Edit: I'm not a chess player, but are there any good rules for a game? I don't mean the rules of the moves and such, but like known-good strategies?
Yes, the ABC rule.
Always
Be
Checkmating
Yes but these obstacles are always in different places, and then you get onto via rules, layer changing rules etc. all different from one design to another... You also have to be aware of cutting your escape routes and blocking routing channels... again skills that are learned... Its OK routing a board with say 5000 connections and getting 90-95% success, then you spend a week trying to clear paths for the remaining routes...
The general consensus from PCB forums such as EDA board and LinkedIn is the same regarding auto routers and placers... they are no good.
As said good PCB design is a skill that is part academic learning and certain skills that are developed by hands on doing layouts.
The boards I am doing now all consist of high current signals with circular Mil connectors so I am having to draw copper pours to get the copper to the inside pins, as well as make sure some signal pairs are broadside routed on adjacent layers, certain signals do not cross because of capacitive coupling issues, all copper to be just the right amount for the current, no more to minimise coupling again all good clean fun, find software that could do this for me (or the engineer) and I would be redundant, luckily it is the other way round and good PCB designers who know there stuff are in demand...
The general consensus from PCB forums such as EDA board and LinkedIn is the same regarding auto routers and placers... they are no good.
As said good PCB design is a skill that is part academic learning and certain skills that are developed by hands on doing layouts.
The boards I am doing now all consist of high current signals with circular Mil connectors so I am having to draw copper pours to get the copper to the inside pins, as well as make sure some signal pairs are broadside routed on adjacent layers, certain signals do not cross because of capacitive coupling issues, all copper to be just the right amount for the current, no more to minimise coupling again all good clean fun, find software that could do this for me (or the engineer) and I would be redundant, luckily it is the other way round and good PCB designers who know there stuff are in demand...
Last edited:
. Rant time🙂 Even though most people think anyone can do a PCB design to do todays modern complex designs properly takes a lot of skill and learning, not only do we have to understand the circuit, but also PCB fabrication, circuit assembly etc. etc.
Anyone can do a PCB if they have enough iterations 🙂. I realised long ago that it was worth every penny on anything over trivial to pay someone who was experienced in the art.
With todays digital you also get a constraint browser as well so you can control skew groups delays, diff pair matching, trace impedance as you change layers and thus the distance to return paths have a look at DDR2 routing for 2 devices (single DDR chips not dims) on a T bus, great fun (DDR3 is easier to lay out with fly by routing). Micron have some good guides...
And of course when you can start to create RF structures on the board. That's a whole new pile of fun.
JN,
Not quite that simple, if I have 70 pF per foot (typical) 4 twisted pairs, and 1500 feet of cable. Just getting the guys to twisted each pair with a different twist seems to be rocket science to them. Asking for concentric shields went beyond that.
Color codes they can do. Jacket color was an issue! But the characteristic impedance of the twisted pairs is in the very right range.
Meets CL3, that they understand.
I've no idea what you meant.
Put a zobel at the load end to prevent load uncoupling as seen by the amp at the far end of the cable.
Characteristic impedance of the cable has little to do with twist pitch. The only thing twist is being relied upon to do is maintain conductor spacing.
As to twist pitch variations, they do not need to know anything about magnetic orthogonality. They just need to know what pitch to twist to.
It's like what I had to do when the cable pullers were pulling the hf coax runs. I could try to explain characteristic imedance, and inductance per foot, and centroids based external field cancellation, and radius of curvature vs coaxial field profiles, or...what I actually told them... (remember, they were all twenty somethings, and all mechanically minded)
""Think of the coax cable as a brake line, or refrigerator tubing. If you are trying to put it through a hole in the firewall, if you bend it too much, it will go oval such that it won't go through a tight hole, and can also constrict. If you aren't careful with the times microwave wire and kink it by bending, the signal will see that ovalled or kinked part, and the end users will not be very happy.""
We've pulled over four thousand rf coax cables so far, and not one of them had a problem. The wire pulling guys still do not know e/m theory for transmission lines, but they understood what was required.
