Yeah. Something like the Avebury seems to make good use of the rear surface to extend the effective horn area. Ideally I'd go with that design, but can't really afford it, nor do I have the brains to spec one myself. So Dallas 2 it is!I think I am leaning towards a design where the mouth is at the rear of the enclosure.
I like me some formulas -- but what exactly are they for? And how do I determine upper freq and octave spread?Fh = Fl*2^n
Fl = Fh/2^n
n = ln(Fh/Fl)/ln(2)
where:
Fh = upper frequency
Fl = lower frequency, or the XO point in this case
n = octave spread
ln(2) = 0.6931
Found me a good writeup on the subject of bracing and a thread or two, but damn if I don't feel more discouraged for every one I find. Been messing around with the bracing on the CAD model, but I'm feeling like my approach to it is wrong. I'll have to read up more on it.
Also been wondering about using fiberglass to strengthen panels. Is this something people do? Figure it might be useful on the bracing material to reduce the acoustic footprint of the panels.
Last edited:
I like me some formulas -- but what exactly are they for?
A good basik primer on horn design with theoretical formulas.
http://p10hifi.net/TLS/downloads/Dinsdale-Horns-3parts.pdf
dave
I like me some formulas -- but what exactly are they for? And how do I determine upper freq and octave spread?
I'm feeling like my approach to it is wrong.
Also been wondering about using fiberglass to strengthen panels. Is this something people do? Figure it might be useful on the bracing material to reduce the acoustic footprint of the panels.
Fhm
By using the octave math I posted........
Strongly suggest you follow your 'feeling'.........
I thought I posted a bracing mini tutorial as a followup to the 71% span esquing your bracing scheme, but can't find it, so more to come........
Yes, fiberglassing was common until health issues became an issue.
Regardless, running a 1/4" masonite board (1/8" is sufficient, but gave up trying to convince folks by the time I joined the WWW) spaced down/offset ~71% of the pathlength as I implied earlier is the preferred way to go; all those little pieces just add 'hot spots'. You want to go 'medieval' on bracing, use a higher Fs material than recommended and/or double up the cab's walls to increase rigidity.
Ah of course, I forgot about that bit. Goes to show how one can easily get swept up in the intricacies and forget about the fundamentals.Fhm
By using the octave math I posted........
I have access to a laser cutter and a damned near infinite supply of 1/4" MDF via work, so that works out perfectly. 71% of the total pathlength (240cm) comes out to ~172cm. So you mean that i should place a few braces at this point, or up to this point? And then offset side to side according to some multiple of the golden ratio. This would place said brace according to the picture.[...]running a 1/4" masonite board (1/8" is sufficient, but gave up trying to convince folks by the time I joined the WWW) spaced down/offset ~71% of the pathlength as I implied earlier is the preferred way to go;
This one is excellently laid out, thanks a bunch.A good basik primer on horn design with theoretical formulas.
http://p10hifi.net/TLS/downloads/Dinsdale-Horns-3parts.pdf
I have a few other questions that have been gnawing at me, in no particular order:
- When stuffing a horn - at least in the simulations - you tend to lose low end. This runs counter to the idea that stuffing essentially makes the box bigger, acoustically. I assume that this has something to do with the very nature of horns, and that you want to keep the stuffing to a minimum if possible then? Just enough to catch some stray HF/MR?
- Is using threaded rod to tension the outside walls (inwards) something people do? Is it effective? Reason I'm asking is I'm considering doing this for the hornmouth to avoid wobble.
- Does placing speaker fabric over the hornmouth impact the horns' coupling ability? Much as I would like to keep it open, if I go with threaded rods to keep things tensioned I don't think it would look very attractive uncovered.
- There's very little space between the rear surface of the speaker and the inside of the filter chamber -- Won't this cause a fair deal of reflections? Would I maybe stand to gain something from reducing as much of the area normal to the speaker as possible, or would some dense stuffing do?
- I do a lot of 3D printing, would there be some way to apply this to the speakers? For example placing vortex generators, diffractory geometry or stepped panels to break up HF along some part of the internal geometry. Maybe in the filter chamber? Figure I have access to so much modern tech, why not use it.
No, the brace is a ~full length divider! The goal in box design is to protect its contents, so we want the horn sturdy enough that if dropped from a high height all four corners act as crush zones and the horn remains 100% intact.
