I made softmounts for the midrange - great success! Much less vibration transfer from the midrange to the baffle. Will do the same for the tweeter!
The pictures below should explain it all. The trick is to tighten the screws just enough, but not too much. Then the driver "floats" quite well.
Mounting hardware:
Rubber seal for the driver:
Larger holes so the screws wont make contact through the hole.
Nut, washer and bushing:
Bushing on the front side as well:
The pictures below should explain it all. The trick is to tighten the screws just enough, but not too much. Then the driver "floats" quite well.
Mounting hardware:
An externally hosted image should be here but it was not working when we last tested it.
Rubber seal for the driver:
An externally hosted image should be here but it was not working when we last tested it.
Larger holes so the screws wont make contact through the hole.
An externally hosted image should be here but it was not working when we last tested it.
Nut, washer and bushing:
An externally hosted image should be here but it was not working when we last tested it.
Bushing on the front side as well:
An externally hosted image should be here but it was not working when we last tested it.
StigErik said:
This will only *reduce* the problem, not remove it...
I told you 😉
But in audio each and everything is about making the right decisions about inferiour compromises.
😀
Decoupling like you have shown for sure is a valid method.
Many DIYer have done this in the past - but as far as I know - for one reason or another this trick hasn't survived in the pro and commercial world.
My guess is that the very dampening mechanism involved (friction related) will introduce a sonic pattern not that beneficial - I'm definitely interested to what conclusions you will come after some longer time of listening.
If you ever did "ride" a Mini (the original one not the retro from BMW!) you immediately know what I mean.
The only "real" solution is to *fly* OB's, I'm affraid - but this would lead you to a *very* different design compared to what you have begun with!
For *your* design, I think you should add some more mass at the points discussed earlier - this will keep the sonic pattern more close to what you are used to IMO
Michael
I've made soft mounts for the tweeter as well. I do like what I hear, at least thats the first impression! 🙂
In my reference speakers, the opposite approach is used, which also works very well. Those speakers are very heavy, stiff and damped with a lot of sand. There's virtually no vibration in those boxes.
Anyway - the softmount trick really worked for the mid and tweeter in the dipoles, although I will do some more to add stiffness and damping.
The woofer is still hardmounted to the baffle, and will remain so, even if make the baffle vibrate a little bit at bass frequencies. I think its important to keep the woofer firmly in place, because the cone movement is many times greater than the midrange.
In my reference speakers, the opposite approach is used, which also works very well. Those speakers are very heavy, stiff and damped with a lot of sand. There's virtually no vibration in those boxes.
Anyway - the softmount trick really worked for the mid and tweeter in the dipoles, although I will do some more to add stiffness and damping.
The woofer is still hardmounted to the baffle, and will remain so, even if make the baffle vibrate a little bit at bass frequencies. I think its important to keep the woofer firmly in place, because the cone movement is many times greater than the midrange.
It sounds like you have a decision on how to reduce the panel vibration. I did sort of the opposite with my open baffle mid. I supported the center of the driver from the back using a simple heavy duty shelf bracket. See below. The mid is mounted from the rear and is bolted to the lexan baffle, with the wood sandwiched in between. Their is a wood piece in front or the bracket and some weather stripping between the wood and the driver magnet.