John
Last edited:
I am living this right now. A novice layout guy was retained, and although well-meaning, has a great deal to learn. I am paying the price for not having learned layout myself. I recommended a skilled person, but somehow the chemistry was just not there and they were less than enthused.Anyone can do a PCB if they have enough iterations 🙂. I realised long ago that it was worth every penny on anything over trivial to pay someone who was experienced in the art.
I worked with a guy once who thought he could do layout. He also was the owner of his little company, and had set a rather low standard for accuracy. He announced once that he was ordering boards at the end of that week, regardless of whether I approved or not (we had gone through numerous cycles of proofing and changes, with the usual occurrence of more errors produced when fixes of other errors were made). I said By all means, if you want to waste your money, but it will be a disaster. He also did his own product literature, and it was so hopelessly amateurish as to be ludicrous. I begged him to let me proof the literature, which he didn't do. I told him what a terrible impression the literature was making on the prospective customers, and he said Oh these guys are just dumb plumbers. I said they are probably smarter than you and making more money as well.
As the old saying goes, Never enough time to do it right. Always enough time to do it over.
That's a nice approach. The bane of electricians pulling coax for master antenna systems and their ilk without such analogies... One would break into walls to find that they had tied RG59 around nails and so forth. No surprise that the systems didn't work very well.It's like what I had to do when the cable pullers were pulling the hf coax runs. I could try to explain characteristic imedance, and inductance per foot, and centroids based external field cancellation, and radius of curvature vs coaxial field profiles, or...what I actually told them... (remember, they were all twenty somethings, and all mechanically minded)
""Think of the coax cable as a brake line, or refrigerator tubing. If you are trying to put it through a hole in the firewall, if you bend it too much, it will go oval such that it won't go through a tight hole, and can also constrict. If you aren't careful with the times microwave wire and kink it by bending, the signal will see that ovalled or kinked part, and the end users will not be very happy.""
We've pulled over four thousand rf coax cables so far, and not one of them had a problem. The wire pulling guys still do not know e/m theory for transmission lines, but they understood what was required.
John
I worked with a guy once who thought he could do layout. He also was the owner of his little company, and had set a rather low standard for accuracy. He announced once that he was ordering boards at the end of that week, regardless of whether I approved or not (we had gone through numerous cycles of proofing and changes, with the usual occurrence of more errors produced when fixes of other errors were made). I said By all means, if you want to waste your money, but it will be a disaster. He also did his own product literature, and it was so hopelessly amateurish as to be ludicrous. I begged him to let me proof the literature, which he didn't do. I told him what a terrible impression the literature was making on the prospective customers, and he said Oh these guys are just dumb plumbers. I said they are probably smarter than you and making more money as well.
It still happens there are as many bad PCB designers as there are good ones, many seem to think a few days learning the software is all they need...
That's a nice approach. The bane of electricians pulling coax for master antenna systems and their ilk without such analogies... One would break into walls to find that they had tied RG59 around nails and so forth. No surprise that the systems didn't work very well.
2 1/4" Heliax installed by gorillas can cause some interesting faults as well. Instead of bending the cable to fit the LNA, they screwed the LNA to the cable then stood on it. Until I saw it I did not believe you could completely shear the inner basket on a 7/16 RF connector. Luckily I was not in charge of the gorillas, just shouted at by the client.
I've no idea what you meant.
Put a zobel at the load end to prevent load uncoupling as seen by the amp at the far end of the cable.
Characteristic impedance of the cable has little to do with twist pitch. The only thing twist is being relied upon to do is maintain conductor spacing.
As to twist pitch variations, they do not need to know anything about magnetic orthogonality. They just need to know what pitch to twist to.
It's like what I had to do when the cable pullers were pulling the hf coax runs. I could try to explain characteristic imedance, and inductance per foot, and centroids based external field cancellation, and radius of curvature vs coaxial field profiles, or...what I actually told them... (remember, they were all twenty somethings, and all mechanically minded)
""Think of the coax cable as a brake line, or refrigerator tubing. If you are trying to put it through a hole in the firewall, if you bend it too much, it will go oval such that it won't go through a tight hole, and can also constrict. If you aren't careful with the times microwave wire and kink it by bending, the signal will see that ovalled or kinked part, and the end users will not be very happy.""