Obviously, if designed this way we can be assured that as construction goes, the horn will be as acoustically inert as practical, i.e. most acoustically efficient.
Ideally we want the divider to 'snugly' fit in between its two ends at different end offsets (no hot spots to crack) and its width at an acoustic or golden ratio offset, though folks normally put it down the middle, presumably so that the terminus looks symmetrical and is of course quite adequate for small horns, but I like to properly educate folks TTBOMK and let them decide how far to deviate from it.
If you want to go the 'extra mile', add a very thick false baffle over the baffle, driver cutout chamfered at ?? angle or roundover that sounds best and duplicate it around its perimeter.
Ideally there's no stuffing, just some damping pads at certain areas such as seen in this dual 15" tapped horn and if you look very carefully you can see Tom's board/panel braces are apparently offset front/back as I noted. https://www.avsforum.com/cdn-cgi/im...wn//attachments/_mg_3283c-medium-jpg.3277279/
Re box stuffing....... https://www.ranger5g.com/forum/attachments/box-builder-fill-er-up-pdf.35156/
Yes, tension rods work and some have used it on speakers.
Obviously, if the covering is dense enough it will damp its response and is sometimes used to critically damp it same as a BR vent; i.e. the pioneer's used specially designed weaves in dense materials to both decoratively cover and fine tune their speakers including their BLHs. Remember, the horn's output is whipping back n' forth at ~1128 ft/sec, so takes a fair amount of density and a lot of clamping rigidity to lower/withstand it.
ATM, the only thing I can think of is 3D printing some horn bells to enhance the driver's polar response.
Well, if I had my way you'd sorely regret offering it to me, but AFAIK no longer have the time nor sufficient enthusiasm to compile it
, but thanks anyway! 👍😎
Obviously, if designed this way we can be assured that as construction goes, the horn will be as acoustically inert as practical, i.e. most acoustically efficient.
Ideally we want the divider to 'snugly' fit in between its two ends at different end offsets (no hot spots to crack) and its width at an acoustic or golden ratio offset, though folks normally put it down the middle, presumably so that the terminus looks symmetrical and is of course quite adequate for small horns, but I like to properly educate folks TTBOMK and let them decide how far to deviate from it.
If you want to go the 'extra mile', add a very thick false baffle over the baffle, driver cutout chamfered at ?? angle or roundover that sounds best and duplicate it around its perimeter.
Ideally there's no stuffing, just some damping pads at certain areas such as seen in this dual 15" tapped horn and if you look very carefully you can see Tom's board/panel braces are apparently offset front/back as I noted. https://www.avsforum.com/cdn-cgi/im...wn//attachments/_mg_3283c-medium-jpg.3277279/
Re box stuffing....... https://www.ranger5g.com/forum/attachments/box-builder-fill-er-up-pdf.35156/
Yes, tension rods work and some have used it on speakers.
Obviously, if the covering is dense enough it will damp its response and is sometimes used to critically damp it same as a BR vent; i.e. the pioneer's used specially designed weaves in dense materials to both decoratively cover and fine tune their speakers including their BLHs. Remember, the horn's output is whipping back n' forth at ~1128 ft/sec, so takes a fair amount of density and a lot of clamping rigidity to lower/withstand it.
ATM, the only thing I can think of is 3D printing some horn bells to enhance the driver's polar response.
Well, if I had my way you'd sorely regret offering it to me, but AFAIK no longer have the time nor sufficient enthusiasm to compile it

Haha, I suppose I'm one of the lucky few who got to close Pandora's box againWell, if I had my way you'd sorely regret offering it to me, but AFAIK no longer have the time nor sufficient enthusiasm to compile it, but thanks anyway!

This is to mitigate edge diffraction, yes? I was considering 3D-printing or laser cutting something to that effect.If you want to go the 'extra mile', add a very thick false baffle over the baffle, driver cutout chamfered at ?? angle or roundover that sounds best and duplicate it around its perimeter.
This is the final hurdle, I promise -- What exactly do you mean by different end offsets? As is offset from the hornmouth/throat an inequal amount?we want the divider to 'snugly' fit in between its two ends at different end offsets (no hot spots to crack)
On the subject of bracing, this is the latest iteration.
