I think I can build a 2 rail 8 bearing sled that will track as well and easily as a single rod.
Using just one of the rails will be for a single 4 bearing model. The single will have the tonearm mounted as conventionality done, but the sled will have a separate vertical pivot. This will separate the lateral and vertical elements. They will be interchangeable for comparison.
The rails will be made from small square brass tubing (K&S). The bearings will ride on the corner edges not the flats. Problem will be to make them smooth and straight which negates just regular buffing as that would certainly make hills and valleys. The polisher has to be perfectly flat to do the job just like using a whetstone on it. I do not foresee buying several expensive whetstones to try. No information found on doing brass; this is at someone's mercy.
Zene
Using just one of the rails will be for a single 4 bearing model. The single will have the tonearm mounted as conventionality done, but the sled will have a separate vertical pivot. This will separate the lateral and vertical elements. They will be interchangeable for comparison.
The rails will be made from small square brass tubing (K&S). The bearings will ride on the corner edges not the flats. Problem will be to make them smooth and straight which negates just regular buffing as that would certainly make hills and valleys. The polisher has to be perfectly flat to do the job just like using a whetstone on it. I do not foresee buying several expensive whetstones to try. No information found on doing brass; this is at someone's mercy.
Zene
Zene,
Keep us posted of course 🙂. Has anyone else noticed that Clearaudio has almost phased out the original Souther concept in favour of the glass tube on even their flagship model?. With double rails though get out the calipers, this will be getting down to mil spec and lower to ride the rails consistently 🙂.
Colin
Keep us posted of course 🙂. Has anyone else noticed that Clearaudio has almost phased out the original Souther concept in favour of the glass tube on even their flagship model?. With double rails though get out the calipers, this will be getting down to mil spec and lower to ride the rails consistently 🙂.
Colin
It makes some sense, since the bearing virtually rides on top of the imperfections because of its radius.
PDR,
I'm very glad you are happy with the arm, I am still using the last iteration with the same success in flawless playback. I can only hope others will also join the ranks of a free concept superbly performing affordable quick build mechanical linear arm, as much as the arguments are food for thought seeing the builds and personal flavour are what make this world a better functioning place 🙂.
Colin
I'm very glad you are happy with the arm, I am still using the last iteration with the same success in flawless playback. I can only hope others will also join the ranks of a free concept superbly performing affordable quick build mechanical linear arm, as much as the arguments are food for thought seeing the builds and personal flavour are what make this world a better functioning place 🙂.
Colin
that is looking promising ! hope you'll like it as much as I do .
btw : who is using MC carts with the arm ? interesting in their findings !!
Paul
btw : who is using MC carts with the arm ? interesting in their findings !!
Paul
PDR,
I am messing with decoupling everything I can at the moment... I think the way our glass tube runs out of a block is wrong. Its better to copy Colin's approach. He passes a metal rod thru the tube and further decouples it from the tube by two rubber bands. The glass tube has only a couple of points of contact to the table. He has further decoupled the tone arm assembly in two other sections. The base and the assembly that holds and adjusts the metal rod.
In the same vain , the use of solid printer rods might also be wrong. As they conduct microphonics. I have found anything solid is terrible for passing vibration to the needle.
I have not had chance to rebuild yet but I will post my impressions soon
I am messing with decoupling everything I can at the moment... I think the way our glass tube runs out of a block is wrong. Its better to copy Colin's approach. He passes a metal rod thru the tube and further decouples it from the tube by two rubber bands. The glass tube has only a couple of points of contact to the table. He has further decoupled the tone arm assembly in two other sections. The base and the assembly that holds and adjusts the metal rod.
In the same vain , the use of solid printer rods might also be wrong. As they conduct microphonics. I have found anything solid is terrible for passing vibration to the needle.
I have not had chance to rebuild yet but I will post my impressions soon
chokesrule let me know what you come up with, I've been thinking of other ways to adjust for height quickly for different thickness of albums. I dont think a wood base is in my future.......and I think your correct on isolating the tube.
As luck would have it I have the next week or so off from work.....perfect timing.
