drilled with pretty high precision pretty easily, much higher than what looks to be +/- mils with the OS stuff, otherwise, microwave waveguides woruld not work. presumably the driver mounting holes have a fixed relationship to the throat section of the driver. Besides, the mandrel can have a masked section extending into the throat of the driver not electroformed to serve as an alignment gauge. I don't see where the complexity or error occurs. it's done evry day in the microwave fabrication industry
But, whatever. I'm not preaching difference here for difference sake. Like I said, I don't want to do this for a living. If I can provide some alternative fab methods, I'm willing to do the explanations.
Maybe try googling electroforming. It's really not so difficult, dangerous, or expensive. I've retired from that line of work (in medicine now) so it's just an art/hobby with me. I'm gonna build some form of waveguide speaker myself, just to explore the technology using EF.
Frank... No, I'm not trying to sell anything. I'm not doing this much anymore, although I have a garage full of stuff in mothballs. Even if I was, the microwave stuff is much more lucrative than any audio applications could ever be.
here are a few more waveguides I've built over the decades..
An externally hosted image should be here but it was not working when we last tested it.
http://en.wikipedia.org/wiki/Electroforming
All the best...
John L.
From a production point of wiev, Gedlees foam waveguide cast directly on the baffle is brilliant, it really is...it costs next to nothing and takes very little effort to make and easy to finish
Once tucked away in a well sounding nicely finished product, noone cares about the inside
Looking solely on the waveguide as a single unit things turn out slightly different
Glassfiber would be preferred, but cost is higher as it takes a lot more effort to produce...luckily that doesnt matter in DIY 😀
Once tucked away in a well sounding nicely finished product, noone cares about the inside
Looking solely on the waveguide as a single unit things turn out slightly different
Glassfiber would be preferred, but cost is higher as it takes a lot more effort to produce...luckily that doesnt matter in DIY 😀
To cast a single piece waveguide exactly as Earl does is still a possible alternative solution. But you would need two metal molds.
Best, Markus
Best, Markus
With Earls foam waveguide I see no way arround the additional mounting plate
Its only brilliant from a production point of wiev, as I see it
But there could be something to it
Make a solid waveguide of plaster upon a plate
Mount the plate upon a squared box
Fill the box with that foam stuff, and you have your waveguide

Its only brilliant from a production point of wiev, as I see it
But there could be something to it
Make a solid waveguide of plaster upon a plate
Mount the plate upon a squared box
Fill the box with that foam stuff, and you have your waveguide

Attachments
Make a solid waveguide of plaster upon a plate
....with the speaker baffle over it - with the plaster sticking thru the waveguide hole.
As you like it 🙂
I would prefer to leave the cast waveguide inside the wooden box, to place upon the midbass box
It should be possible to have pinbolts or something mounted on the rear, so that an additional mountingplate can be avoided
Throat hole could be made fairly accurately in wood
How about a nice big nice elliptical one
I would prefer to leave the cast waveguide inside the wooden box, to place upon the midbass box
It should be possible to have pinbolts or something mounted on the rear, so that an additional mountingplate can be avoided
Throat hole could be made fairly accurately in wood
How about a nice big nice elliptical one
I get the impression that the Geddes waveguides are NOT "foam"
amiklos posted:
It seems more like they are solid polyurethane -like a skateboard wheel. This would be solid and well-damped and would support the weight of the driver easily.
I could be wrong but there might be confusion from the discussion of foam for the plug....
amiklos posted:
Just a point of clarification as it's clear you've not seen one of these waveguides in person. They are in no way similar to a lump of foam. They are solid as hell. I'm quite impressed with my waveguides and it sounds like Earl has refined the most recent waveguides even further.
It seems more like they are solid polyurethane -like a skateboard wheel. This would be solid and well-damped and would support the weight of the driver easily.
I could be wrong but there might be confusion from the discussion of foam for the plug....
What about alumilite?