The bracing now spans ~71 percent of the acoustic path length, with holey panels offset according to the golden ratio. Additionally I've added dowels/threaded rods across the hornmouth, also spaced according to the golden ratio in the X and Y axes. If using 6mm (1/4") MDF and 30mm dowels, the total volume lost only comes out to about 1.6L.
Primary worry I have with this design is that the many edges perpendicular to the flow of air might generate chuffing noise as air flows over them. Will also most likely break up laminar flow which, based purely on intuition, should affect the coupling ability of the horn -- So maybe I'd be better off using solid panels?
If you play around with HornResp you will discover some things with "reagular" size horns. Low pass frequency is largely determined by horn length and output eveness by mouth area. Messing around with flare types like exponental, hyperbolic and such does nothing in comparison.
Why no braces at the throat where the pressure is highest? The bracing at the mouth is good as the freee edges of the box is way way weaker than those braced by a perpendicular wall.
Why no braces at the throat where the pressure is highest? The bracing at the mouth is good as the freee edges of the box is way way weaker than those braced by a perpendicular wall.
Finally we see nice holey braces. Their placement should be such that the sub-spans created are not equal.
dave
dave
Given time, we all see the reason of holey bracesFinally we see nice holey braces. Their placement should be such that the sub-spans created are not equal.

I'm still curious about whether or not the hole surfaces perpendicular to the flow of air create wind noise and disrupt laminar flow, though -- If laminar flow is even something one needs on the internal surfaces of the horn.
That would be because I know next to nothing about speaker construction. What would be the least intrusive kind of brace? Considering the throat is the smallest section of the horn, any bracing would have a proportionally larger impact on the total acoustical area.Why no braces at the throat where the pressure is highest?
This is to mitigate edge diffraction, yes? I was considering 3D-printing or laser cutting something to that effect.
This is the final hurdle, I promise -- What exactly do you mean by different end offsets? As is offset from the hornmouth/throat an inequal amount?
The bracing now spans ~71 percent of the acoustic path length, with holey panels offset according to the golden ratio. Additionally I've added dowels/threaded rods across the hornmouth, also spaced according to the golden ratio in the X and Y axes. If using 6mm (1/4") MDF and 30mm dowels, the total volume lost only comes out to about 1.6L.
Primary worry I have with this design is that the many edges perpendicular to the flow of air might generate chuffing noise as air flows over them. Will also most likely break up laminar flow which, based purely on intuition, should affect the coupling ability of the horn -- So maybe I'd be better off using solid panels?
Correct.
OK, just been spouting proper box design basics and now down to horn specifics...........
Correct; as Dr. Boar noted, the greatest pressure is at the horn throat, so bracing begins at this end and if you take my ~71% as a continuous length, which applies to bracing a basic box, then it will terminate too far from the terminus/mouth, so in general and as shown in (hard to see) Tom's TH we ignore corners, tight bends as they are inherently stiff/rigid enough from the side walls and any long spans only need to be braced ~71% of its length and offset from its bends. 😉
Re 'holey' bracing; never seen any measurements, but common sense 'says' they will create some 'stiction' unless heavily rounded over, so personally only either use solid/smooth Masonite or similar or cut them out of marine grade or similar quality plywood to leave a framework of well sanded 'saw blade' pattern bracing to mimic truss bridge construction.
Note too that I normally used 3/4" thick, so always added 3/4" to the design width.
Re damping; from a long ago? thread (forgot to save the link):
BLHs, some TLs OTOH really requires a bit of knowledge as to how (ideally) continuous the air mass 'plug' is whipping back n' forth along its axial path length at the SoS, so friction/stiction plays a (significant) role in the horn's HF response, hence the need for keeping lossy damping to a minimum when trying to get the right hand-off for best blend to the driver's forward radiation at smoothest response (a tall order!), though if a bass horn the acoustic XO will be low enough that we just want to quell as much HF coming out of the horn as practical, so damping is somewhat more dense and in different locations from the wide range, so to a great extent each differing BLH horn design is ~unique, ergo IME no easy 'rules-of-thumb'.
So they should all be offset from one another by some uneven/golden ratio subdivision of the total span, then?
When i am bisecting a panel i usually place one edge of thr ebrace on th ecentre line.
