This reminds me of a friend that built some nice speakers with lovely cherry veneer. One day when he was out working, his wife decided to move them, because they were in the wrong place or something. They were too heavy to pick up, so she dragged them across the hardwood floor and chewed the sh*t out of the veneer. Man was he pi$$ed. 🙂My wife took my old Vienna Accoustic Hayden bookshelf speakers and painted them (poorly) black because she didn't like their color in my office on my bookshelf.
jeff
I got lucky to hook up and marry someone much younger. She takes a real interest in our music equipment, we karaoke, dance and the best thing is that she recognises and respects what the equipment does and isOne day when he was out working, his wife decided to move them
Well I can't be mad because she promised me if she screwed up, I could get new speakers...This reminds me of a friend that built some nice speakers with lovely cherry veneer. One day when he was out working, his wife decided to move them, because they were in the wrong place or something. They were too heavy to pick up, so she dragged them across the hardwood floor and chewed the sh*t out of the veneer. Man was he pi$$ed. 🙂
But honestly while the cabinets look like shite, on axis the speakers still sound good. I know Vienna Accoustics did upgrade the Haydens over the years, but for book shelf speakers... they still sound great. (relatively speaking)
I guess I could take them apart, paint the cabinet properly, and put them back together, then see what they did on the insides and what the crossover looks like... still I am considering doing something else.
That's the cool thing about DIY. Quite often the only constraints are visual, just to keep the SO happy.still I am considering doing something else.
So you're wanting to build new desktop speakers and main speakers?
jeff
Not so much desk top, but bookshelf speakers. Small office w no real space for floor stands.
Its really early on...I mean the first thing I'm going to do is fix my old speakers if the closest maker space has some space to paint, or I can find someone who has a paint 'booth' or something and they can do it fairly inexpensively.
Then consider something to replace the Haydns.
Looking at kits like the CSS TD1-X. Or design my own, and then a subwoofer if I stay with book shelf sized speakers.
I like the look of the Fyne F1s.
Not tied to it... there are some other designs that have caught my eye.
If I do something beyond a kit like the CSS TDX-1X ... I will have to bribe my nephew to help w the CAD and CNC stuff.
Not to mention all the design software is on windows and I'm on a Mac... and Linux boxes.
Its really early on...I mean the first thing I'm going to do is fix my old speakers if the closest maker space has some space to paint, or I can find someone who has a paint 'booth' or something and they can do it fairly inexpensively.
Then consider something to replace the Haydns.
Looking at kits like the CSS TD1-X. Or design my own, and then a subwoofer if I stay with book shelf sized speakers.
I like the look of the Fyne F1s.
Not tied to it... there are some other designs that have caught my eye.
If I do something beyond a kit like the CSS TDX-1X ... I will have to bribe my nephew to help w the CAD and CNC stuff.
Not to mention all the design software is on windows and I'm on a Mac... and Linux boxes.
This is why I laminate several different materials in my speaker boxes. I glue up layers of MDF, birch ply, and hard wood to get a good laminated sammitch. Some might think it’s constrained layer construction but, I can’t get the glue thin enough without a giant sized press, and the materials (wood products) aren’t uniform. What I do know is it makes for stiff heavy boxes that don’t ring. Well, don’t ring as much. I’ve gotten good results with three layers of 1/4” material. MDF, concrete board, and plywood, is a messy, dusty combination that makes a good panel. Also, the box still needs bracing. There is high density fiber (HDF) board. I haven’t tried that out yet.MDF is like thick paper made from a goop of wood fibre and water-soluble glue. A lot of glue. It gets its stiffness from dry material bulk and fibre length is not long enough to be structural. Think of it as woody plastic which will start vibrating at certain frequencys and power. I have a high excursion 7" in a ported MDF box smaller than a cubic foot. At a good volume the cab buzzes like cardboard but same thing happens with plywood at little further up the volume. Try to brace with something that itself wont vibrate at certain frequencies or power otherwise an MDF brace can even play the box like a guitar string 😀
Its fine if you not using enough power to get it to vibrate
My logic was heavy material moves the vibration to a lower frequency, stiff material moves the vibation to a higher frequency, so laminating heavy and stiff materials should disrupt the vibrations. That’s my theory anyway. I should probably do a study.
Remember, there are many successful loudspeakers out there that use/used particle board or plywood. 😱
This is why I laminate several different materials in my speaker boxes. I glue up layers of MDF, birch ply, and hard wood to get a good laminated sammitch. Some might think it’s constrained layer construction but, I can’t get the glue thin enough without a giant sized press, and the materials (wood products) aren’t uniform. What I do know is it makes for stiff heavy boxes that don’t ring. Well, don’t ring as much. I’ve gotten good results with three layers of 1/4” material. MDF, concrete board, and plywood, is a messy, dusty combination that makes a good panel. Also, the box still needs bracing. There is high density fiber (HDF) board. I haven’t tried that out yet.