Alumilite is popular for casting parts in the hobby and crafts world:
http://www.alumilite.com/Category.cfm?Category=Casting Resins
Alumilite is popular for casting parts in the hobby and crafts world:
http://www.alumilite.com/Category.cfm?Category=Casting Resins
Rotational molding is another approach to making uniform waveguides. It could easily include a mounting plate.
Very complex shapes and volumes can be made (like polyurethane plastic toys, etc). Shrinkage needs to be accounted for during the molding process. And, of course, a CAD-type drawing is needed. (something beyond my skill level...)
Very complex shapes and volumes can be made (like polyurethane plastic toys, etc). Shrinkage needs to be accounted for during the molding process. And, of course, a CAD-type drawing is needed. (something beyond my skill level...)
Variac, of course they are not foam. This should be clear by simply looking at the various pictures posted. The material is like plastic but more brittle. It's more rigid than e.g. skateboard casters. The HOMless waveguide consists of two parts: the waveguide itself and a glued in foam plug.
rljones, otational molding wouldn't work because the important surface is the inner shape of the waveguide not the outside.
Best, Markus
rljones, otational molding wouldn't work because the important surface is the inner shape of the waveguide not the outside.
Best, Markus
tooling
probably a few hundred bucks and a little creativity. Here's where I made all the parts displayed in previous posts... in my garage..
can't comment on the learning curve... if you can follow a cookbook, you could electroform (assuming some rudimentary chemistry knowledge and lack of fear regarding electricity and water...😉 😉 )
I've seen far more spent on distortion analyzers, signal generators, etc. in pursuit of that perfect amp... after all gedlee figured out how to cast poly... and he's a physiscist!!
John L.
FrankWW said:
Look, I'm a skeptic but not about your competence. What would it cost, do you figure, for a DIYer to setup to electroform a waveguide?
Most DIyers don't have that sort of kit, do they?
How long, do you figure, is the learning curve before they successfully make one?
<snip>
probably a few hundred bucks and a little creativity. Here's where I made all the parts displayed in previous posts... in my garage..
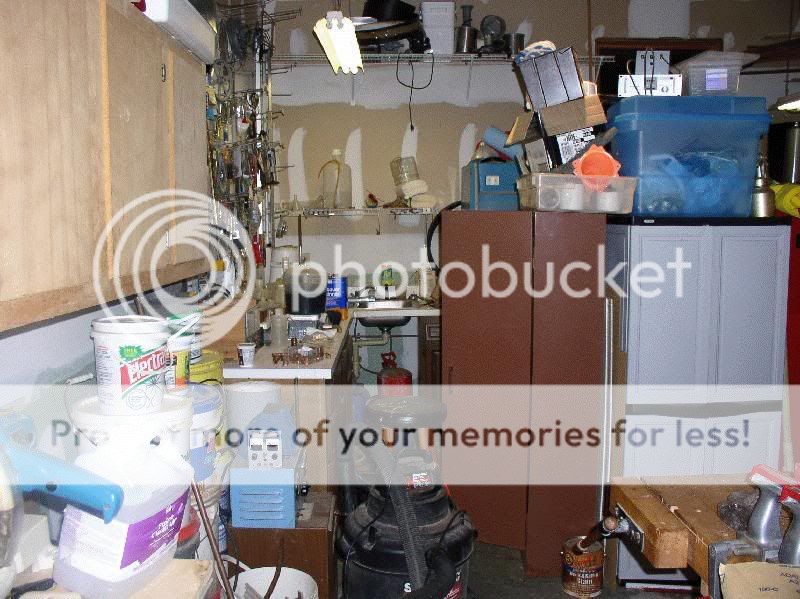
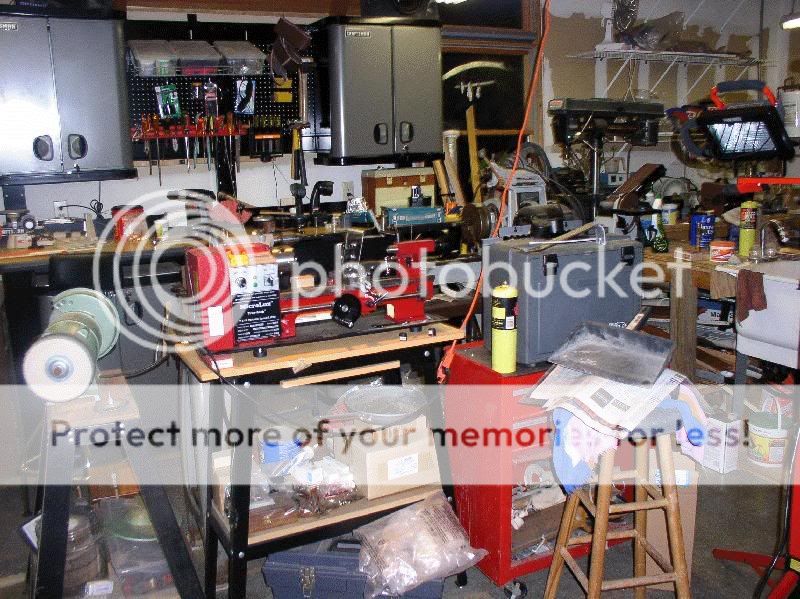
can't comment on the learning curve... if you can follow a cookbook, you could electroform (assuming some rudimentary chemistry knowledge and lack of fear regarding electricity and water...😉 😉 )
I've seen far more spent on distortion analyzers, signal generators, etc. in pursuit of that perfect amp... after all gedlee figured out how to cast poly... and he's a physiscist!!
John L.
First things first.
