I had read about bending wave drivers a very long time ago but then I listened to a Manger loudspeaker more than 2 decades ago which inspired me to build my own loudspeaker with these MSW (Manger Schall Wandler). I think the main reason they sound better (at least in some music relevant aspects) than almost any pistonic driver is that they have a very wide frequency range avoiding any crossover above the low mids and their very excellent time behavior. But the MSW have some significant issues with uneven frequency response and distortion peaks. I found some improvements by adding Moongel absorption pads to the center of these drivers and I wrote about it, including some measurements, 12 years ago https://www.diyaudio.com/community/threads/manger-msw-moongel.208995/ . This year Manger made some upgrades to that design https://mangeraudio.com/en/discover/blog/press-release-the-new-manger-high-tech-sound-transducer-w06 with an upgrade to the center damper which reduced the distortion (I found no measurements to verify that).
I was also interested in other bending wave drivers and I once visited the Göbel loudspeaker factory to listen to their bending wave speakers. They sounded quite good but were never available for DIY and it is strange that I did not find any measurements of those loudspeakers in spite of the fact that Oliver Göbel originally provided acoustic measurements before he actually marketed that design. His most expensive flagship models don’t even use bending wave topology.
There are omnidirectional bending wave drivers like German Physics, based on a Lincon Walsh invention, but I was never interested in something which has so much room reflected sound vs direct sound.
Bending wave drivers are simulating an infinite membrane as the surround is designed to absorb all vibration. In contrast distributed mode loudspeakers (DML) are using a finite membrane. I played around with some of the Hiwave/Tectonic exciters and lost my interest fast in DML. I also considered BMR drivers almost as a hybrid with a pistonic driver and a vibrational device but after testing some of them it also did not divert me from real bending wave drivers.
Manger MSW uses a round (semi) soft membrane material with a star shaped damping structures in the periphery and a central damper. Göbel uses a stiff rectangular membrane with damping laser cuts on the periphery.
I started playing with the bending wave driver concept at least 2 decades ago but about 10 years ago I thought my design sounded better than the MSW when I replaced the MSW with my design. Still, I am playing around with different components, so I think I will never be done tinkering, but I think I should publish something now. That will need to be more than one single post.
There are two main components to a bending wave driver: the membrane and its damping surround and the magnetic motor /voice coil design. The goal is to activate all frequencies evenly and prevent any back reflection which would cause interference.
One issue with the majority of loudspeaker drivers, including the MSW, is that the voice coil is round and concentric to a round membrane, having a constant distance to the perimeter and to the center leading to more specific vibrational modes. I decided to use a rectangular/linear voice coil which has varying distances to the perimeter distributing vibrational modes. I also found that using any shape of membrane with corners like a rectangle causes strong modes which can not be efficiently damped.
This is my recent test speaker enclosure, the walls are made from flax composite with a balsa core. The driver plate is made from an aluminium sheet laminated to Richlite panels with Loctite viscoelastic glue.
Here is a frequency response of one recent version (Fuzz Measure in room at 0.3m)
Step response (the negative dip before the rise and some of the small ringing at the peak is measurement microphone dependent, this is with Umik 2 and Umik 1 looks different there, otherwise identical)
A lot more detail to follow in additional posts, slowly
I was also interested in other bending wave drivers and I once visited the Göbel loudspeaker factory to listen to their bending wave speakers. They sounded quite good but were never available for DIY and it is strange that I did not find any measurements of those loudspeakers in spite of the fact that Oliver Göbel originally provided acoustic measurements before he actually marketed that design. His most expensive flagship models don’t even use bending wave topology.
There are omnidirectional bending wave drivers like German Physics, based on a Lincon Walsh invention, but I was never interested in something which has so much room reflected sound vs direct sound.
