It's basically what I'm in the process of doing but with MDF. This is the first time I've seen another cabinet built upwards like that rather than slicing sideways or with rings.
Calculating the interior is proving tricky so the prototype may end up being sealed and filled with water to measure 🙂
Calculating the interior is proving tricky so the prototype may end up being sealed and filled with water to measure 🙂
Yeah I'm building the prototype by hand but I will get my mate to CAD the several shapes and now I know how difficult it is lining up hand routed layers of MDF on slippery glue, I'll get a local company to CNC the bits.
Of to look at your build thread 🙂
Of to look at your build thread 🙂
Wesayso
The cnc'd template idea is really ingenious. I find it incredible that you did all the cutting with a router. You must have saved a boatload of cash doing it that way. This easily has to be the most ambitious project I've ever seen on these pages.
The cnc'd template idea is really ingenious. I find it incredible that you did all the cutting with a router. You must have saved a boatload of cash doing it that way. This easily has to be the most ambitious project I've ever seen on these pages.
Well I've read enough to see that I was completely on the right track and the solutions I'd found along the way so far are very similar to yours.
However I will take your idea of just having the tamplates made in aluminium as using an MDF tamplate on the router table causes a groove which means all the aprts are not identical.
Would you do steel rod again or something like a 10mm dowel to keep everything lined up?
Is the wavey internals worth it if all the internal walls are curved anyway?
I didn't get far enough in to see if you still lined the inside with sound deadening material.
I'm so glad I sumbled across your thread as I'd only ever reall seen boxes used as DIY and I wondered if there was a reason, apart from being a massive pain in the neck to build, why no-one was doing it this way.
However I will take your idea of just having the tamplates made in aluminium as using an MDF tamplate on the router table causes a groove which means all the aprts are not identical.
Would you do steel rod again or something like a 10mm dowel to keep everything lined up?
Is the wavey internals worth it if all the internal walls are curved anyway?
I didn't get far enough in to see if you still lined the inside with sound deadening material.
I'm so glad I sumbled across your thread as I'd only ever reall seen boxes used as DIY and I wondered if there was a reason, apart from being a massive pain in the neck to build, why no-one was doing it this way.
It was all done in a strange period in my life. I found myself with lots of time and no money. I have been at it as if it was a day job and it still took quite a while to accomplish.
If I did have money and no time I would have outsourced it all.
I found myself between jobs due to the economy at the time. Not being in perfect health made that period quite a bit longer than I envisioned. But it gave me an opportunity to realize a dream, while using it at the same time to keep me busy and sane. Although if you see what I've done that last part is debatable 😀.
I've learned a lot from it, I do not regret it happening either.
If I did have money and no time I would have outsourced it all.
I found myself between jobs due to the economy at the time. Not being in perfect health made that period quite a bit longer than I envisioned. But it gave me an opportunity to realize a dream, while using it at the same time to keep me busy and sane. Although if you see what I've done that last part is debatable 😀.
I've learned a lot from it, I do not regret it happening either.
Calculating the interior is proving tricky so the prototype may end up being sealed and filled with water to measure 🙂
Sketchup will do it too. Well, it will give you the area and then you just need to multiply by your height. Free and possibly easier to learn than 3D CAD.
I've been using Sketchup - I've used ot before for designing Descking and Pergolas etc - even laying out floor tiles.
I'll look into the area feature, thanks.
I'll look into the area feature, thanks.
Don't get too exited about the enclosure since there isn't any measurements available. It looks mostly marketing talk. It seems to be a complicated solution to a non problem, typical differentation stuff. In fact, location of the port and driver are the worst possible, quaranteed leakage of standing waves from the port unless the inner structure actually works, but due to long wavelenghts I'm doubt it does nothing. If the walls are not resonating then it could be better than a typical box. So, a unnecessary negative talk from me. Just trying to remind everyone not to take everything found from internets as true. Peace 🙂
In a stack like mine? I'd do rods again. but use something that can be deformed ever so often. The wood will expand/contract. With a lot of force actually. So making many smaller stacks with a deformable layer between each and holding it up with rods seems like a possible solution. It is what I have now, and has been solid for over 5 years of use.Would you do steel rod again or something like a 10mm dowel to keep everything lined up?
Is the wavey internals worth it if all the internal walls are curved anyway?
I don't think so, but at least it makes for a random thickness of all walls.
I didn't get far enough in to see if you still lined the inside with sound deadening material.
Yes I did, while taking impedance sweeps to see how effective it was.
I'm so glad I sumbled across your thread as I'd only ever reall seen boxes used as DIY and I wondered if there was a reason, apart from being a massive pain in the neck to build, why no-one was doing it this way.
My main reason was to be able to create a fluent outer shape of the enclosure, out from the cone outwards, to limit diffraction effects. It has always been just a hunch, an idea in my head, but has recently been proven to at least have some merit.
If you read from here on forward, you'll see some simulations of the shape I chose compared to a more traditional shaped enclosure.
In other words: it works! 😀
I've been using Sketchup - I've used ot before for designing Descking and Pergolas etc - even laying out floor tiles.
I'll look into the area feature, thanks.
Highlight the area of interest, so for eg., the inside bottom area of the cabinet. Right click and select Entity Info. Area is up at the top.

I am no fan of translam boxes, but its one asset is the ability to generate exotic shapes. This looks to have been well used on the inside of the box.
Takin gthe idea brougth by things like the B&W DM302…
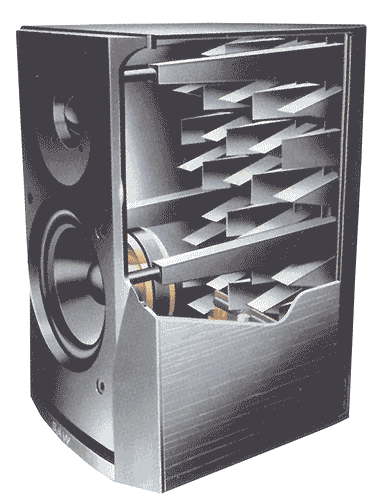
… and the airCavity treatments seen in this thread: Taking the Air Cavity/pre-chamber to the next level...
NICE! The inherent flaws of plywood,
I find that gets “boring” eventually, first thot i hasd was what if these were in a glossy, piano type finish that emphasises the lovely curves.
dave
… but this is the first time I've seen one with a diffuser interior.
I have seen a number of examples, using the same style of construction, few as dramatic as these — there does have to be significant (relatively) delta in the distances to the walls to have a useful effect.
dave
The waste probably outweighs the product🙂
Besides that, one is not using the ply in the direction of its strengths, so the walls have to be thicker.
This box has gross volume consideraby larger than its net volume, likely uses sufficien tmaterial to build many more “normal” boxes of the same volume. Mass will be substantial for the volume, and shipping goes up. Lots of extra costs to be paid to realize this kind of design.
dave
Magico did it early on.
They did the translam, they didn’t take the interior as far.
This kind of box is far from new.
dave
Very pretty version with a famous name tagged onto it:
Philharmonia by Jean Nouvel
I saw them at Munich High-End in 2018, but they couldn't demo them as they showed them in a public area - kind of made to be seen, not heard (they might have had a by-appointment listening room as well). They were rather attractive, I have to say.
Philharmonia by Jean Nouvel
I saw them at Munich High-End in 2018, but they couldn't demo them as they showed them in a public area - kind of made to be seen, not heard (they might have had a by-appointment listening room as well). They were rather attractive, I have to say.
- Home
- Loudspeakers
- Multi-Way
- Now that's what I call a cabinet!