My logic was heavy material moves the vibration to a lower frequency, stiff material moves the vibation to a higher frequency, so laminating heavy and stiff materials should disrupt the vibrations. That’s my theory anyway. I should probably do a study.
Remember, there are many successful loudspeakers out there that use/used particle board or plywood. 😱
I've been doing a bit of research on this... thanks to everyone's input.
If I understood what I've learned... every speaker cabinet will resonate if there's enough energy and at the right frequency.
I've seen materials like panzerholtz which is a highly compressed laminate. Some call it "densified".
("Panzerholz® A DIN 7707-compliant hardened panel material made of a combination of phenolic resin and hardwood with a hardened structure. ")
Per one of the online sources. You could find some online videos and articles on it, and similar materials. Someone wrote that the key was in the phenolic resin, which may have some issues with manufacturing and not made in the US w some importers. There are alternatives but again, still not much in the US and relatively expensive.
I've seen videos of tours of some of the high end speaker factories which have huge presses to make their molded (shaped) cabinets. And then place solid inserts to help reinforce/deaden the vibrations. (Really interesting tech, well beyond what any DIYer could dream of doing. )
I did see one speaker maker on youtube make his own laminate, in the shape of his cabinet. Impressive and beyond my skills.
To be honest, this is all part of the journey, doing the research before the design and build.
Thx.
laminates are just layering. There are structural and no structural laminates. The systems that you are mentioning are not interpreting structural laminates correctlylaminate
The layers with grain orientation should sandwich the spacer layer, best made with a rigid but low density substrate like foam or hexcel. There isn't a better alternative to that. The structural system as relevant to speakers relies on the skin being forced to stretch and bend over the core, and it's the shear strength of the glue holding the skin on that defies panel deflection. Layers to change panel properties like impact damage resistance are formed as matrix in the skins, not the substrate
Doing so with the substrate and not using skins is building a panel that in only relying on material thickness, and you can do that with just about anything
Randy,
Sorry I was using the terms that were in the articles and videos.
The wood in the plywood would be the laminate and then held by the glue. They call these highly compressed laminates in that they are bonded at high temp and pressure to get a denser overall material. (Although some point out that the resin is what increases the density. )
From what some say here... you could improve something like the CSS TD1X kit by building your own cabinets (using their plans) by using different materials like birch plywood. (And using the higher end cross over.)
Sorry I was using the terms that were in the articles and videos.
The wood in the plywood would be the laminate and then held by the glue. They call these highly compressed laminates in that they are bonded at high temp and pressure to get a denser overall material. (Although some point out that the resin is what increases the density. )
From what some say here... you could improve something like the CSS TD1X kit by building your own cabinets (using their plans) by using different materials like birch plywood. (And using the higher end cross over.)
An actual improvement for birch plywood to make best use of internal space would be to simply use a ply stringer on each panel and fillets in the seams. Then glass the lot with biax as described in the link, Gets rid of all resonance and bracing issues by creating a true monocoque with the plyFrom what some say here... you could improve something like the
https://www.westsystem.com/instruction/the-gougeon-brothers-on-boat-construction-book/
Bottom line is one needs to look at its MOE referenced to a known one such as the BB ply in my link.
I read your link and it’s interesting. I don’t know if my laminates are any better than 3/4” birch plywood, and there is a lot to be said for thick MDF. I havent measured the difference. I have measured my boxes and they are relatively quiet. I need some better equipment to get a definitive answer. I may have to make some 2’x2’ panels and measure their resistance to ringing. That would be a good summertime project, in between fishing trips.😉
I don’t think MOE is the only factor in making a strong non resonant box. Mass matters, as does strength. For example MDF is heavier than plywood, maybe 10 pounds heavier than 3/4” birch ply. Plywood is hugely stronger than MDF. MDF will only support 35-40 pounds where inexpensive plywood can easily support twice the load.
So the idea is to use 3/4” / 19mm birch or apple ply, if you can’t afford that use 1 1/2” / 40mm thick MDF. As a very general rule of thumb. Then brace the crap out of it. An article on cabinet bracing would be helpful. I think people are doing it wrong by bracing the corners and not the center of the panels. The bracing should look like bracing in a guitar or an airplane wing.