Bending wave drivers are simulating an infinite membrane as the surround is designed to absorb all vibration. In contrast distributed mode loudspeakers (DML) are using a finite membrane. I played around with some of the Hiwave/Tectonic exciters and lost my interest fast in DML. I also considered BMR drivers almost as a hybrid with a pistonic driver and a vibrational device but after testing some of them it also did not divert me from real bending wave drivers.
Manger MSW uses a round (semi) soft membrane material with a star shaped damping structures in the periphery and a central damper. Göbel uses a stiff rectangular membrane with damping laser cuts on the periphery.
I started playing with the bending wave driver concept at least 2 decades ago but about 10 years ago I thought my design sounded better than the MSW when I replaced the MSW with my design. Still, I am playing around with different components, so I think I will never be done tinkering, but I think I should publish something now. That will need to be more than one single post.
There are two main components to a bending wave driver: the membrane and its damping surround and the magnetic motor /voice coil design. The goal is to activate all frequencies evenly and prevent any back reflection which would cause interference.
One issue with the majority of loudspeaker drivers, including the MSW, is that the voice coil is round and concentric to a round membrane, having a constant distance to the perimeter and to the center leading to more specific vibrational modes. I decided to use a rectangular/linear voice coil which has varying distances to the perimeter distributing vibrational modes. I also found that using any shape of membrane with corners like a rectangle causes strong modes which can not be efficiently damped.
This is my recent test speaker enclosure, the walls are made from flax composite with a balsa core. The driver plate is made from an aluminium sheet laminated to Richlite panels with Loctite viscoelastic glue.
Here is a frequency response of one recent version (Fuzz Measure in room at 0.3m)
Step response (the negative dip before the rise and some of the small ringing at the peak is measurement microphone dependent, this is with Umik 2 and Umik 1 looks different there, otherwise identical)
A lot more detail to follow in additional posts, slowly
Incredibly even frequency (and step) response! Does this include any filter/dsp?
Very interesting, thanks for posting!
Very interesting, thanks for posting!
To explain more about the bending wave driver I was developing I will first give details about the magnetic motor structure and voice coil. Almost all magnetic motor structures for pistonic drivers and bending wave drivers are round using a cylindrical voice coil. That is easy to produce and and also easy to center the voice coil. My reasoning for using a rectangular driver is to avoid a concentric geometry to have a wide spread of relationships of voice coil to the membrane geometry to avoid as much as possible specific dominating resonances. There have been some rectangular/linear voice coil/magnetic motors developed over time like the one Carl Pinfold published in the 80ties and more recently a Harmon Kardon loudspeaker with flat drivers https://support.harmanaudio.com/on/...ASCADE MODEL 9^INF^lit^mrs white paper^^^.pdf
One parameter which, very different from pistonic drivers, is the that bending wave drivers have almost no movement of the membrane as it is constrained, so displacement of the voice-coil within the magnetic gap, even at low frequencies, is irrelevant (x-max is irrelevant).
Presently, I am using a magnetic rectangular assembly 80mm long, the voice coil a few mm longer, the width of the voice coil varies between 12mm and 18mm depending on how exactly the magnet assembly looks like. I am using neodymium block magnets (N42 to mostly N48 and I am trying to get some with higher temperature ratings especially for the elements adjacent to the voice coil). Some of them are custom magnets.
Originally, I made some magnetic structures using low carbon steel to direct the magnetic field to the magnetic gap for the voice coil similar to most standard loudspeakers. I was reading several papers by Guy Lemarquand about ironless magnetic motors and their advantages to reduce distortions e.g,: https://hal.science/hal-00462380/file/Applied_Acoustics_71_6_Merit_2010.pdf. There have been almost no commercial attempts to use ironless motor structures for loudspeakers except Borrensen for their top of the line 0-series and Cleer Audio for headphones.