As luck would have it I have the next week or so off from work.....perfect timing.
I follow these thread from a while, very interesting, lot of useful information
thank you guys.
These helps people like me who has no experience with linear tracking tonearm to have some idea where to start.
I collected the material for a suspended tonearm with neodymium magnets and I started to work on but never put it together because I want min 16" arm or so and that suspension if I remember well only for 9-12" max length tonearms.
So I have some nice ultra light titanium wind, some carbon fiber and aluminum arrow shaft.
I think I can achieve better result with these type of arm.
I have several question before I purchase or order (spend more money on tonearm material)
I see some people use acrylic or aluminum for head shell, also I saw someone used commercial head shell.
What would be the optimum thickens for the glass tube?? It must be tube or can be solid to.
Bearing size smaller is better or there is any optimum size, for example like these would do the job?
10pcs Miniature Model Bearing MR73ZZ 3x7x2 5mm | eBay
How important the head shell material or the arm (shaft) material.. You guys all meat with these question at any DIY or commercial tonearm.
If someone know a site where I can get detailed information, measurement etc that would be great to.
Answer to my question would be greatly appreciated , that would help to purchase the missing items and start my own DIY tone arm.
Thank you very much.
Greetings Gabor
thank you guys.
These helps people like me who has no experience with linear tracking tonearm to have some idea where to start.
I collected the material for a suspended tonearm with neodymium magnets and I started to work on but never put it together because I want min 16" arm or so and that suspension if I remember well only for 9-12" max length tonearms.
So I have some nice ultra light titanium wind, some carbon fiber and aluminum arrow shaft.
I think I can achieve better result with these type of arm.
I have several question before I purchase or order (spend more money on tonearm material)
I see some people use acrylic or aluminum for head shell, also I saw someone used commercial head shell.
What would be the optimum thickens for the glass tube?? It must be tube or can be solid to.
Bearing size smaller is better or there is any optimum size, for example like these would do the job?
10pcs Miniature Model Bearing MR73ZZ 3x7x2 5mm | eBay
How important the head shell material or the arm (shaft) material.. You guys all meat with these question at any DIY or commercial tonearm.
If someone know a site where I can get detailed information, measurement etc that would be great to.
Answer to my question would be greatly appreciated , that would help to purchase the missing items and start my own DIY tone arm.
Thank you very much.
Greetings Gabor
PDRCanada:
I see want you are trying to do but it would take a lot of work to make it rigid enough. You can save yourself a lot trouble by looking on ebay under" height gauge". These are used in conjunction with a surface plate to measure or scribe material with precision. These tools already have a very rigid base and caliper type movement.
Joe
I see want you are trying to do but it would take a lot of work to make it rigid enough. You can save yourself a lot trouble by looking on ebay under" height gauge". These are used in conjunction with a surface plate to measure or scribe material with precision. These tools already have a very rigid base and caliper type movement.
Joe
Colin ... what do you think the optimum wheel c to c spacing is considering 62mm arm length and why? If an equilateral triangle would be approx 72mm.
Thanks, Zene
Thanks, Zene
Hey Joe,
I've seen those before, they look like they would work excellent, except
for the adjustment to level the tube. With a rigid base like the height gauge
has, how would you set the tubes angle?
I'm going to buy a cheap caliper and try some modifications. See how sturdy
the base will be.
Thanks for the suggestions, please keep them coming.
I've seen those before, they look like they would work excellent, except
for the adjustment to level the tube. With a rigid base like the height gauge
has, how would you set the tubes angle?
I'm going to buy a cheap caliper and try some modifications. See how sturdy
the base will be.
Thanks for the suggestions, please keep them coming.
MC cartridge
Not a soul who is using an MC cart with the arm ? or even tried to 😀
Well .. I guess I will just take some out of the drawer here .. as some aren't that bad concerning compliancy in my view .
Paul
Not a soul who is using an MC cart with the arm ? or even tried to 😀
Well .. I guess I will just take some out of the drawer here .. as some aren't that bad concerning compliancy in my view .
Paul
Paul, I cannot remember who it was that replied to a question that I posted, but someone was using a Denon 103 (of some revision) and were quite pleased with it.