Surely the first problem to be solved is not what method of deposition etc.... is used to create the Waveguide, its how does the accurate negative/mandrel get produced?
After all whats the use of poly/electroforming/glassing etc if one doesnt have a form to create around?
Polymorph could be used to create a one off set of waveguides around a decent negative.
Polymorph is available in the UK HERE
regards
Nick
Surely the first problem to be solved is not what method of deposition etc.... is used to create the Waveguide, its how does the accurate negative/mandrel get produced?
After all whats the use of poly/electroforming/glassing etc if one doesnt have a form to create around?
Polymorph could be used to create a one off set of waveguides around a decent negative.
Polymorph is available in the UK HERE
regards
Nick
Re: First things first.
hmmnn... geez, I coulda sworn I said you could fill an existing waveguide with (fill in the blanks) and an appropo release agent and VOILA! (or walla in webspeak😀) you'd have a negative.
we used limestone filled wax at Bell Textron when I was building deuterium fluoride chemical laser combustor mandrels and manifolds, so it's a pretty precise method...
but what do I know?
John L.
Grumpy_Git said:Surely the first problem to be solved is not what method of deposition etc.... is used to create the Waveguide, its how does the accurate negative/mandrel get produced?
After all whats the use of poly/electroforming/glassing etc if one doesnt have a form to create around?
Polymorph could be used to create a one off set of waveguides around a decent negative.
Polymorph is available in the UK HERE
regards
Nick
hmmnn... geez, I coulda sworn I said you could fill an existing waveguide with (fill in the blanks) and an appropo release agent and VOILA! (or walla in webspeak😀) you'd have a negative.
we used limestone filled wax at Bell Textron when I was building deuterium fluoride chemical laser combustor mandrels and manifolds, so it's a pretty precise method...
but what do I know?
John L.
John,
I guess all processes around electroforming are familiar to you but not to the average DIYer. The learning curve is too high. And we still don't know if or what metal is suitable for this special audio application. I don't see the advantage of electroforming a waveguide in comparison to casting, turning or building it from glass fiber reinforced plastic.
Best, Markus
I guess all processes around electroforming are familiar to you but not to the average DIYer. The learning curve is too high. And we still don't know if or what metal is suitable for this special audio application. I don't see the advantage of electroforming a waveguide in comparison to casting, turning or building it from glass fiber reinforced plastic.
Best, Markus
- Home
- Loudspeakers
- Multi-Way
- Oblate Spheroid Waveguide - Consolidated Construction Thread