My first attempt was to just have two additional neodymium magnets on both sides of the the magnetic gap avoiding iron directly next to the voice coil. That gave me a significant improvement especially in distortion levels but also frequency response (in general the step response is much less dependent on voice-coil/motor design and more dependent on membrane/surround).
schematic showing the orientation of the magnetic fields
I also tried some completely ironless designs, the first is based on a Halbach magnet array structure which is a stack of 3 magnets generating the magnetic gap on each side of the voice coil. Each stack has on one side a weak magnetic field (facing outwards) and a strong magnetic field towards the voice coil.
The spacing between the left and right stack pairs and subsequently the width of the voice coil can be varied, wider is not better.
red is Al or Cu
In a further version, I replaced the two inner Halbach stacks with one stack of magnets with identical poles facing each other separated by a copper or aluminum spacer. That version generated the highest efficiency so far.
I tested various materials to make the voice coil former, including titanium foil, but I found that a nonconducting material with high stiffness is optimal in terms of frequency response and distortion levels (no eddy currents). The best I found is S-glass fiber fabric (much stiffer than standard E-glass) with heat resistant epoxy resin and the addition of 1-2% hexagonal boron nitride (hBN), a white powder similar to graphite/graphene; a good conductor of heat but not at all for electric current (insulator) to increase heat transfer and stiffness. For the voice coil itself I am using 33 or 35 AWG copper magnet wire with a winding height of 4-6mm generating between 4 to 8 Ω DC resistance.
I will show some measurements of these different motor structures with identical membranes, but it will take a couple of days.
P.S.: Assembly of these magnetic structures requires care, experience and jigs, I broke many magnets!
One parameter which, very different from pistonic drivers, is the that bending wave drivers have almost no movement of the membrane as it is constrained, so displacement of the voice-coil within the magnetic gap, even at low frequencies, is irrelevant (x-max is irrelevant).
Presently, I am using a magnetic rectangular assembly 80mm long, the voice coil a few mm longer, the width of the voice coil varies between 12mm and 18mm depending on how exactly the magnet assembly looks like. I am using neodymium block magnets (N42 to mostly N48 and I am trying to get some with higher temperature ratings especially for the elements adjacent to the voice coil). Some of them are custom magnets.
Originally, I made some magnetic structures using low carbon steel to direct the magnetic field to the magnetic gap for the voice coil similar to most standard loudspeakers. I was reading several papers by Guy Lemarquand about ironless magnetic motors and their advantages to reduce distortions e.g,: https://hal.science/hal-00462380/file/Applied_Acoustics_71_6_Merit_2010.pdf. There have been almost no commercial attempts to use ironless motor structures for loudspeakers except Borrensen for their top of the line 0-series and Cleer Audio for headphones.
My first attempt was to just have two additional neodymium magnets on both sides of the the magnetic gap avoiding iron directly next to the voice coil. That gave me a significant improvement especially in distortion levels but also frequency response (in general the step response is much less dependent on voice-coil/motor design and more dependent on membrane/surround).
schematic showing the orientation of the magnetic fields
I also tried some completely ironless designs, the first is based on a Halbach magnet array structure which is a stack of 3 magnets generating the magnetic gap on each side of the voice coil. Each stack has on one side a weak magnetic field (facing outwards) and a strong magnetic field towards the voice coil.
The spacing between the left and right stack pairs and subsequently the width of the voice coil can be varied, wider is not better.
red is Al or Cu
In a further version, I replaced the two inner Halbach stacks with one stack of magnets with identical poles facing each other separated by a copper or aluminum spacer. That version generated the highest efficiency so far.
I tested various materials to make the voice coil former, including titanium foil, but I found that a nonconducting material with high stiffness is optimal in terms of frequency response and distortion levels (no eddy currents). The best I found is S-glass fiber fabric (much stiffer than standard E-glass) with heat resistant epoxy resin and the addition of 1-2% hexagonal boron nitride (hBN), a white powder similar to graphite/graphene; a good conductor of heat but not at all for electric current (insulator) to increase heat transfer and stiffness. For the voice coil itself I am using 33 or 35 AWG copper magnet wire with a winding height of 4-6mm generating between 4 to 8 Ω DC resistance.