As soon as I can afford a pair of SUT transformers, I will pick up a Denon MC cartridge. Right now, I am relegated to the MM carts that I already own. Who knows, maybe Santa will be good this year ;-)
As soon as I can afford a pair of SUT transformers, I will pick up a Denon MC cartridge. Right now, I am relegated to the MM carts that I already own. Who knows, maybe Santa will be good this year ;-)
PDRCanada:
Mounting the tube will take some doing. It depends on the type height gage you buy.
You might be able to fasten a piece of an aluminum block that is drilled out to the diameter of the tubing and screw or otherwise fasten it to the side of the piece that holds the scribe blade. This may not be easy because most height gages are hardened steel ( or stainless steel ).If you drill a hole in the front of the block and cut a small slot in the back of the block vertically you will be able to tilt or lift the tube slightly. This would require you to drill and tap hardened steel which can be very tricky. You will have to decide what your capabilities are. If you find a solution that works post a picture if possible. Good luck.
Joe
Mounting the tube will take some doing. It depends on the type height gage you buy.
You might be able to fasten a piece of an aluminum block that is drilled out to the diameter of the tubing and screw or otherwise fasten it to the side of the piece that holds the scribe blade. This may not be easy because most height gages are hardened steel ( or stainless steel ).If you drill a hole in the front of the block and cut a small slot in the back of the block vertically you will be able to tilt or lift the tube slightly. This would require you to drill and tap hardened steel which can be very tricky. You will have to decide what your capabilities are. If you find a solution that works post a picture if possible. Good luck.
Joe
Zene
I settled on a 40mm spacing for the bearings, why?, because it worked best and it comes down to final weight of the carriage vs friction. I was previously using a 50mm spacing, as stated prior with many experiments this is all the best set of compromises to create an exceptional sounding and performing mechanical linear arm.
Colin
I settled on a 40mm spacing for the bearings, why?, because it worked best and it comes down to final weight of the carriage vs friction. I was previously using a 50mm spacing, as stated prior with many experiments this is all the best set of compromises to create an exceptional sounding and performing mechanical linear arm.
Colin
Why not just get an xyz platform? The work is done for you and you bolt the arm mount to the platform. I'm not talking about something that cost big bucks here, maybe about $250US or so. You will likely have micrometers for the movement (most that I have seen do) and you can adjust forward, backward, up, and down. Would work perfectly.
Why not just get an xyz platform? The work is done for you and you bolt the arm mount to the platform. I'm not talking about something that cost big bucks here, maybe about $250US or so. You will likely have micrometers for the movement (most that I have seen do) and you can adjust forward, backward, up, and down. Would work perfectly.
Or a :
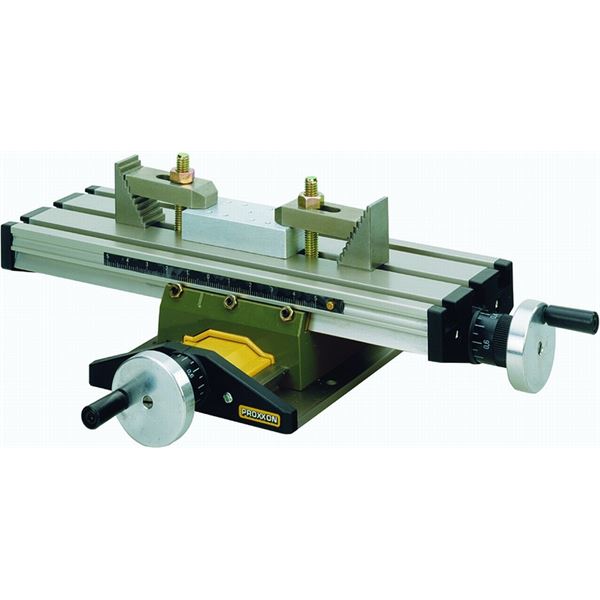
PROXXON - KT 70 - MICRO COMPOUND TABLE
€ 80 brand new. 😉
- Home
- Source & Line
- Analogue Source
- DIY linear tonearm