Just think of moment of inertia…will depend on where most of the mass is. A lighter platter could have a bigger moment of inertia depending on the profile... Is not just weight
Last edited:
BUT the basic size and shape of the platters is almost the same in every case. So, many times the mass almost always give many times the inertia. Why do you think they would make a heavy platter in the first place?
I have two on-loan Heybrook TT2 which are sometimes billed as a "poor-man's Linn". They have so many things wrong with them, but once you get the platter spinning (often requiring some external assistance) they play records. I'll get round to weighing the platter.
This is also what you must do frequently before replacement...... Why do diamond needles and vinyl records wear out? | Breier Audio Video
If you play just 2 LP's a day on average, that means you replace tip every year or two.
Unfortunately, where does that leave the used LP? you have to replace the LP also to keep noise and distortion as best it will ever be/ as new.
THx-RNMarsh
If you play just 2 LP's a day on average, that means you replace tip every year or two.
Unfortunately, where does that leave the used LP? you have to replace the LP also to keep noise and distortion as best it will ever be/ as new.
THx-RNMarsh
BUT the basic size and shape of the platters is almost the same in every case.
If that's true, the masses will be similar unless they're made from bizarrely different materials.
The AR and Linn platters are both principally aluminum. They are featherweight compared to actual high mass platters. My TT uses lead-weighted acrylic, and has a much heavier duty bearing. There's heavier ones out there for sure, but the contrast with AR or Linn is striking. The Technics platters are lower mass, comparable to the AR or Linn, lighter than an Oracle, lighter than a Win (to name two that I've also used for an extended period), way lighter than the old Empire or Microseiki.
The correlation between mass and performance is not a strong one. There do seem to be cults around certain brands (e.g., Linn, Lenco, Garrard), the vociferousness of which similarly doesn't correlate well with performance. The correlation with cost is even poorer.
Same address as the old Audio Dimensions? Any connection?
LP12 is high zinc content so around 2.5 times the density of Al. Roksan used to make a big play of the platter being Al but higher inertia than Linn.
Me, I just couldn't hack the bouncy bouncy. Cost per year of my turntable has been low 🙂
Me, I just couldn't hack the bouncy bouncy. Cost per year of my turntable has been low 🙂
Brits, as always, tried to get away 'on the cheap' 😀is the nearest brits ever got to building a high mass turntable. I so lusted after one as a student.
Take a look at this German monster. 50 kg platter, is that enough?
Apolyt
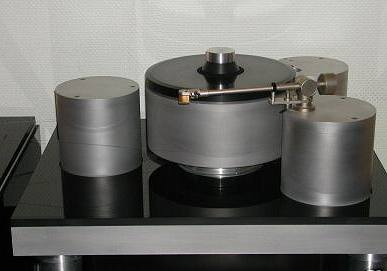
Several manufacturers have made a big deal about using polymers (e.g., acrylic, polycarbonate), rationalizing that they provide an acoustic impedance match to the vinyl, thus don't reflect waves caused by stylus rattling. I haven't seen any good data but the argument is plausible (and yes, plausible enough that I use a platter designed with that in mind), and the ability to absorb stray energy seems to me to be a positive.
Interesting, it doesn't raise any eyebrows that test records might be pre-distorted or even test records are not but many LP's are? IMHO makes a lot of published data from the last few decades a waste of time.
Does anyone remember RCA dynagroove - pre distortion to compensate for stylus shape, inner grove tracking error, etc and general backache and other maladies
Interesting, it doesn't raise any eyebrows that test records might be pre-distorted or even test records are not but many LP's are? IMHO makes a lot of published data from the last few decades a waste of time.
😎🙂
-RNM
J. Gordon Holt certainly didn't like the RCA "dynagroove" stuff:
Down with Dynagroove! | Stereophile.com
But, there's more to the story. RCA made some important other improvements to their recording techniques at about the same time that "dynagroove" was unleashed:
Article: Dynagroove: The Sound of Tomorrow
Cheers,
ZAPNSPARK
Down with Dynagroove! | Stereophile.com
But, there's more to the story. RCA made some important other improvements to their recording techniques at about the same time that "dynagroove" was unleashed:
Article: Dynagroove: The Sound of Tomorrow
Cheers,
ZAPNSPARK
J. Gordon Holt certainly didn't like the RCA "dynagroove" stuff:
Down with Dynagroove! | Stereophile.com
But, there's more to the story. RCA made some important other improvements to their recording techniques at about the same time that "dynagroove" was unleashed:
Article: Dynagroove: The Sound of Tomorrow
Cheers,
ZAPNSPARK
Thanks Jim, the dynamic stylii correlator looks to be what I was interested in.
Same address as the old Audio Dimensions? Any connection?
I have no idea who they are...... just one of several on the topic found on LP wear/tip replacement.
-RNM
So much knowledge has been lost in the last 30 years. Here is a collection of nuggets I pulled from ancient memory.
Nakamichi made a turntable that would center an off center record automatically in the '80s. High mass platters have been around forever. Final Audio had a 50 Lb brass platter in the late 70's driven from a string. The first gen Thorens TD124 used a cast iron platter to get mass and a separate aluminum platter on top that would start and stop fast. Needless to say the cast iron was a problem with moving coil cartridges.
Some of the servo controlled turntables (Denon for example) used a magnetic track recorded under the platter for feedback. You can also use several pickups arraigned symmetrically to cancel out of round etc. Pabst used two toothed rings to generate the pulses which worked quite well.