We've pulled over four thousand rf coax cables so far, and not one of them had a problem. The wire pulling guys still do not know e/m theory for transmission lines, but they understood what was required.
John
We ain't arguing. There have to be Zobel networks at each loudspeaker run as the impedance over the amplifier's bandwidth approaches 100/1. (One amplifier manufacturer will not honor warranty repairs if they know shielded cable is used!)
Didn't say the impedance has to do with the twists. I have funny insulation to meet CL3 and get the right impedance with the conductor sizes used.
Twist pitch is a an issue due to crosstalk which increases a bit with shielding. Becomes a bit of an issue when the power levels for each driver in a loudspeaker system have quite different drive levels.
Last edited:
2 1/4" Heliax installed by gorillas can cause some interesting faults as well. Instead of bending the cable to fit the LNA, they screwed the LNA to the cable then stood on it. Until I saw it I did not believe you could completely shear the inner basket on a 7/16 RF connector. Luckily I was not in charge of the gorillas, just shouted at by the client.
The biggest I had to contend with was LMR 900, that was only 300 foot lengths (IIRC). Had to keep bend radius over two feet. For specials like that, I will don a hardhat, gloves, and safety goggles, and I will put myself in the most critical and most difficult location to help perform the work. Everybody responds much better if the engineer telling them what to do actually gets hands dirty with them, and then gives them the freedom and trust to continue the work by themselves. Once they own the work, everybody is happy.
More specifically, as they later pulled the LMR900 off the spool, they found a section which had a big crease in it. While they could have simply pulled it into the tray without telling anybody, they instead stopped the pull and notified me that the cable had a crease.
I then called in the RF guy to determine if it was an issue. It wasn't, but it was an excellent example of people owning a job, as opposed to simply doing a job. Respect does a lot.
John
Last edited:
We ain't arguing.
Didn't say we were. I just said I didn't know what you meant to say..
John
I used to work with a guy like that, bcarso. I got along with him fine, so when a business opportunity came up in 1978 to make my own audio equipment, I brought him in to do all the fabrication including cases and layout. His first layout with me was a battery powered headamp that picked up hum very easily. That should have warned me, but I ignored it. Then UC Berkeley hired me to participate in an ultra low noise electronic design, and they hired him to do the layout. The layout was so bad, that it was rejected, and had to be redone by someone else. This is when I was sure that he was incompetent to do layout, but I just could not tell him due to his overt denial. He, I also realized, was incompetent in other areas as well.
It just so happened that a competitor secretly was hiring him away from me, and they gloated when they got him. I just said, wait 5 years and we can talk about your 'victory' then. He started out OK with them at first, just as with me, BUT in a year or so they threw him out of their company with 'prejudice'. They hated the guy, and so it goes.
I floated along with a few other layout guys, one who did OK, and was later hired full time by Dolby, with my blessing. Then, I met Carl Thompson and we have worked together for the last 30+ years or so. A great layout is worth its weight in gold when it comes to successful audio design.
It just so happened that a competitor secretly was hiring him away from me, and they gloated when they got him. I just said, wait 5 years and we can talk about your 'victory' then. He started out OK with them at first, just as with me, BUT in a year or so they threw him out of their company with 'prejudice'. They hated the guy, and so it goes.
I floated along with a few other layout guys, one who did OK, and was later hired full time by Dolby, with my blessing. Then, I met Carl Thompson and we have worked together for the last 30+ years or so. A great layout is worth its weight in gold when it comes to successful audio design.
I've always hand drawn PCB layouts (in the early years), and laterly by manually routing layouts in DipTrace working directly on screen from a printed schematic. I find that mostly things fall into place... then you have a think and come back and retweak continually homing in on your goal.
The first one has quite an elaborate grounding scheme and symmetry that an auto router could never get close to, the second a much simpler affair but again all manually routed.