More generally: The aspect ratio of subpanels created by a brace shoukd be gretaer then the aspect ratio of the panel being braced, and those subpanel aspect ratios should differ.
curious about whether or not the hole surfaces perpendicular to the flow of air create wind noise and disrupt laminar flow
They are hopefully too small to be seen by the much-much longer wavelengths.
dave
Stands to reason. I suppose another benefit over solid panels is that you even out the pressure somewhat and don't end up with differential velocities either side of the braces.They are hopefully too small to be seen by the much-much longer wavelengths.
This still isn't quite making sense to me, sorryThe aspect ratio of subpanels created by a brace shoukd be gretaer then the aspect ratio of the panel being braced, and those subpanel aspect ratios should differ.

At long last, I get it!any long spans only need to be braced ~71% of its length and offset from its bends. 😉
Hm. Makes me wonder if it might be worth it having the braces be "stair step" curves of stacked smaller panels to bleed off HF while also creating a more rigid geometry.[...]though if a bass horn the acoustic XO will be low enough that we just want to quell as much HF coming out of the horn as practical, so damping is somewhat more dense and in different locations from the wide range, so to a great extent each differing BLH horn design is ~unique
Imagine looking at the speaker head-on, and the braces having a stepped airfoil profile. Not curved enough to meaningfully affect path length, but rather to "catch" a bit of the air column, redirecting LF but diffusing HF. Will CAD it up when i get home.
I can see how it might create pressure eddies that could generate noise, though.
Here's the aforementioned stepped brace. If this isn't acceptable, wouldn't at the very least a curved brace be stronger, structurally?
Last edited:
This still isn't quite making sense to me, sorry
That is why i gave the practical example first.
I also should have mentioned that i typically am for 30-40% holes so if an 18mm holey brace is installed th ewidth of the box should increas eby 12mm.
dave
No, from holes = stiction to "stair step" = much higher stiction in theory and no it won't strip out HF because the HF is on the leading edge of the wavefront where particle density is exponentially much lower, i.e. the divider will be minimally to completely transparent with increasing frequency above the horn's gain BW.Hm. Makes me wonder if it might be worth it having the braces be "stair step" curves of stacked smaller panels to bleed off HF while also creating a more rigid geometry.
Imagine looking at the speaker head-on, and the braces having a stepped airfoil profile. Not curved enough to meaningfully affect path length, but rather to "catch" a bit of the air column, redirecting LF but diffusing HF. Will CAD it up when i get home.
I can see how it might create pressure eddies that could generate noise, though.
Correctomundo and personally like my (mid) bass 'straight, no chaser'. 😉
Sorry for not reading all of the thread, but I will just add my experience with Coral 8. We are back to the seventies - to after year 2000 - they lived with me for more than 25 years. I started with Lowther, but the Coral Beta 8 was fantastic in the Duelund concrete horns. I am still missing the openness in the sound,. My set was built by Duelund himself.
Two links here
http://archive.nerds.dk/article/index.html?aid=44.html
https://web.archive.org/web/20011205075152/http://www.muyiovatki.dk/duelund/duelund.htm
Two links here
http://archive.nerds.dk/article/index.html?aid=44.html
https://web.archive.org/web/20011205075152/http://www.muyiovatki.dk/duelund/duelund.htm
So this Duelund concrete is made of dual horns? And so all the lamination, fluid, braces and holes doesn't hold in this case. Is the dual/divided path my hallucination or ..?!
Btw I like OP's sketch but I keep wondering why the upper-ghost chamber on the baffle isn't eliminated, such to make a sloped baffle - B&W used it -?
Btw I like OP's sketch but I keep wondering why the upper-ghost chamber on the baffle isn't eliminated, such to make a sloped baffle - B&W used it -?
Is the dual/divided path my hallucination or ..?
I have seen this done often.
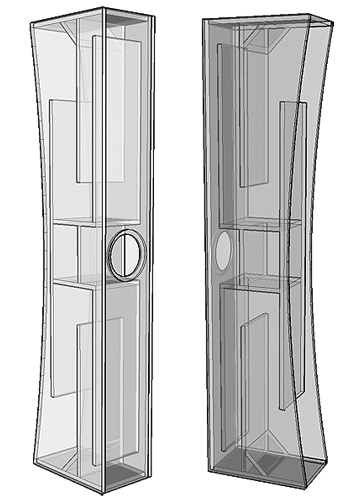
dave
- Home
- Loudspeakers
- Full Range
- Modified Beta 8 BLH Design? Help!