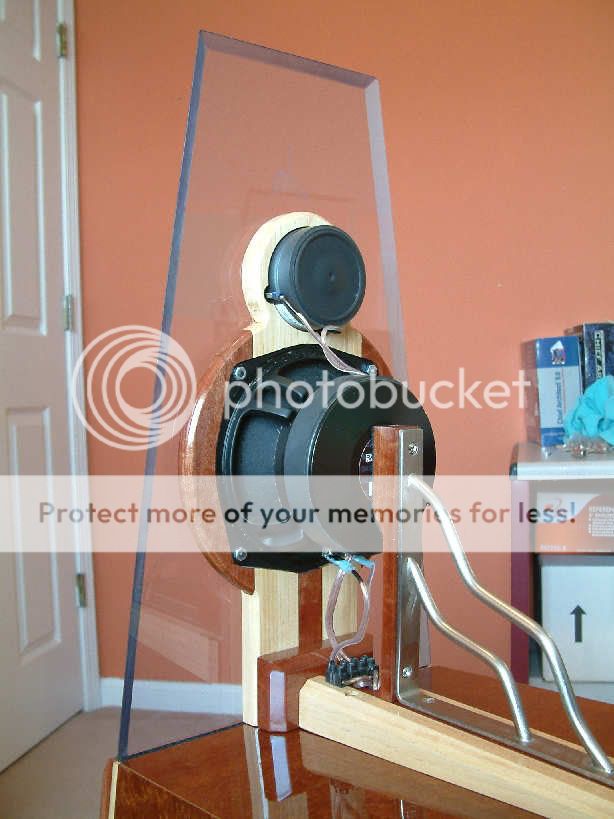
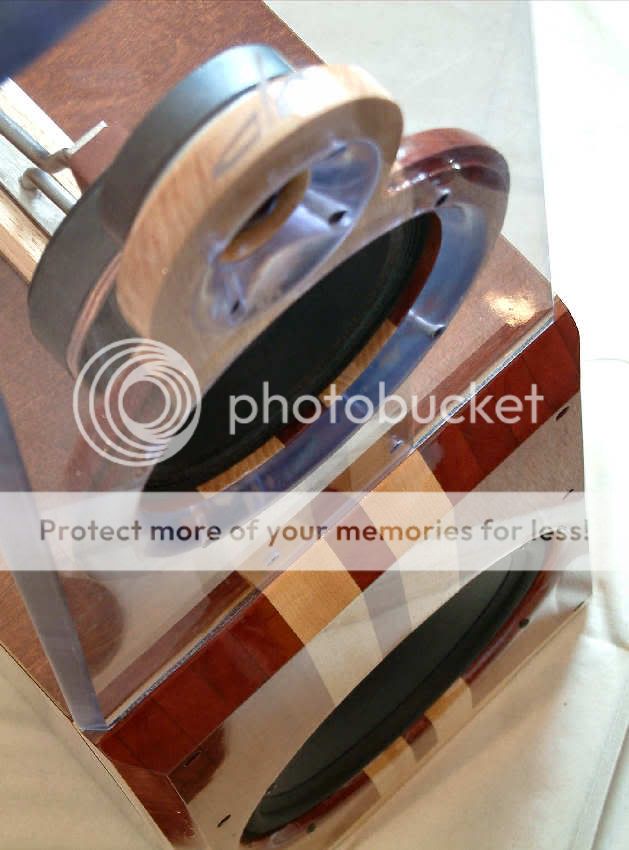
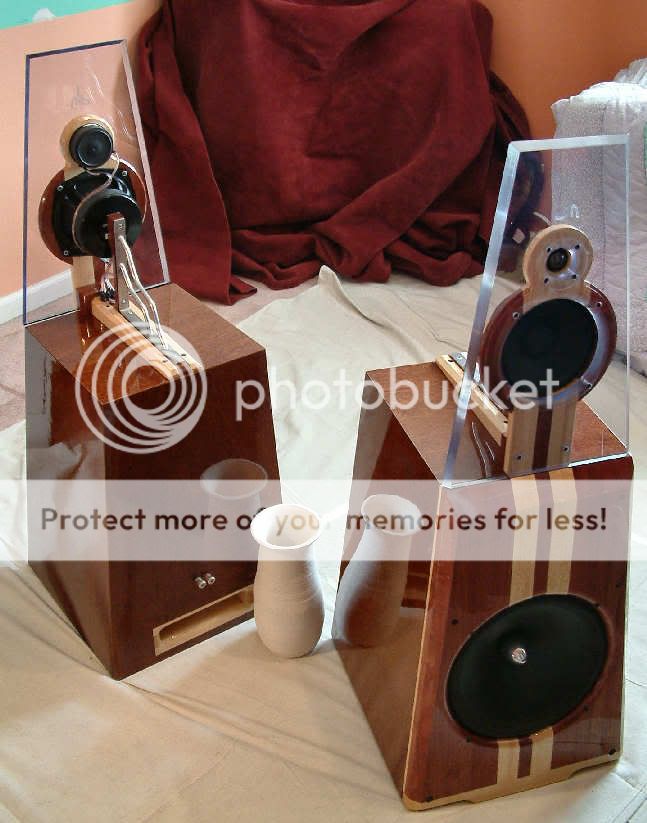
StigErik said:I've made soft mounts for the tweeter as well. I do like what I hear, at least thats the first impression! 🙂
Excellent
🙂
Just a minor remark or two to what has been suggested by Lindell and David
To use a separate "stand" for the high / mid works pretty well. I used a flimsy single straight piece of wood rod perpendicular to the driver axis though.
Basically what you aim for with this approach is *not* to make the stand as rigid as possible but in contrary – make it as low in frequency as possible in its basic mode.
Meaning the whole thing swings gently if you excite it by hand.
In addition to that, don't use metal as material as it does not do a good job in dampening higher order modes of the structure (you can look at the rod as a guitar string to get the picture).