I will show some measurements of these different motor structures with identical membranes, but it will take a couple of days.
P.S.: Assembly of these magnetic structures requires care, experience and jigs, I broke many magnets!
Last edited:
Very interesting. So the magnets had to be drilled. I'm curious to see how the membrane is constructed. It's great that you share your knowledge with us. Many thanks. Greetings
It is almost impossible to drill through a magnetized neodymium magnet, they are therefore custom magnets
Hello, now I have found the drilled magnets. How high is the BL product of your drives? Have you also tested a flat coil, like with the rubanoide or does the area of 8 cm square have advantages? Greetings
I have no way to measure the BL of there's magnet structures , it would be nice to know the difference between the different designs.Hello, now I have found the drilled magnets. How high is the BL product of your drives? Have you also tested a flat coil, like with the rubanoide or does the area of 8 cm square have advantages? Greetings
Around 5 years ago I tested a flat voice coil /magnet structure
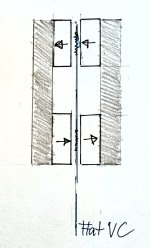
it worked well except winding a voice coil with thin magnet wires on a flat surface is past my patience level. Also keeping the flat voice coil former centered in the magnetic gap is difficult to impossible except if one uses a wide magnetic gap or a spider on top of that structure but that would likely causes issues with distortion etc. There're a piston driver with flat coil develop and one is available:https://www.parts-express.com/Dayto...ore-Neodymium-Woofer-4-Ohm-295-248?quantity=1 but these are pistons drivers not bending wave drivers
I can try to simulate the magnet force in the gap with the femm program. To do this I would need to know the size of the magnets, the copper plate and the gap width. I assume the arrows indicate the direction of the magnetization. Greetings
That would be great. Yes the arrows indicate the direction of magnetization. All the magnetic gaps are 1.7mm wide. The dimensions of the Halbach like array is 7x7x80mm for the center magnet and the lower and upper ones are 3.5x7x80mm. The magnet dimensions of the inverted array is 6x15x80mm, the central copperplate is 5x15x80mm. For the first magnet system with the iron joke the all magnets adjacent to the gap are 2.3mmx9x80mm. The lower magnets are 6.25x19x80mm. I wonder if it would be just as effective to replace these magnets with an iron element and slightly increase the depth of magnets around the gap to 3-4mm
I have used FEMM for exploring magnet/pole-piece structures (although not for acoustic drivers). It can be very good for quickly evaluating the effect(s) of changing magnet and pole piece geometries.
I also (eventually) moved to using the built-in script processor Lua. One great advantage of using it is that you can specify exact geometries, which simplifies the machining work needed to create a real-world version.
FEMM can also calculate the forces acting on your conductors so you can optimize force vs displacement linearity. THAT is where Lua really could help you out.
I also (eventually) moved to using the built-in script processor Lua. One great advantage of using it is that you can specify exact geometries, which simplifies the machining work needed to create a real-world version.
FEMM can also calculate the forces acting on your conductors so you can optimize force vs displacement linearity. THAT is where Lua really could help you out.
If the gap is less than 1.25 mm, you can use a Gauss meter:I have no way to measure the BL of there's magnet structures , it would be nice to know the difference between the different designs.
Keeping any iron ut of a speaker motor will reduce distortion - its really important as this kind is really ugly.I wonder if it would be just as effective to replace these magnets with an iron
//
I beg to differ.
To get close to linear magnetic flux density in the gap, you mostly need iron pole pieces.
To get close to linear magnetic flux density in the gap, you mostly need iron pole pieces.
Last edited:
Well, if you are content with hysteresis anomalies of course it is the best way to build flux. But it is nasty... I say, all iron out ;-) impossible... to any cost 🙂
//
//
- Home
- Loudspeakers
- Planars & Exotics
- improving bending wave drivers