I don’t think MOE is the only factor in making a strong non resonant box. Mass matters, as does strength. For example MDF is heavier than plywood, maybe 10 pounds heavier than 3/4” birch ply. Plywood is hugely stronger than MDF. MDF will only support 35-40 pounds where inexpensive plywood can easily support twice the load.
So the idea is to use 3/4” / 19mm birch or apple ply, if you can’t afford that use 1 1/2” / 40mm thick MDF. As a very general rule of thumb. Then brace the crap out of it. An article on cabinet bracing would be helpful. I think people are doing it wrong by bracing the corners and not the center of the panels. The bracing should look like bracing in a guitar or an airplane wing.
there is a lot to be said for thick MDF
It burns fairly well.
heavier
Heavier is not an asset unless it is a side effect of greater stiffness, and if it could be stiffer and yet lighter that is better.
It is MUCH harder to excite a high frequency (potential) resonance. Everything resonates. If they never get excited it is as if they did not exist.
dave
I think we are agreeing. However, I don’t think stiffness is necessarily the answer. Many stiff materials ring like a bell, metal, carbon fiber, glass. So, damping is important too and I think MDF has some damping abilities, maybe not that much? That’s part of the reason I layered stiff, soft, light, and heavy materials together. The different materials transmit sound well at different frequencies, the different materials act like filters effectively canceling much of the ringing in the panels. Well, that’s the theory anyway. Like I said I may be better off using 3/4“ plywood.
Do you recommend specifically birch ply or are there other materials you are using? Acora makes granite enclosures. https://www.acoraacoustics.com/
Might be a bit beyond the capabilities of your average diy’er and the average floor. I’ve seen many enclosures made from concrete or Corian.
You reminded me of an experimental isobaric subwoofer project I did that was made from MDF. I just painted it with clear polyurethane which it sucked right up. After my experiment was deemed a flop I needed space in my workshop so I ran the boxes through my tablesaw making them into fireplace sized pieces. That crap burned like crazy! I’m lucky I didn’t burn the house down. I think poly infused MDF would make great survival fuel, or rocket fuel.
Do you recommend specifically birch ply or are there other materials you are using? Acora makes granite enclosures. https://www.acoraacoustics.com/
Might be a bit beyond the capabilities of your average diy’er and the average floor. I’ve seen many enclosures made from concrete or Corian.
You reminded me of an experimental isobaric subwoofer project I did that was made from MDF. I just painted it with clear polyurethane which it sucked right up. After my experiment was deemed a flop I needed space in my workshop so I ran the boxes through my tablesaw making them into fireplace sized pieces. That crap burned like crazy! I’m lucky I didn’t burn the house down. I think poly infused MDF would make great survival fuel, or rocket fuel.
Last edited by a moderator:
Hmm, we seem to be 'having a failure to communicate' 😉, the goal with a LF box is to push its resonance either well above its BW (at least an octave IME)/stiff = MOE or well below (massive), which IME it's a lot easier/cheaper for most folks to go stiffer.
Move up the BW to shorter, less powerful WLs and going massive is increasingly the better choice with increasing frequency.
Move up the BW to shorter, less powerful WLs and going massive is increasingly the better choice with increasing frequency.
Not all folks have the same aptitude man, I hope no one goes around using MDF for fuel after reading thatYou reminded me of an experimental isobaric subwoofer project I did that was made from MDF. I just painted it with clear polyurethane which it sucked right up. After my experiment was deemed a flop I needed space in my workshop so I ran the boxes through my tablesaw making them into fireplace sized pieces. That crap burned like crazy! I’m lucky I didn’t burn the house down. I think poly infused MDF would make great survival fuel, or rocket fuel.
I'll try once more. Dampening is really about load lines. Think about what happens when you pick up a corner of a sheet of graphite and flick. A wave will travel away from where the work is applied. Stick a sheet of ply to that and flick it. Ply bends and graphite sheet bends. They'll deflect together and when pushed enough, the weaker material fractures first, followed by a very quick failure of the stronger material as it takes up all the load
Now please really try to ponder this. Graphite doesn't want to stretch, so apply that to both sides of the ply with epoxy, as that has the required shear strength. Now flick, the wave will try to deflect the ply but since the graphite is on both sides, for the ply to bend, it has to first be able to stretch the graphite one side and compress it on the other side. The epoxy bond at every macro meter of panel length is so strong that the stretch is just not going to happen, hence the deflection is not going to happen, hence the wave gets dampened. This is the function of the 'skins' spaced over a firm but light core. The thicker and lighter and firmer the core, the more dampening happens. And you can even strap an actual jet engine to it!