The basic idea to catch behind all of this is that we want the local mass of the speaker (and the attached OB) to build up for the reaction forces and *not* the structure (down to mother earth).
One usual misunderstanding in this mechanism is that we *don't* have to see the mass "dampening" the movement in its very sense.
The mass acts as a counterpart to build up the reaction force and the overall amplitude gets lower the higher the reaction mass is with respect to the diaphragm mass.
But - it's not *dampening* - its pure *cancelling* - best thing in world you can have – as its the *solution* not a "work around"
The approach of let springs between bass and mid / high do the job is based on the same principles (same you find in sub chassis turn tables)
The Linn Sondec – one of the most prominent proponent – is said to have lovely "flow" in its presentation (and I confirm that anytime)
Michael
dlneubec said:It sounds like you have a decision on how to reduce the panel vibration. I did sort of the opposite with my open baffle mid. I supported the center of the driver from the back using a simple heavy duty shelf bracket. See below. The mid is mounted from the rear and is bolted to the lexan baffle, with the wood sandwiched in between. Their is a wood piece in front or the bracket and some weather stripping between the wood and the driver magnet.
Beautiful work !
Did you glue the speaker to the bracket?
Michael
In order to decouple driver from baffle this is my prototype..
An externally hosted image should be here but it was not working when we last tested it.
An externally hosted image should be here but it was not working when we last tested it.
An externally hosted image should be here but it was not working when we last tested it.
An externally hosted image should be here but it was not working when we last tested it.
An externally hosted image should be here but it was not working when we last tested it.
An externally hosted image should be here but it was not working when we last tested it.
An externally hosted image should be here but it was not working when we last tested it.
An externally hosted image should be here but it was not working when we last tested it.
Jaco Pastorius said:In order to decouple driver from baffle this is my prototype..
[/URL]
Like the rig of a sail boat ...
May you always have warm winds and an inch of water below her keel !
😀
Michael
Originally posted by mige0
Like the rig of a sail boat ...
Yes and it woks fine like boats ones! 🙂
The MDF support behind the midwoofer is only 1.9 mm thick just not to interfere with the back wave.. Steel roads prevent it from bending…
mige0 said:
Beautiful work !
Did you glue the speaker to the bracket?
Michael
Thank you. The bracket is press fit to the speaker magnet. The mid driver, a B&C 6md38 has a built in rubber seal on the front of the driver, which presses against the back of the baffle. The bracket is screwed to a wood piece below it The wood piece was needed to set the angle for the baffle (which is 5º). The wood piece is held to the box with threaded inserts in the box and cap head screws through the wood. the entire assembly of the top MT section can be dissassembled.
There's a lot of good ideas here, thank you all for that. 🙂
I think I'll finish the speaker as it is right now, with the soft-mounts, and beefing up the baffle a little bit.
Maybe I'll try something else next time (there will definitely be a next dipole project).
I think I'll finish the speaker as it is right now, with the soft-mounts, and beefing up the baffle a little bit.
Maybe I'll try something else next time (there will definitely be a next dipole project).
Updates!
I've made wings for the upper part as well - only on one speaker, so I can compare the two.
There was no significant difference in vibration level, maybe just a tiny bit less. It should be shifted up in frequency, since the baffle is stiffer. Damping with asphalt sheet should be more effective on higher frequency modes I think.
The biggest improvement was much smoother response from the midrange - less peaks and dips.
I've made wings for the upper part as well - only on one speaker, so I can compare the two.
There was no significant difference in vibration level, maybe just a tiny bit less. It should be shifted up in frequency, since the baffle is stiffer. Damping with asphalt sheet should be more effective on higher frequency modes I think.
The biggest improvement was much smoother response from the midrange - less peaks and dips.
An externally hosted image should be here but it was not working when we last tested it.
Ahh - you are using twisted solid copper wire to reduce inductivity and for good stray field immunity!
Can give very good results - my brother used to be a fan of that.
Does the mid vibrate equally, less or more if you hold it in your hands instead of mount it in the OB?
Michael
Can give very good results - my brother used to be a fan of that.
Does the mid vibrate equally, less or more if you hold it in your hands instead of mount it in the OB?
Michael
The baffle is almost completely dead if we hold the driver by hand without touching the baffle. The softmounts helps for that problem, but its not perfect. Using a bracket like Linkwitz does might be the best solution, but we are trying to squeeze the most out of this thing as it is. I do think that the softmounts helped a lot, the speaker sounded a lot better with that modification.
Mhh, actually I meant how much is the mid driver vibrating in your hand compared to hard or soft mounting?