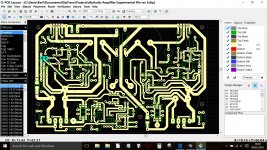
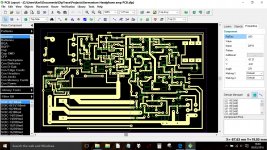
The first one has quite an elaborate grounding scheme and symmetry that an auto router could never get close to, the second a much simpler affair but again all manually routed.
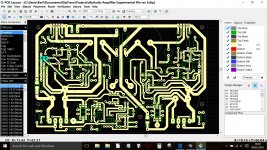
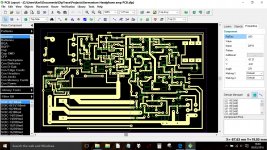
John, we seem to have had similar experiences. I also found "The Man" for the job in my fifth go, with 25 years of professional experience with professional electronics, including RF work as well, as that ain't no pot of roses. But I'm happy with his work, which is both electrically and visually very neat and tidy. He admitted that what I saw was most often the n-th iteration, he does the first go, looks it over and either corrects it or does it all over again if he's not happy with the result. Sure, I could do it myself, but I am well aware that I'm no match for his skills.
Shades of Elon Musk saying that the raids on and defections of his engineers to Apple etc. didn't bother him, as they were not anywhere near his best 🙂It just so happened that a competitor secretly was hiring him away from me, and they gloated when they got him. I just said, wait 5 years and we can talk about your 'victory' then. He started out OK with them at first, just as with me, BUT in a year or so they threw him out of their company with 'prejudice'. They hated the guy, and so it goes.
I have never had a perfect layout person to work with, but some were much better than others. One who was fairly talented had such a bad attitude that I swore I would never use him again. Another one that took the cake as it were told me frequently how great he was. Then he did a layout and the hurried client bought boards. There were many many errors, pinouts, you name it, starting with a reversed a.c. adapter jack! I tried to fix some things manually and finally (after about 4k worth of labor which remains unpaid, and as the company fell into near-insolvency) gave up and said You must fix your mistakes!
His response: Why should I do that if we don't know that your circuitry works? And then the client suggested that I should do the troubleshooting and hand mods for free.
One can understand why these people earned a very high position on my permanent $hit list.
And of course when you can start to create RF structures on the board. That's a whole new pile of fun.
Yes, and you can forget FR4 for that... I'm surprised that none of the snake oil types haven't got into sophisticated substrates claiming it's needed for audio... 😀
On the pcb front, unless you etch your own pcbs the low cost prototyping services available these days make 4 layer boards very cost effective even for diy... Very useful.
2 1/4" Heliax installed by gorillas can cause some interesting faults as well. Instead of bending the cable to fit the LNA, they screwed the LNA to the cable then stood on it. Until I saw it I did not believe you could completely shear the inner basket on a 7/16 RF connector. Luckily I was not in charge of the gorillas, just shouted at by the client.
Yes, I've been amazed at what butchery has been done to even big RF connectors... We also now have, as part of installer training, a how-to for SMA connectors that starts with "do not use a 12 inch wrench to tighten an SMA".... Sigh...
Yes, I've been amazed at what butchery has been done to even big RF connectors... We also now have, as part of installer training, a how-to for SMA connectors that starts with "do not use a 12 inch wrench to tighten an SMA".... Sigh...
We have mini SMA-only torque wrenches for that. I found it hard to believe but I was told the cal standards specify exact torque especially when working at >10GHz.
Yes, and you can forget FR4 for that... I'm surprised that none of the snake oil types haven't got into sophisticated substrates claiming it's needed for audio... 😀
.
FR4 is good to 2GHz at least if the layup is controlled, although a colleague of mine once wrote in a report 'FR4 is good...for canoes'.
Our very own JC used teflon substrate for the blowtorch.
We have mini SMA-only torque wrenches for that. I found it hard to believe but I was told the cal standards specify exact torque especially when working at >10GHz.
I have seen intermod results change by 30dB just by torquing up an RF connector properly.
- Status
- Not open for further replies.
- Home
- Member Areas
- The Lounge
- John Curl's Blowtorch preamplifier part II