I did measurements of a Technics SP10 and a Linn for a long defunct magazine, "Sound Advice" on flutter and wow using a CD4 test record (30 KHz reference tone) and a high resolution spectrum analyzer (Tek 7L5) looking for differences. What I saw was that the spectrum of the Linn was centered around 30 KHz with pretty sharp drops on both sides. the SP10 has a double hump distribution with a "null" at 30 KHz, showing a sort of deadband around the center frequency. I think much better can be had from servos, especially if you don't need it to come to speed in 1/4 turn.
Some Japanese manufacturer made a turntable that was vertical and had some sound rationale for it. The Finial Audio turntable would remove all issues around needle drag using an optical pickup but its way too expensive for us mortals.
There are some portable lathes with pivoted arms but they work with pregrooved records. Normally the cutterhead is driven from a leadscrew to move across the featureless disk.Changing the speed of the leadscrew changes the spacing of the grooves.
The RCA Dynagroove was an equalizer (stepped passive) driven from the leadscrew to boost the highs at the inner groves. But that story would not sell. And that was the days of Mad Men so the story was "embroidered" to be much more interesting. There was also some real money to be made in the music and playback industries. I think that free music (pick your free streaming service) will be the end of any music industry.
Groove computers are interesting. Early ones used a preview head on the tape machine. Later ones have a digital delay that the audio passes through to the cutterhead. (Many of your favorite albums were cut with one of these.) The bass is summed also to remove "excess" vertical modulation. Unfortunately there is usually some significant phase difference between mikes at even low frequencies if the instrument is not perfectly centered so the process will compromise bass. Not to worry,most of the speakers sold today have no usable output below 80 hz and rely on tricks to "recreate" bass they aren't actually producing.
The Technics linear tracking story does highlight how good engineering does not need to add to the cost of a product if its successful. No one is making anything like that today?
Nakamichi made a turntable that would center an off center record automatically in the '80s. High mass platters have been around forever. Final Audio had a 50 Lb brass platter in the late 70's driven from a string. The first gen Thorens TD124 used a cast iron platter to get mass and a separate aluminum platter on top that would start and stop fast. Needless to say the cast iron was a problem with moving coil cartridges.
Some of the servo controlled turntables (Denon for example) used a magnetic track recorded under the platter for feedback. You can also use several pickups arraigned symmetrically to cancel out of round etc. Pabst used two toothed rings to generate the pulses which worked quite well.
I did measurements of a Technics SP10 and a Linn for a long defunct magazine, "Sound Advice" on flutter and wow using a CD4 test record (30 KHz reference tone) and a high resolution spectrum analyzer (Tek 7L5) looking for differences. What I saw was that the spectrum of the Linn was centered around 30 KHz with pretty sharp drops on both sides. the SP10 has a double hump distribution with a "null" at 30 KHz, showing a sort of deadband around the center frequency. I think much better can be had from servos, especially if you don't need it to come to speed in 1/4 turn.
Some Japanese manufacturer made a turntable that was vertical and had some sound rationale for it. The Finial Audio turntable would remove all issues around needle drag using an optical pickup but its way too expensive for us mortals.
There are some portable lathes with pivoted arms but they work with pregrooved records. Normally the cutterhead is driven from a leadscrew to move across the featureless disk.Changing the speed of the leadscrew changes the spacing of the grooves.
The RCA Dynagroove was an equalizer (stepped passive) driven from the leadscrew to boost the highs at the inner groves. But that story would not sell. And that was the days of Mad Men so the story was "embroidered" to be much more interesting. There was also some real money to be made in the music and playback industries. I think that free music (pick your free streaming service) will be the end of any music industry.
Groove computers are interesting. Early ones used a preview head on the tape machine. Later ones have a digital delay that the audio passes through to the cutterhead. (Many of your favorite albums were cut with one of these.) The bass is summed also to remove "excess" vertical modulation. Unfortunately there is usually some significant phase difference between mikes at even low frequencies if the instrument is not perfectly centered so the process will compromise bass. Not to worry,most of the speakers sold today have no usable output below 80 hz and rely on tricks to "recreate" bass they aren't actually producing.
The Technics linear tracking story does highlight how good engineering does not need to add to the cost of a product if its successful. No one is making anything like that today?
I have no idea who they are...... just one of several on the topic found on LP wear/tip replacement.
-RNM
A Japanese vendor of diamonds for styli told me that 500 hours was the expected life of the tip. For a $10,000 cartridge that would be about $10 a side to play. An afternoon of listening would be about the same as a ticket to a major opera performance (upper balcony but still. . .)
I once came across a boxed CD set on the DG label (from a library) that was unplayable. The discs had a curious mottled appearance when held to the light and with a bright light behind you could read a book through them. That was an all over kind of 'rot'.
My own CD's which date back to day one have never suffered at all. One thing I do with all new CD's and that goes against what you might read (so you do this at your own risk) is to heavily polish them with a silicon based polish. I use to use Servisol 'Excel' polish for this but any similar household polish is the same. Whether that helps seal the finish I can't say but all I know is my discs are pristine and have never suffered a problem in over 30 yrs.
My own CD's which date back to day one have never suffered at all. One thing I do with all new CD's and that goes against what you might read (so you do this at your own risk) is to heavily polish them with a silicon based polish. I use to use Servisol 'Excel' polish for this but any similar household polish is the same. Whether that helps seal the finish I can't say but all I know is my discs are pristine and have never suffered a problem in over 30 yrs.
- Status
- Not open for further replies.
- Home
- Member Areas
- The Lounge
- John Curl's Blowtorch preamplifier part II