What I would like you to find out is if there are resonancies that *increase* amplitude of vibration or if its simply the counter movement of the speakers mass (diminished a little bit by the OB stiffness).
*If* you have more vibration with the driver mounted you could try to rest the magnet on a piece of wood you put to fit between the magnet and the horizontal bracing (screw it to the horizontal bracing).
Then thighten the magnet with cable straps or anything else to that piece of wood providing an additional path of energy transfer - less directly related to the baffle itself.
Michael
What I would like you to find out is if there are resonancies that *increase* amplitude of vibration or if its simply the counter movement of the speakers mass (diminished a little bit by the OB stiffness).
*If* you have more vibration with the driver mounted you could try to rest the magnet on a piece of wood you put to fit between the magnet and the horizontal bracing (screw it to the horizontal bracing).
Then thighten the magnet with cable straps or anything else to that piece of wood providing an additional path of energy transfer - less directly related to the baffle itself.
Michael
I would like to begin with the efforts of Vidar Öierås to mount baffles and elements. His sketch is most illuminating:
Your idea is not novel but interesting I think. Vidar's approach would be as good as yours. He used some crude (tovet) woolfelt between baffles to allow for friction and slight movement. All absorbed into warmth.
Myself I have experimented with elements fastened with venetian blind strings and resting on rubber strip seal. That has been partly succesful. With the light Monacor 130/X8 it functioned quite well. But with the more heavy Visaton B200 I had to tighten the strings so fast as to hold the element in place, so that some friction was going over to the baffle.
I think your method might work better, putting some (plumbing ?) rubber seals around the element and not fasten to hard. No doubt Magnet Mount will be superior.
I have however one more thing to communicate and that is a simulation of the Beyma bass element in a 22 x 22 " x 14 " deep U baffle, done with MJK's worksheet software:
Crossover at 250 Hz 24 dB/octave.
/Erling
An externally hosted image should be here but it was not working when we last tested it.
Your idea is not novel but interesting I think. Vidar's approach would be as good as yours. He used some crude (tovet) woolfelt between baffles to allow for friction and slight movement. All absorbed into warmth.
Myself I have experimented with elements fastened with venetian blind strings and resting on rubber strip seal. That has been partly succesful. With the light Monacor 130/X8 it functioned quite well. But with the more heavy Visaton B200 I had to tighten the strings so fast as to hold the element in place, so that some friction was going over to the baffle.
An externally hosted image should be here but it was not working when we last tested it.
I think your method might work better, putting some (plumbing ?) rubber seals around the element and not fasten to hard. No doubt Magnet Mount will be superior.
I have however one more thing to communicate and that is a simulation of the Beyma bass element in a 22 x 22 " x 14 " deep U baffle, done with MJK's worksheet software:
An externally hosted image should be here but it was not working when we last tested it.
Crossover at 250 Hz 24 dB/octave.
/Erling
Member
Joined 2003
You can also use short sections of soft rubber tubing over the bolt where it passes through the baffle. This ensures there is no inadvertent contact between the bolt and baffle.
Vidar's idea is more or less the same as I did. I used rubber o-rings for suspension.
My screw holes are large enough to avoid contact with the baffle through the hole, but to avoid problems later on I will use rubber tubes through the holes, and also cut the baffle hole a bit larger to avoid contact.
I've put on asphalt damping sheets at the rear side of the baffle. This trick works very well on regular boxes, and it worked great here as well. I feel that the baffle vibration is low enough now. It also sounds a whole lot better.
Here's a picture of the rear side with asphalt. Not a piece of art, but it works very well!
My screw holes are large enough to avoid contact with the baffle through the hole, but to avoid problems later on I will use rubber tubes through the holes, and also cut the baffle hole a bit larger to avoid contact.
I've put on asphalt damping sheets at the rear side of the baffle. This trick works very well on regular boxes, and it worked great here as well. I feel that the baffle vibration is low enough now. It also sounds a whole lot better.
Here's a picture of the rear side with asphalt. Not a piece of art, but it works very well!
An externally hosted image should be here but it was not working when we last tested it.
And here's one from the front!
An externally hosted image should be here but it was not working when we last tested it.
StigErik said:And here's one from the front!
An externally hosted image should be here but it was not working when we last tested it.
A little bit of nice finishing and it would become pretty impressive for sure!
As it shouldn't be a big issue to do flat on-axis EQ'ing for you - could you post some measurenents at off-axis angels?
Its a topic I'm most interested in at the moment.
Michael
- Home
- Loudspeakers
- Multi-Way
- My open baffle dipole with Beyma TPL-150