Now that flat composite panel just created will behave with bass but will resonate with higher. Answer, don't use a flat panel. Design a box that uses curved panels, place and hold your ply or foam core into its final shape and skin over that. Now the panel will behave with audio frequencies
I am able to introduce a software from another field and go step by step on how to easily do this, but I have migrated to foam and do not have any ply builds planned nor any correctly modelled speakers to show with
If anyone following this has a ply box they want to build as an FRP composite, throw it up and let's discuss curves and BOM first. We can than go and convert the acoustic model to a box with curved sides and build it without pain or head scratching
Many stiff materials ring like a bell, metal, carbon fiber, glass.
As long as you never excite them, it is as if they do not exist.
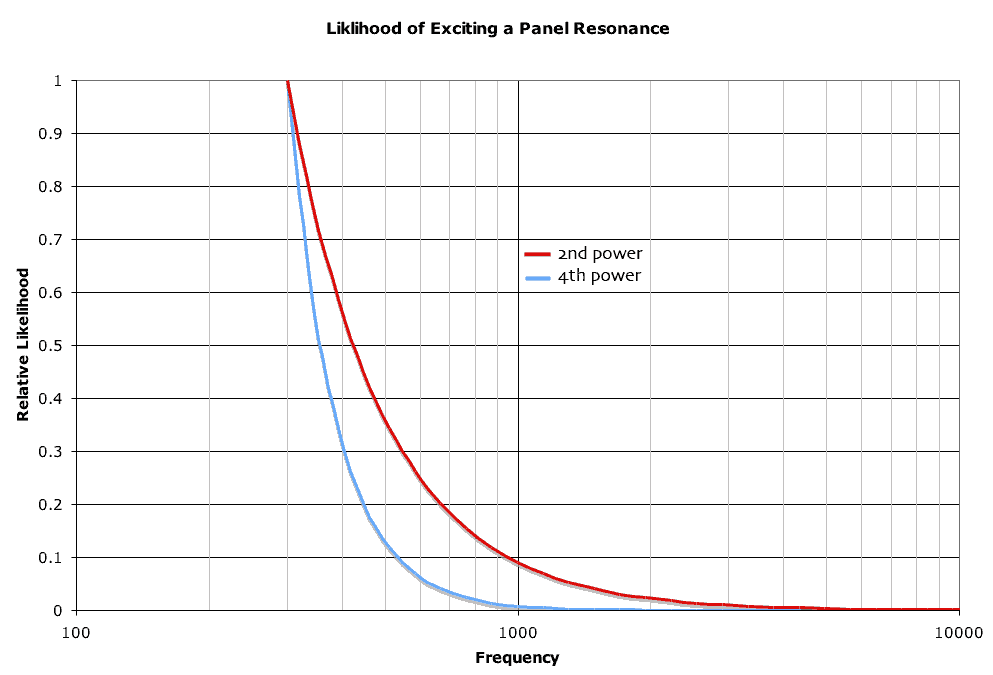
And if you can make the Q of the potential resonance high it is even less likely to get excited.
dave
Have look at this pic, it is an FRP composite using 6 and 8mm ply and e-glass skins on each side of the ply. The glass is in a non-woven stitched form with half the fibres running across the rest. Woven glass or carbon fibre is useless
Look at the small hole, that holds the steering hub for a regular sized wheel, that is a very long lever from the hub to handhold. Actually longer than most common spanners. This boat has a GEV footprint and designed to ride the apex of chop to 2 feet and slice the peaks of taller. Now think of about yours truly at almost 90kg hanging on the that wheel with both hands and taking off from every 4th to 6th peak and landing while travelling at about 30 knots. Look at the curves radiating away from that hole. Think about how the glass on each curved face is holding the hub flat and true. No PA sub can blow this 8mm box apart. The sides on the other hand are designed as springs with glass only on one side of each face. Really ponder the load lines at the hub and floor fix
Look at the small hole, that holds the steering hub for a regular sized wheel, that is a very long lever from the hub to handhold. Actually longer than most common spanners. This boat has a GEV footprint and designed to ride the apex of chop to 2 feet and slice the peaks of taller. Now think of about yours truly at almost 90kg hanging on the that wheel with both hands and taking off from every 4th to 6th peak and landing while travelling at about 30 knots. Look at the curves radiating away from that hole. Think about how the glass on each curved face is holding the hub flat and true. No PA sub can blow this 8mm box apart. The sides on the other hand are designed as springs with glass only on one side of each face. Really ponder the load lines at the hub and floor fix
- Home
- Loudspeakers
- Full Range
- Noob Cabinet design questions...